In the early versions of Semreh, we relied on original N20 Pololu 6v 3000rpm motors paired with voltage regulators. The N20 motors proved to be highly versatile and beginner-friendly, as they come with pre-attached gearboxes and a D-shaped shaft, making it easy to mount wheel hubs. Additionally, Pololu manufactures Hall effect encoders specifically designed to be soldered onto these motors, further enhancing their usability:
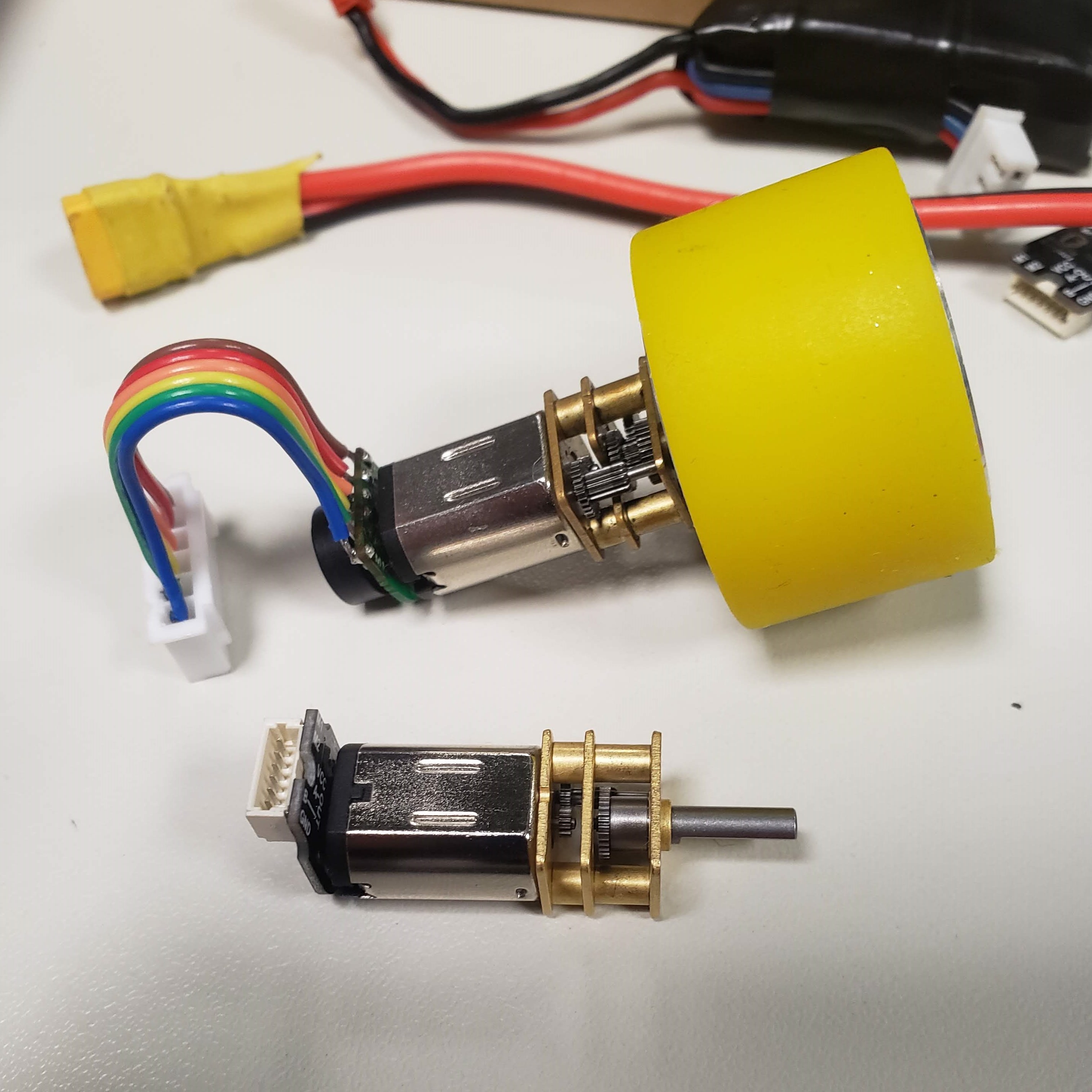
The voltage regulators stepped down the 7.4V of 2S batteries to approximately 6V, keeping the motors within their rated specifications. However, through discussions with other teams, we discovered that N20 motors could handle overvoltage without significant degradation. This led us to experiment with removing dedicated voltage regulators, resulting in noticeable performance gains. Encouraged by these results, we further pushed the limits by switching to 3S 11.1V batteries without regulators. Surprisingly, the N20 motors handled the increased voltage remarkably well, delivering impressive acceleration that significantly improved our robot’s speed.
The Coreless Motors:
However, the real breakthrough in our motor research came with the adoption of a 1020 coreless motors (7.4v) commonly used in low-cost drones. These motors provided extraordinary torque and an impressive RPM, but at a significant costs: their extremely high current consumption and the necessity of its own gearbox:
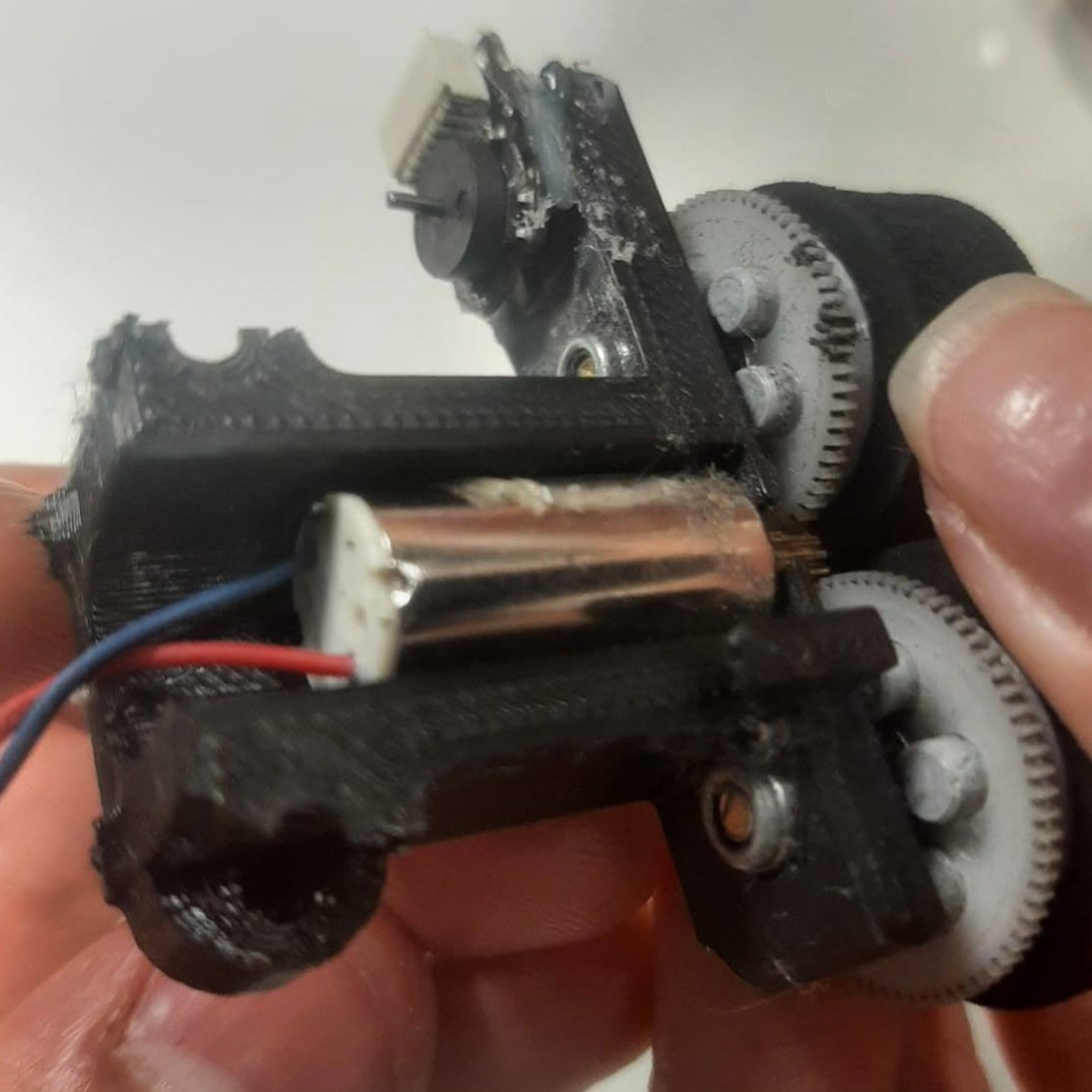
This excessive draw would trigger the built-in protection of the TB6612 H-Bridge we were using in Semreh, causing the robot to shut down when performing tight turns or zigzags. These turns placed a heavy demand on the motors, which pulled too much current, activating the protection system and momentarily disabling the motors.
To resolve this issue, we developed a custom H-Bridge module using a perforated board and two more powerful H-Bridge ICs RZ7886. The entire module was hand-soldered, providing a much higher current handling capability. This adaptation allowed us to fully utilize the potential of the coreless motors without system failures:
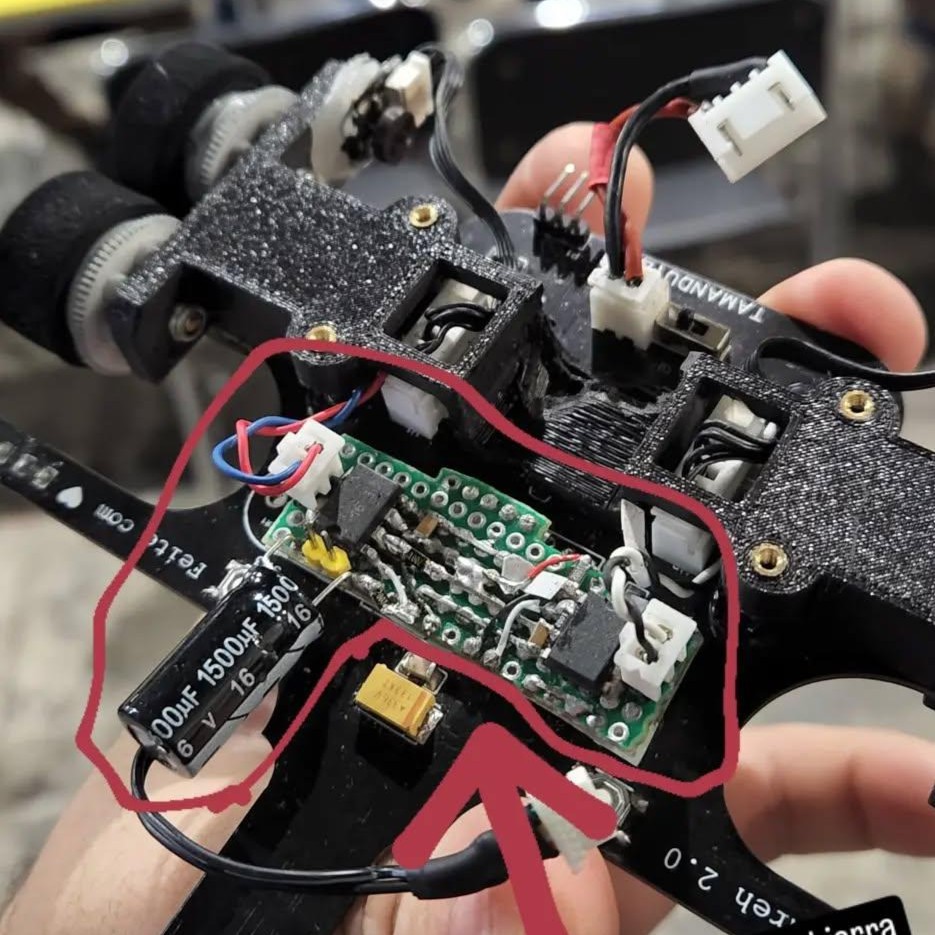
Another crucial step was designing a custom gearbox to integrate the 1020 coreless motors into our system. Since these motors lack pre-attached gearboxes like the N20, we created a reduction system using nylon gears bonded to 3D-printed structures. This approach allowed us to tune gear ratios while maintaining a lightweight design; but we'll a post only about how we design the gerbox.
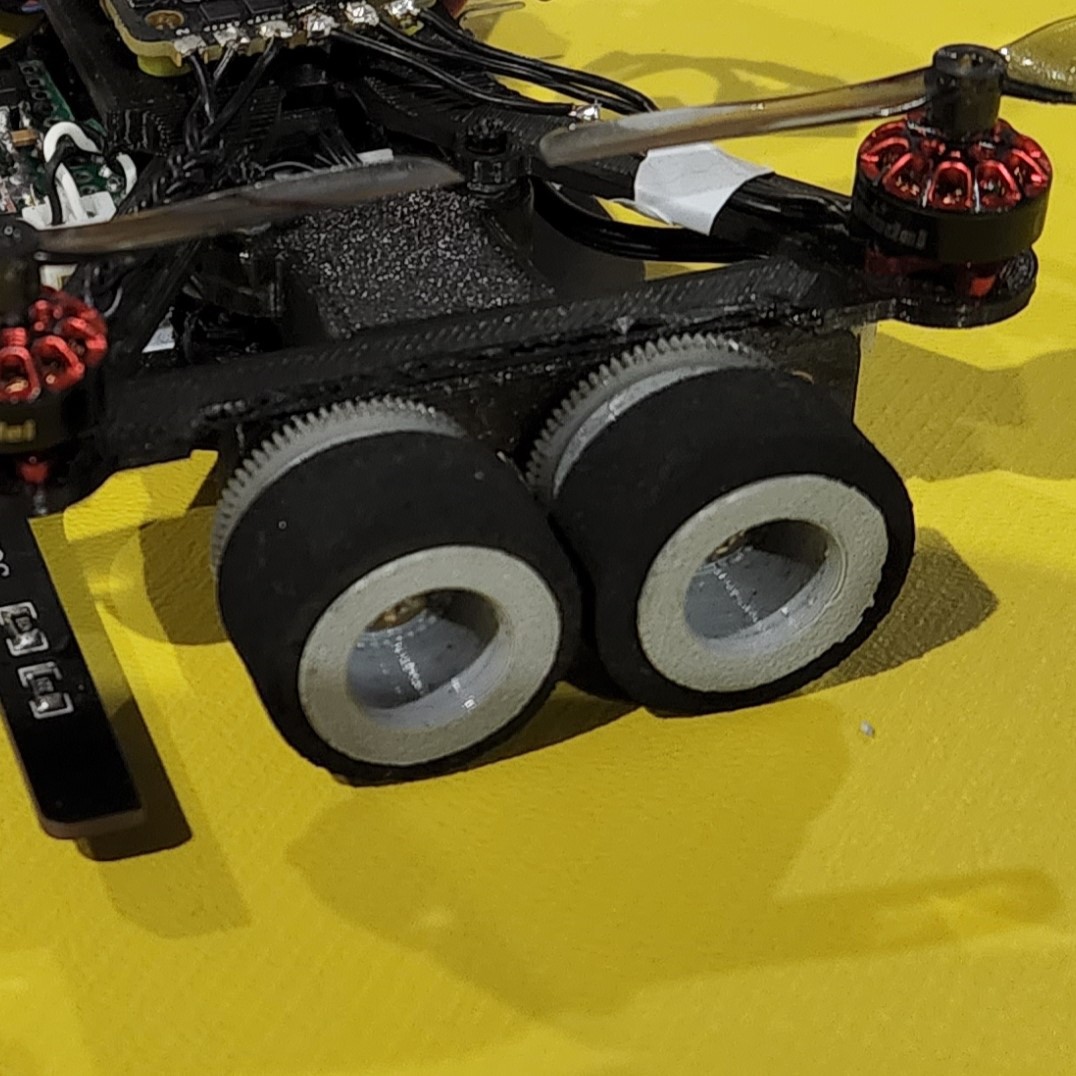
An additional challenge we faced was how and where to place the encoder on this drivetrain. Our solution was use the pololu encoders, fixed with hot glue, and attached the axis of the wheel gears via an additional gear:
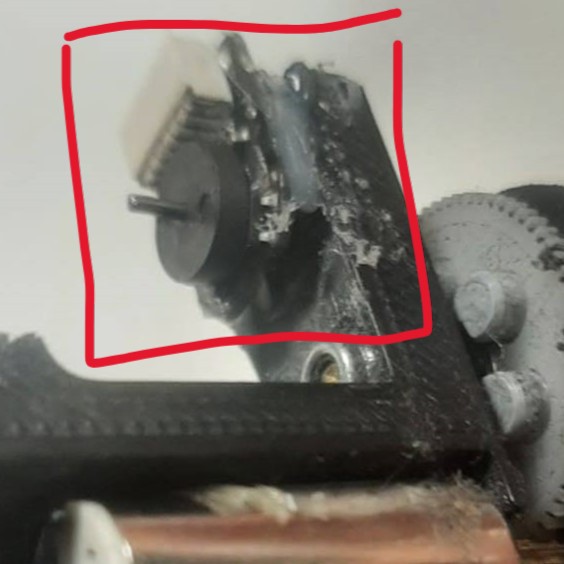
Through these advancements, we successfully transformed Semreh’s drivetrain, achieving superior speed, control, and stability for the brazilian robotics competitions.
Discussions
Become a Hackaday.io Member
Create an account to leave a comment. Already have an account? Log In.