Most things with v4.1 of the end effector are working out well.
The thickness of the inside surface was tweaked so a binder clip spring holds the hotend firmly in place by slotting into the groove below the groove mount.
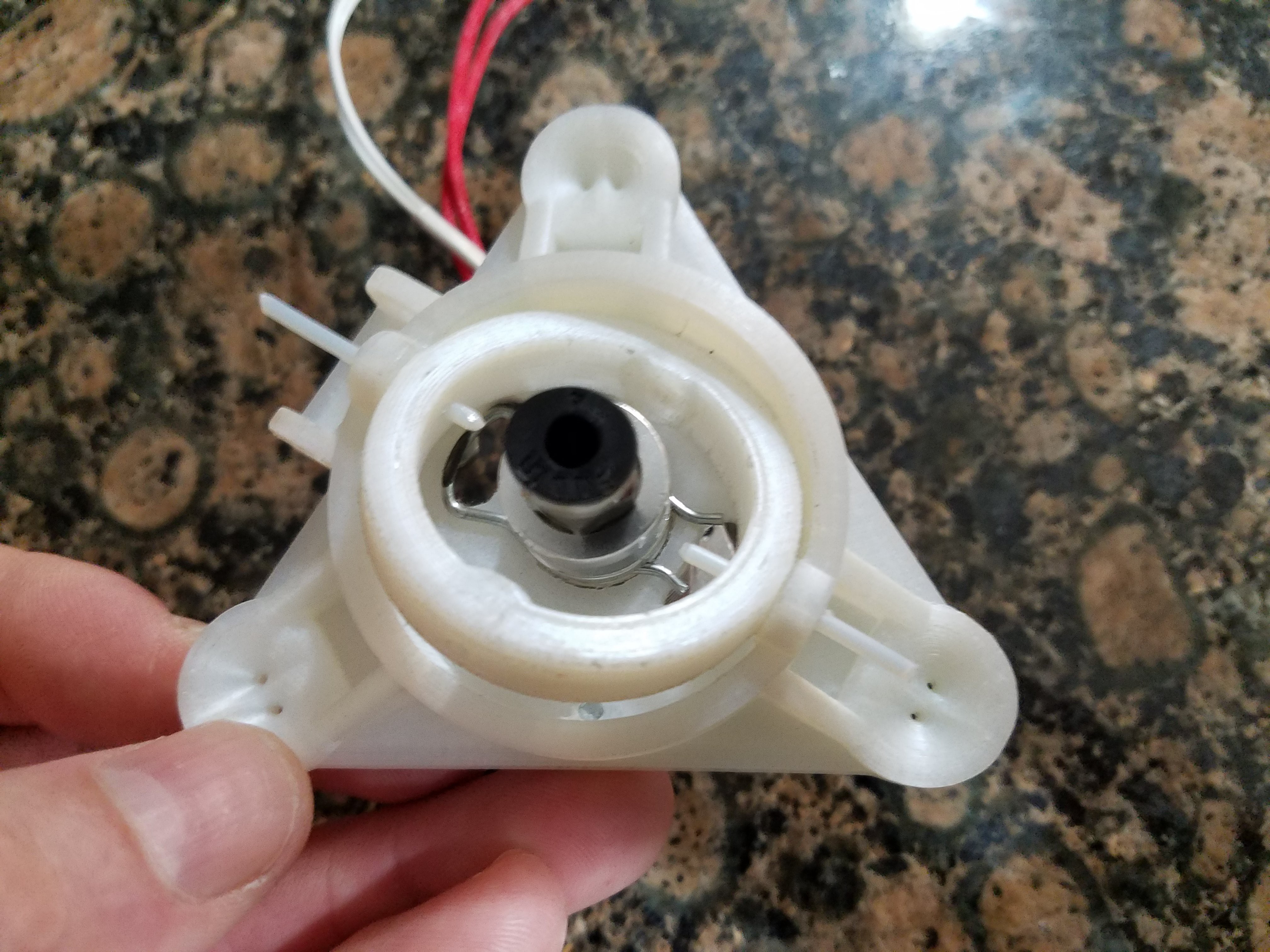
So now the heatsink sits flush on the bottom.
Added the three screws you see for leveling.
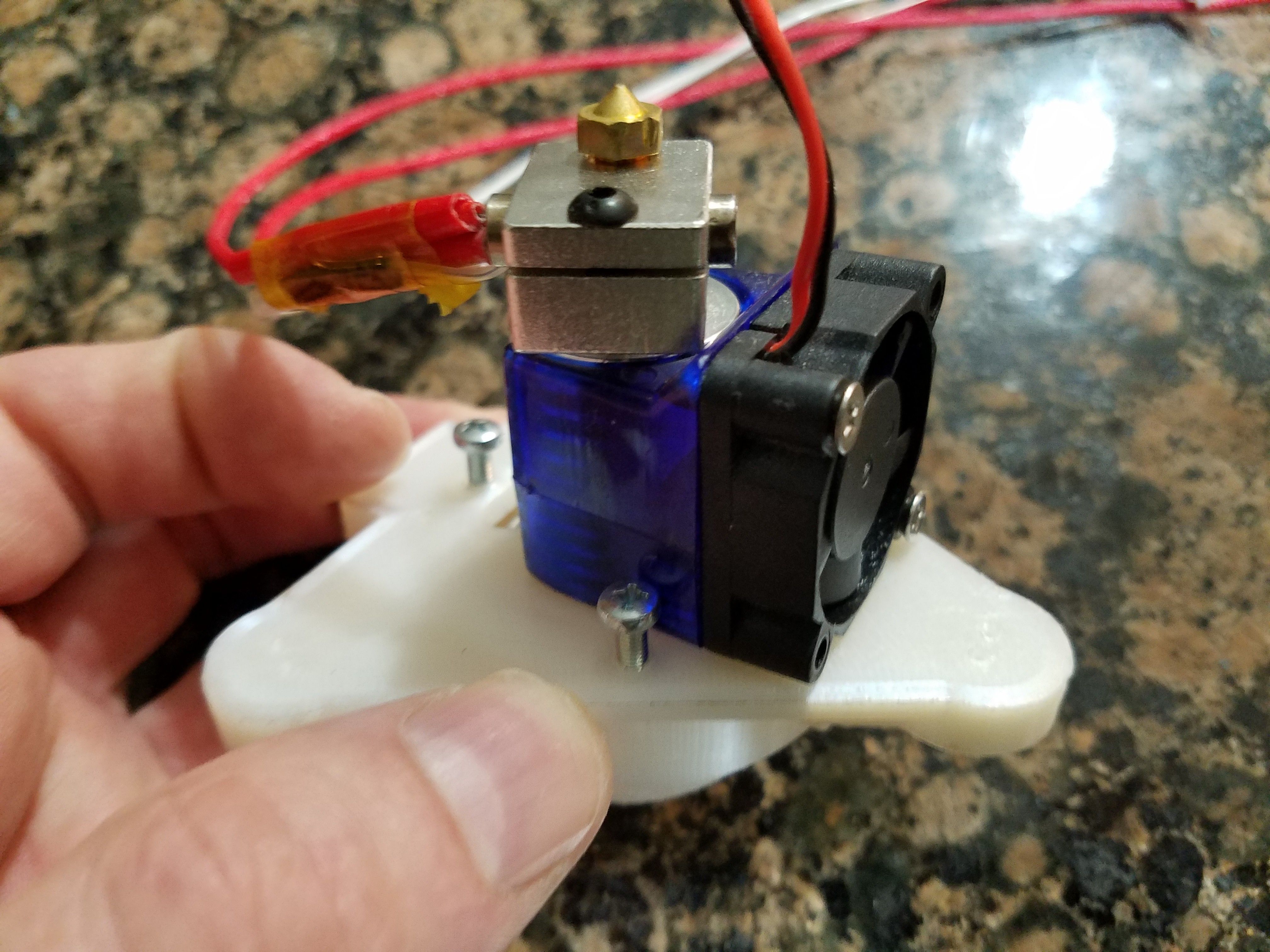
But printing the push rod joint, which was working well before, now is bumpy and brittle.
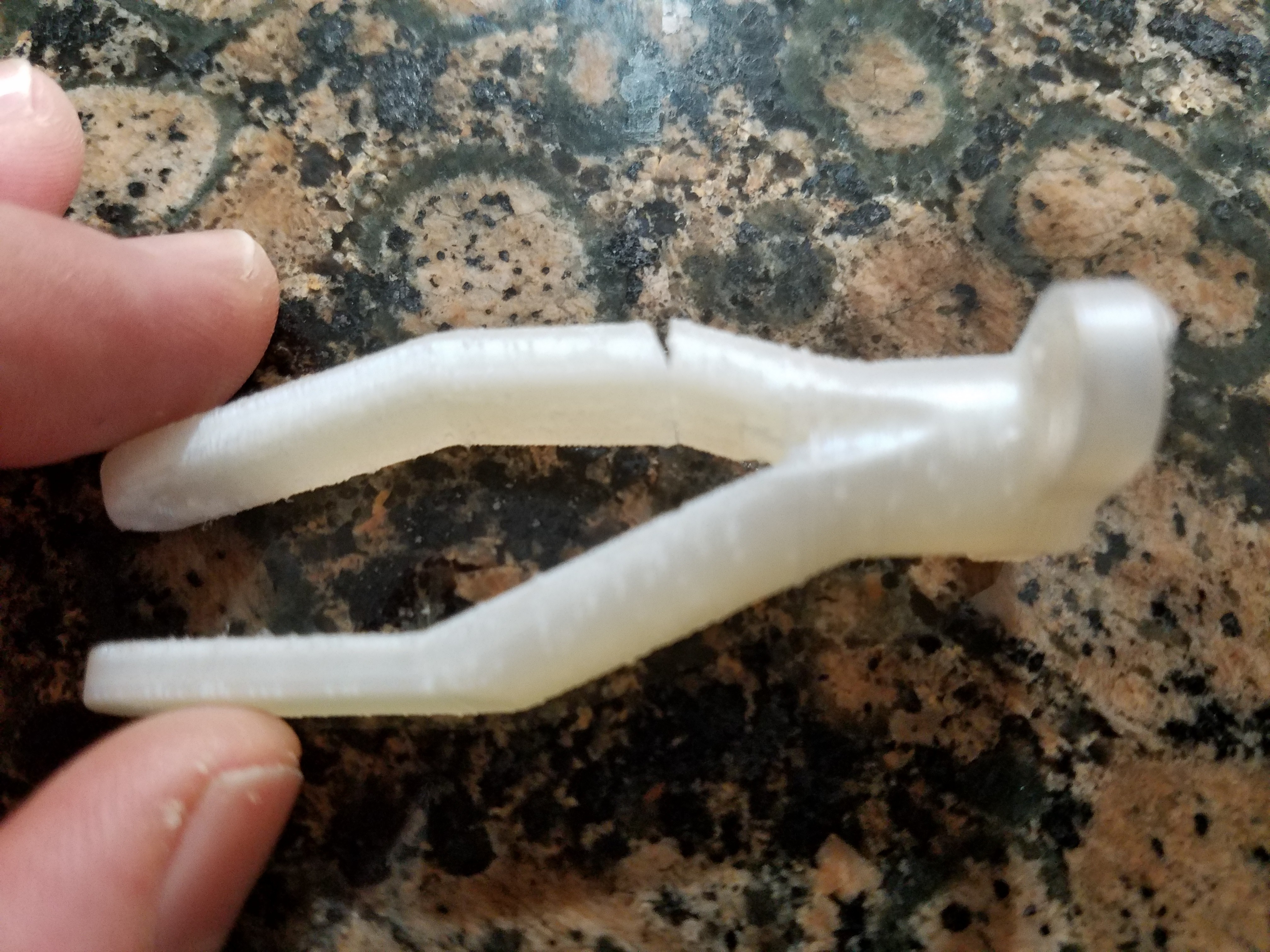
Lost the settings I had used before, so experimenting.
My nylon filament has the perfect moisture level (12% on a humidistat) and is printed right from its own dedicated airtight container so that's not it.
Printed it at 250 to 265C, bed starting at 80C, .4mm nozzle, .1mm to .2mm layer height, 15mm/sec to 80mm/sec.
If you have any advice to lend here, feel free to drop it in the comments.
EDIT: I think I may need to go hotter. Printing fast seems to work better for the layer adhesion which I think is the result of having more latent heat in the part.
Drying my filament again just in case, and I'll give that a try.
EDIT: Raised the temp to 280C and with dry filament all my issues went away. Contrary to popular opinion though, cooling was needed to go fast. It took 30% fan at 72mm/sec with 10 second layer threshold.
Discussions
Become a Hackaday.io Member
Create an account to leave a comment. Already have an account? Log In.