I've decided to not run the bowden tube down the middle of the push-rod now.
With moving the extruder mount so it puts it's mass on the center-line of the pushrod, I would now have to cut a slot in the pushrod to get the bowden tube back out of it. This would weaken it excessively.
So I redesigned the push rod joint to allow the bowden tube to track along the outside and still have a relatively straight path. Also added some integrated wire guides so the bowden tube will be retained near the rod, but is still allowed to move.
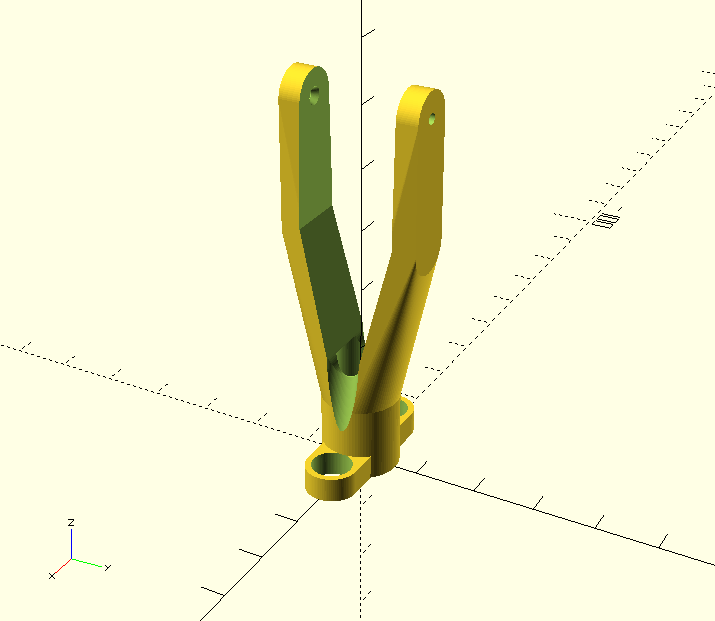
In case you are wondering why I'm putting the extruder on the push rod tube at all, it is so I can have a much shorter bowden tube.
This way I get the best of both worlds:
- A low mass end effector for faster acceleration/printing.
- A bowden tube short enough to still be able to print flexible filaments.
EDIT: I decided to offset the joint towards the fitting a little to give the bowden tube a straighter path.
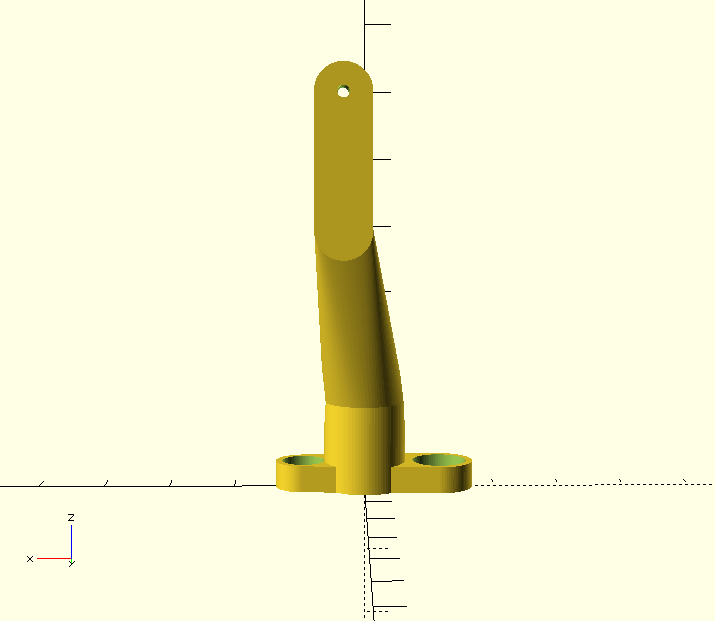
The push rod won't mind.
Printing.
In case you are about to comment about my obvious stringy issue, I disable retraction for nylon (and most structural parts actually)
My recipe for the strongest structural parts:
- Disable retraction and increase non-printing movement speed to maximum. A linear delta printer helps here as my maximum is 500mm/sec.
- Over-extrude until you have obvious surface artifacts or your extruder skips. Somewhere between 5% to up to 20% is right. All your dimensions may need adjusting...
- Print as hot as your material/hot end allows.
- Disable cooling, if you can. If your parts actually start to sag due to excessive heat, slow down instead of using a fan. Cura does this for you.
Discussions
Become a Hackaday.io Member
Create an account to leave a comment. Already have an account? Log In.