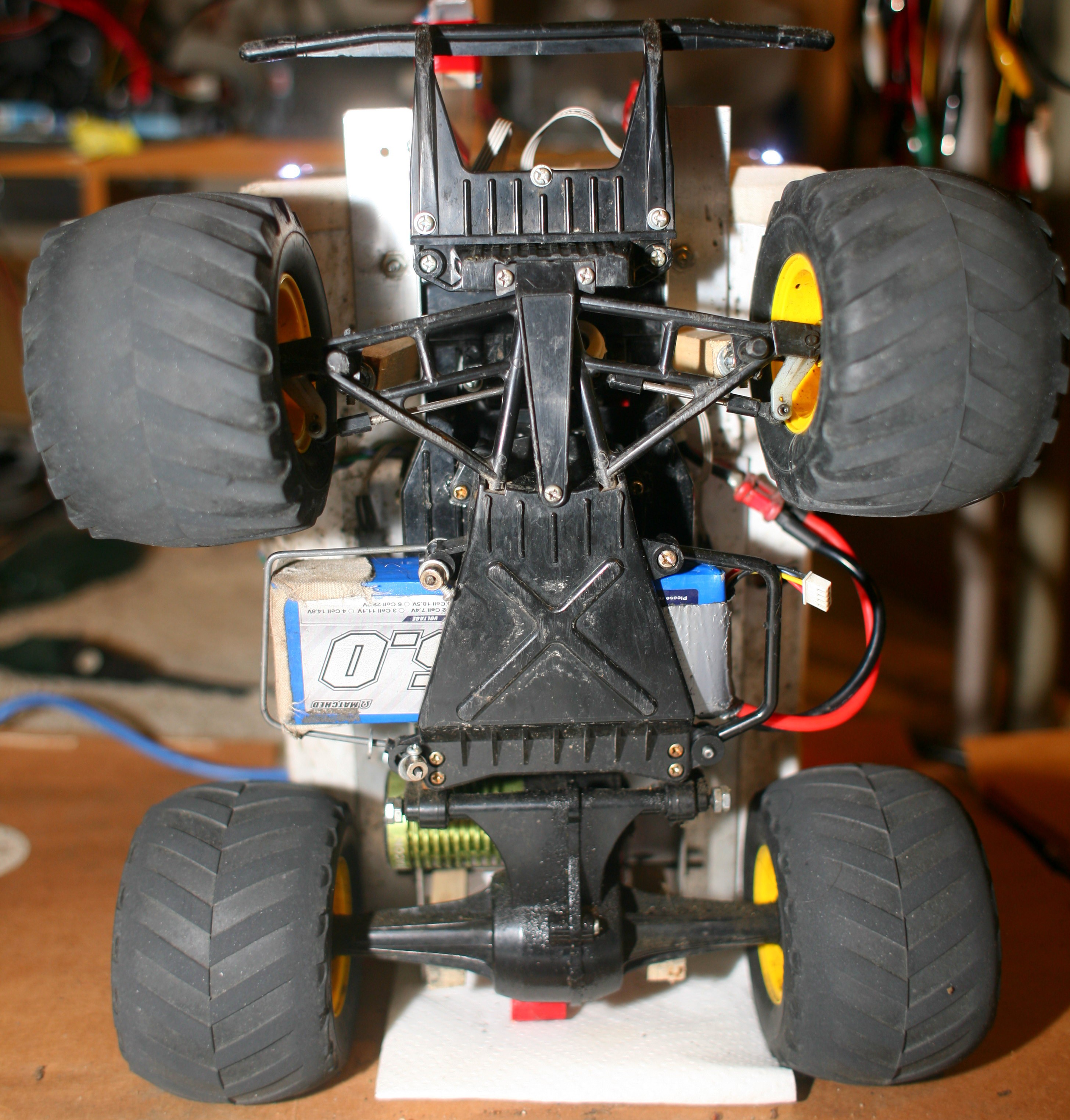
Shifted the pushrods so the wheels were centered when the servo horn was centered. This was off, but wasn't causing the oscillation. Because the servo is off center, lowering the suspension made the right wheel extend more & made the steering naturally pull right.
Pushrod alignment can't be corrected in software, because of the geometry of the servo horn. The pushrods still weren't long enough to handle the lowered suspension, so they're still pointing slightly to the right. A slight toe out is required with the lowered suspension. Tire wear is caused by oscillations.
The vehicle requires a diaper to collect oil from the gearbox. The gearbox is real noisy without massive soaking & it's hard on the ears after 20 miles.
In other news, you can make a notch filter of sorts with the PID controller's resonant frequency. The problem is the 4 independent variables: gain & bandwidth for the high & lowpass.
Discussions
Become a Hackaday.io Member
Create an account to leave a comment. Already have an account? Log In.