The object of the robot is manetaining a constant speed & heading on its own. This is just automated enough for a lion to drive it with 1 paw while doing something else. The journey began in Jan 2014, with a $40 G-Buggy the lion kingdom got for free.
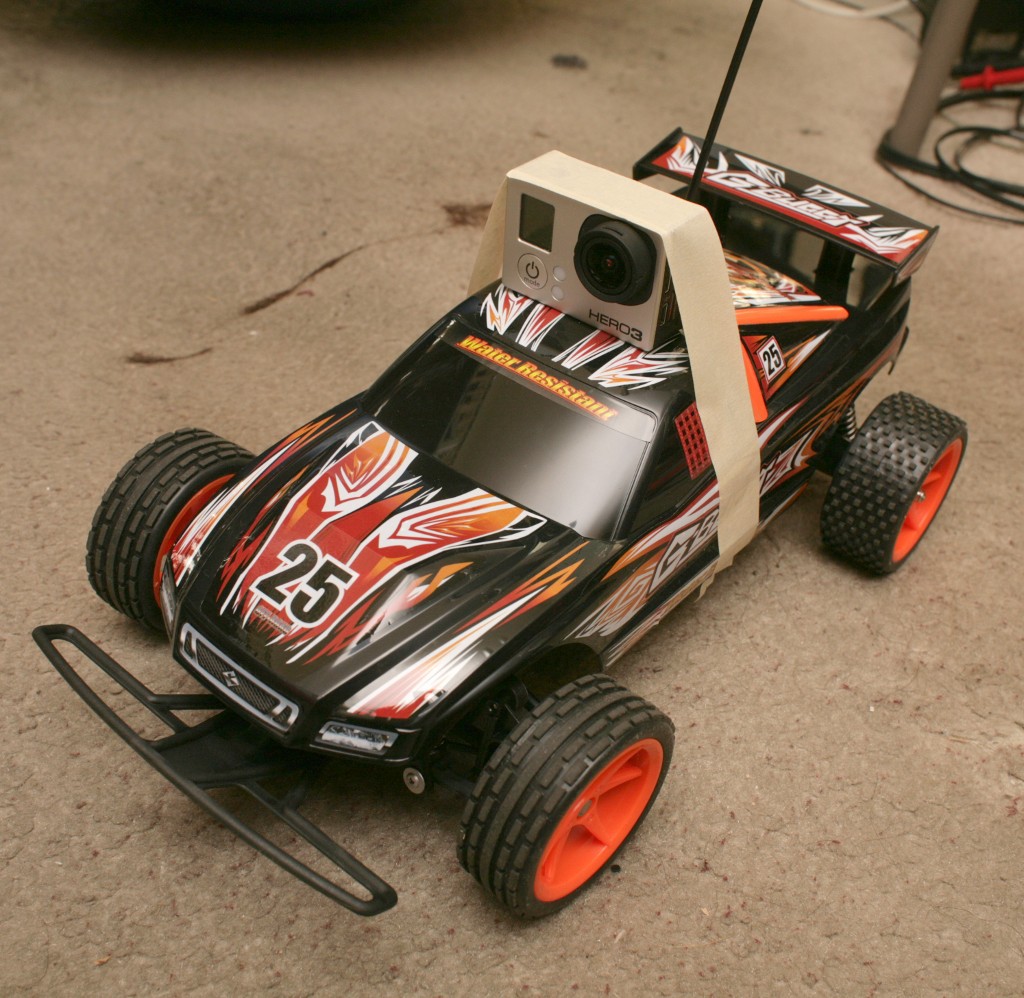
This was the seed of the idea. The lion kingdom would have never developed the complete robot if it wasn't for the original free G buggy.
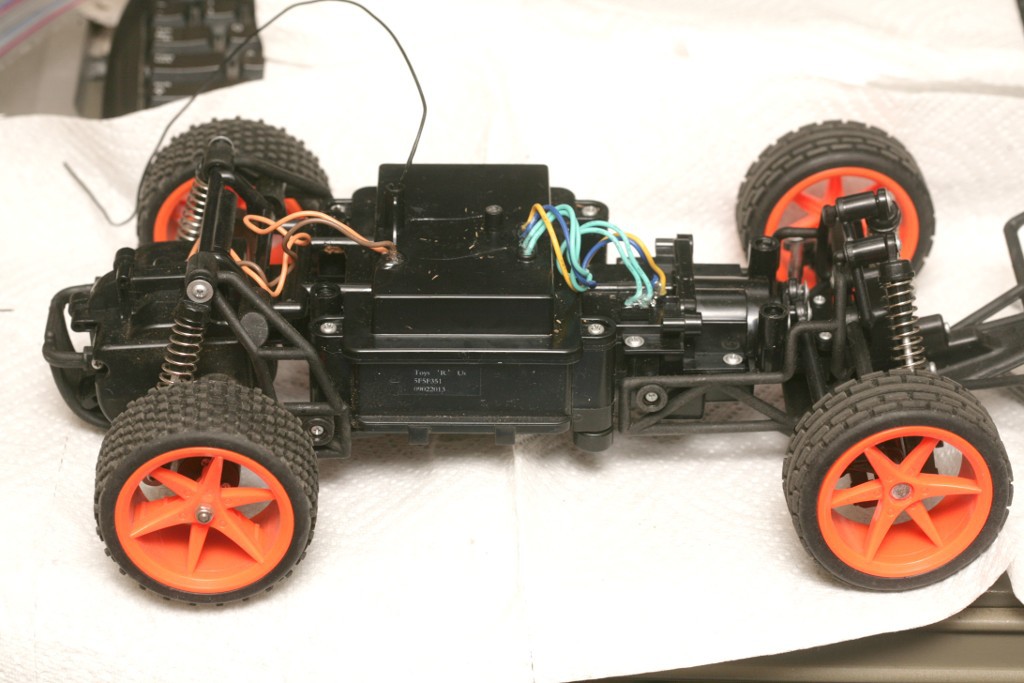
It was a very poor at setting a pace, couldn't carry cargo, but could carry a camera. The potential for documenting runs was there. There was no easy way to measure speed & the steering was binary. With enough tuning however, the steering could be made proportional enough to hold a heading.
The steering mechanism was an interesting reduction of a servo into a spring that centered the wheels & a clutch plate that applied a steering force proportional to the speed of a motor. The controller it came with could only do binary steering, but with a fast rate sensor & feedback loop, the steering could be made somewhat proportional.
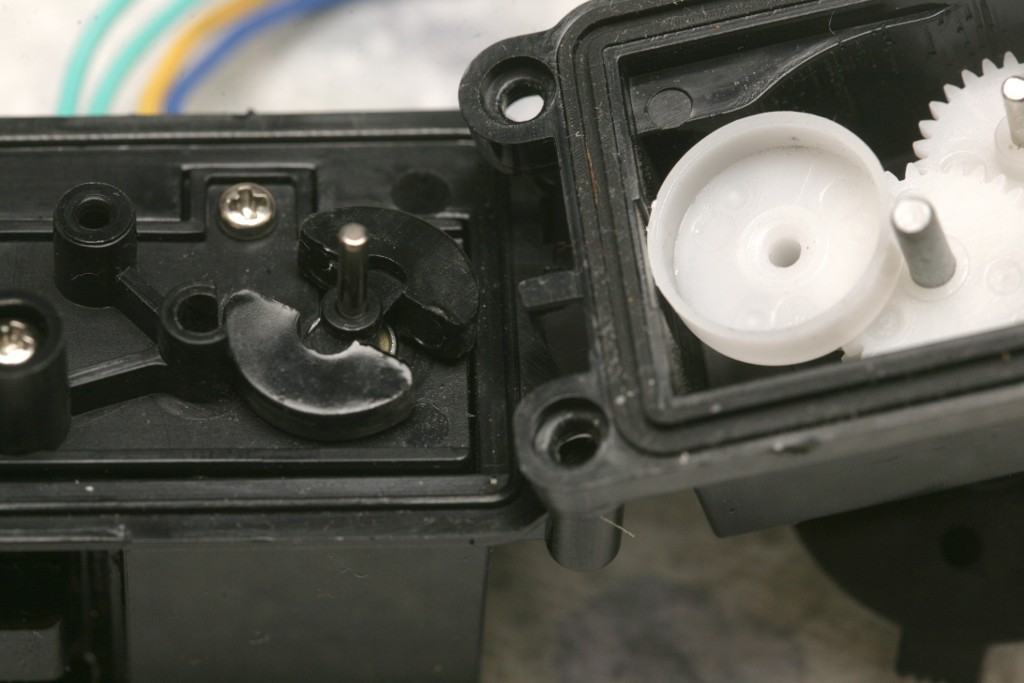
The inner clutch plate & outer ring it pressed against while spinning, but not while stationary.
With a constant voltage applied to the traction motor, it achieved poor speed regulation but infinitely better than lions trying to pace themselves.
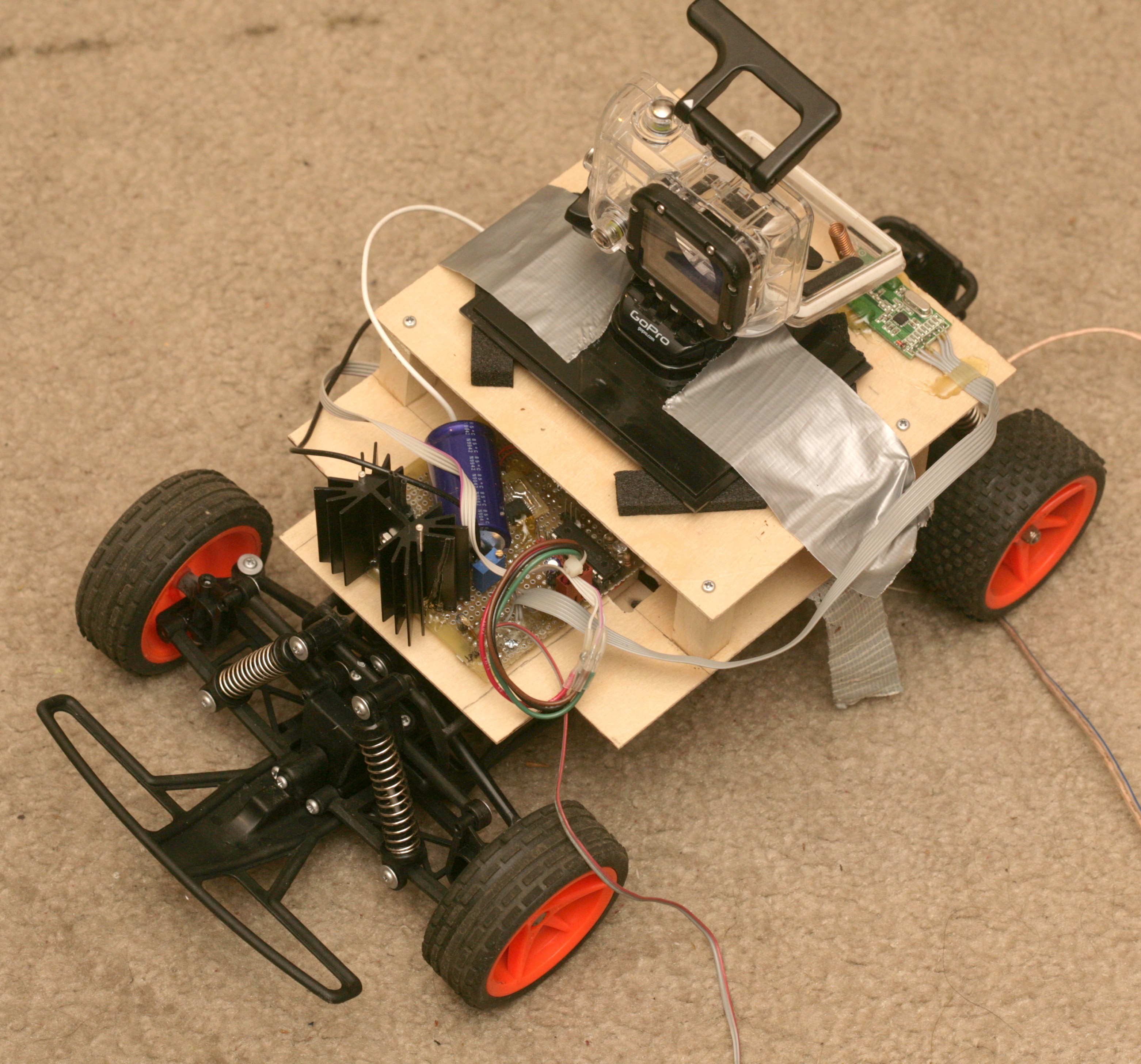
The final form of the 1st model.
Several models came afterwards, as budgets increased, culminating in the Tamiya Lunchbox. The steering was finally proportional & the speed could finally be regulated.
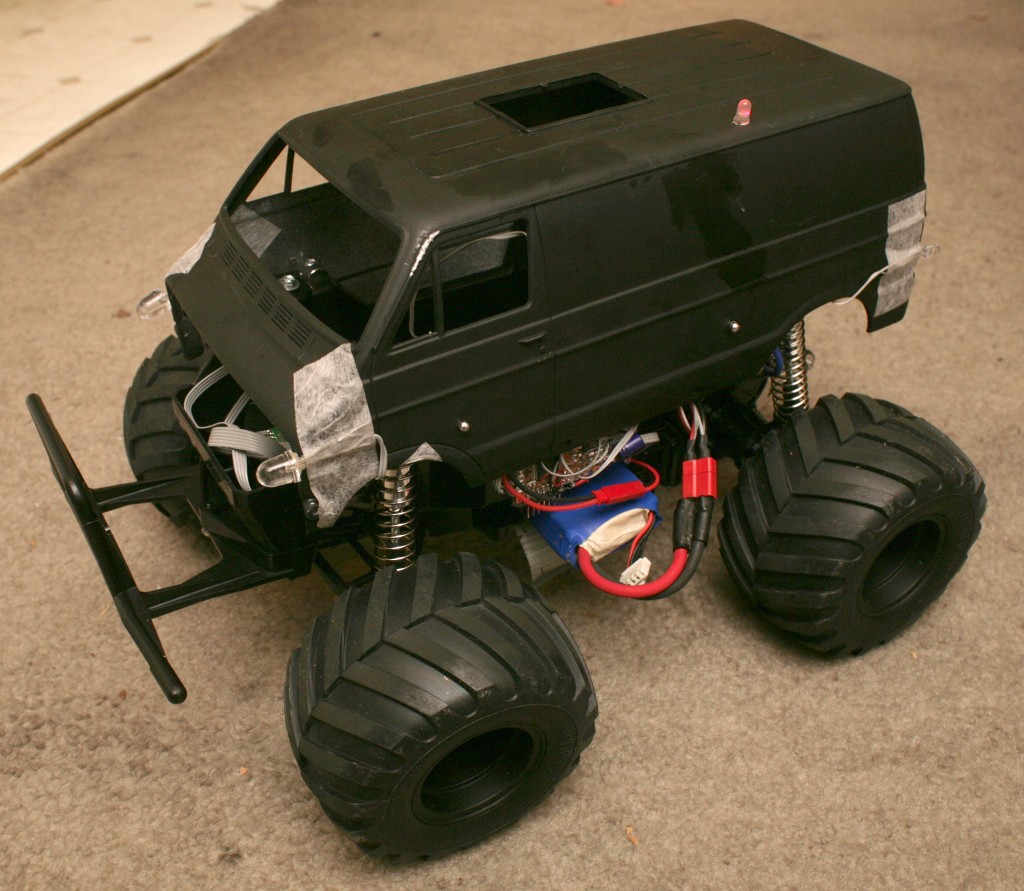
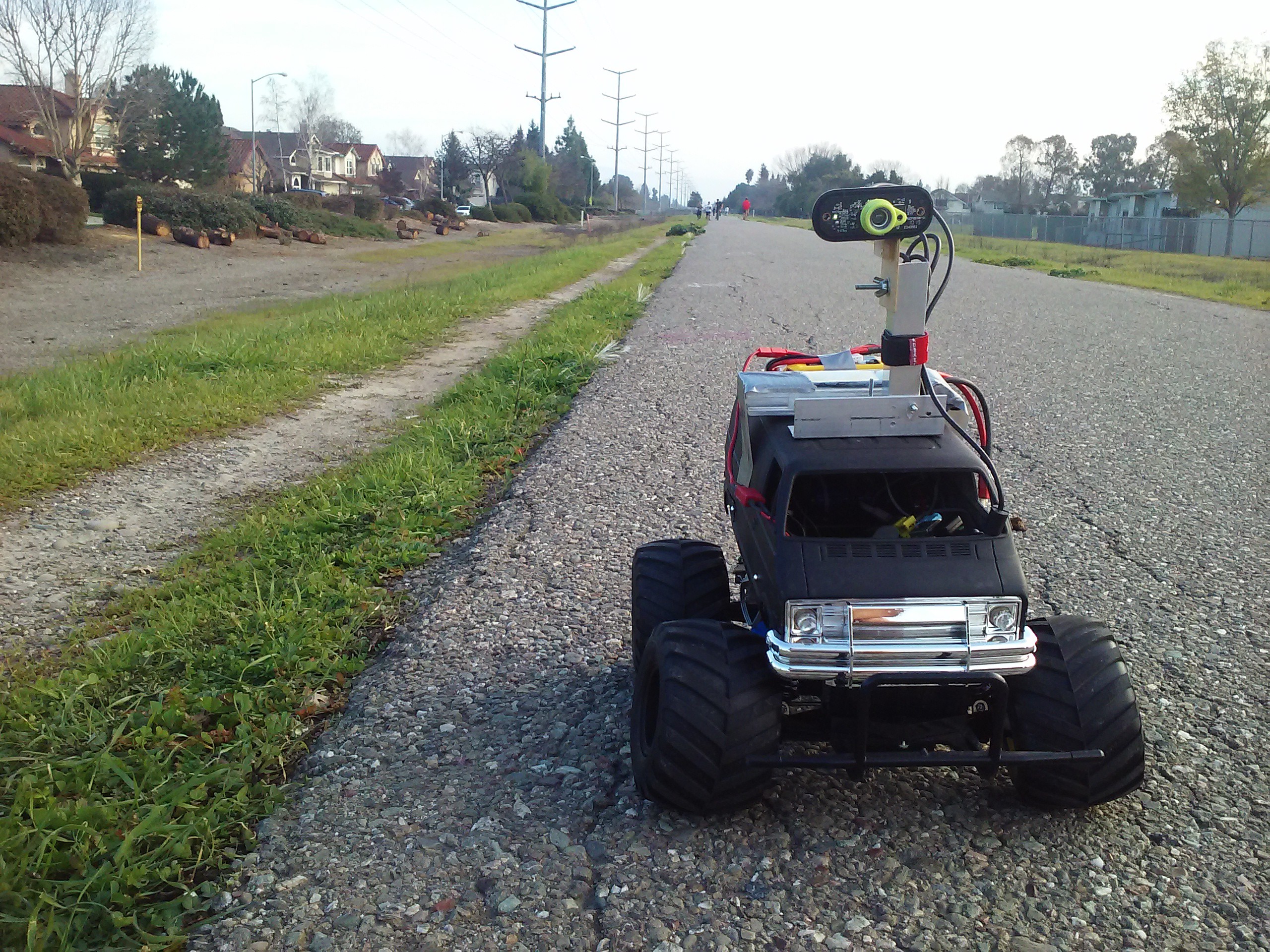
Attempts to make it self driving all failed, for reasons startups are too familiar with.
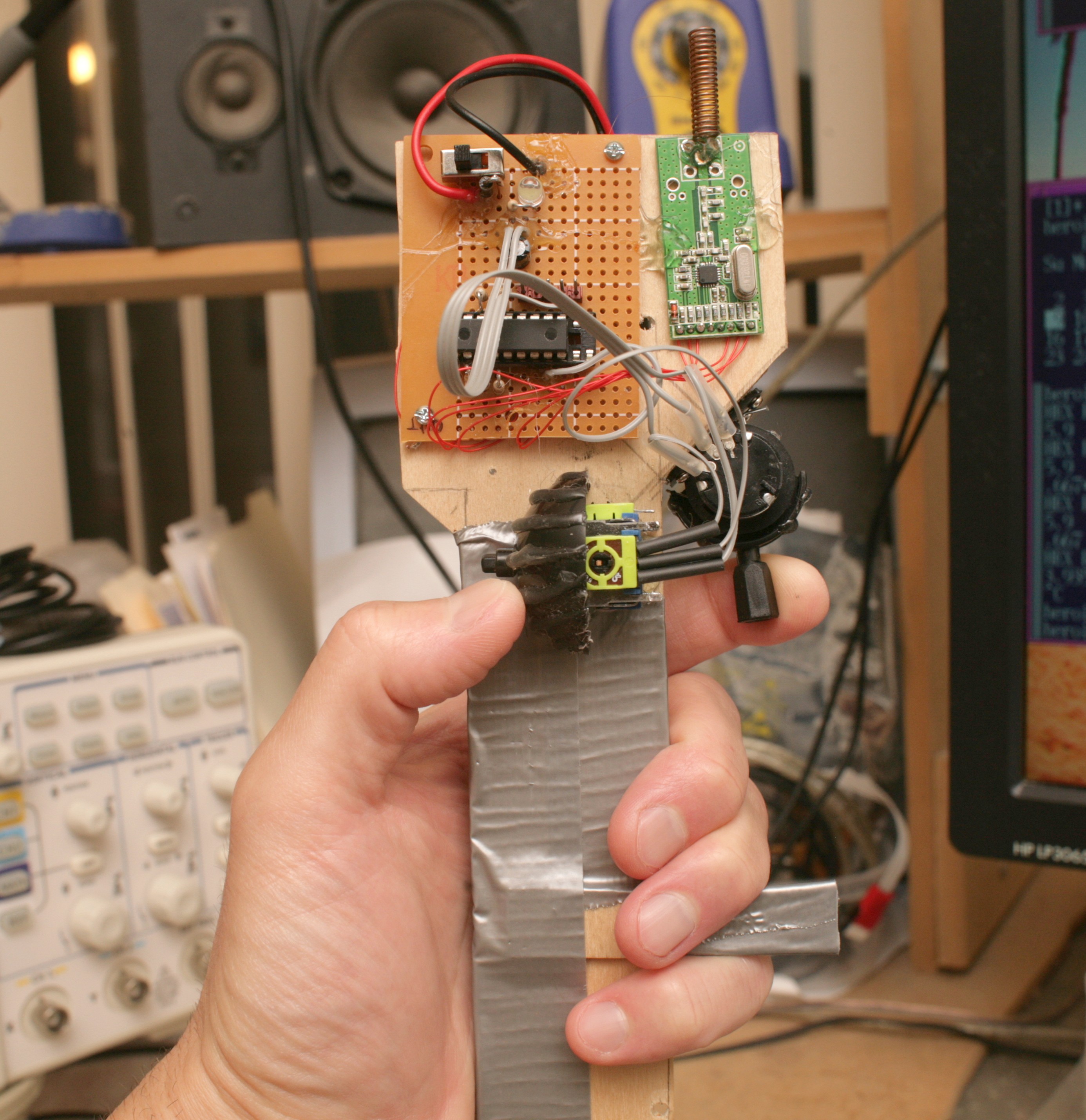
Key to making it all work was a paw controller which lions could provide semi autonomous control from. Proportional steering & throttle would be nice, but weight & durability dictated binary tact buttons. China simply never made a durable, compact, proportional sensor.
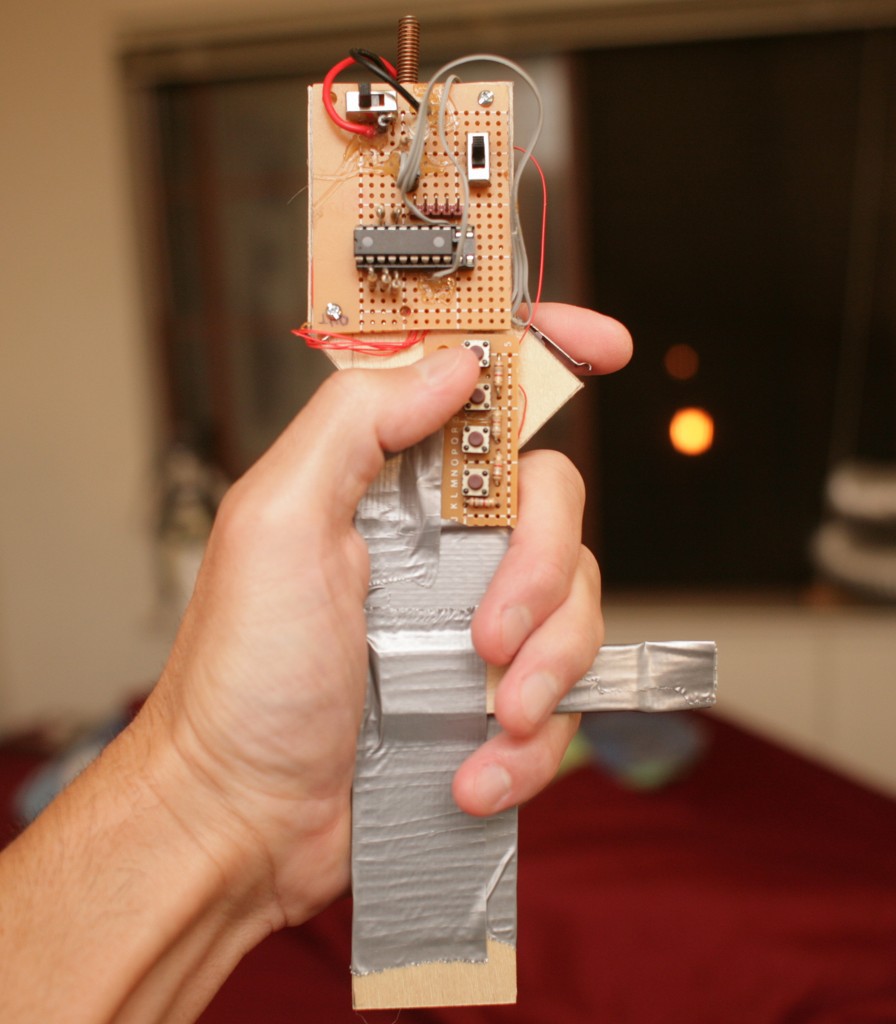
In May 2014 came the 1st controller which lasted a reasonably long time.
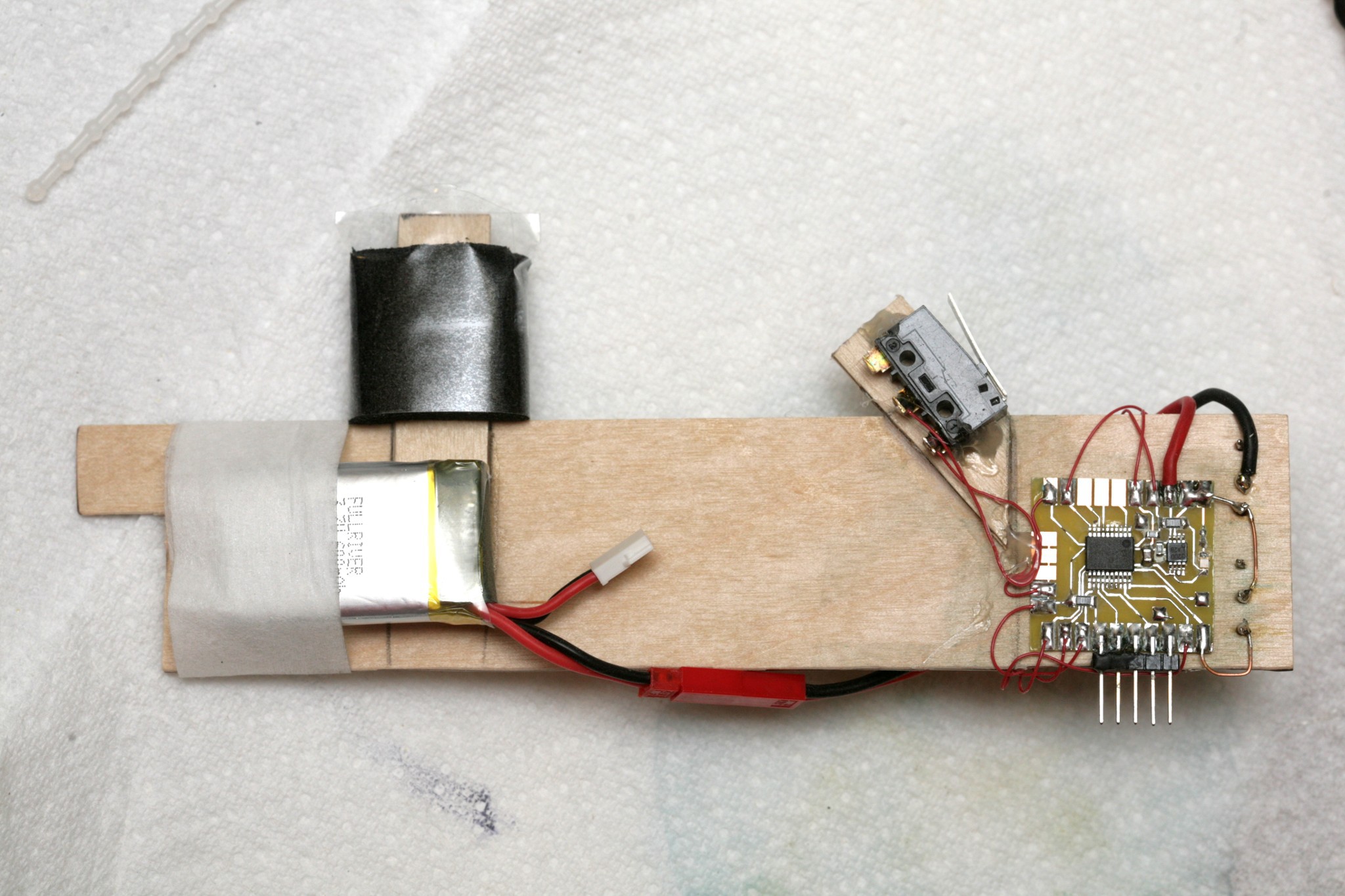

The final design had 2 buttons for slow steering, 2 buttons for fast steering, 1 button for throttle. This was proportional enough for all needs, with the computer automating speed & heading. 1 switch controlled reverse.
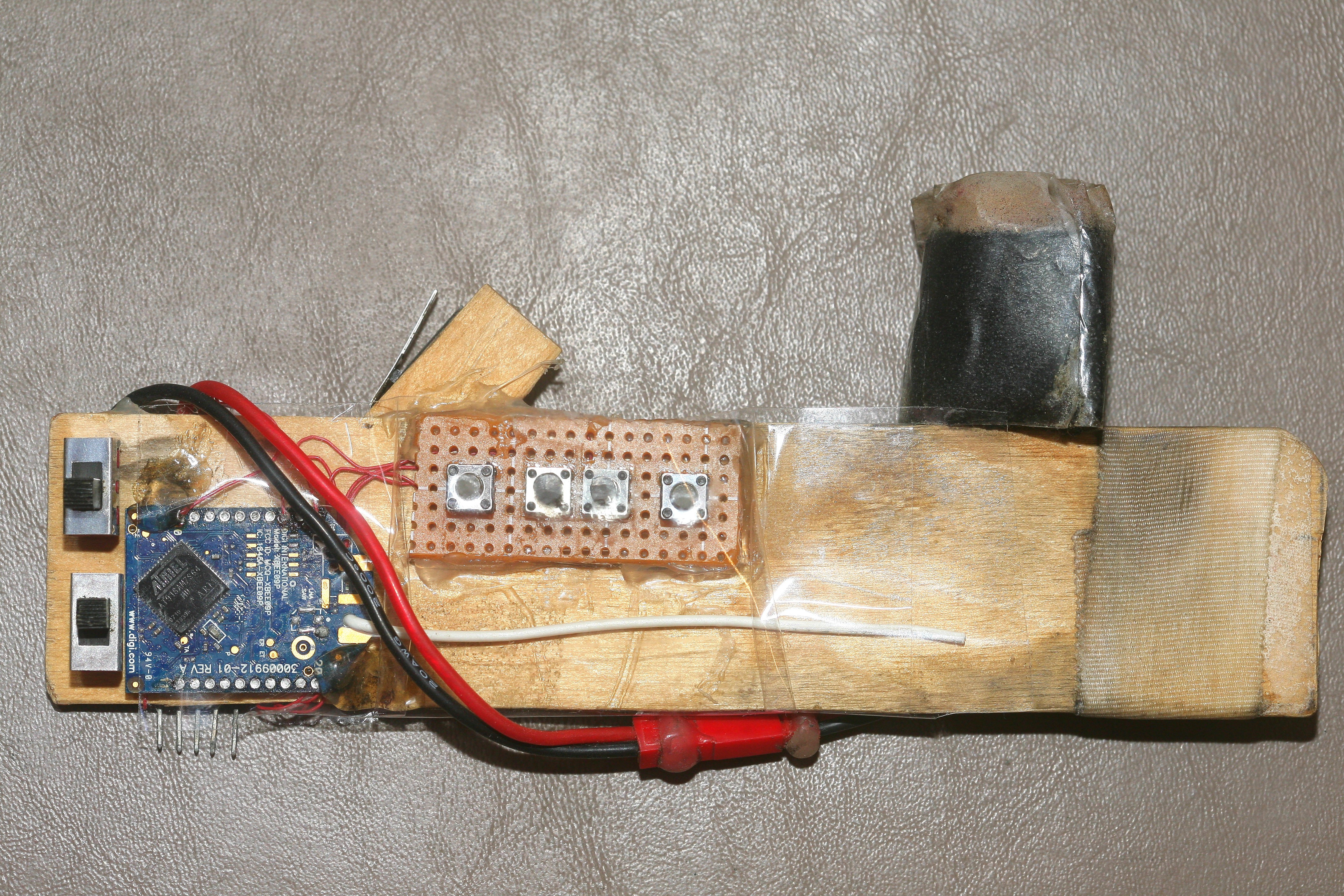
The stick was further refined with 900Mhz frequency hopping radios, 4" packing tape to insulate the switches from sweat.
Attempts to make it self driving continued through 2015. Attempts to go beyond pacing & make it carry stuff began in Dec 2015.
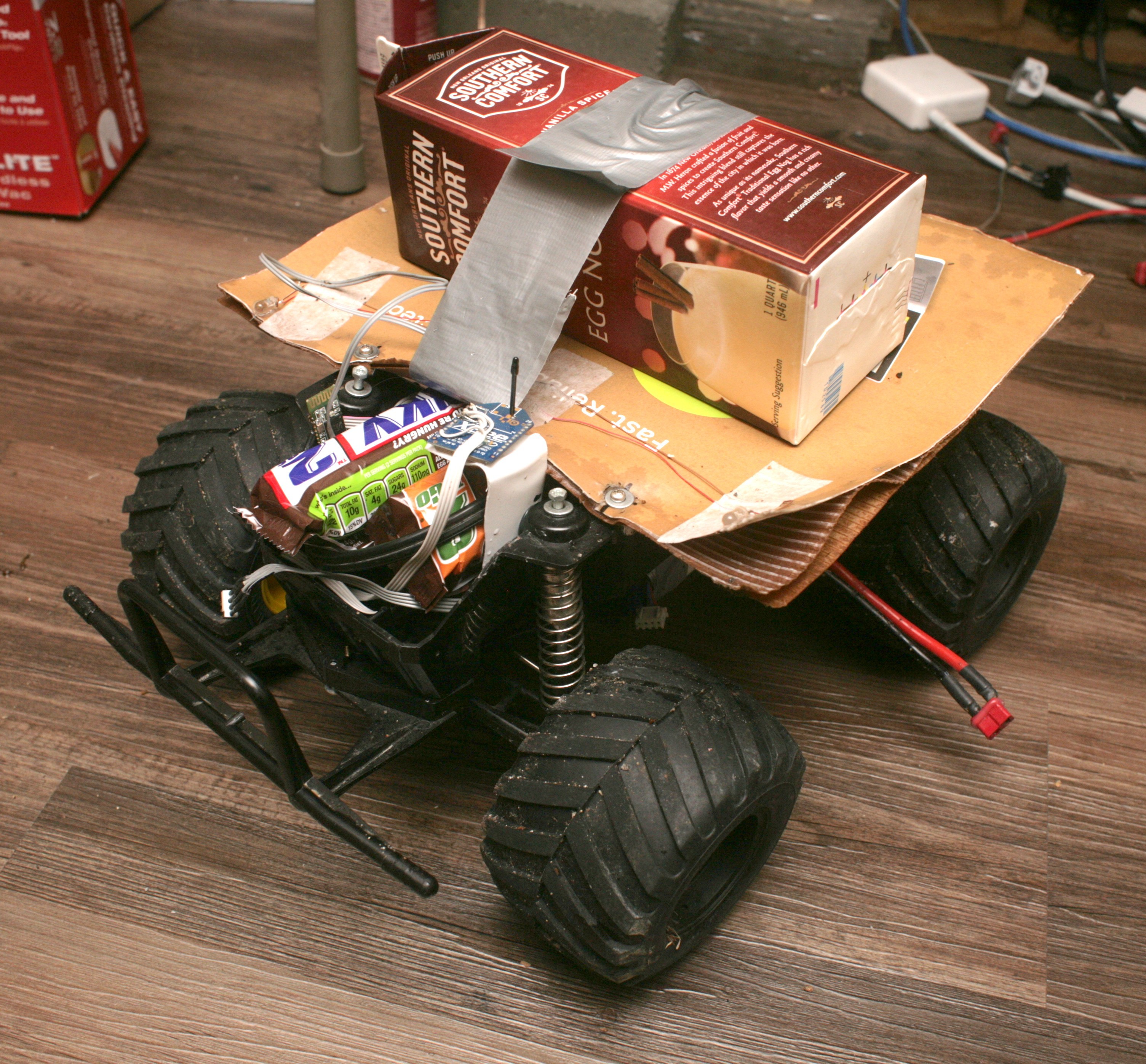
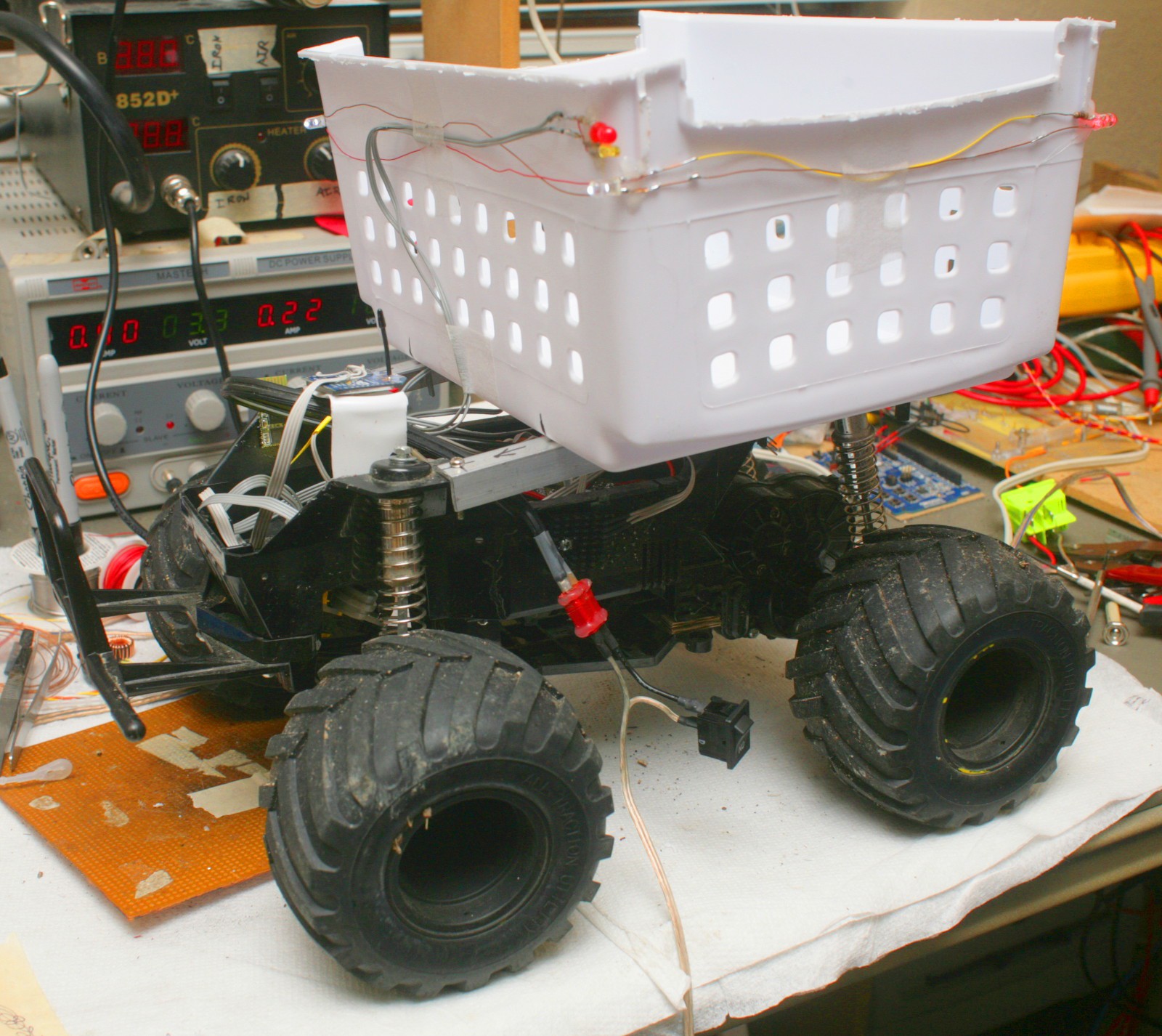
This was the shift from a toy to a practical logistical solution. It was also the moment lions realized it's better to have a semi autonomous solution that works than to perpetually search for self driving while having nothing useful.
The final lunchbox system had a very large container.
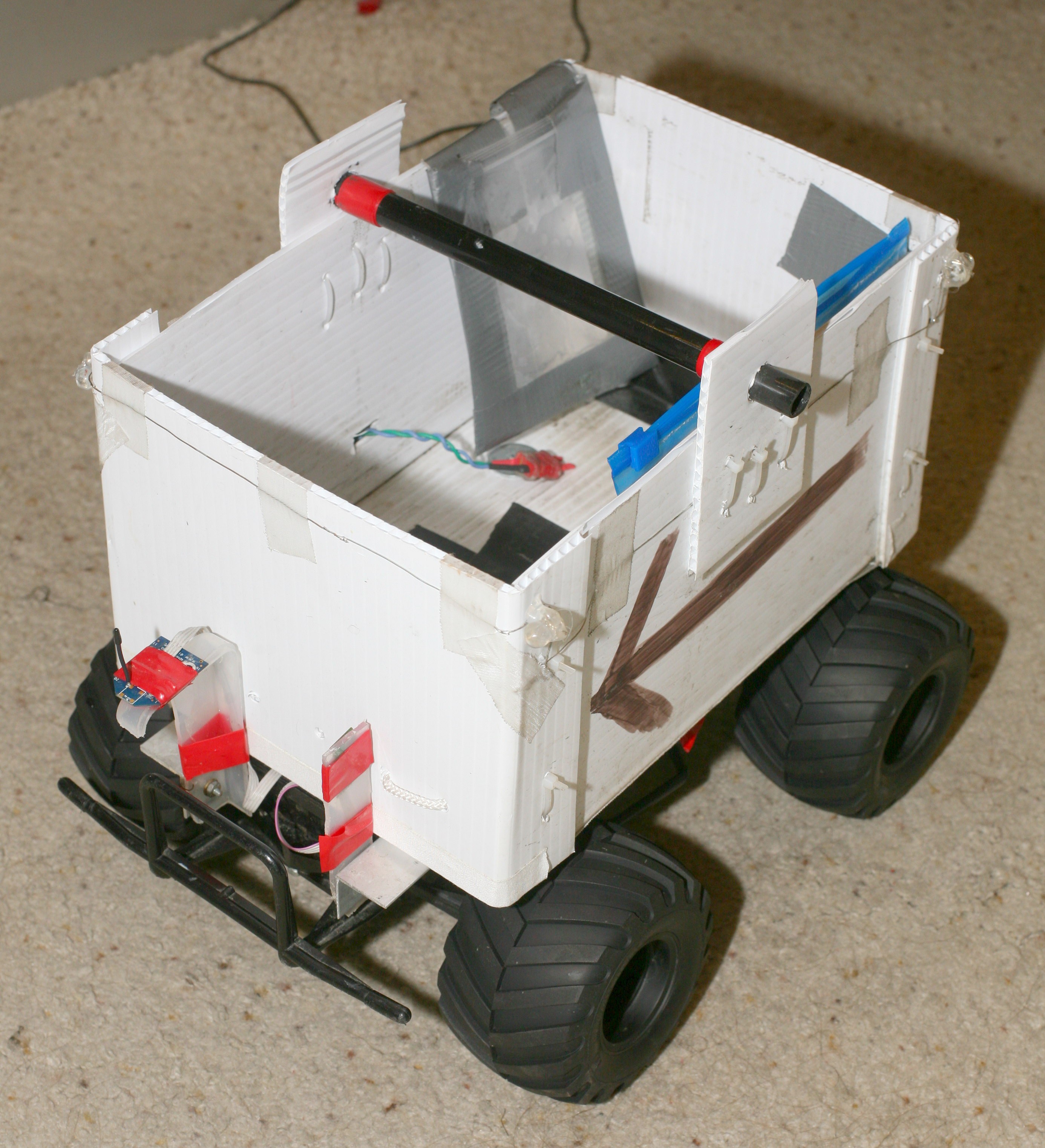
Suspension was lowered. Wheels were reinforced. Tires were wrapped in nylon.
Current mail order parts which have yielded the best results, after thousands of miles:
Lunchbox kit https://www.amazon.com/Tamiya-TMYTAM58347-1-12-Lunchbox/dp/B000BMVIGW/ref=sr_1_3?ie=UTF8&qid=1549922090&sr=8-3&keywords=tamiya+lunchbox+parts 147.2
motor https://www.hobbypartz.com/96m276-2848-2400kv-16t.html discontinued
1:10 2400kv size 540 35mm diameter 3.17mm shaft. The 2848 descriptor is not reliable.
bec https://hobbyking.com/en_us/turnigy-5a-8-40v-sbec-for-lipo.html 6.86
... Read more »