I had some time the other day to work on my project so I connected the oscillscope and checked the time between the channels when it turns off and then on.
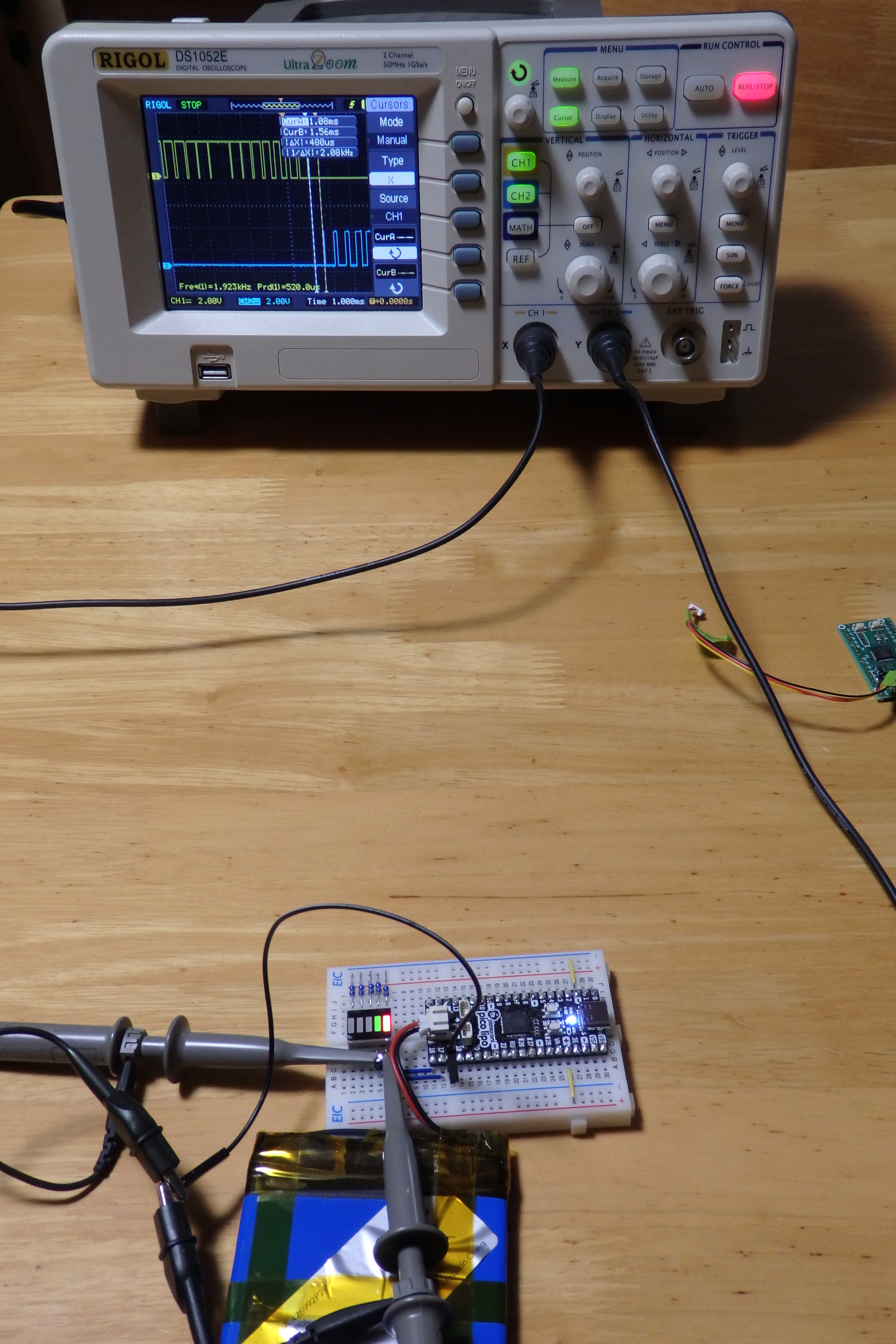
I will never run the h-bridge over 50hz but even if I run it as quickly as I can with my 20kHz pwm output, just one LUT element of deadtime is enough since the h-bridge can handle up 400kHz. My deadtime is in the microsecond range and the h-bridge do stuff in the nanosecond range. So I should be safe to connect the h-bridge.
I've desoldered the connections to the old h-bridge from the PSU and added input and output capacitors which will hopefully give me lower coldstart times. I also soldered the pin header on the h-bridge. I also soldered the socket header on my uart module which I'm going to use for another project for a bit.
Now I just have to make sure we don't get any back emf from the coil back to the h-bridge as our 40 volts is very close to the maximum voltage of the h-bridge which is 44 volts.
I removed the old capacitor from the bell ringer replaced it with a new one, added resistors to protect from back emf.
As I read through the h-bridge IC datasheet I notice that it seems to put in a deadtime of 200-300ns in hardware, which I missed.
It was written more like a note instead of on the specifications page, which is why I missed it so many times looking through the datasheet.
I connected everything together. Turned it on and the bells rang nicely. I read the voltage coming out of the H-bridge IC it was at 44 volts which is the H-bridge maximum. I have to take readings with the oscillscope to see whats going on.

The fact that this motor driver can be used have reduced the size of the h-bridge to a small IC chip.
Discussions
Become a Hackaday.io Member
Create an account to leave a comment. Already have an account? Log In.