After being stalled by the automated tracking for over 8 years, the decision was finally made to make a remote control for panning the camera manually. 3D printing finally enabled the custom bearings. The remote control has 8 functions. 4 timelapse movements are enabled by holding a button during power on. 4 smooth panning movements are performed by the buttons after power on. The camera is panned by a brushless gimbal motor.
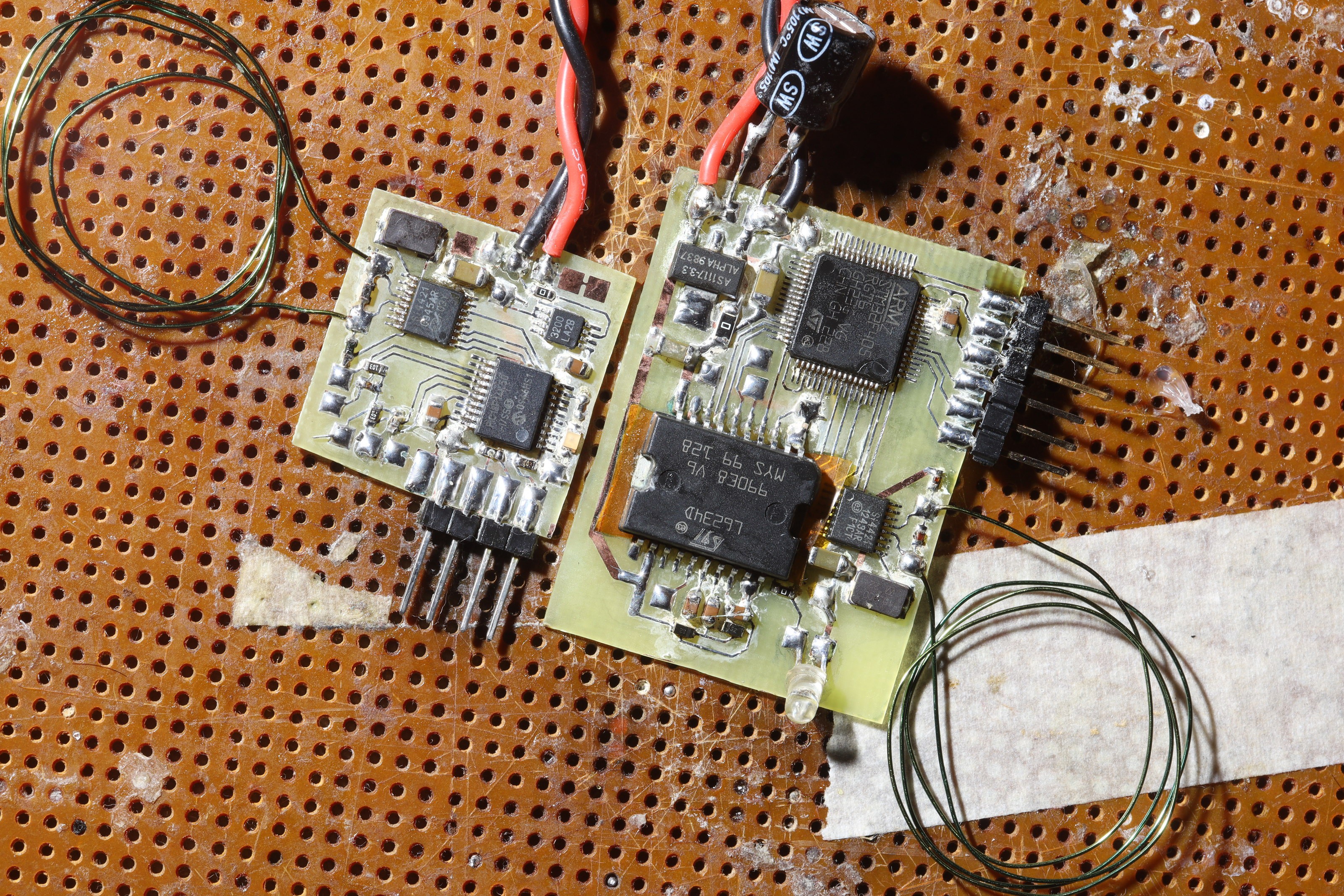
It was after laying this out that the lion kingdom realized how much its philosophy changed in the last 20 years. An ARM is seriously overkill for controlling a 3 phase motor & receiving packets from the radio.
20 years ago, a lion would have used an 8 bit PIC, developed the routines required to generate 3 PWM waveforms in software & receive packets from the radio. It's just so much easier to get that working on an ARM & there are enough spare ARM chips in the apartment, it's no longer worth the trouble. If it was 20 years ago & lions had only PIC's, it would have been done the old way.
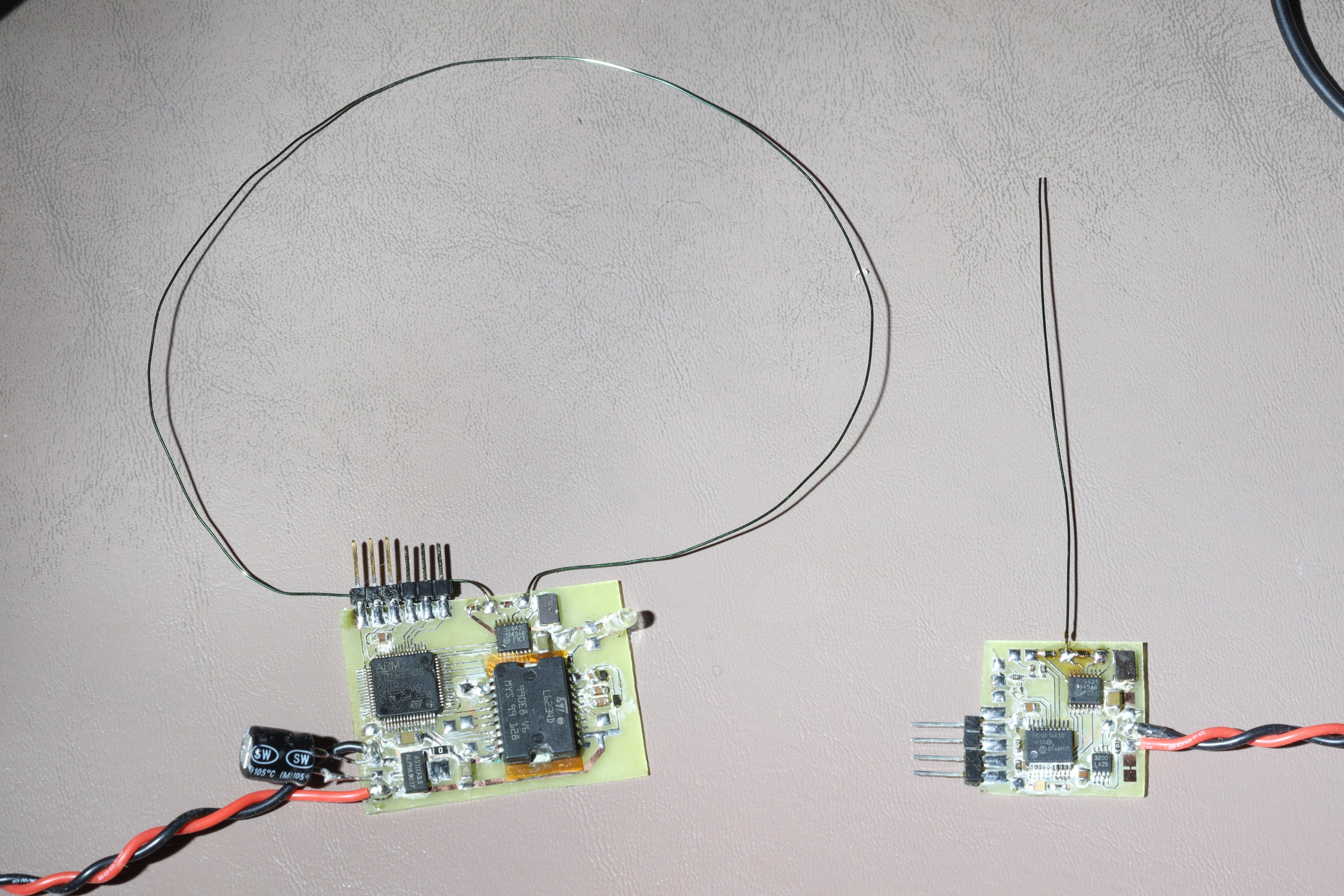
Then, after playing with the spectrum analyzer, it was revealed that the giant loop antennas lions used for the last 11 years are unnecessary. They were seen as a way to use balanced antenna pins without a balun. In reality, a monopole gives good results with just a 16nH inductor shorting the outputs & a 100nH inductor in the 3V supply position. If a loop antenna is used, it doesn't need the 16nH inductor.
Lions had always based their usage on the balun circuit in the MRF49XA datasheet & never tested the signal strength of different antennas, even with the RSSI functionality built into the radios. They just spread the radios apart on a golf course until they stopped receiving.
The extra parts for the MRF49XA may have been to match a 50 ohm load. When this part was rebranded later as the SI4421, the new datasheet only showed a loop with no inductors, but lions never saw it. They even left out the 100nH inductor that supposedly chokes the RF from entering the 3V rail. The 100nH would only be needed for transmitting & FCC certification. Not sure where the 16nH came from. The MRF49XA datasheet showed a 22nH.
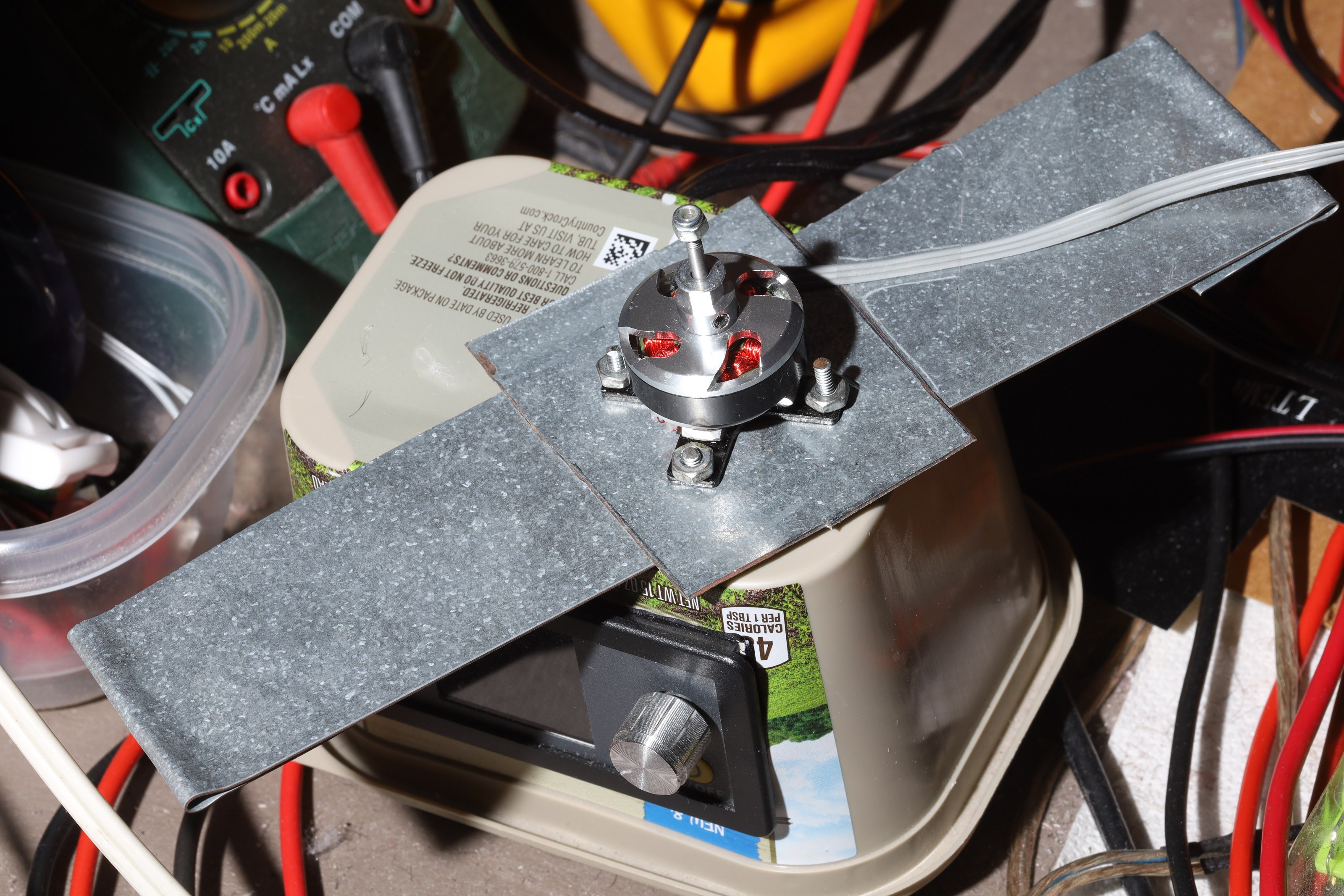
Sadly, 3D printing can't form metal so we're still stuck with ugly metal motor mounts.
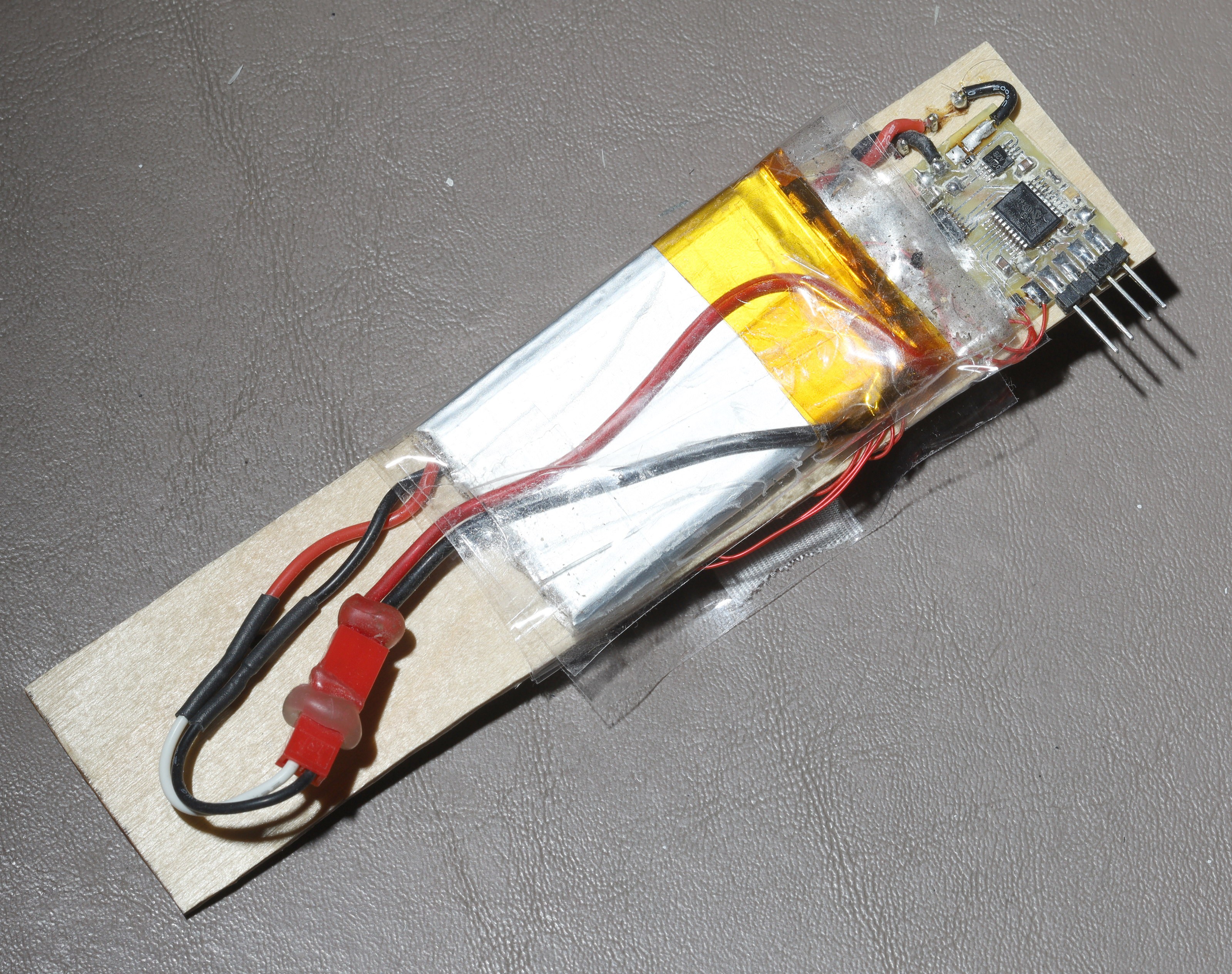
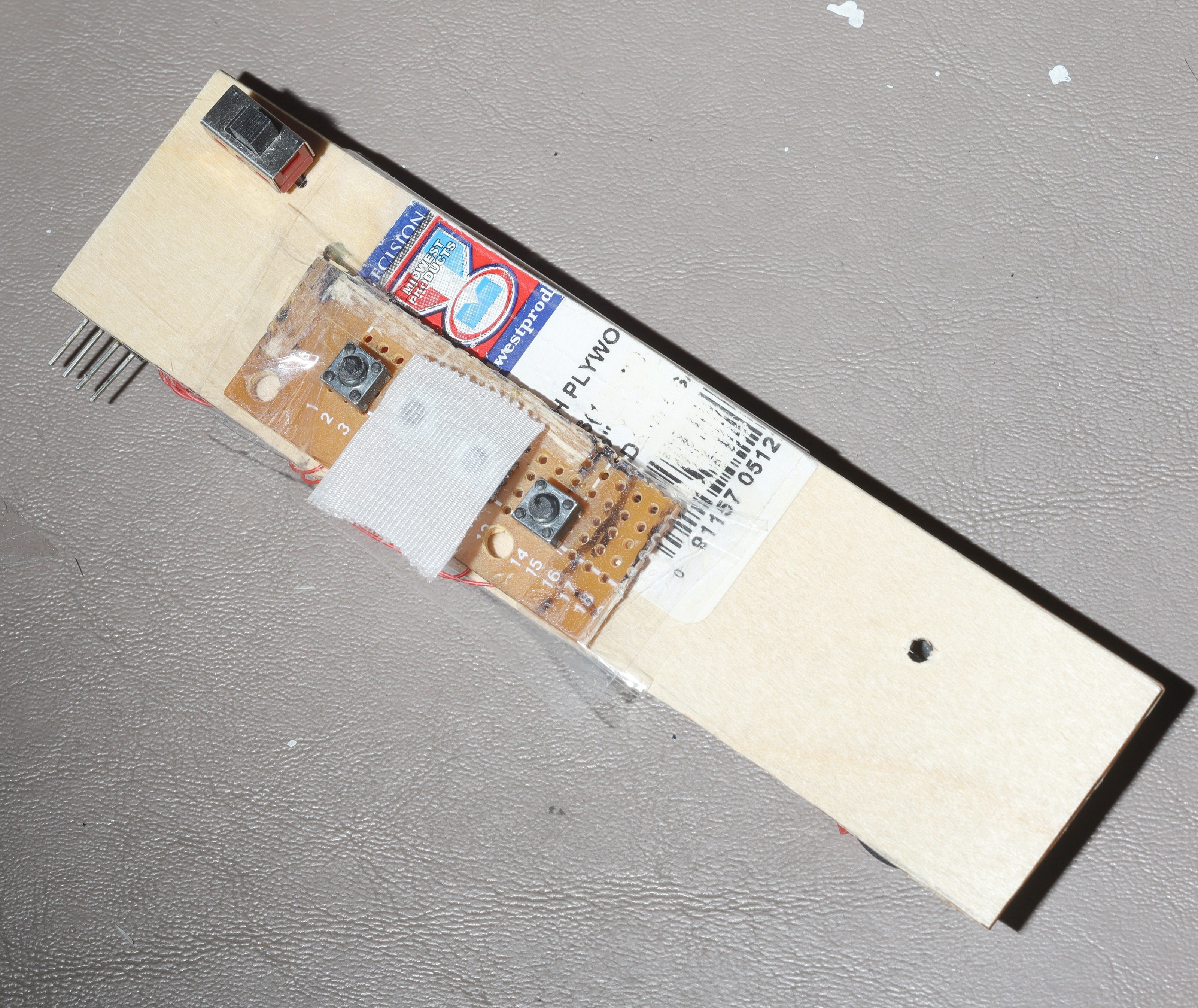
Hopefully the last plywood remote control lions ever make. This one proved without a protrusion, lions tend to hold it like a TV remote instead of a gun.
What allows lions to point guns is thumb pressure. Otherwise, they need another protrusion to grab. The boosted board remote has a thumb wheel to keep it pointed like a gun. Lions have used a pinky protrusion for 7 years to free up their thumbs. It's not the most comfortable.
With that discovery, the waterproof version is probably going to be as similar to the plywood as possible.
The remote continued the tradition of 4 steering buttons. Lions settled on this design 3 years before the boosted board remote became popular & indeed long before there were any electric skateboards. It's worth reviewing how modern skateboard remotes work with some stills from https://www.youtube.com/watch?v=kXDz
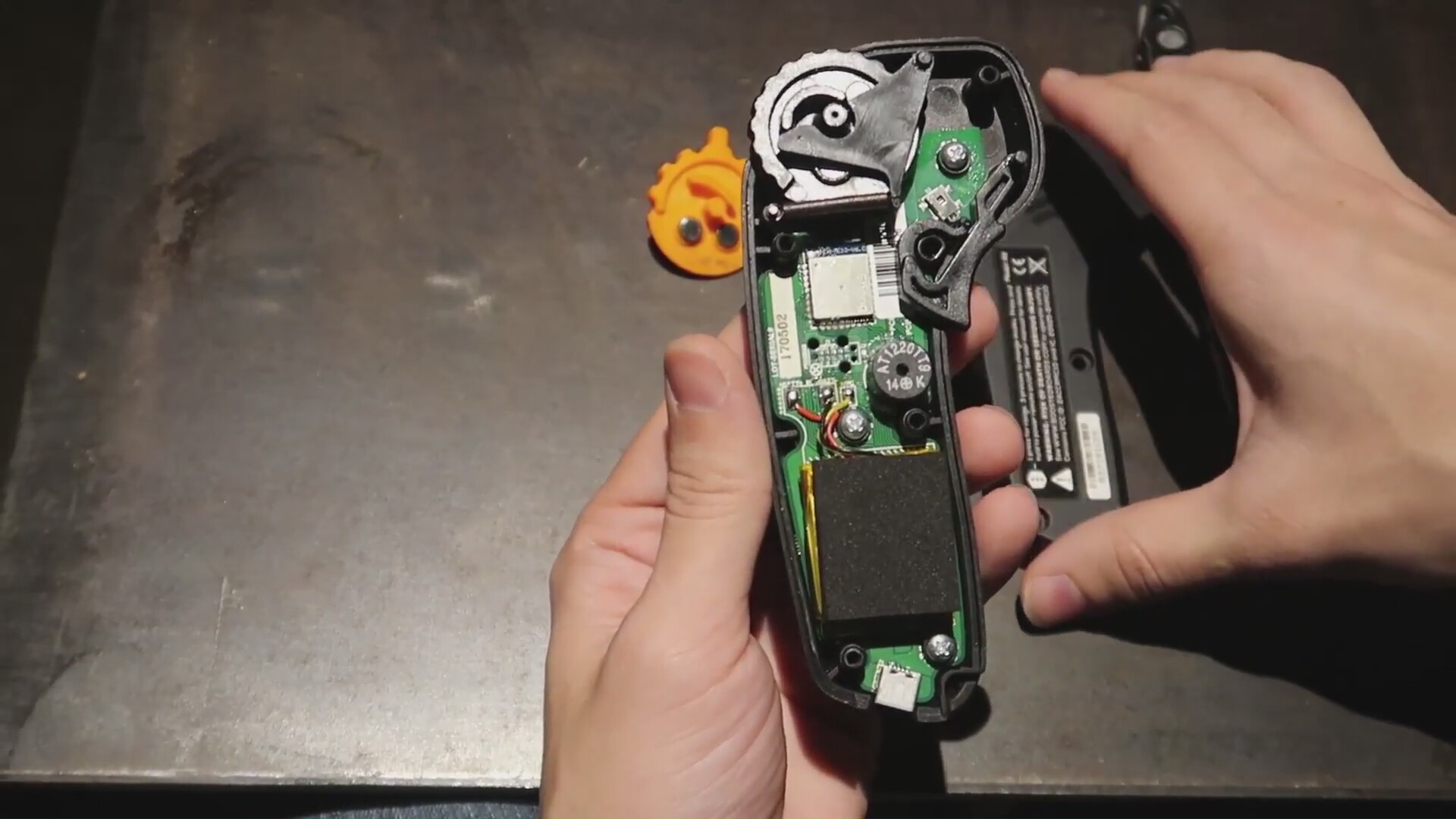
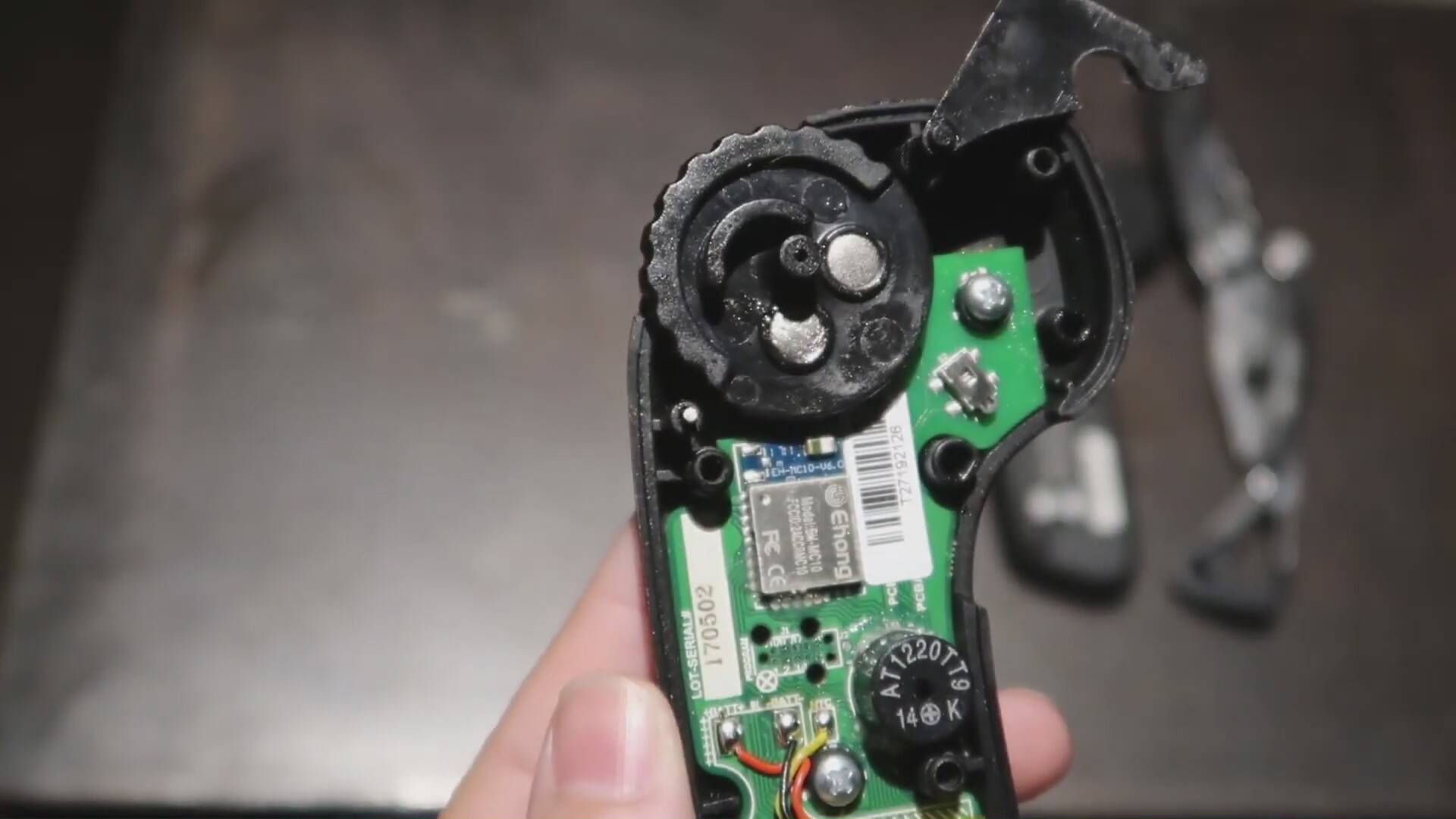
It uses a single hall effect sensor & 2 magnets for the proportinal speed.
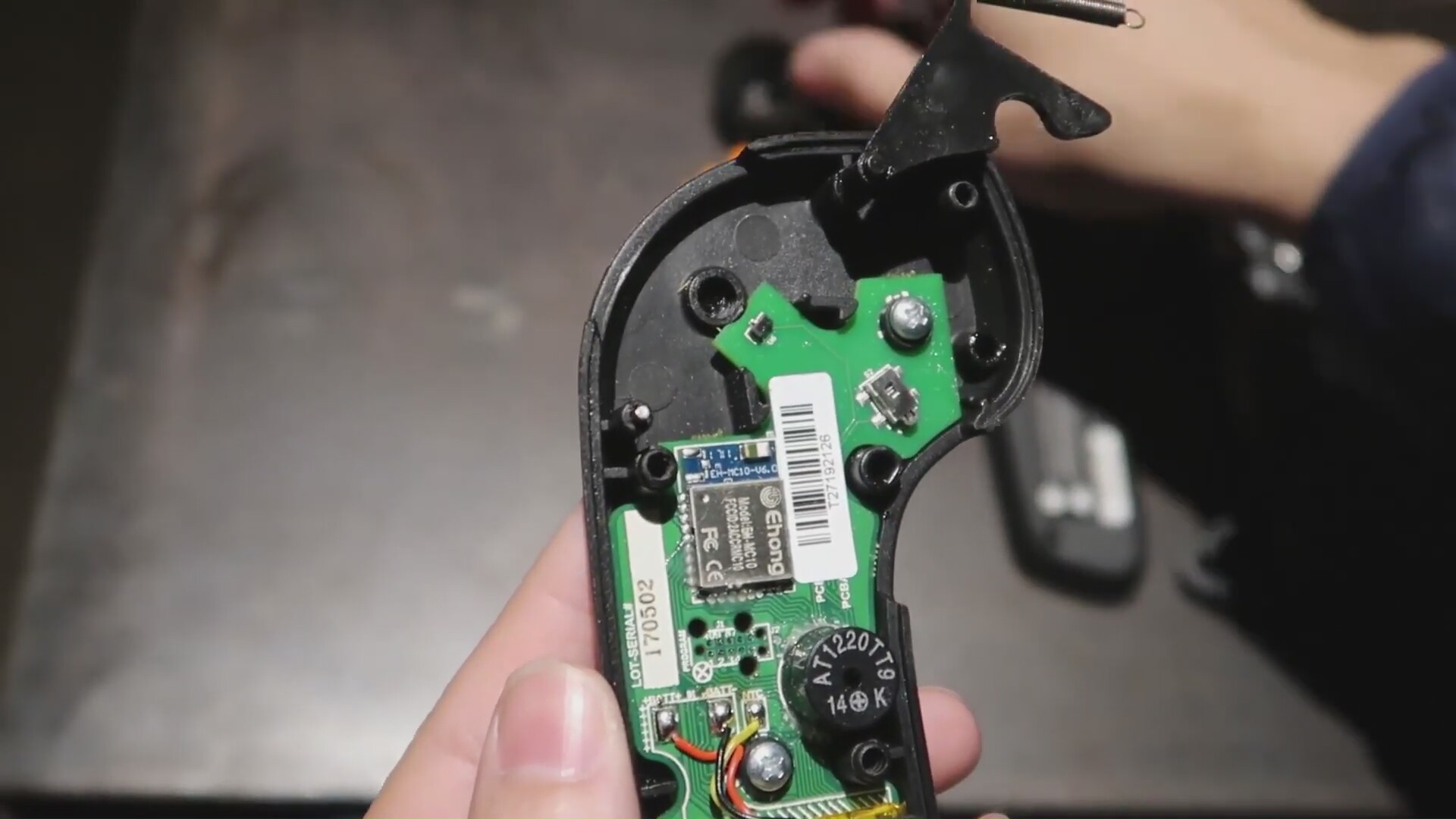
It has some weather proofing but not enough to withstand years of lion sweat. Sweat getting through the LED holes would instantly destroy it. They're designed for high paid executives who can afford a $2000 skateboard, who don't exert themselves. The key to waterproofing is hall effect sensors. All buttons could be waterproof if the magnets were small enough, but the size of the magnets limit hall effect sensors to proportional inputs. The only option for buttons is the rubber dome.
4 button steering has proven advantageous because it doesn't require thinking. The real slow trimming that comprises 99% of a lion's run is a lot easier with buttons. A proportional wheel might be useful for camera panning, though.
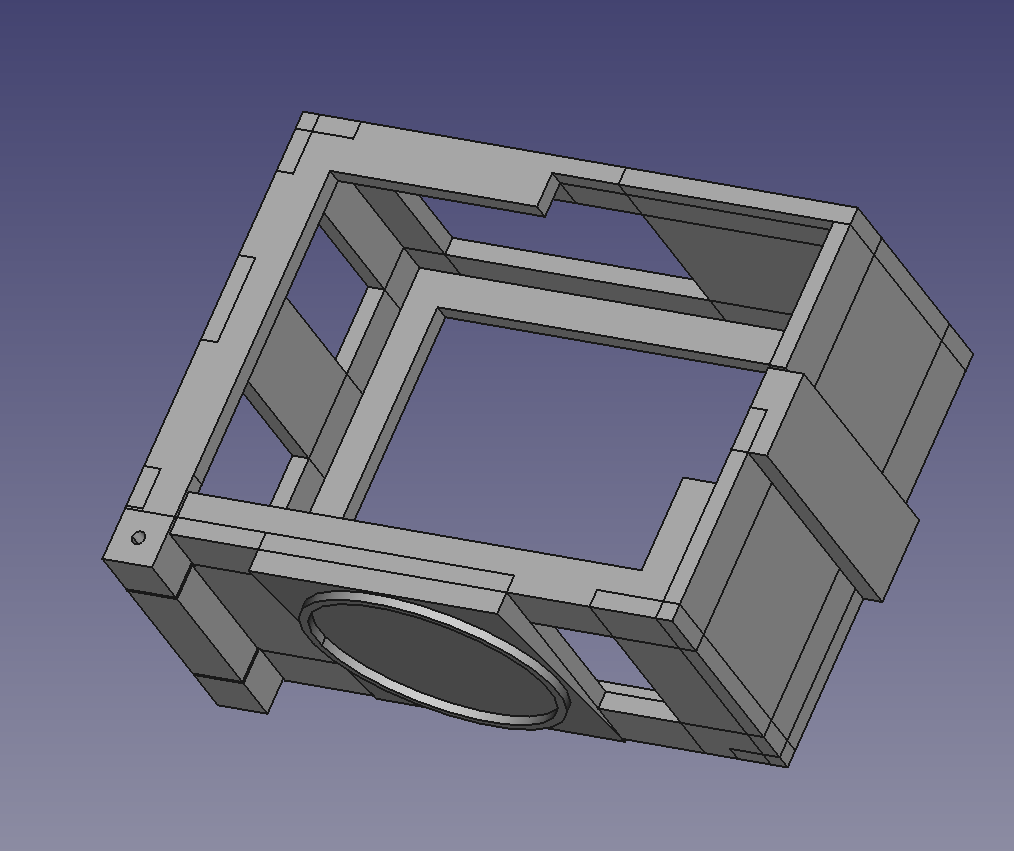
It was finally possible to abandon the stock gopro mounts, make something lighter, which didn't slip, & which farstened to carbon fiber.
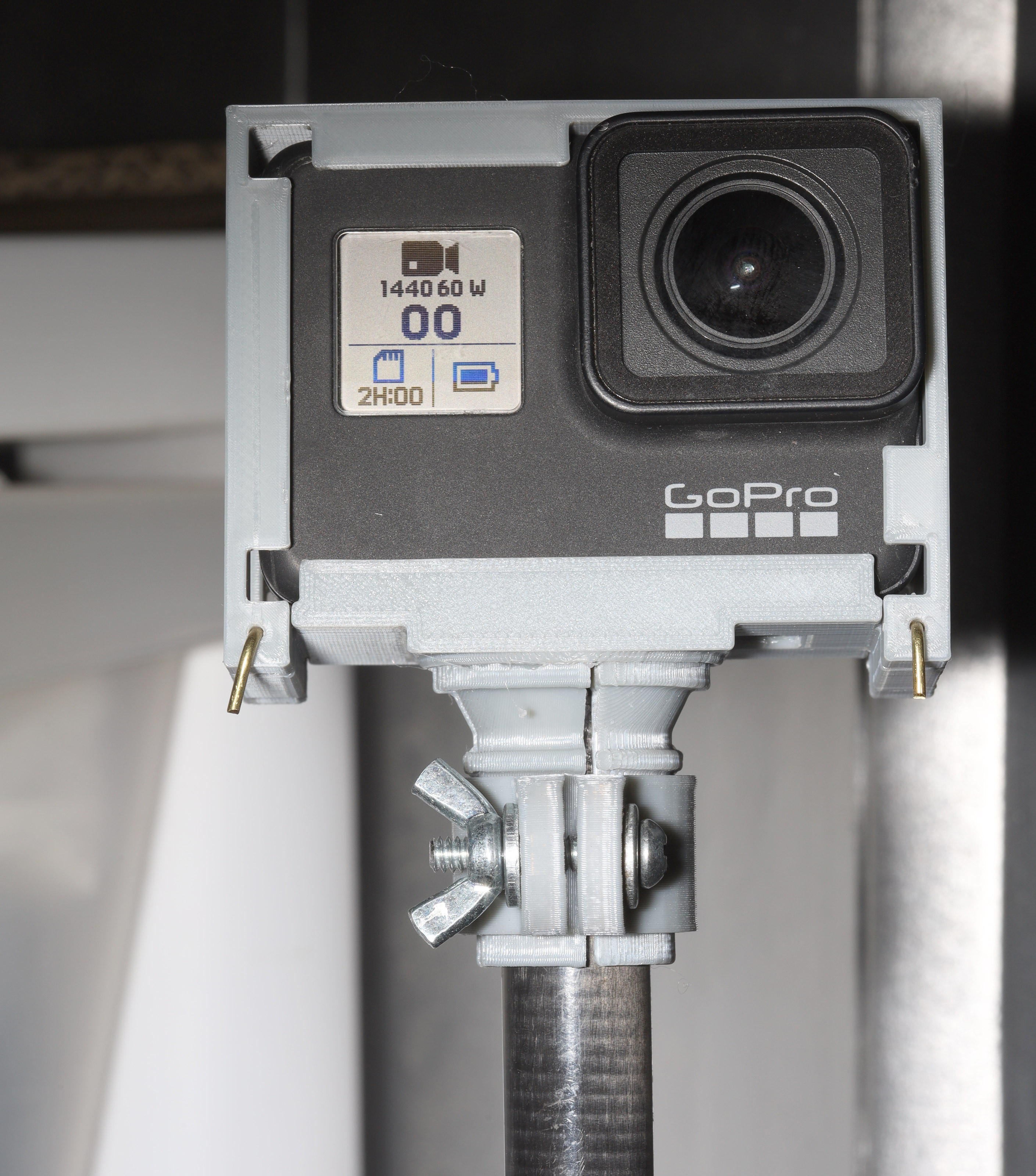
Gopros & carbon fiber were never meant to be together until now.
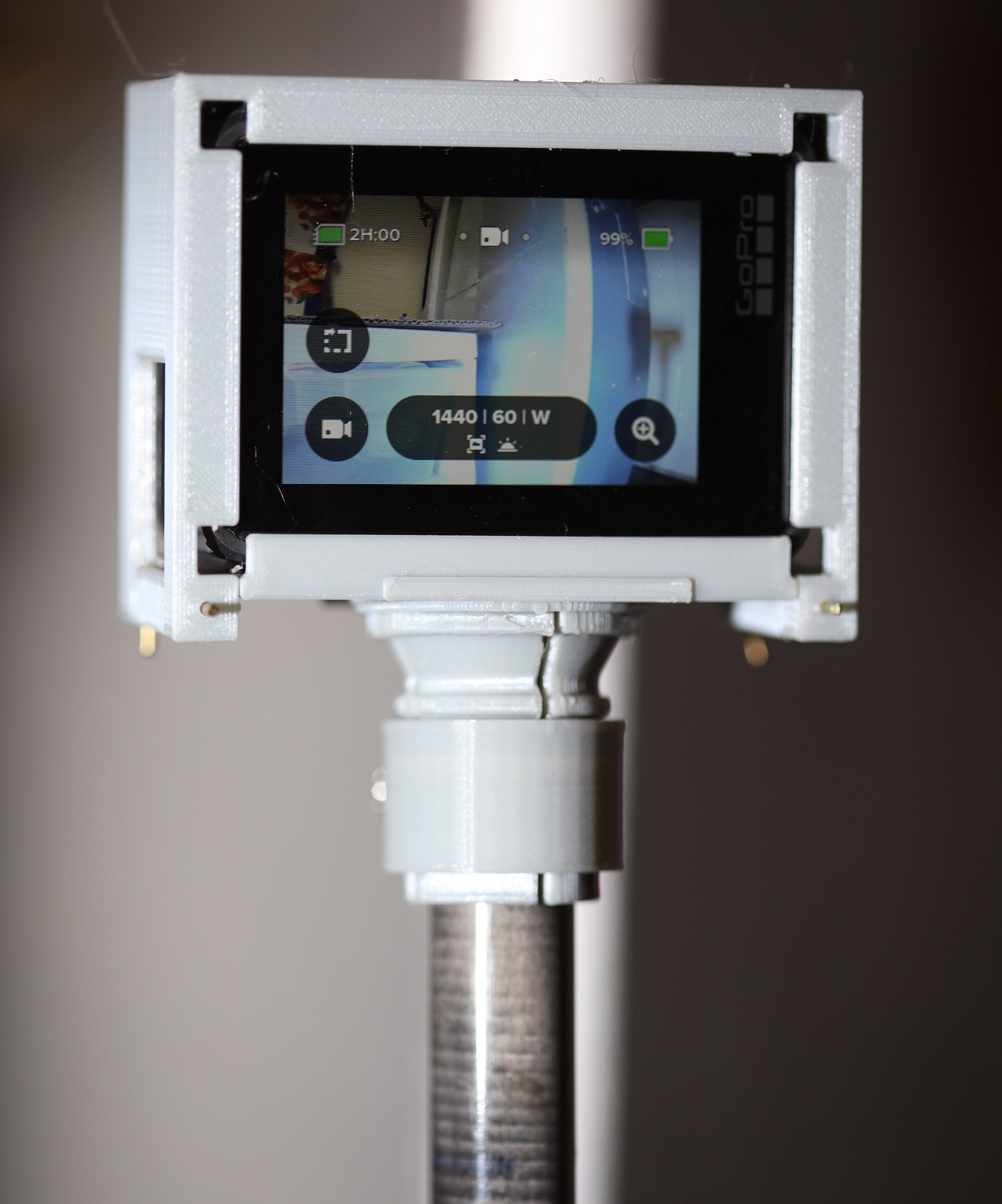
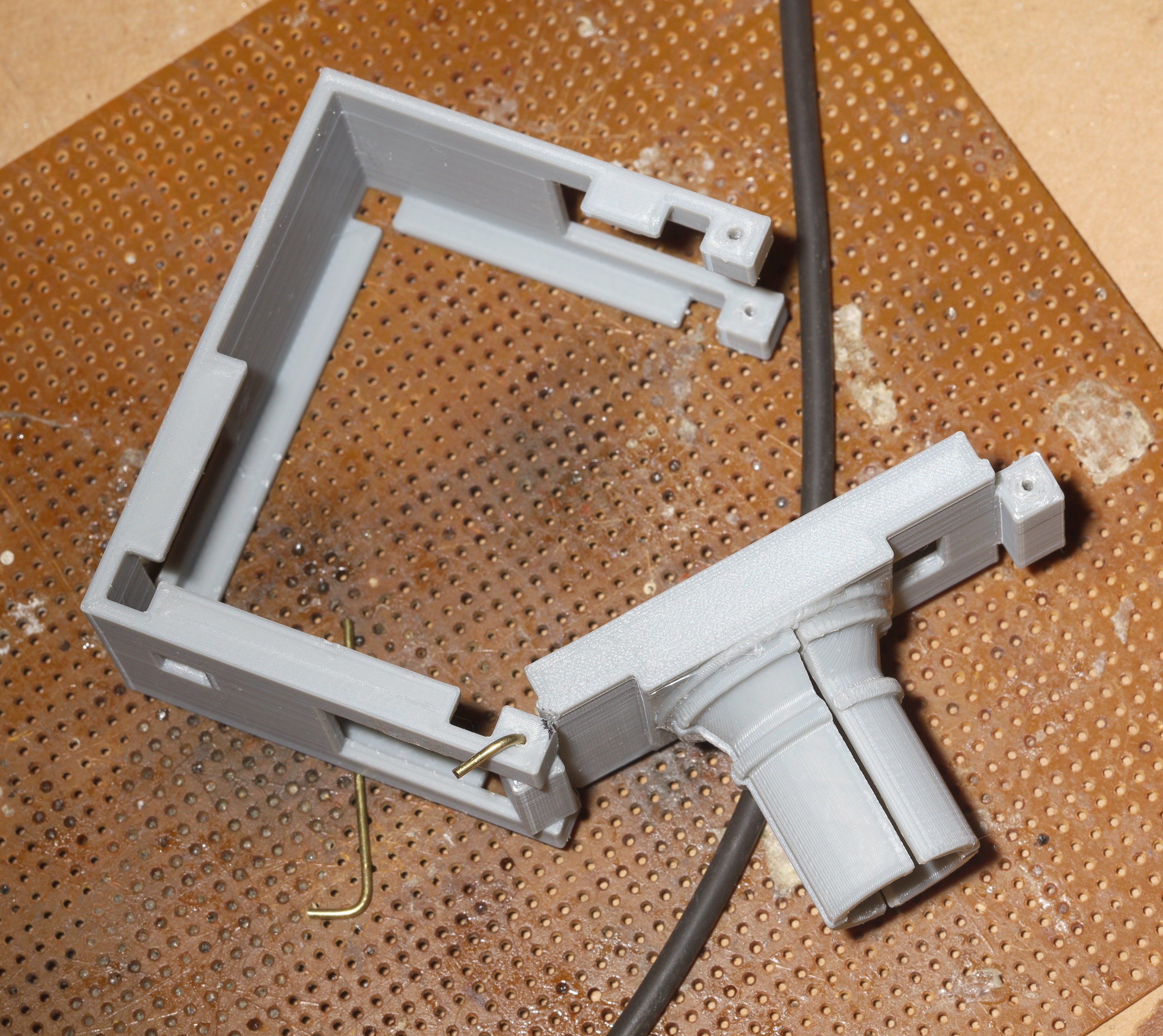
TODO:
- round joints on the outside instead of square joints on the inside
- knobs for the wire bits
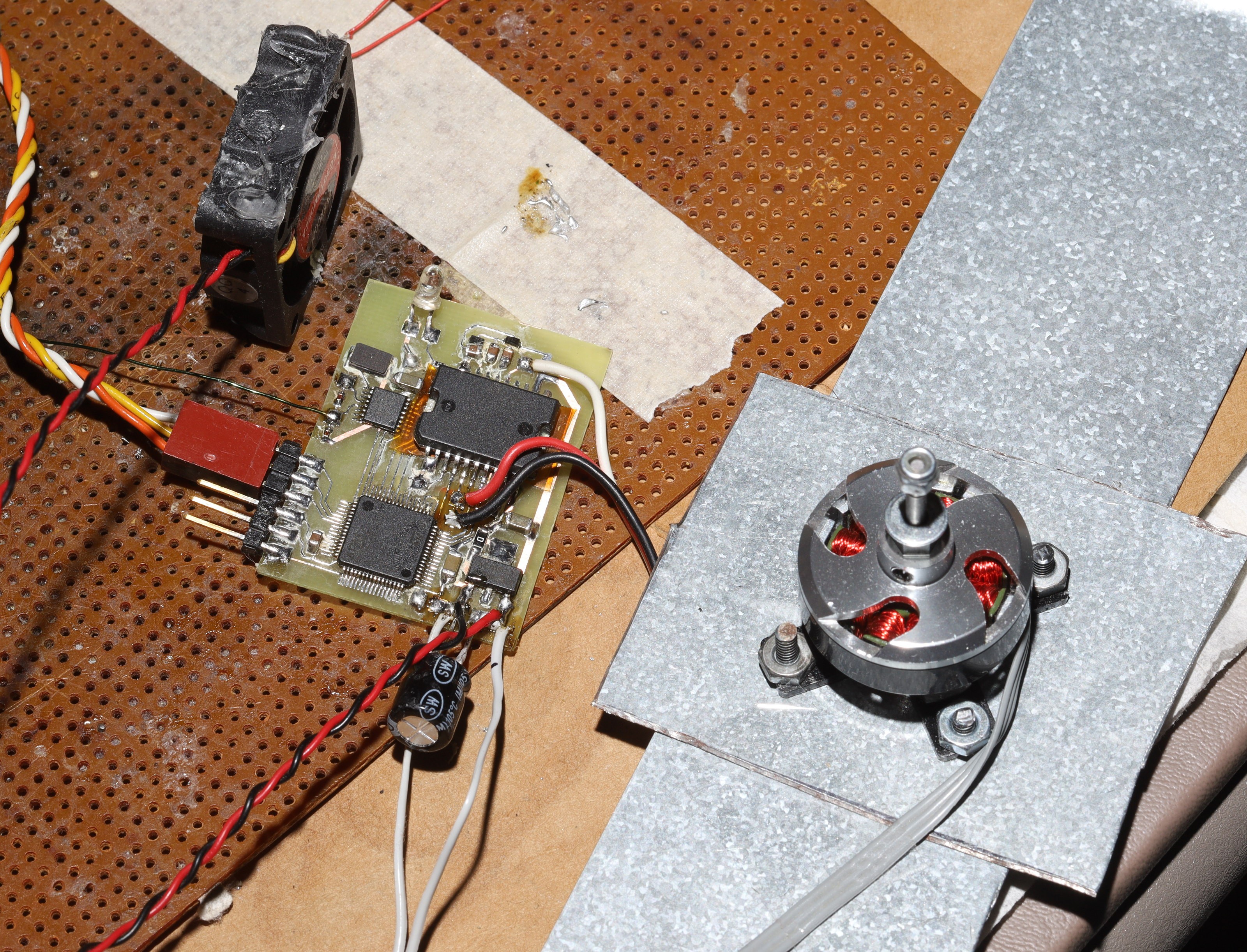
Smooth panning is actually really hard for a direct drive motor. The mane problem is cogging. Brushless gimbals have a true position from an encoder which allows them to lead or lag the motor phase, depending on the cogging. Most of them just rely on moving fast to hide the cogging. The lion kingdom's AI camera is smooth by being incredibly expensive & heavy.
Without some kind of encoder, your only option is driving the magnets harder. It takes a cooling fan, metal motor mount, high temperature farsteners, high capacity power supply. A geared stepper motor is what you need, but takes more space. A gearbox would allow it to be powered down when not moving.
This circuit proved to be an utter disaster. Not only was the STM32 overkill, it turns out lions had abandoned the L6234 in 2017 in favor of using common ESC's as dumb H bridges but forgot about it due to old age. Common ESC's handle a lot more power, have better thermal management, & cost less. Their mane limitation is less precision. The current on the panner is limited by the motor rather than the L6234 so an ESC wouldn't really achieve anything besides cost savings.
Given the desire to finish, lions just stuck with the crummy circuit, used in camera stabilization to smooth out some cogging & got something good enough.
No, a brushless gimbal wouldn't be easier. It would add weight to the wrong end of the pendulum.
Quite a relief to finish 8 years of trying to solve this problem with a 1st design that gave pretty good results on the 1st try. It definitely would be better with proportional steering, especially for tracking objects. Timelapse mode was overrated. Timelapse needs a brushless gimbal.
The remote control buttons need to have the same steering directions as the driving buttons. Being a right or left pawed controller makes no difference in lion perception of what direction should be on top. It needs an enclosure to prevent cargo from interfering with the motor. Needing an enclosure, it might as well receive a gearbox. The remote needs the pinky grip. Holding it like a TV remote for 1 hour is stressful.
Discussions
Become a Hackaday.io Member
Create an account to leave a comment. Already have an account? Log In.