System Overview
Performing the deposition in a controlled atmosphere is essential to generate films and structures with the appropriate characteristics. A decent vacuum ( ideally under 1e-6 torr ) and perhaps different low pressure reactive species (for examples O2 in the order of 1e-2 torr for oxides) must be alternated in quick succession.
Usually high vacuum pumps such as turbomolecular pumps operate within a narrow range of conditions, and turning them on and off is a time consuming process. Therefore, is important to design a vacuum system with a set of valves which allow fast variations among different atmospheres.
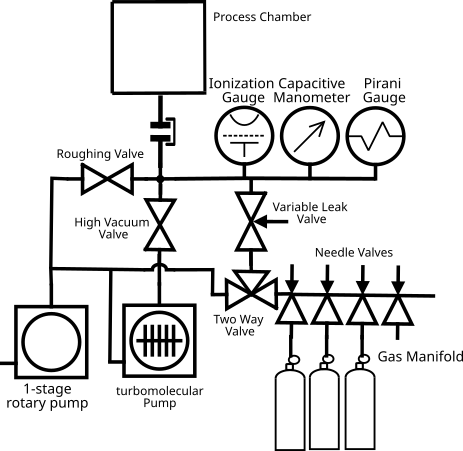
This implementation took advantage of several components that I had available, which is far from ideal.
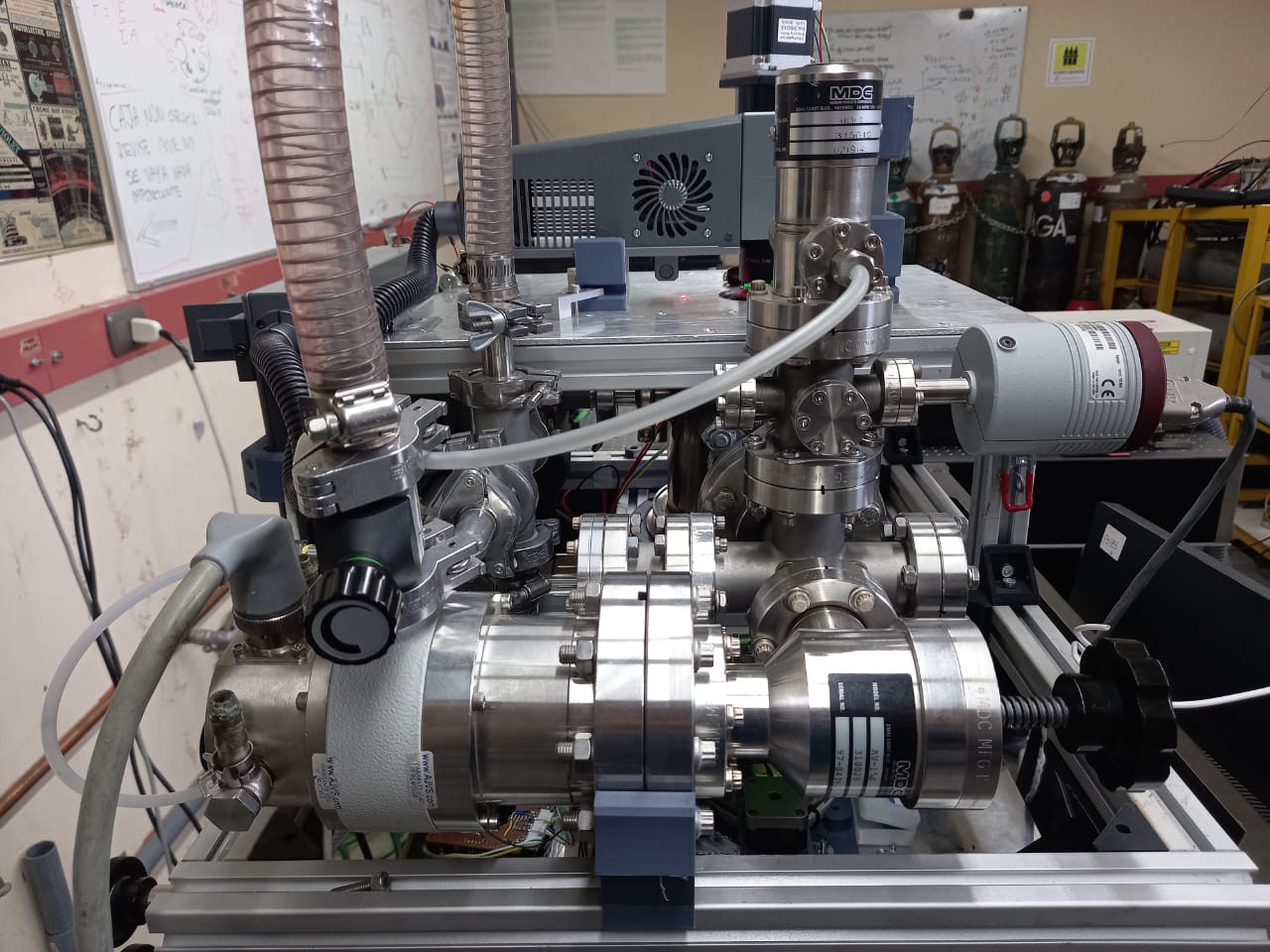
The Process Chamber
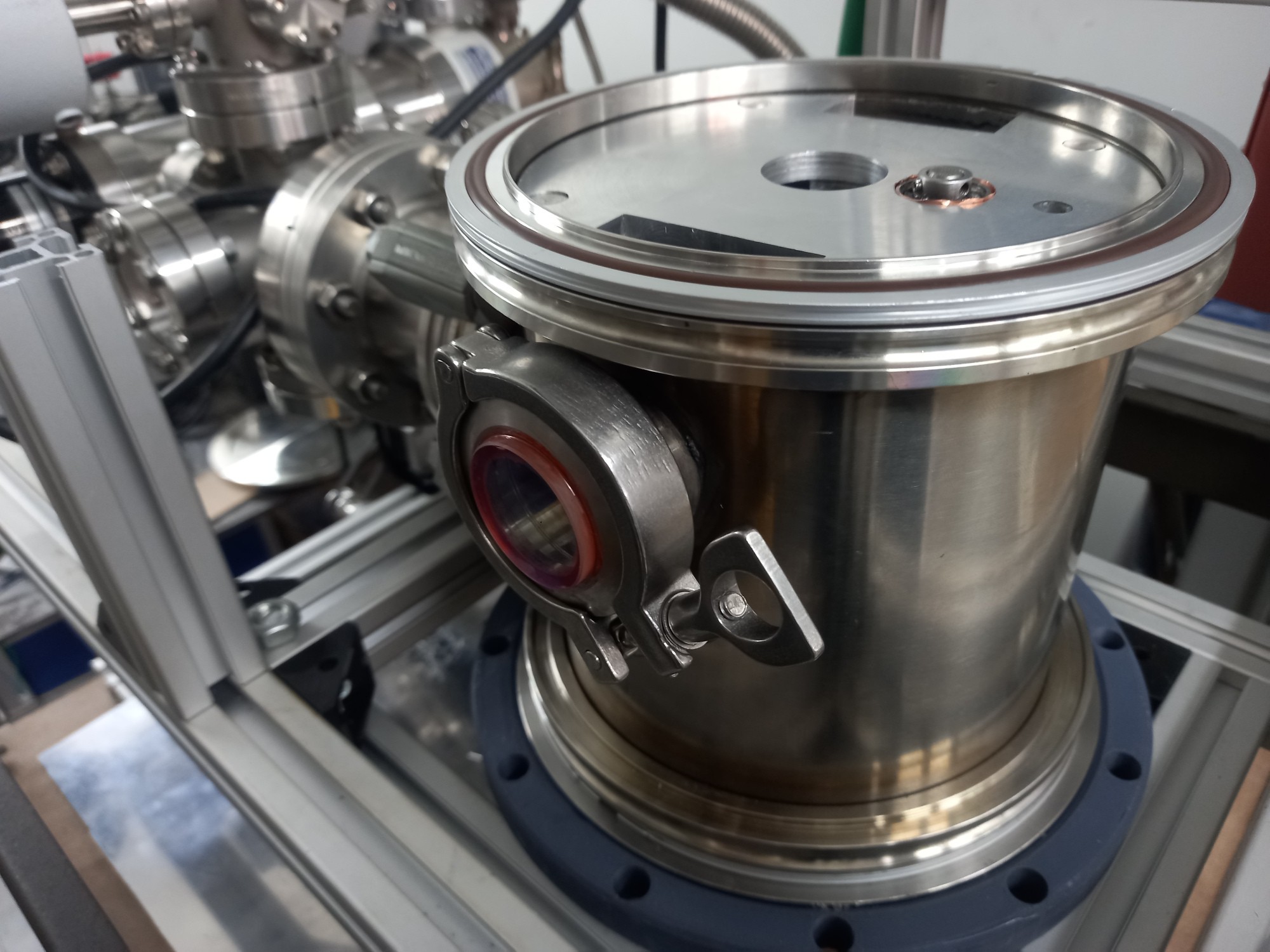
While most components where taken 'off the shelf', the mechanism chamber had several dimensional requirements (specially regarding the target-substrate distance and the different lasers focal lengths) that could only be met with a custom chamber. As those are very expensive, I had to manufacture it myself.
The cylindrical shape is quite standard due to it's ease of machining and good distribution of the pressure differential related efforts. I used a standard size for flanges, choosing ISO160 for their ease of use. I bought several Inner weld flanges from Aliexpress, as well as a 154mm OD x 2mm thick stainless steel pipe. Curiously I couldn't find any vendor from where I'm from, so I had to buy it abroad as well.
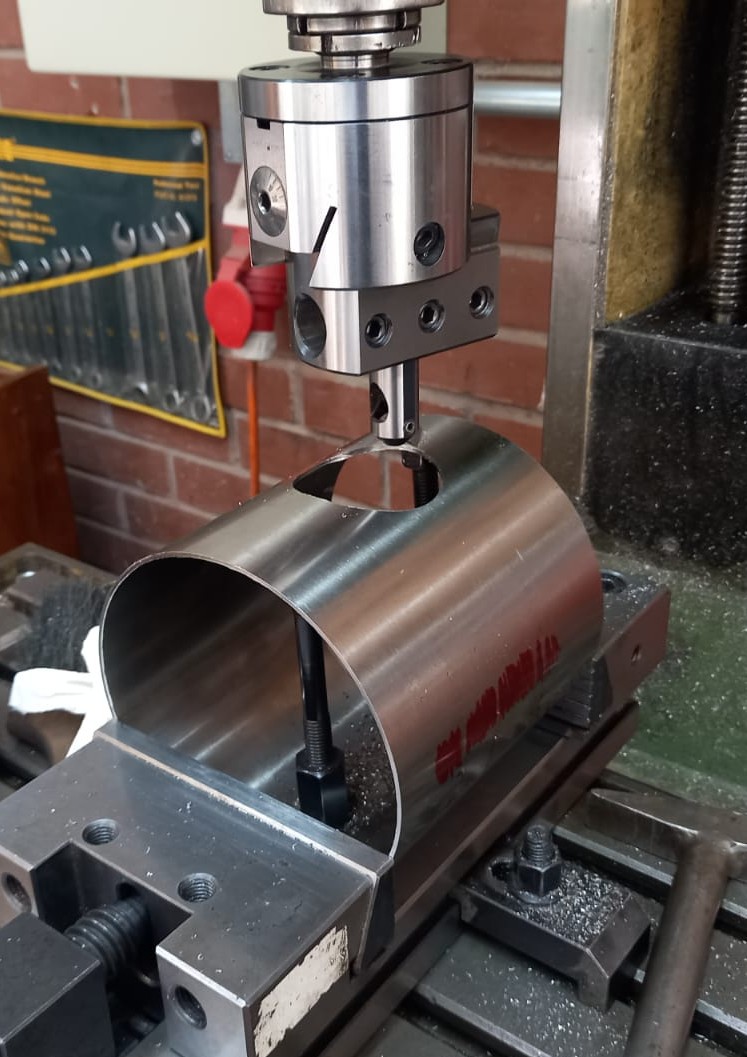
The chamber was machined to length in a lathe, and then the aperture for the flanges where milled.
The KF40 flanges, initially though as viewports and for plume diagnostics, where bought from Aliexpress (they are fairly inexpensive) and then machined to provide the right fit to the main chamber:
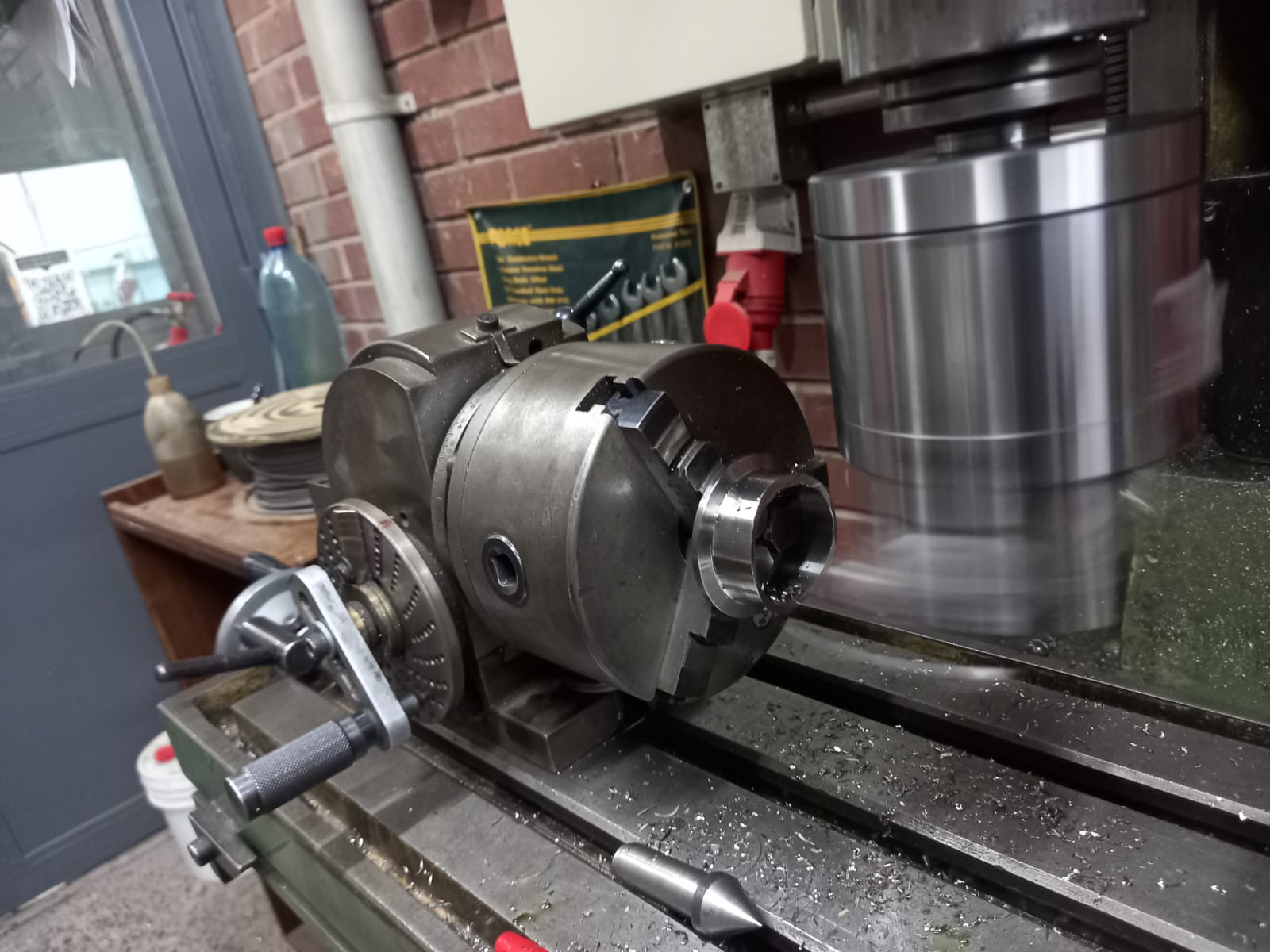
The same process was made for the ISO63 flange intended initially as a coupling to an existing turbomolecular pump.
After making sure that the tolerances were acceptable, I proceeded to TIG weld the chamber together.
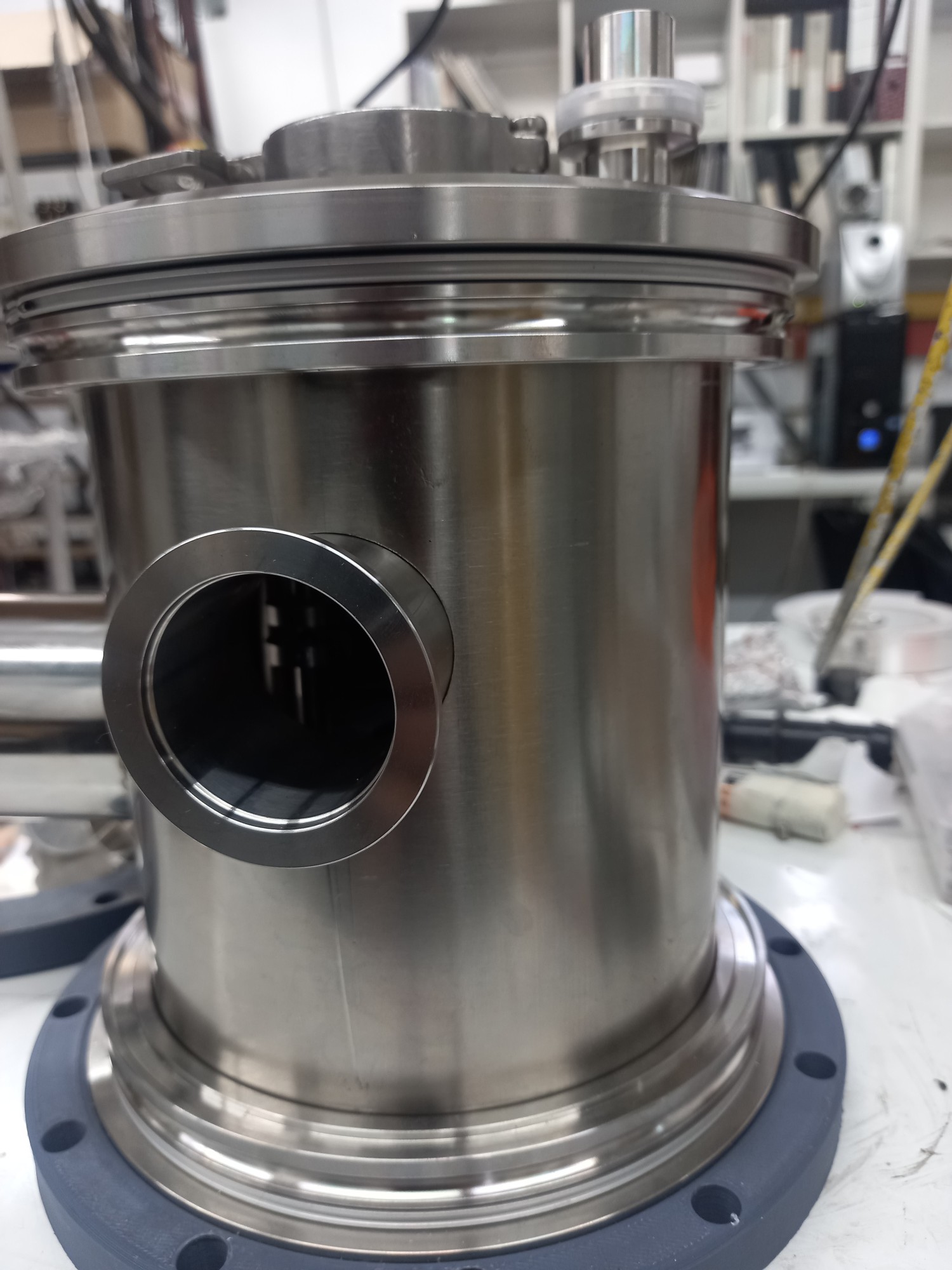
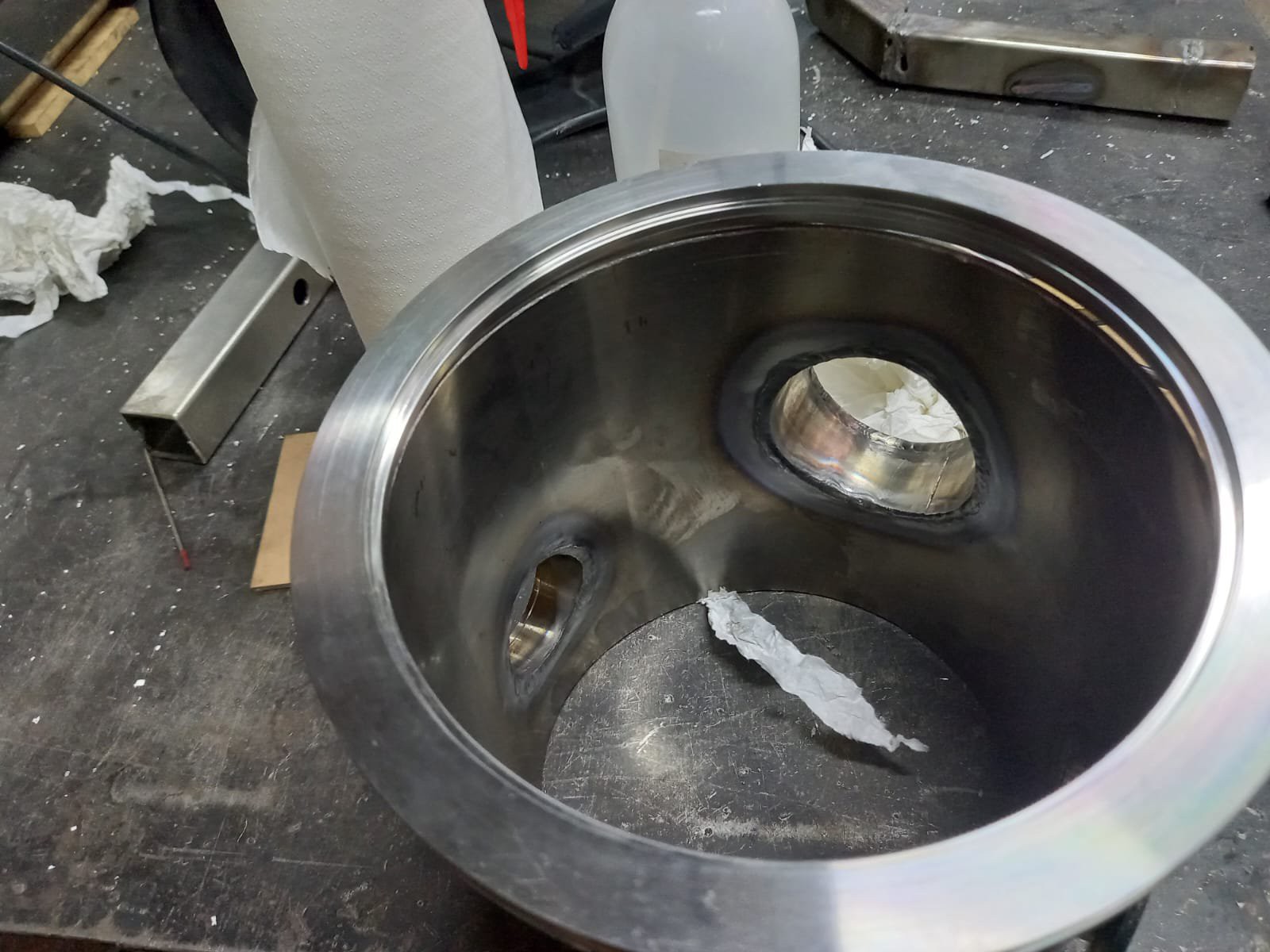
While definitively not very pretty welds, after a few adjustments they seemed to hold a decent vacuum :).
The process for the covers was quite similar: They also required custom apertures for the laser windows and manipulators. By mistake I bought KF160 instead of the proper ISO160 blind plates, but fortunately both standards are interchangeable.
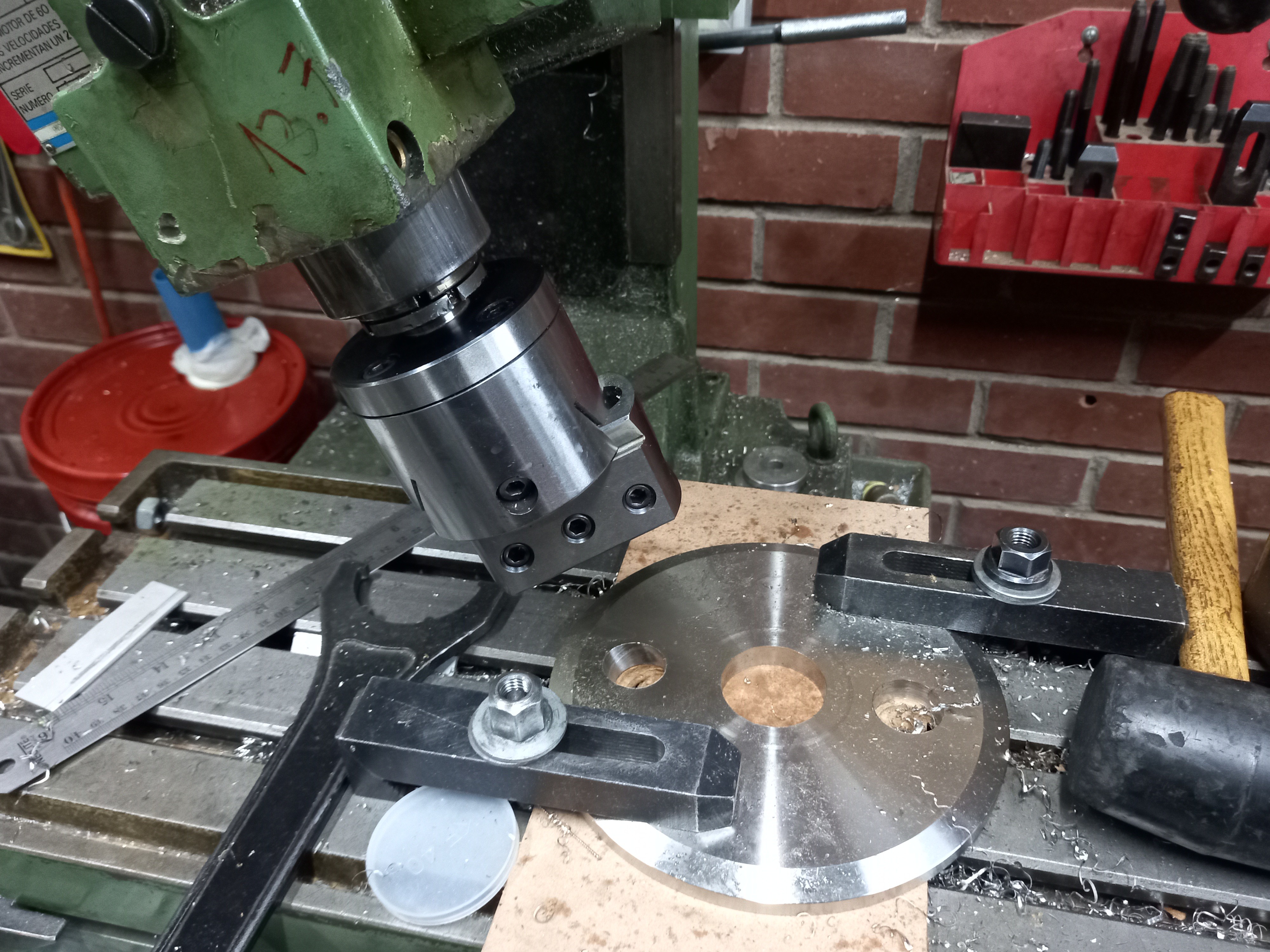
After the holes where bored, cheap KF(40/25/16) flanges were welded in place.
Discussions
Become a Hackaday.io Member
Create an account to leave a comment. Already have an account? Log In.