I'm currently waiting while components are coming in slowly, in order to finish the bed. In the meantime I found these digital thermometers so I can keep track of my motor temperatures, which is probably a bit frivolous, but does look cool :)
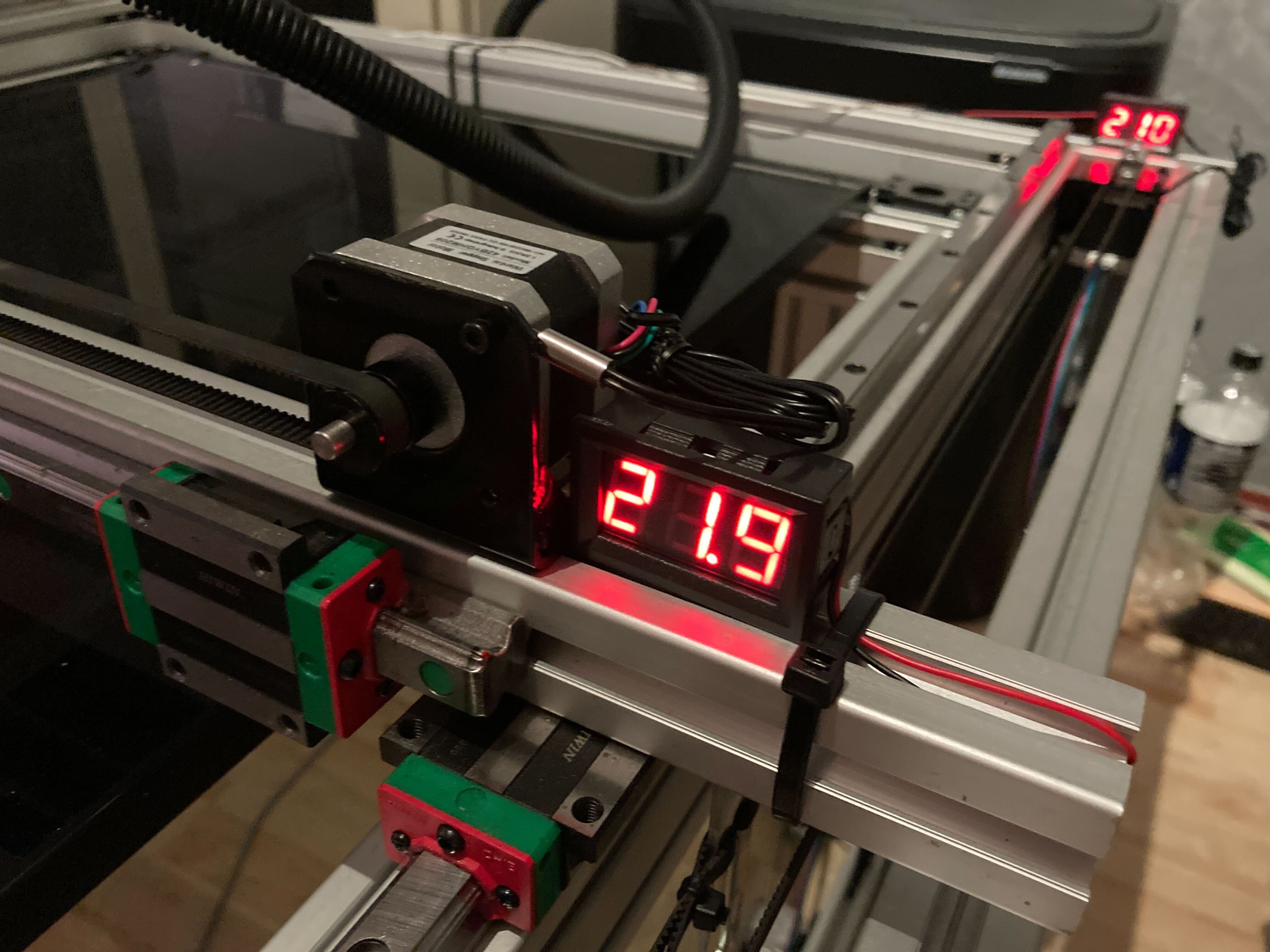
Automatic Belt Tensioning
Now, having 2 motors for an axis, one on each side, allows for a cool trick. We can counter-rotate the motors and add tension to the belt, and as long as we power the motors with enough torque they should be able to hold the tension between them.
One minor issue is that for this to work they both need their own motor controller, and currently I only have a single controller attached to both X motors (in parallel), while the Y controllers are split between left and right, not sharing a belt. So I ordered a can-bus extension board for the extruder which comes with a dedicated TMC 2209, freeing up one motor controller on the main board and allowing me to clean up some wiring along the way.
Initially I will just add some manual offset to just one of the steppers during the homing procedure while the other holds its position, but what I really like to try, later, is to use TMC's StallGuard to get an even tension regardless of the initial state (tension) of the belt.
Discussions
Become a Hackaday.io Member
Create an account to leave a comment. Already have an account? Log In.
Here's a challenge for the belt tensioning problem: maybe one can put an accelerometer onto the print head and leverage FS90R servos for tensioning actuation (e.g. a linear drive that pushes an idler up against the belt through a force multiplication stage). The accelerometer data can pick up the signature of backlash and probably also the frequency reponse up to 500 Hz
Are you sure? yes | no