Filament Paste? You Betcha!
For the longest time, 3D printing has been limited to solid thermoplastics like PLA, ABS, and PETG. What if we could break out of those bounds and turn any paste into a 3D printable filament? That's exactly what I'm doing with Filament2—and as a proof of concept, I’ve developed the world's first chocolate filament.
But this project isn’t just about chocolate. Imagine printing materials like ceramics, silicone, or even epoxy on a standard FDM printer, without swapping extruders or investing in expensive, specialized equipment. The goal here is to make 3D printing as versatile as possible by turning paste or semi-solid materials into 1.75mm filaments that can be used with regular 3D printers like Prusa, Bambulab, and others.
This journey has been full of trial and error, with plenty of lessons learned. Along the way, I’ve designed a number of custom systems to handle the unique challenges that come with printing pastes—including a cutting nozzle, a continuous tube-filling system, and even a cooling bed to solidify materials like chocolate almost instantly. Let’s dive into the details of how it all works!
Challenge 1: Creating a Paste Filament
The main goal was simple: create a 1.75mm filament from paste or semi-solid materials that could work seamlessly with regular FDM 3D printers. While this sounds straightforward, pastes like chocolate, clay, and silicone aren’t the easiest materials to work with. They’re messy, they don’t harden quickly on their own, and they don’t behave like typical thermoplastic filaments when extruded.
Chocolate Trials: Since I love chocolate, it seemed like a perfect starting point for this proof of concept. But chocolate presented a unique set of challenges. It’s temperature-sensitive and has a tendency to melt at the worst possible times. There were countless failed prints—chocolate oozing everywhere, prints collapsing, and general chaos in my workspace.
Breakthrough: The first major breakthrough came with the food-safe polymer tube. By encasing the chocolate (or any paste) in a polymer tube, the material could be safely contained until it was extruded. The tube would be 1.75mm in diameter, making it compatible with standard FDM printers. The polymer is food-safe, so the chocolate remains clean and protected inside the tube until printing. This opened the door for the chocolate to flow consistently while keeping the process neat and controllable.
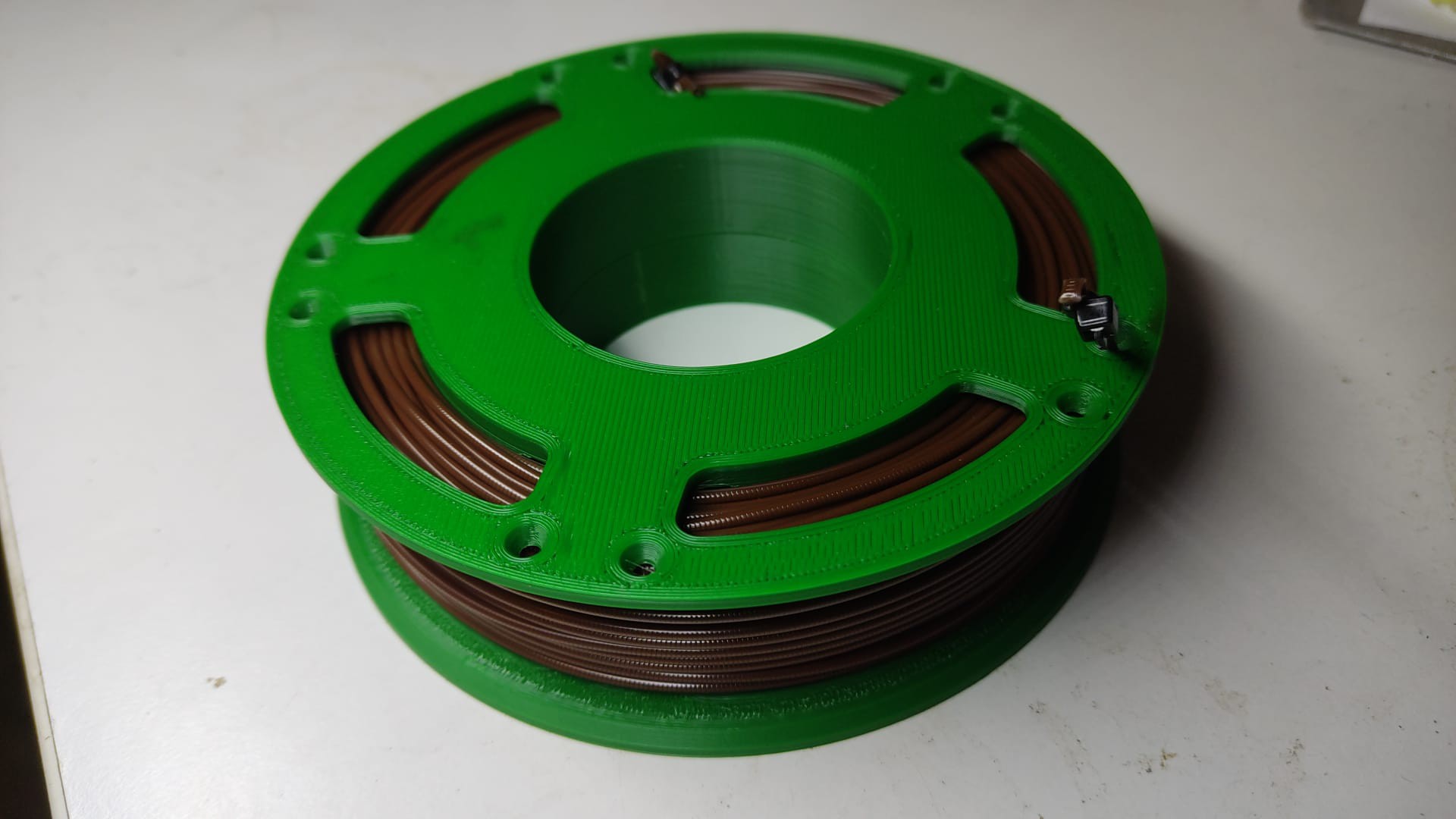
Challenge 2: The Cutting Nozzle
Once the chocolate was safely encased in the tube, the next problem was how to cut the polymer tube as the paste was extruded. I didn’t want the polymer tube to come out of the nozzle alongside the chocolate—it would ruin the print and leave plastic residue behind.
That’s where the cutting nozzle came in. This specially designed nozzle cuts the food-safe polymer tube at the moment the core material (chocolate, in this case) is extruded. The result? Only the chocolate comes out, leaving the tube behind in the printer, which keeps the printed object completely free from any unwanted material. It took quite a few iterations to get the cutting action just right, but once it worked, it was a game-changer. This innovation allows for clean extrusion of the core material without contaminating the print.
Here's a picture of my first cutting nozzle, since then I've progressed a lot!
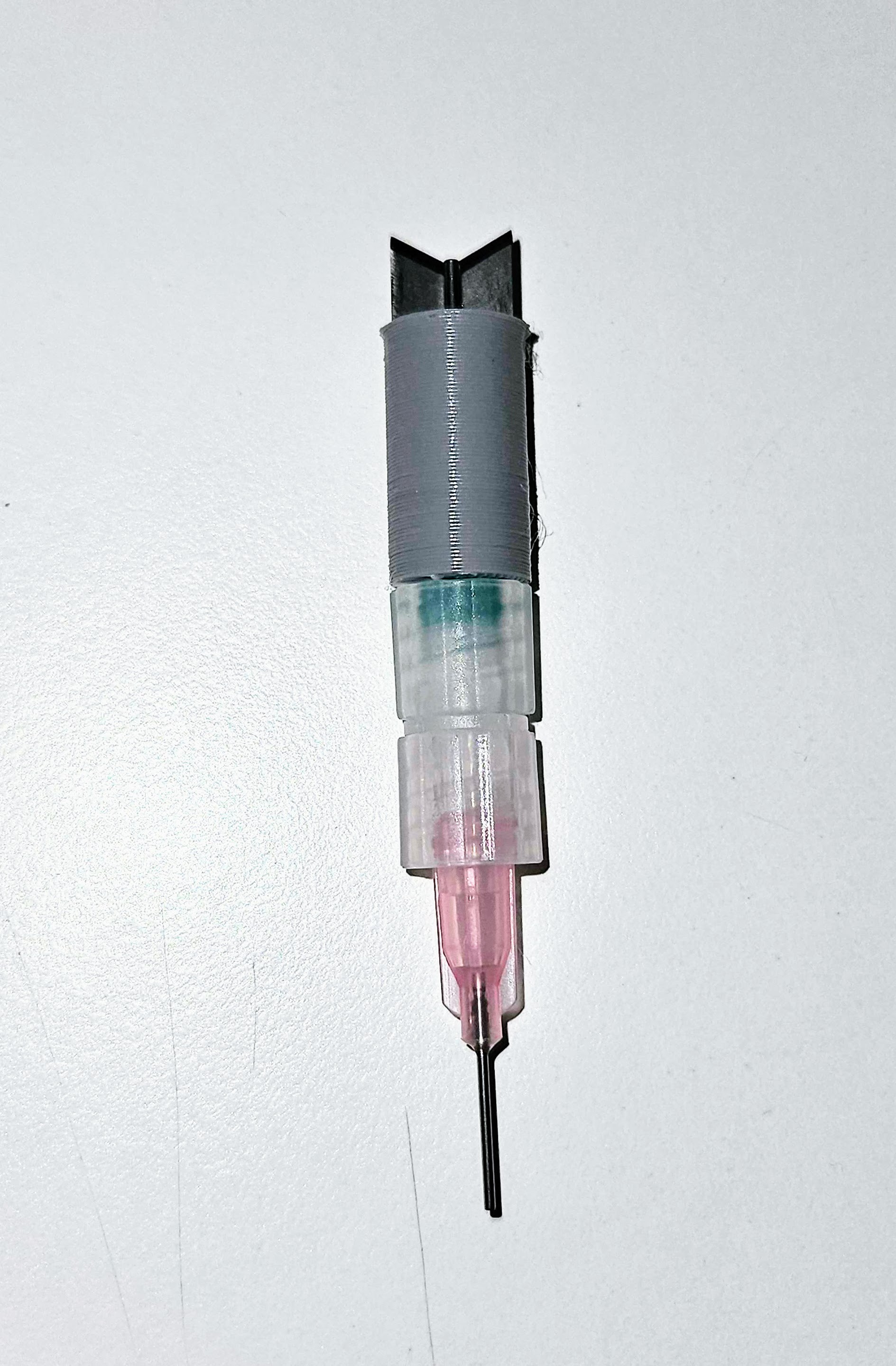
Challenge 3: Continuous Tube Filling
Printing for extended periods meant I needed a way to continuously feed the filament without constant manual refilling. Traditional FDM filament spools can hold a lot of material, and I wanted something similar for paste-based filaments.
I designed a system to cut, fill, and “weld” the tube during the printing process, allowing for continuous filling of the filament. The system is capable of cutting the food-safe polymer tube, filling it with the paste, and then "welding" it back together in a seamless process. This allows the printing to go on without interruption, ideal...
Read more »