Design Process
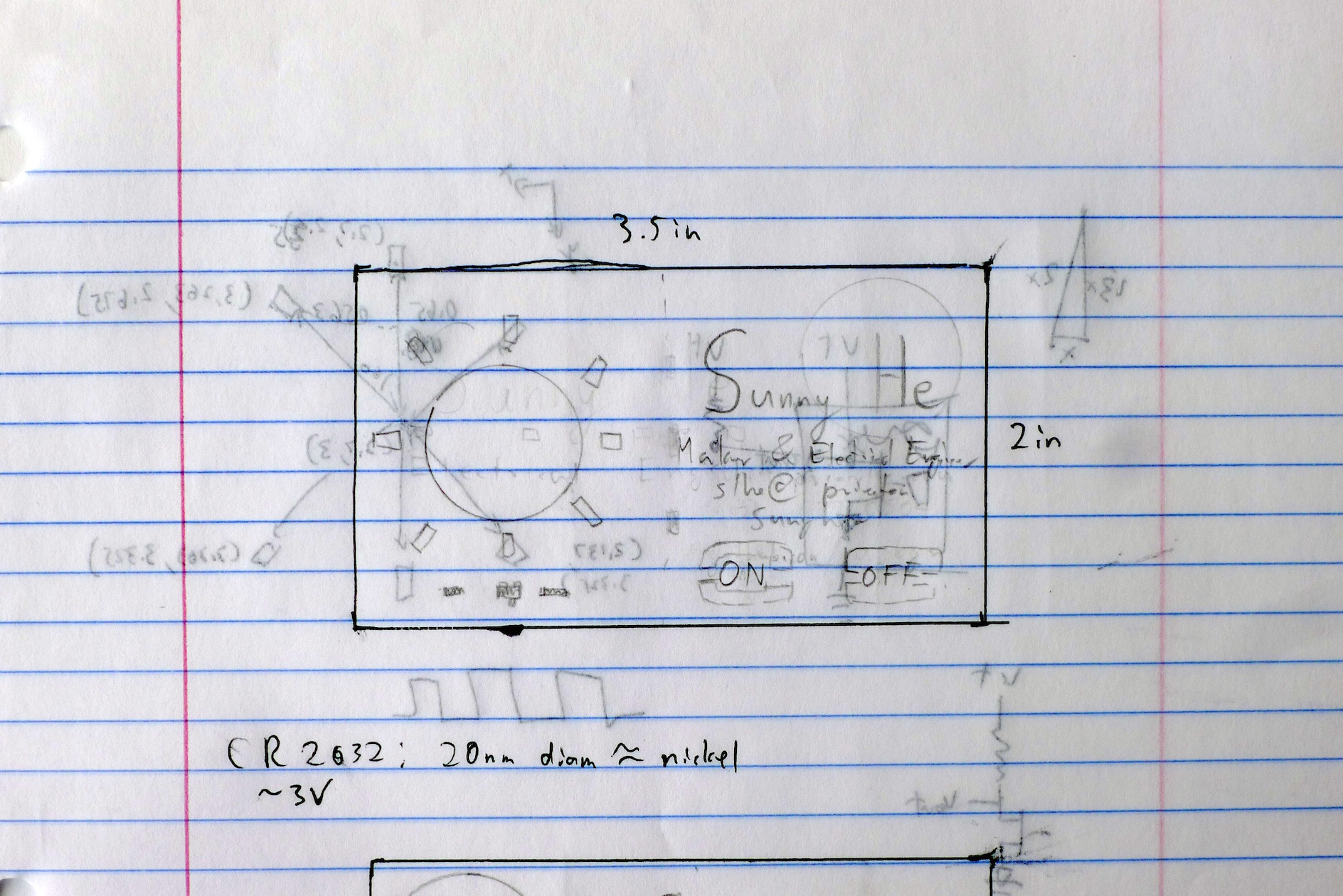
I performed the inital brainstorming and rough design on paper, mocking up different options with pencil in a ink 3.5x2" rectangle. I had the idea for the MOSFET-based touch circuit from earlier work, but there were some special design contraints to work with for this board.
- Size: The board must be within the normal business card size of 3.5x2", and be low-profile enough to carry around
- Components: While surface-mount components were mandatory to reduce the thickness of the card, I didn't have access to a reflow oven. To ease hand-soldering, all components had to be at least 1206.
- Simplicity: Use as few components as possible and avoid IC's.
- Clarity: My name and contact information had to be prominently featured. This is a business card after all.
- Aesthetics: It had to look good.
I eventually settled on a star formation of LED's arranged around the battery, taking advantage of the dominating circular form to evoke a classic star or "sun" shape.
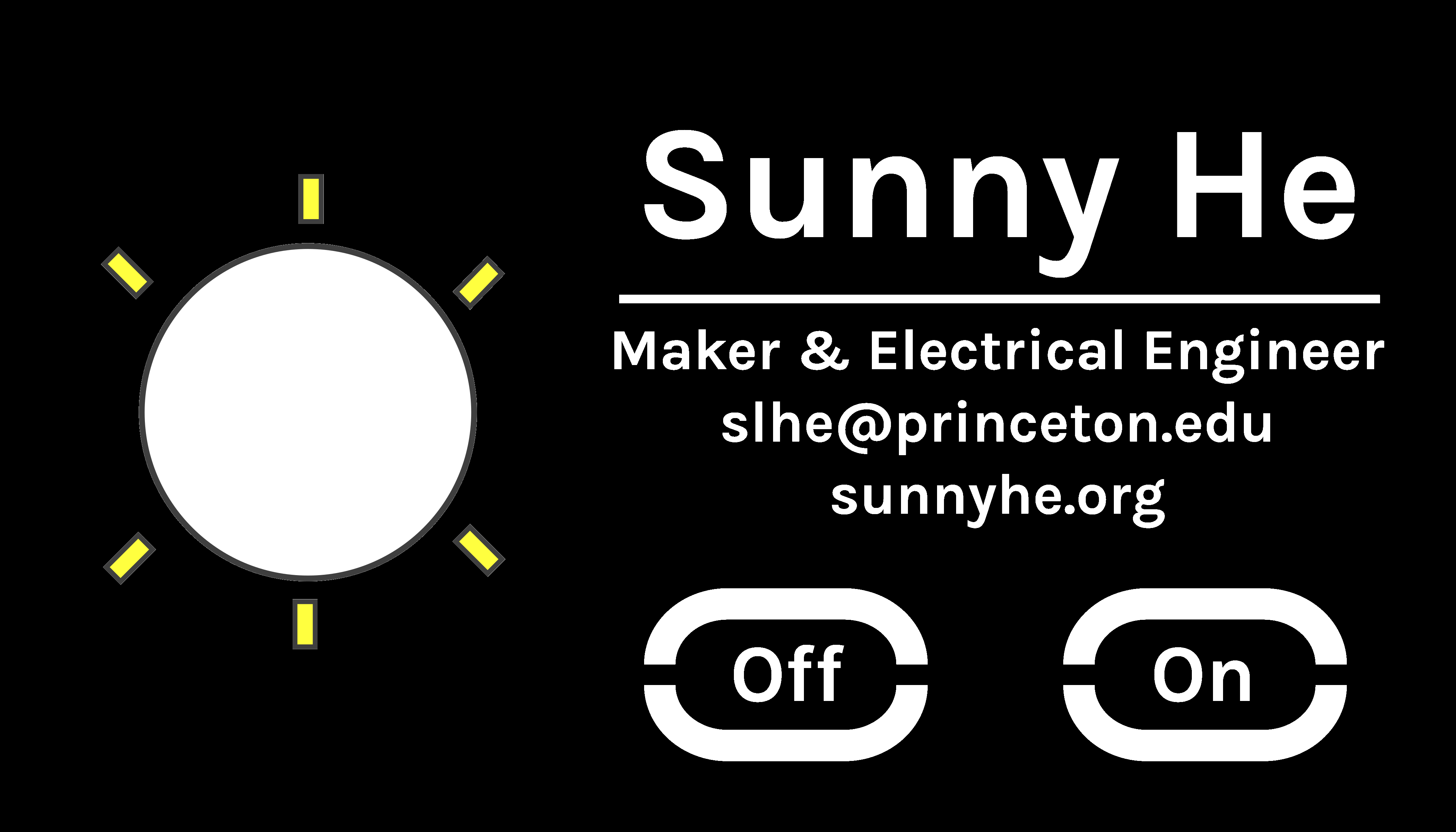
Next the design was finalized in Inkscape as an SVG vector file. I used the Google Fonts tool to find the Karla font used for all the lettering.
PCB Layout
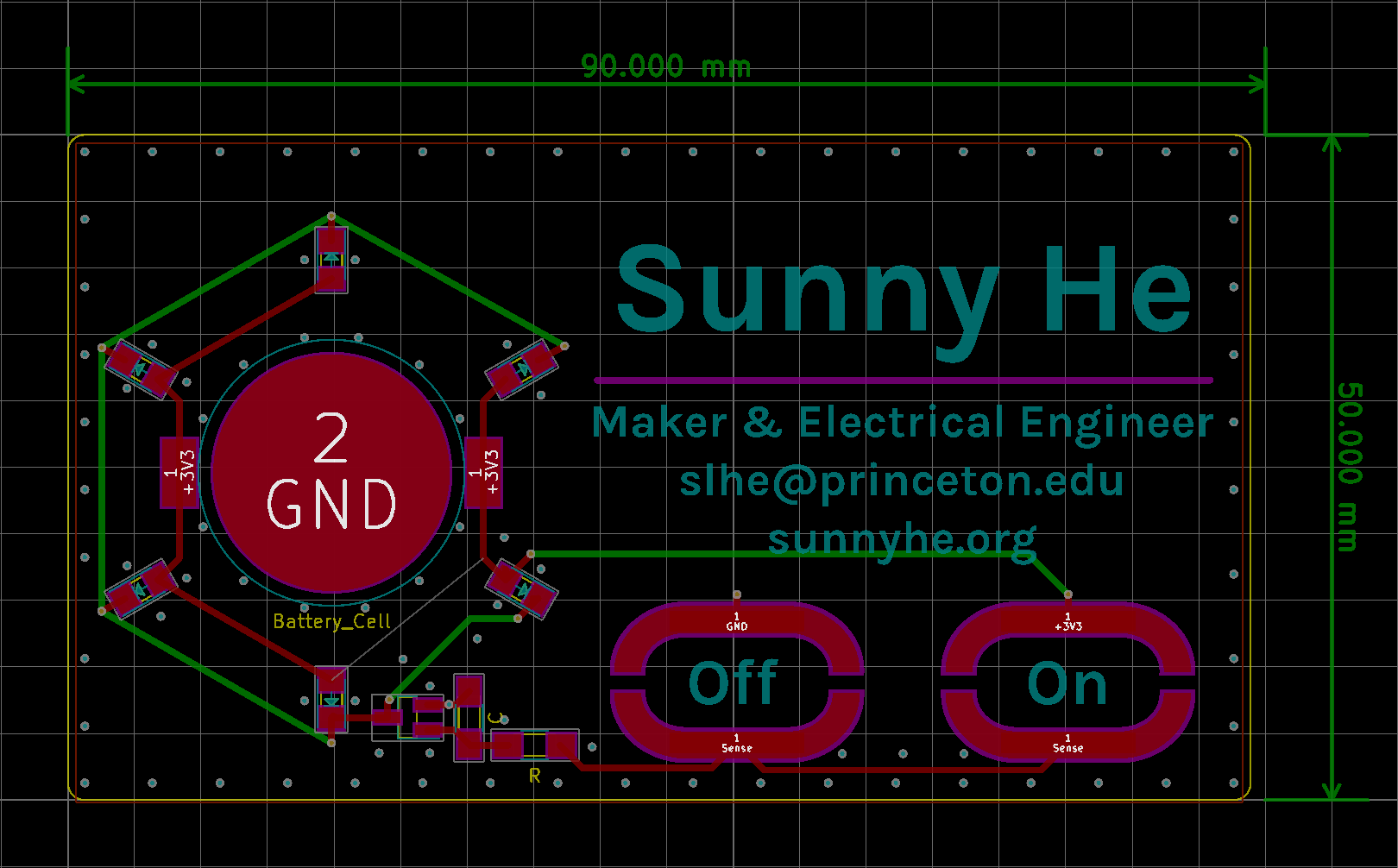
The rest of the board layout was performed in KiCAD. Silkscreen elements were directly converted into KiCAD components using the svg2mod tool. The touch pads were individually made into their own components in order to properly define pads and solder mask. The image of the schematic on the rear was created by plotting an SVG representation of the schematic from KiCAD, then cleanup and conversion to a PNG in Inkscape, followed by importing via the bitmap2component tool in KiCAD. The svg2mod tool had difficulty with the thin lines in the schematic, and bitmap conversion proved to give a much better result. I also resized the board slightly, to 50x90mm.
Manufacture and Assembly
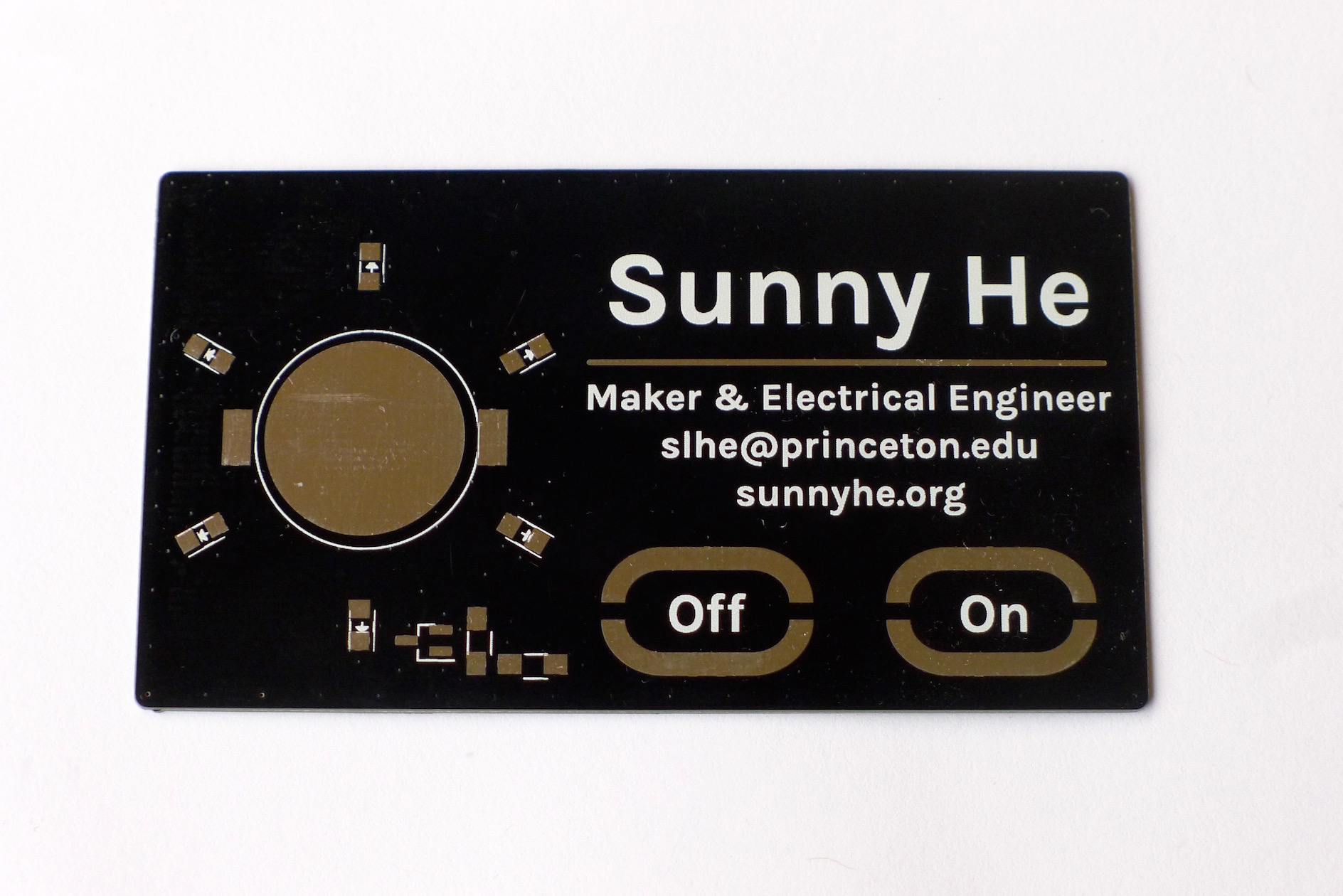
I ordered ten boards from Elecrow's PCB service, choosing a black soldermask and 0.6mm thickness. With DHL shipping ($17.04), the total price came out to $28.54. Elecrow has a nice habit of sending extra boards, so I ended up with 11 boards at a cost of $2.59 each.
From there on out, all the boards were hand assembled. Because my hands are absurdly unsteady, I used Scotch tape to position and hold down components before soldering. Even though this was probably an extreme ESD hazard, most of the components were simple passives anyway and everything worked out alright. In hindsight, assembly took so long that it might be worth subcontracting assembly out to a small batch company for future runs.
Nice project! I designed some PCB business cards which just arrived today. I'll be posting a project soon, mine is more complicated but I really like the simplicity of yours. Have you considered a resistor to limit the LED current? Clearly you're using the source impedance of the 2032 to limit the current but adding a small resistor in series with the paralleled LEDs would substantially increase the battery life.