I'm worried that the machine isn't stiff enough! I don't know enough about the cutting forces to really judge this. The test jig seemed to work under hand actuation, but it did make screetchy noises sometimes when dragged quickly. I think the gantry was flexing and vibrating under load. But I was able to get great results across a range of cuts, so perhaps it's not a big deal. Either way, the Circuit Graver has a longer kinematic chain as compared to the single-axis test jig, so there are more chances for the machine to flop about.
I decided to design a test gantry that probably isn't too far off the finished piece, but is intended mainly to sprint towards a clamped-on-the-table test. That means it needs to hold the X-axis rails and lead screw bearings, and lift the spindle to the correct height so it can grave a bit of FR4 taped to the table. Thus:Desired print orientation drove the decision to make it in three pieces. I had reasonable luck getting the MGN7 rails aligned on the test jig with its support printed up, so I wanted to use the same strategy here on the smaller MGN5 rails. It's nice to have the long M2 mounting holes print upright as well to reduce the need for annoying support material removal. But I also wanted the lead screw bearing mounts to be printed axially for a better press-fit, so I designed the part to have some overlap and included four M4 bolts on either side to secure it all together.
The MGN5 rails I sourced (via eBay) each had four carriages, so I transferred a bunch onto two storage rails. I'll need to fabricate storage blocks at some point, but this is fine for now:
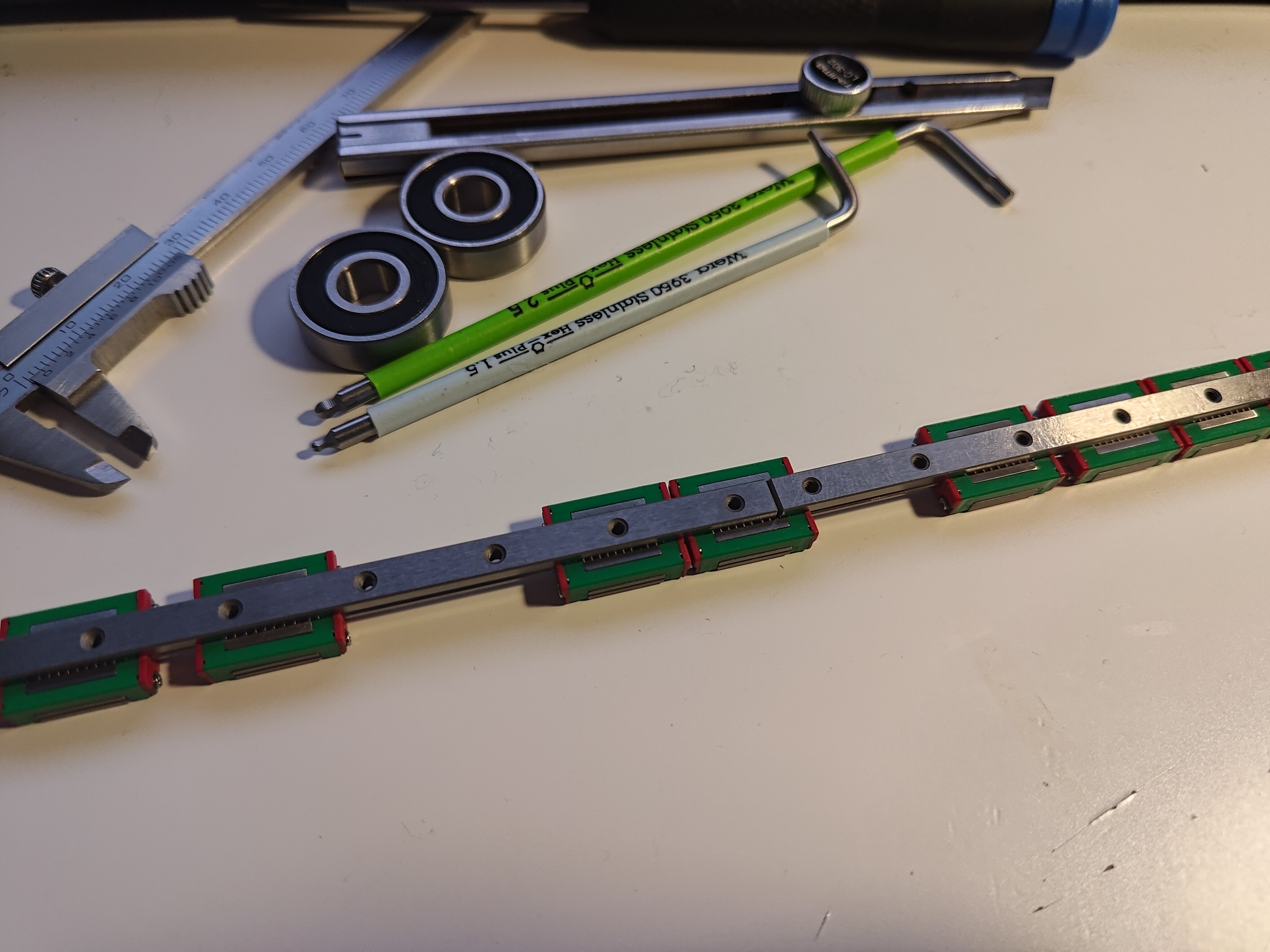
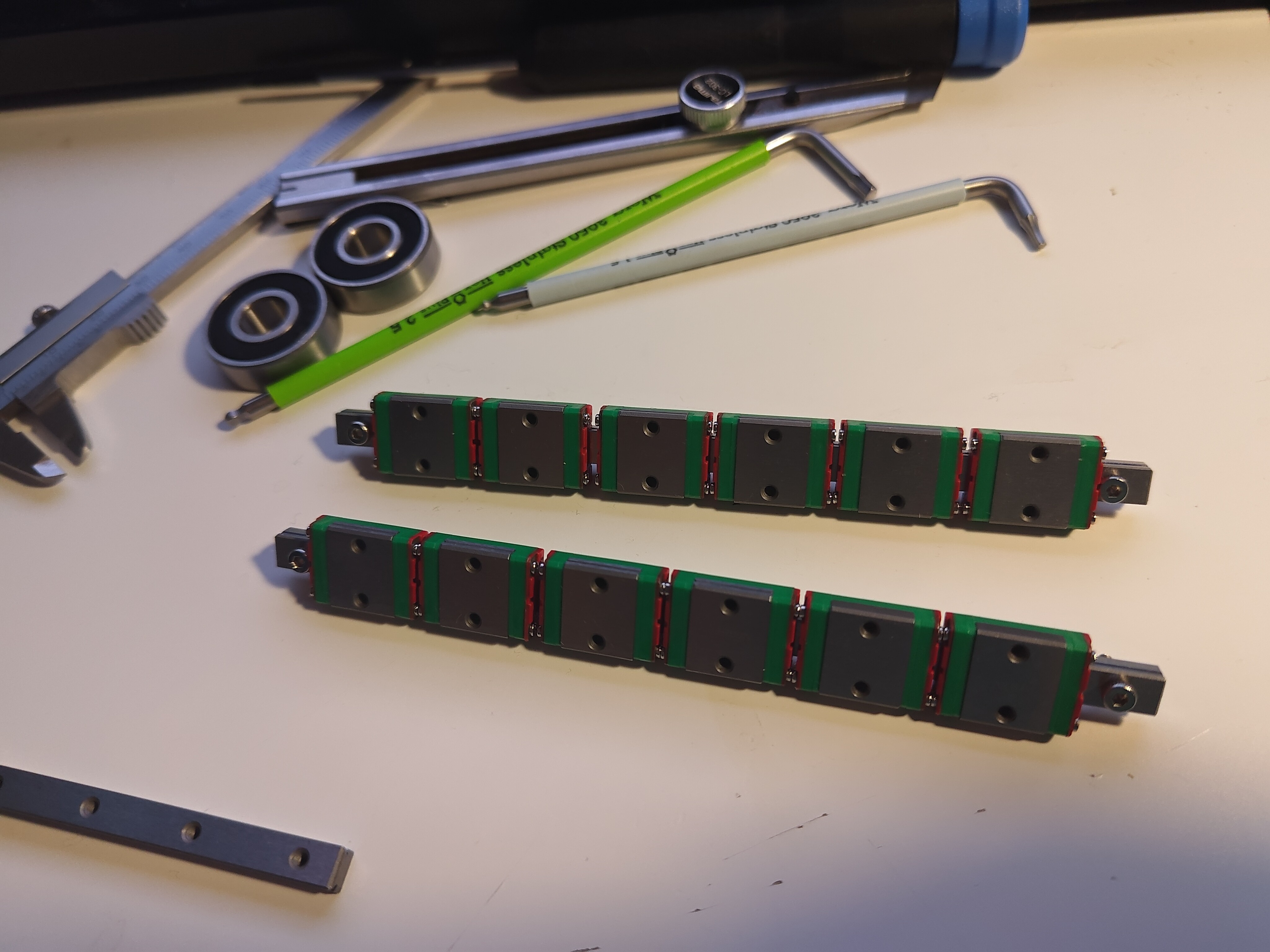
I designed and fabricated a dial indicator mount which spans a pair of MGN5 carriages, and used this to tram the top rail in against the bottom one. The mounting parallelism tolerance in the datasheet is an unlikely 2 μm, but I was still able to get within a tick (10 μm) of the indicator, so perhaps I'm only off by a factor of 2 or 3:
After tightening the rails and re-checking alignment, I mounted the plate, installed the bearings, and slid the leadscrew into place. I added a bit of lithium grease to the lead screw, and some thin synthetic PTFE-based oil to the linear guides. The lead screw is low as compared to the far bearing, suggesting I mis-measured an offset somewhere (which isn't surprising):
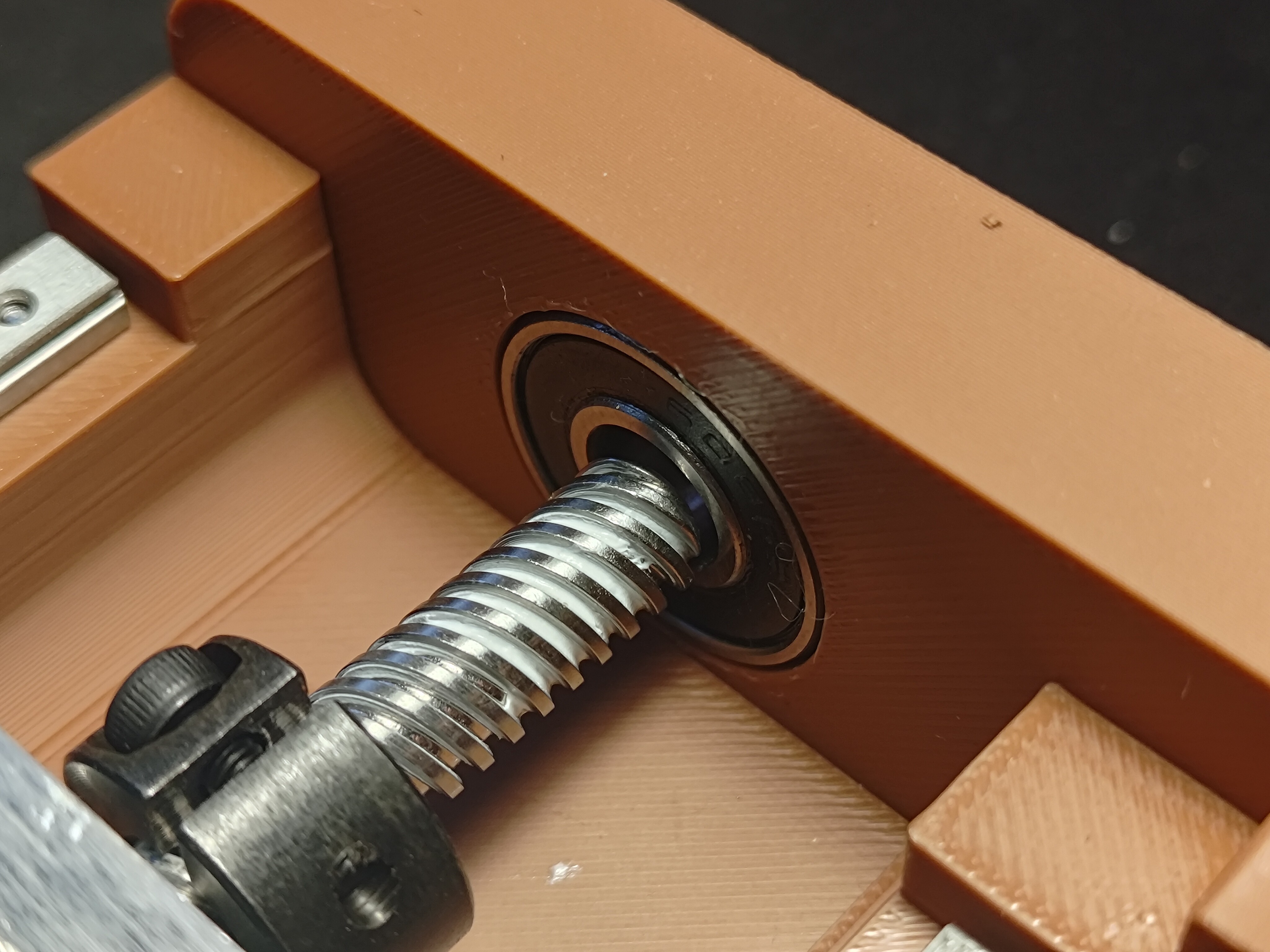
But this isn't a huge problem; there is enough compliance in the other bearing mount that the lead screw still works smoothly after applying a bit of preload. I replaced the far bearing with a blanking plate and then tightened the nearer locking collar with some manually applied axial preload on the screw itself:
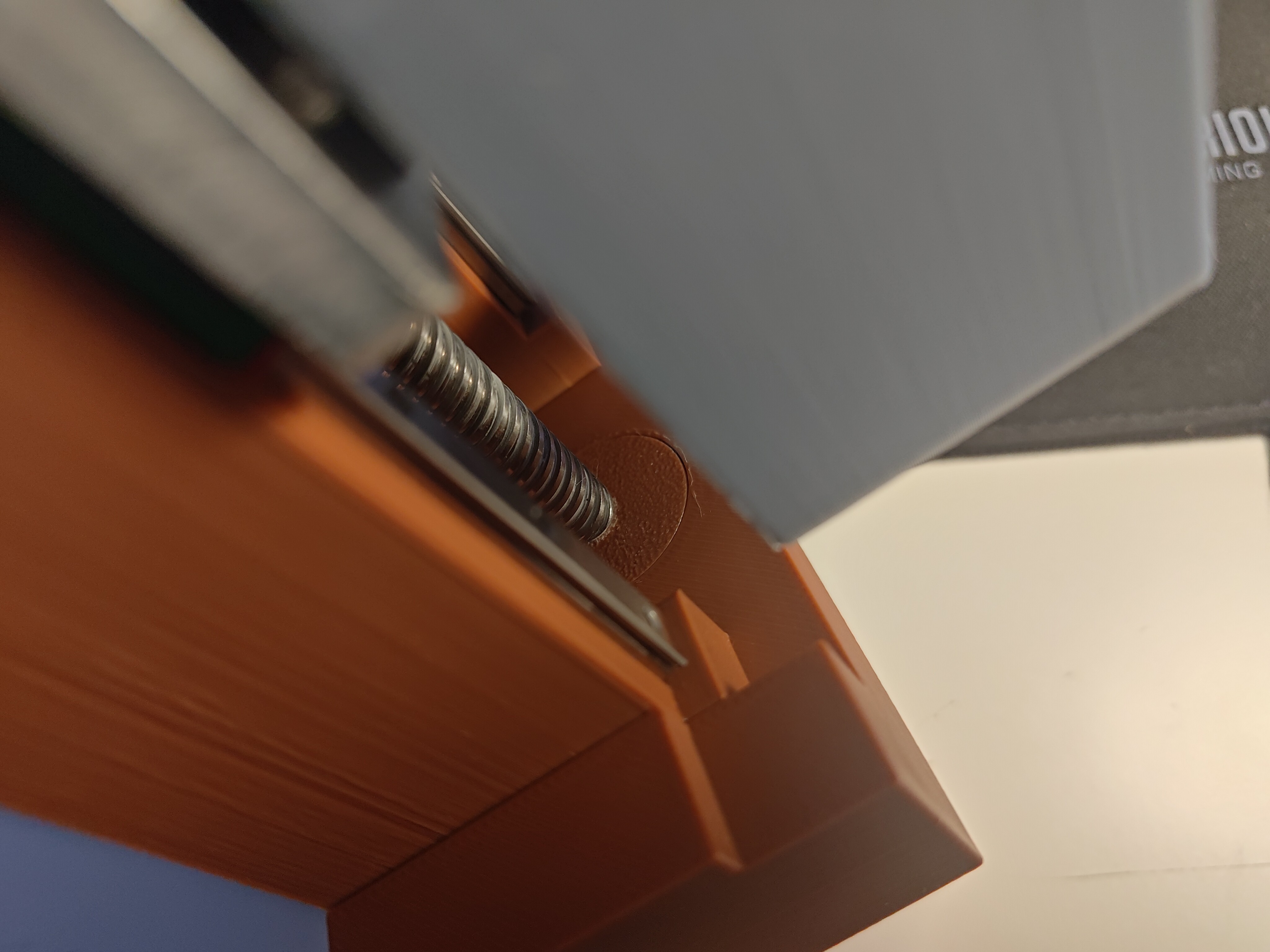
The servo got in the way so I removed it, and then installed the Z-axis flexure assembly (actually attached in the image above; I'd just forgotten to photograph the blanking plug before reassembly):
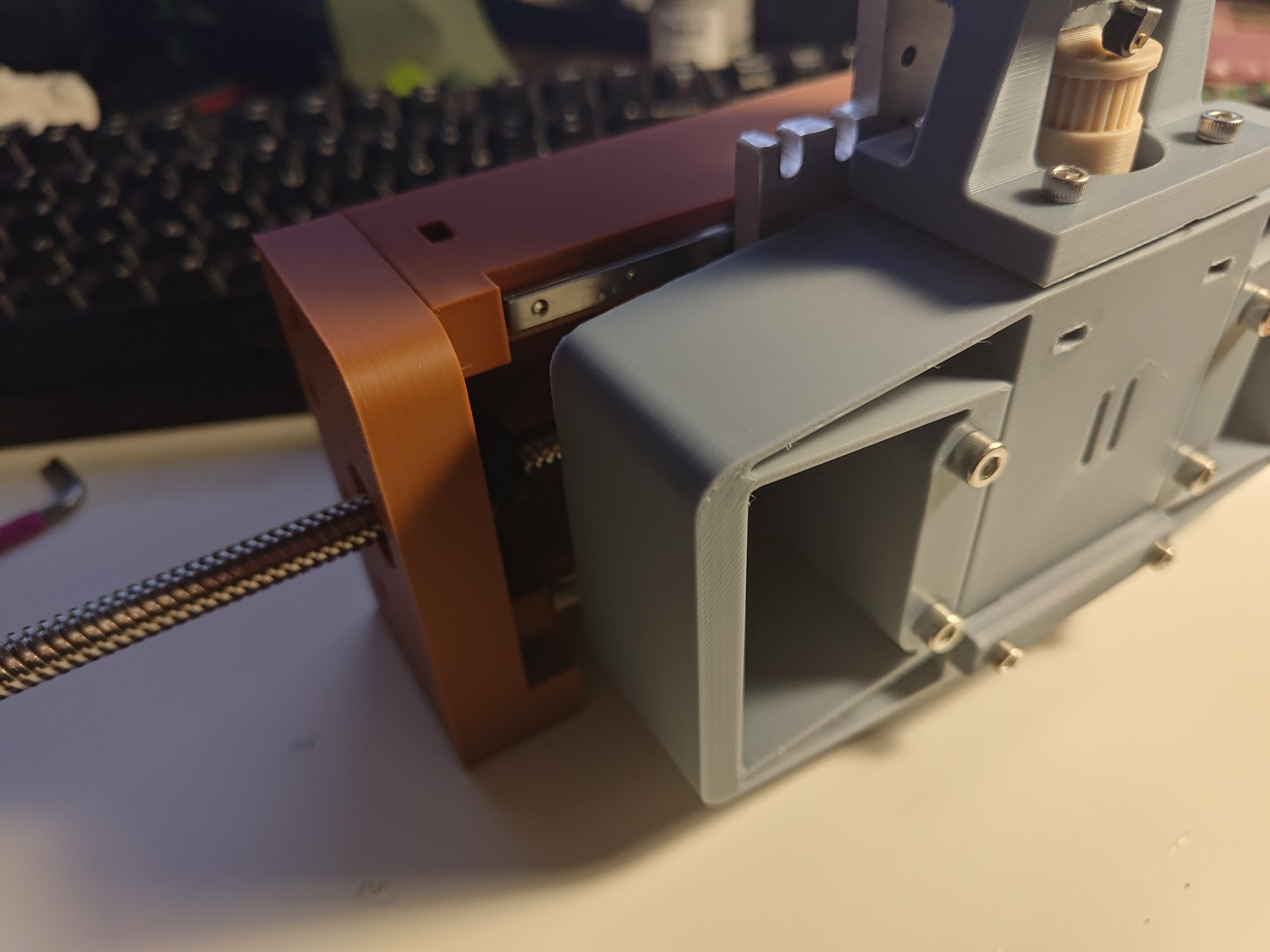
I kept the test lead screw preload flexure assembly on the far side of the lead screw, and just cranked its preload screws up so it turned into a convenient handle. I opened my recently-arrived box of PCB blanks:
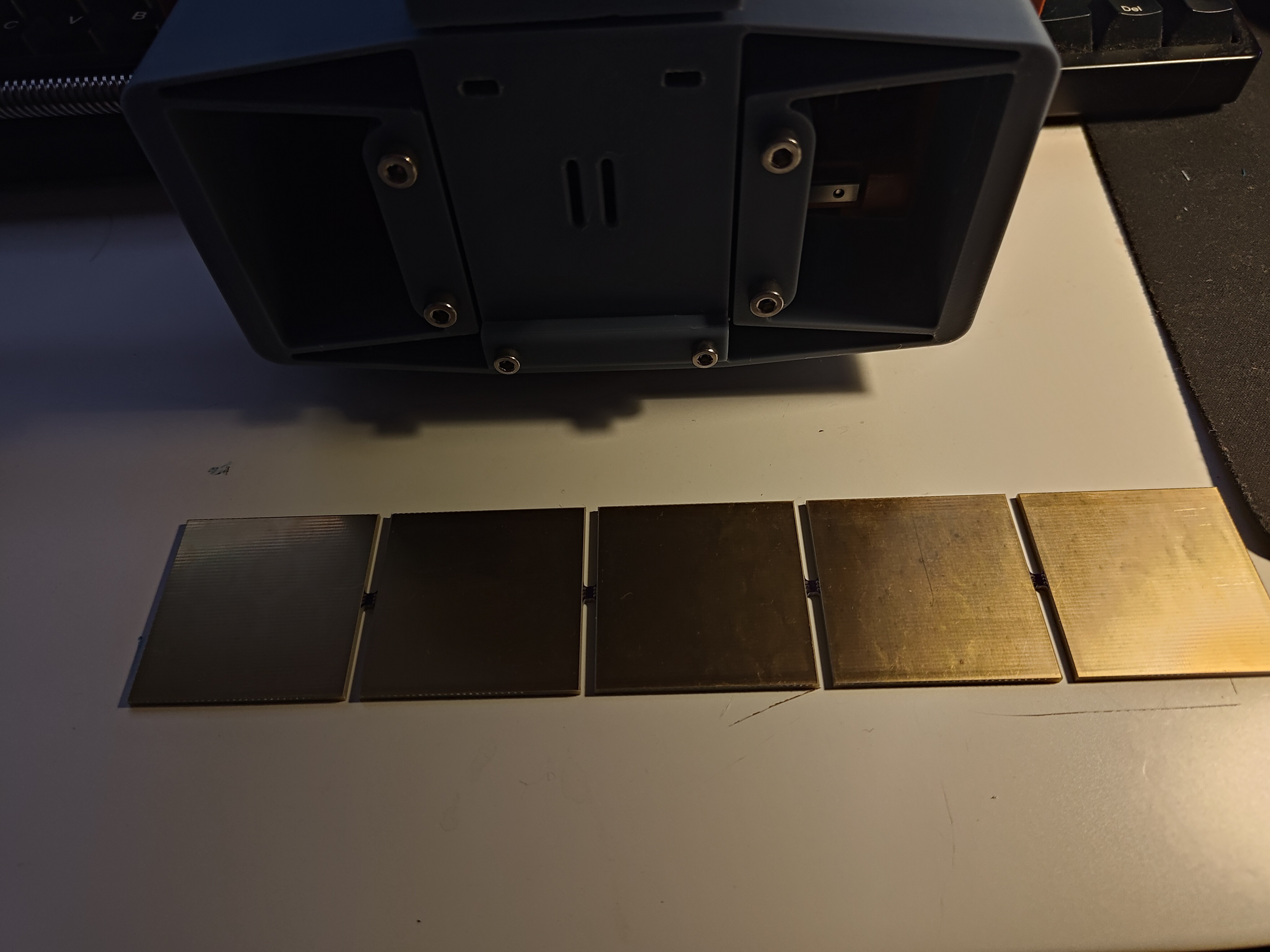
... singulated one, and secured it to the table with double-sided tape. I installed a cutter on the spindle, taped the gantry down above the PCB, and adjusted the cutting force to what seemed like a reasonable value. I advanced the lead screw to pull the cutter across the board and saw a good result on the first try:
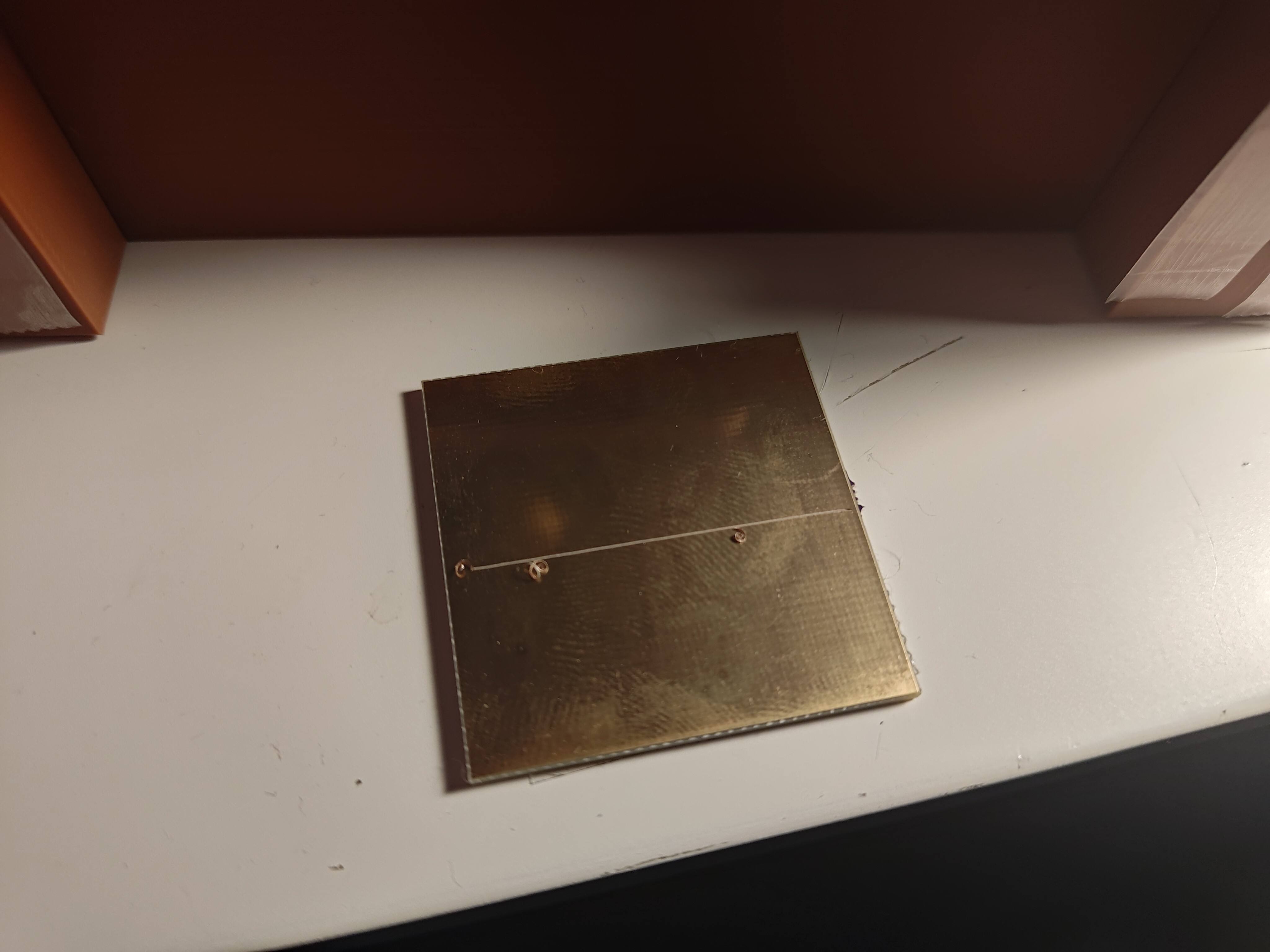
A few subsequent cuts were pretty good, and then I started futzing with preload and got some less good cuts. I think the fixturing moved a bit, or maybe the tape started bunching up and changed the height of the cutter enough to start getting worse results; in any case, later cuts weren't as great. But I think that might be related to the test setup; it's certainly not caused by the machine not being stiff enough. So the test was good! I think a reasonable next step is to design the rest of the machine: updated gantry towers (with a corrected bearing location), a static base which connects the towers, and the Y-axis assembly. One slight concern is that the machine may be quite sensitive to height, despite using pressure control for cuts; since the gantry towers will bolt in place, I may want to include some kind of precise tramming adjustment to level the table if needed.
Discussions
Become a Hackaday.io Member
Create an account to leave a comment. Already have an account? Log In.