"I think I want to build an eSkate.."
"Why?"
"Because I think the commercial versions are too expensive and don't pack enough range for actually being usable for commuting"
"... great! I guess ..."
If you had a conversation like that if your life, you're very likely to have one of these spot welders somewhere in your workshop. Spot welders. Why a spot welder?
It's simple:
With a spot welder your can weld metal to metal without actually adding material. You just melt both materials and mix the viscose metals into one object. It's actually that easy.
Spot welding comes in two variants (as far as I know):
- Welding from opposing sides (like used in the automotive industry)
- Welding side by side (like used for almost all battery packs on the planet)
When I started researching material for electric skate boards there were two types of people. One is using lipos straight from a hobby store and one is going the extra mile to use 18650 or bigger batteries and make their own packs. Both works well. In fact, it seems easier to identify shitty lipos from HobbyKing than shitty 18650s even from sources like Amazon or ebay because people know them already and there are not as many counterfeits.
However, people using the 18650s are convinced it's the better battery technology. They are widely used in laptops and Tesla's and many other electric vehicles out there. So why not use genuine 18650 cells and make a great high power pack? Because you need decent tools to make the actual pack. Like a spot welder, a long strip of Nickel as well as a decent battery management system to keep all individual cells balanced. Always.
So, ok. What do I need for making a spot welder:
- A high power transformer that can be converted to a spot welder
- A switch able to switch 15A 120V reliably
- A fuse would be great
- Something to time the actual welding. Manually works as well but I'm an embedded systems engineer
- An enclosure so that the spot welder can be on my desk as well as being transported when I move
- VERY thick wire that allows enough current without much loss and without getting hot in the process
- Some type of electrodes that transfer the current into the material to be welded without loosing integrity due to overheating or even get welded themselves in the process
All of the above is relatively easy to obtain, starting with the transformer.
Most people salvage their transformers from old microwaves. People also say that it should have more than 1000 Watts. I found the latter to be untrue. The microwave I stripped was only 750 Watts and the current seemed to have been limited by the use of magnetic shunts inside of the transformer that I could remove. It turns out, my transformer runs at 14.5 Amps during welding and at 4.5 Amps when free flying after removing the magnetic shunts.
P = U x I gives us 120V x 14.5 A = 1.740 Watts! Geeeeezzz! Far more than enough!
My configuration has only 2 windings on the secondary coil and an unknown number of windings on the primary coil. However, what I do know is that 120 VAC get transformed down to 2VAC! That's a factor of 60!
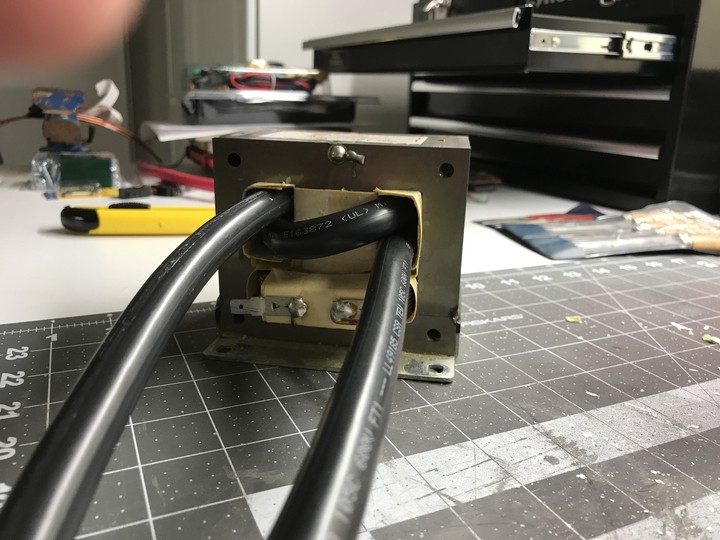
Considering that the primary coil draws 14.5 Amps during welding, this should translate (x60) to 870 Amps on the secondary coil during welding.
If you look at the wire you are supposed to use for this type of current you will end up with something that is essentially unusable and unobtainable. Not surprisingly, most people just use some "thick wire" to build their welders and of course will never achieve these currents during their spot weldings. The internal resistance of the wire itself is just too high and the voltage will break down.
However, I was able to acquire "1 AWG" which is rated for a max current rating of somethingsomething 200 Amps continuous. That seems ridiculously low considering the thickness of the material and having worked with RC cars before where something like a Mamba Monster Motor/ESC has a burst current of ~1000 Amps.
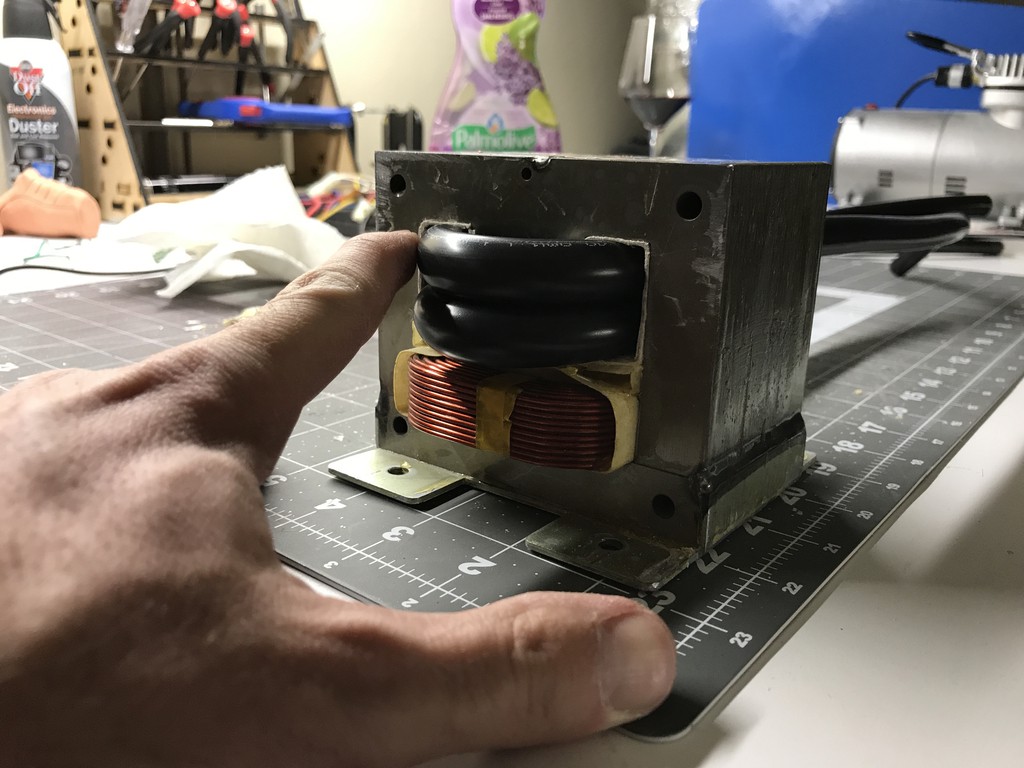
From my brief tests I can say the following: The wire does not get hot and I can weld 0.75mm steel plates on top of each other using simple copper electrodes and side by side welding.
The ratings mentioned in the standards are designed for continuous current. Spot welding utilizes very short bursts of current going through the material to weld it. A voltage drop is not important. Having the wire increasing the temperature by 0.1 deg C per weld is neglectable even when welding 100 batteries together. That's likely why most people use thick speaker wire or jumper cables to build their welders.
My first test looks like this:

Discussions
Become a Hackaday.io Member
Create an account to leave a comment. Already have an account? Log In.