It's been a while since I've posted anything but we've been busy here working on a new robot design. The main goals of the redesign are to make the robot more reliable and easier to build. The pushrod mechanism for the legs in the previous version put huge forces through a relatively small area causing the leg mounts to distort and giving the legs more give than is ideal. To fix this we've changed the design to use a belt drive and large carbon fibre tube for the main support. Following is picture of a prototype for the new leg design.
Another limitation of the old design was the minimum height it could walk at, this prevented the robot lowering its body to the ground which is useful for fall prevention as well as recovery. To give the legs more freedom they now are fixed on the side of the robot rather than under it as in the previous design. This design also simplifies the kinematics, and makes the design more efficient as there is now effectively one motor per joint.
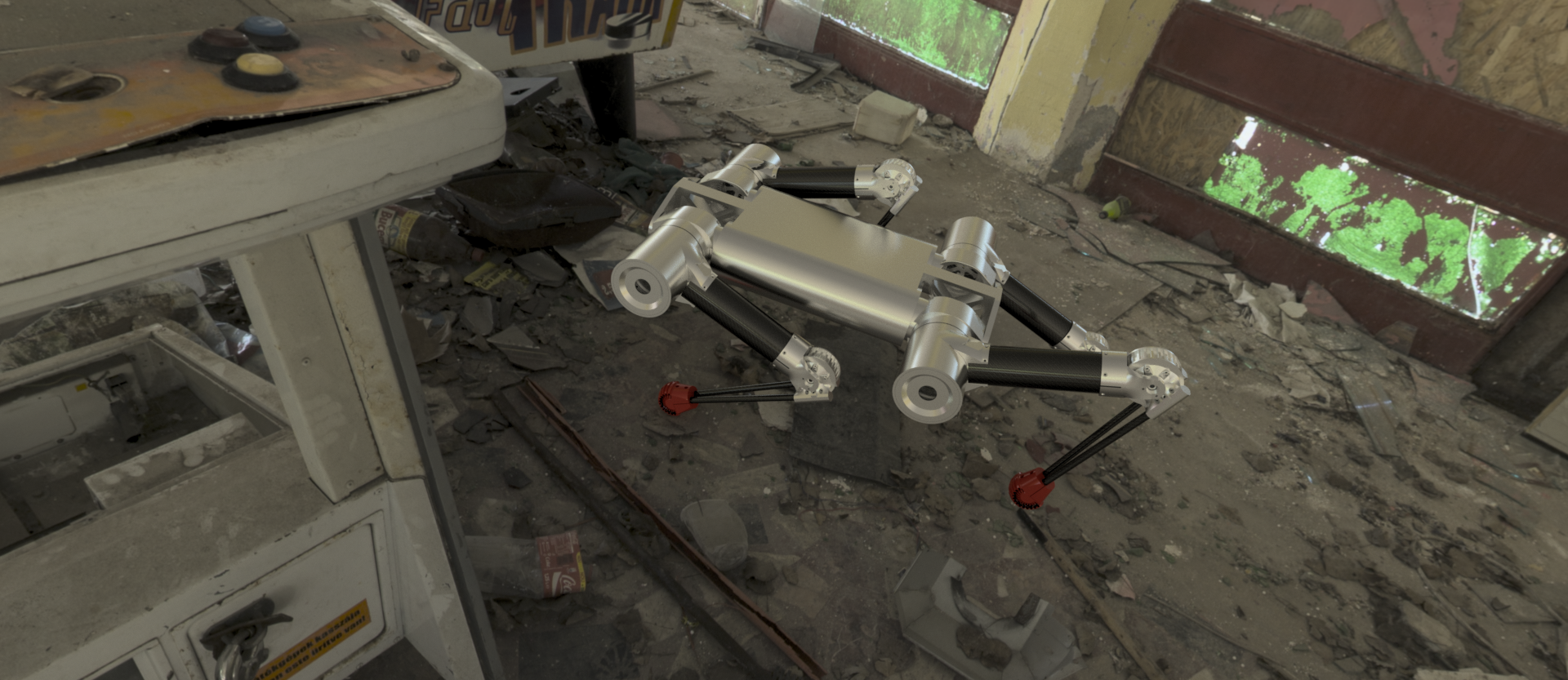
The old design was definitely a winter beast, the PLA used to build it and the motor controllers struggled to work on a hot summer day. To address this we're looking at using a plastic called ASA for the new build, ungraded motor controllers, and some new 100kV motors which reduce the power need when the robot is in a position requiring high torque.
Discussions
Become a Hackaday.io Member
Create an account to leave a comment. Already have an account? Log In.
Yes, I think the constraints of keeping the legs light, avoiding linked joints because when motors work against each other they waste power, and having a good range of movement do push towards this kind of design
Are you sure? yes | no
That new design looks very promising. A tube sounds like something that can be very rigid, so hopefully you would get rid of that wobbling. It's interesting to see how a lot of quadruped robots have recently converged into very similar configurations — looks like they are getting closer to the optimum?
Are you sure? yes | no