Problem:
• OSTEOARTHRITIS (OA) is often said to be a natural consequence of ageing and is one of the leading causes of disability and functional limitations in older adults
•The knee joint bears the full weight of the human body and the highest pressure loads while providing flexible movement, it is the body part most vulnerable and susceptible to osteoarthritis (OA)
• The growing number of cases is a heavy burden on the existing medical care system and the access to physiotherapist is quite difficult.
• While physiotherapists are able to work with the patient in their clinics and hospitals, They lack tools to supervise the patient's compliance to therapy and getting quantifiable data reflecting the performance.
• Long term real world gait would be essential to give the patient better care and can lead to better prevention and rehablitation
Background:
I, Vignesh am a final year engineering student from Chennai, India. I've always been into biomedical sensing and combining electronics and biomedical engineering. Inspired after playing Deus Ex: Human Revolution as a 16 year old, My adolescent my mind was blown away by the possibilities in front of me. Reading about the work done by Dr.Hugh Herr at the Biomechatronics lab and Dr.Rosalind Packard at the Affective Computing lab MIT media lab. I realized I wanted to work on wearable sensors, After seeing the unbelievable progress in Machine Learning for the past few years empowering doctors with Machine Learning for diagnostics is my current goal. I have seen my mom suffer from Arthritis a year back and seen her struggle to do her physiotherapy exercise. One instance she over did the exercise causing a minor knee complication. I was thus inspired to work on a solution to help my mom and many other OA patients to get better care and lead a more comfortable life.
Solution:
OrthoSense- Wearable multisensory knee sleeve to monitor Osteoarthritis
(Fig: Initial design of OrthoSense)
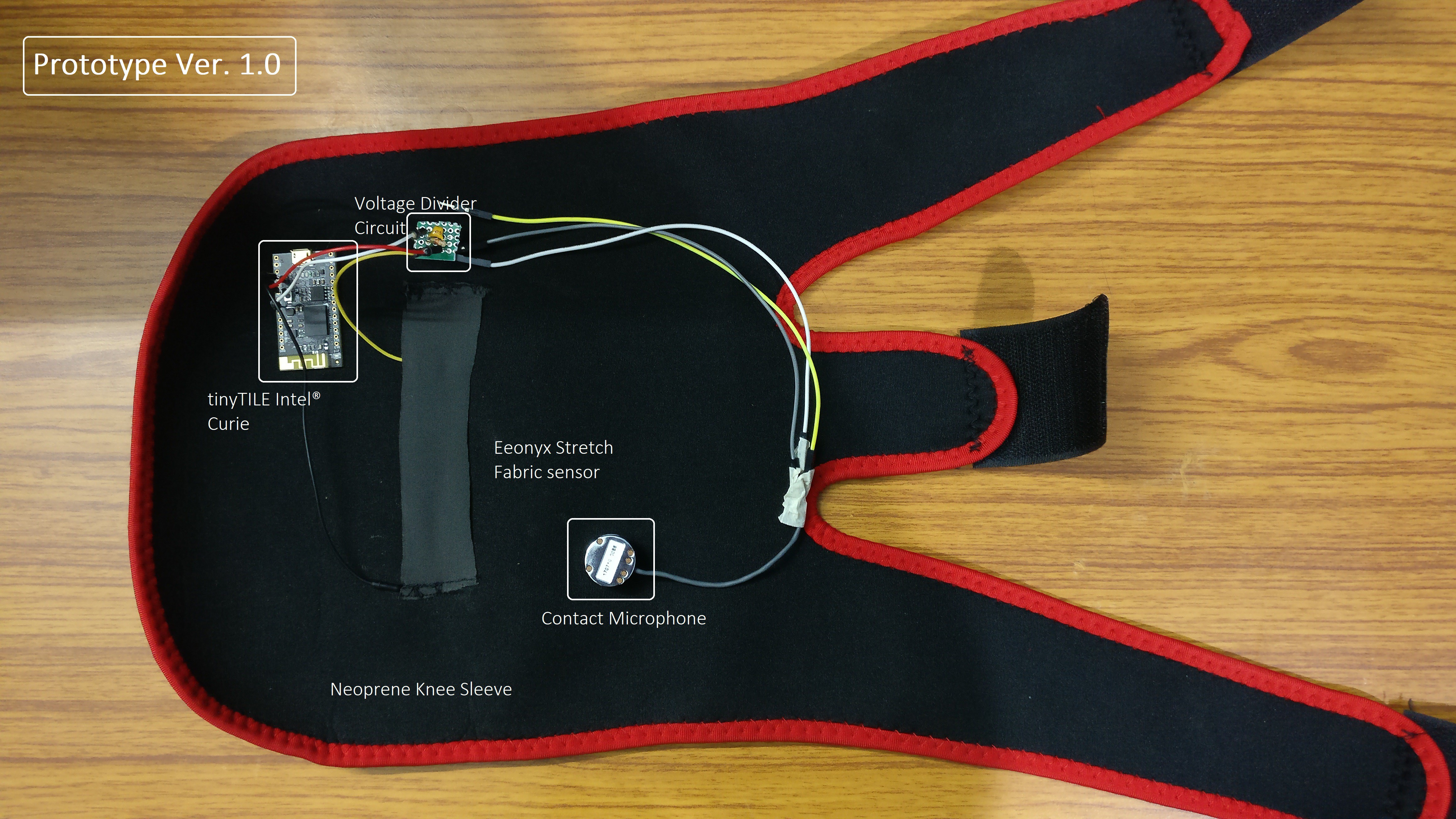
Our solution is a sensor enabled knee sleeve made with comfortable and non obstrusive fabric sensor for gait measurement(joint angle) along with other essential parameters of the knee joint for both the physiotherapist and the patient to monitor progression of the their joint ailment. Our solution is a low cost (85$) method for the patient to acquire better care for OA. The solution can either be purchased by the patient or be prescribed by the doctor in a rental model to out patients.
The patient wears the comfortable knee brace just as he is to start his daily physiotherapy exercise and pairs the device to his phone. After login, The custom rehabilitation exercise for the patient is loaded and friendly instruction animations guide the patient. A piezoresistive fabric sensor running through the knee joint measures the joint angle of the knee while the patient does the prescribed exercises. A 6DOF IMU records the joint motion data to give context to the other measurement. Finally, A tiny contact microphone picks up the acoustic emission of the knee bone giving insight on the nature of physical structure, soft tissue and most importantly the cartilage condition between the bone. This acoustic recording would provide cruicial information the patient's well being. The patient after exercise closes the session and continues on with their daily life still wearing the unobstrusive knee brace. The motion data and joint angle and acoustic are captured with the wearable during the patient's daily life when motion is present.
The data would be synced to cloud using the smartphone where classifiers would scrub through the data for valuable insights. The...
Depending on how much data you can collect you may even be able diagnose issues with joints before they become a problem.