Since embarking on the 'WiFi AC controller' project quite a few months ago now, I have learned more than I ever wanted to know about building (climate) control, and seen the scope of what had seemed like a simple project at first balloon in size as a result.
Instead of just controlling the fans in what I later learned are called Fan Coil Units (FCUs), the need also arose to control the valve(s) for each FCU, and naturally the backend service should be able to read out and switch the system state for a segment from heating to cooling and back.
As a result I ended up with what I now lovingly call the Building Management and Control (BMaC) project, which in graphical format looks somewhat like this:
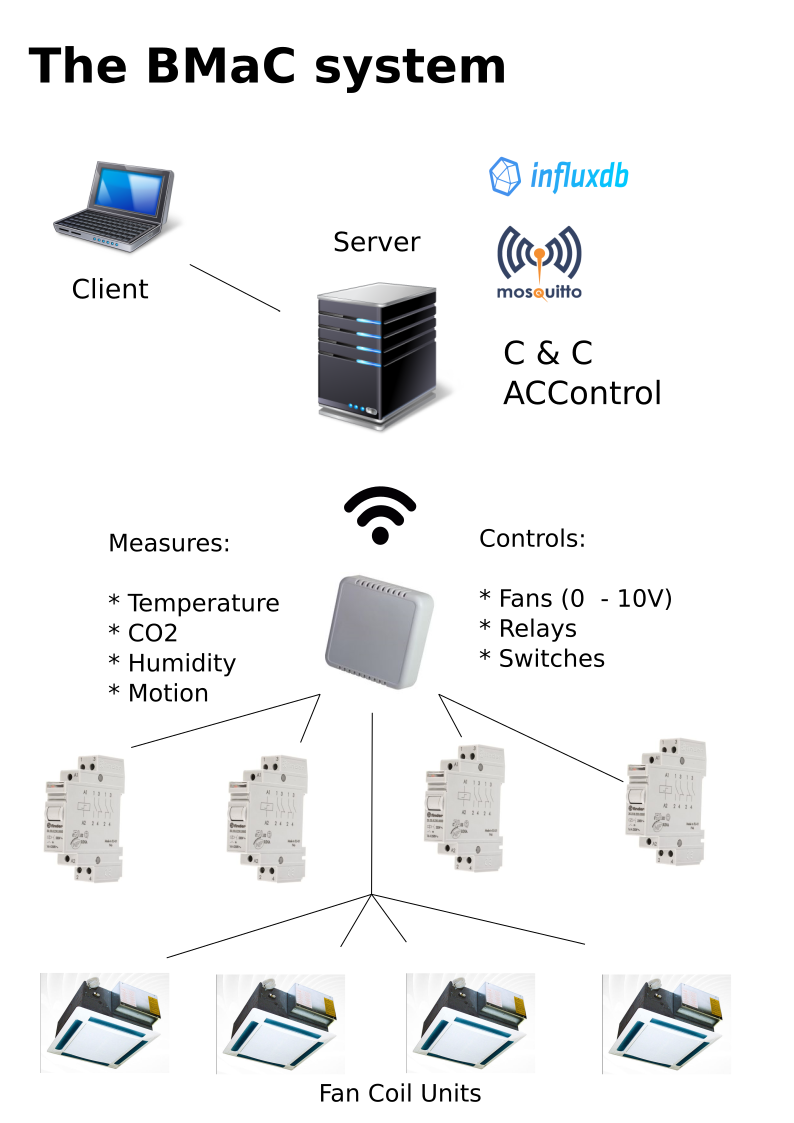
Slightly more complex than just having a microcontroller or similar driving a fan, I guess.
As illustrated in the above graphic, the idea is that one node (CMN) can control up to four FCUs and the relays that control the valves while also providing real-time sensor data on temperature, humidity, air pressure and CO2 levels. Since these sensors placed in the midst of the area that is being climate-controlled, the backend service (ACControl) can make rapid and accurate changes to fan and valve settings due to very short thermal feedback loop.
Because I was running out of GPIO pins on the ESP8266 after adding the i2c and PWM (and motion) functionality, I decided to create an i2c-based GPIO expander device. This took the form of an MCP23008-based design, along with an ULN2003 and some loose components for flavour. Today I added a PCB design for it to the project page.
This i2c relay controller board looks like this:
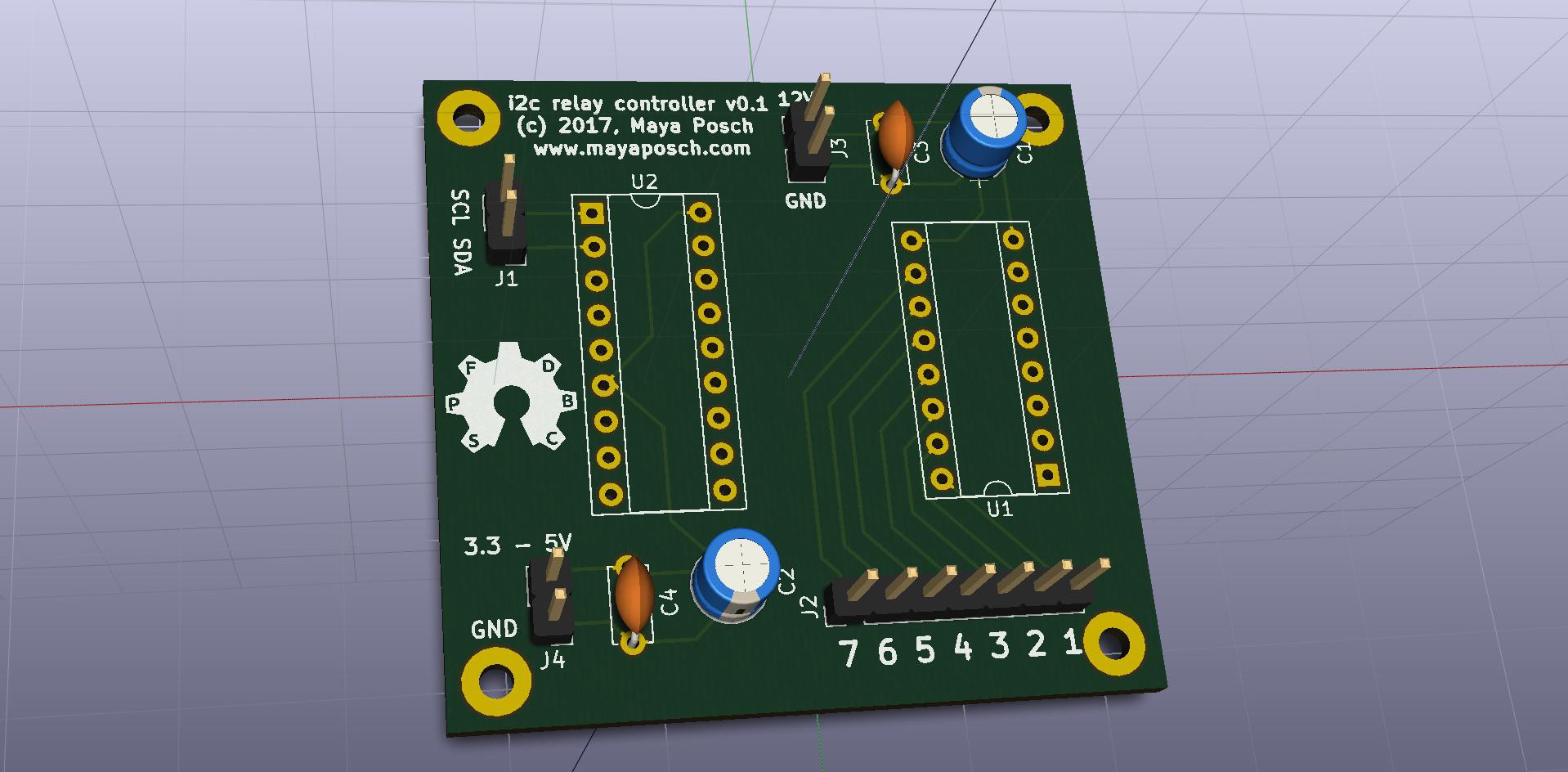
It's a positively tiny (48x46 mm) board despite being based on a socketed PDIP design and using only through-hole parts. Since it's supposed to drive 12 VDC relays, I figured that a bit of added robustness and ease of replacement (blown ULN2003 chips or such) would be a bonus.
A perfboard-based version of this design currently runs inside the small BMaC system here at the office, driving three relays which in turn control the 24 VAC thermoelectric actuators on the respective valves.
The final part of the BMaC system is the latching relay switch, for which I will release the design as well. This component is only needed in 2-pipe FCU systems, however.
The software for everything can always be found on the GitHub page linked from the HaD.io project page.
As mentioned in a previous log already, I recently got laid off, so that I won't have the opportunity to further develop the small BMaC system at this office. I am however definitely still interested in developing this system further, either as a hobby project or as part of my next job.
Discussions
Become a Hackaday.io Member
Create an account to leave a comment. Already have an account? Log In.
Totally blown away about how you can start looking into a small problem and end up designing a full scale BMS. Well done
Are you sure? yes | no