ELM incorporates electromagnet to do the task of lifting or dragging objects. There are benefits and disadvantages to this approach:
PROS (compared to mechanical grippers):
- Cheaper, easier maintenance and reliable (no mechanical joints)
- More reliable grabbing and dropping of object
- Stronger grip than mechanical grippers
- Doesn't use mechanical force to press on the object
- Smaller and lighter the larger in volume object gets
- Easier to interface with system from software side
CONS (compared to mechanical grippers)
- Objects need to be metal or need to have metal gripping area
- Consumes electricity during entire operation
- Force holding the object is concentrated in smaller surface area
Electromagnet mounted on ELM needs 12 volts DC to operate. If your system voltage is lower than 12 volts, onboard boost converter can be used to power the electromagnet. In systems where voltage is around 10 to 15 volts boost converter can be omitted with jumper. ELM also includes reflective optical sensor to detect if object is present and LEDs for optical signalization. LEDs and sensor can be powered by on-board step down converter or external voltage. Module is interfaced with system via 6 pin IDC connector.
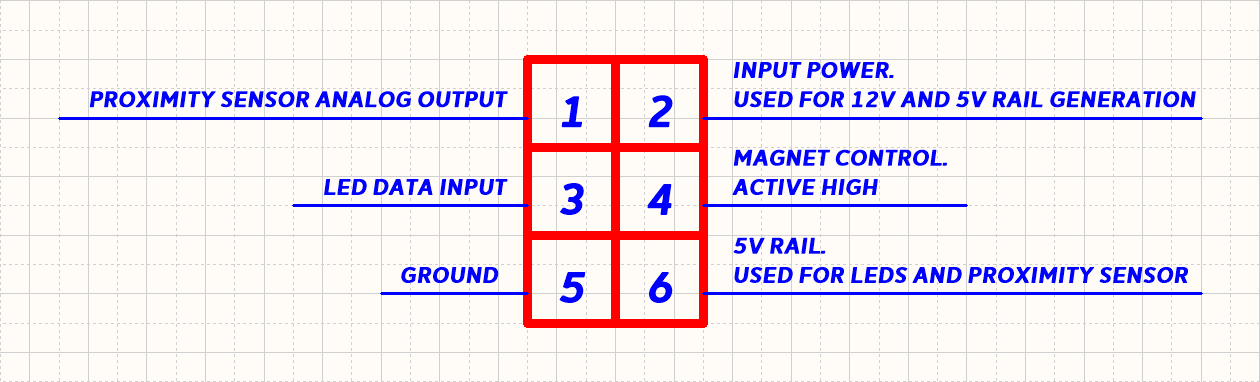
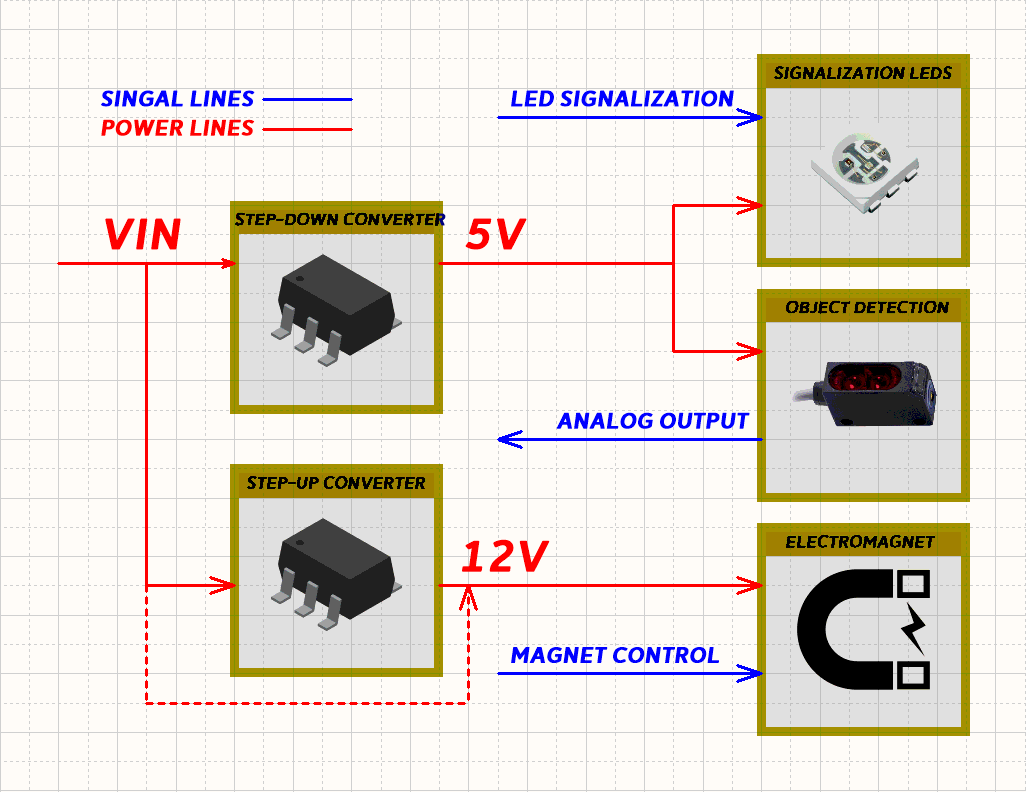
Project is published under MIT License. For more information visit this link.
you can also use programmable magnets
https://diydrones.com/profiles/blogs/electro-permanent-magnet-for-reliable-cargo-lifting-on-a-quad
or mechanical rotate magnets to get the same behavior
https://spanntech.eu/magnete-lasthebemagnete/lasthebemagnete-80-funktion.html