I have been furiously working to get out v0.2 that fixes many of the issues I found in v0.1 (the first prototype). I did a fair bit of design work in Autodesk Inventor because I am most comfortable with it. Once I felt good about the design, I moved over to Onshape and started remodeling the design but this time I made it highly parametric. The idea is that you can change a few parameters to make the parts suit your on hand components and personal goals. Everything was going well until I took a break to work on the kinematics of the new layout. I immediately found a core flaw that caused the whole redesign to fall apart like dominoes.
THE PROBLEM
Can you see it? The bottom belt can't do anything. I swear I thought about this being a problem and then figured a solution around it but here it is. I have a solution for this but I have to start from the ground up again. This design is very interdependent and all the parts have to work in concert. I actually like the new direction better but it has delayed me a week.
I am obviously still working on the design and am not ready to publish step by step instructions for this project. However, in a show of good faith, I have uploaded my working prototype files and firmware. I can't stress enough that no one should build it directly. There are some easy things that could be fixed. (belt tensioners, fixed arm lengths, increased mechanical advantage, plastic reduction)
Warning: I provide the files as is. Please don't build this version. If anyone decides to build a HELIOS from these files, they will be on their own. I am working furiously (with precious little free time) to finish v0.2. I will gladly provide support for v0.2 builders. Any time that I have to spend supporting a v0.1 build will take away the time I have to devote to v0.2.
Discussions
Become a Hackaday.io Member
Create an account to leave a comment. Already have an account? Log In.
Does this help?
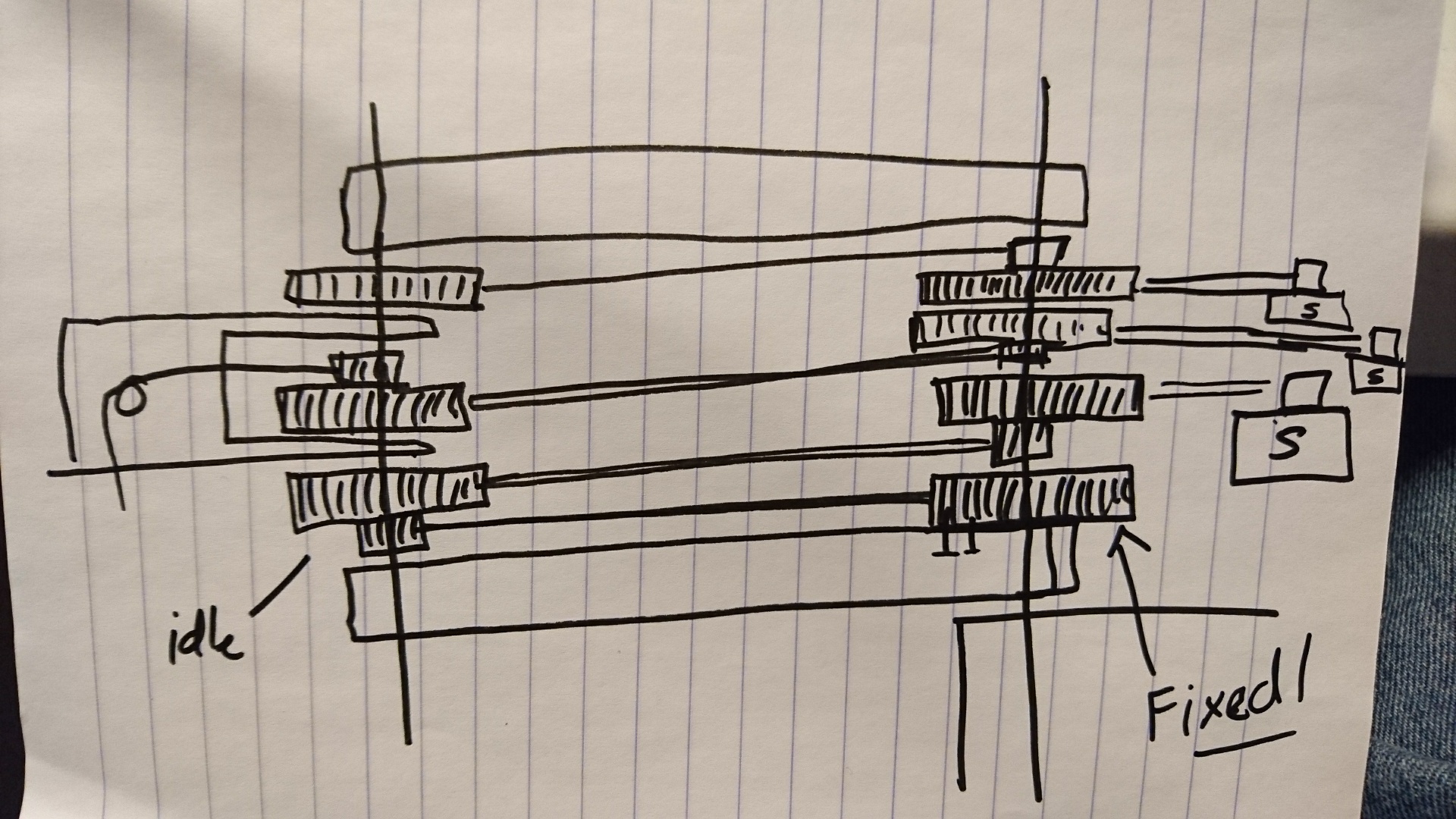
Are you sure? yes | no
The bottom two belts can't move relative to the arm. The three stage reduction is really just one. This exact layout got me too.
Are you sure? yes | no
ohh yes, so in the end it should move to the base maybe, but that takes room..
unless you have a small stage in the other stepper pilar maybe... with just a m8 bolt (short). hmmmm
http://www.epenko.com/wp-content/uploads/2017/05/hellios2.jpg
Are you sure? yes | no
The drawing is 90% right. The pulley marked with "fixed" needs to be fixed to the base not to the arm. That way the idler pulley can use it to move itself around it. So instead of the last pulley the arm moves.
Are you sure? yes | no
I guess there is no way to do a 2 step reduction this way (other than moving the intermediate shaft elsewhere).
But a 3 step reduction is probably what's wanted here anyway. The first joint has twice the arm length to deal with when fully extended. And it only costs a bit of extra height of the arm and a double idler pulley.
Are you sure? yes | no
Is there a reason you can't use a live shaft on the shoulder axis? Connect the upper and bottom pulleys together, and stack the wrist belt/pulley on top of it on another bearing.
Are you sure? yes | no
I don't quite follow. Could you sketch something out?
Are you sure? yes | no
http://imgur.com/t6uwVz4
Does that make sense? The x's are bearings.
Are you sure? yes | no
So the middle pulley can slide up and down? Its not making sense to me yet.
Are you sure? yes | no
The middle pulley can rotate on top of a shaft that connects the upper and lower pulleys. Then the upper and lower pulleys are fixed together and don't both need to be driven by separate belts.
Are you sure? yes | no
Oh. Yeah that can be done but the new design works with a dead shafts and a bunch of duplicates of the same compound pulley idler.
Are you sure? yes | no
Hi Nicholas, i couldn't see the problem at first, but now i do.
Is there something someone can do to help you?
Are you sure? yes | no
I just need more time. :-) Luckily, I just graduated from grad school so there is an extra block of time. The current problem for the next week is dealing with all the things I ignored in order to graduated. Blah blah blah. Development should pick back up in a week.
Are you sure? yes | no
Awesome progress!! Keep up the great work!
Are you sure? yes | no
The files I included are for the version in all the videos. I really have solutions to all my problems it is just a matter of working all the solutions into one design in a way to flows.
The added complexity is three more pulleys and three more belts but I think it is worth it.
Are you sure? yes | no
Do you think you'll stick with 608 gears? and Belts (GT2 - 500mm)?
Are you sure? yes | no
I will use 608 bearings and GT2 belts. I doubt that any of the belts will be much over 400mm in the next iteration.
Are you sure? yes | no
hi! It looks nice but indeed a bit more complex indeed :)
So bonus with this would be: more precise, smaller printed pulleys
cons: more pulleys, more belts needed, a bit more complex, idlers needed (or just smooth parts)
Tomorrow i will look into the files. Thanks!
(if i see a solution i'll let you know offcoarse ;)
Are you sure? yes | no