These pages describe in great details how I built a reliable and efficient high voltage nixie power supply -showcased above-; from the idea to selling it!
Be sure to read project logs!
- Part 1: Idea
- Part 2: Design & Simulation
- Part 3: Making a prototype
- Part 4: More prototypes!
- Part 5: Sending for Assembly
- Part 6: Efficiency
- Part 7: Production Run
- Part 8: Selling & Conclusion
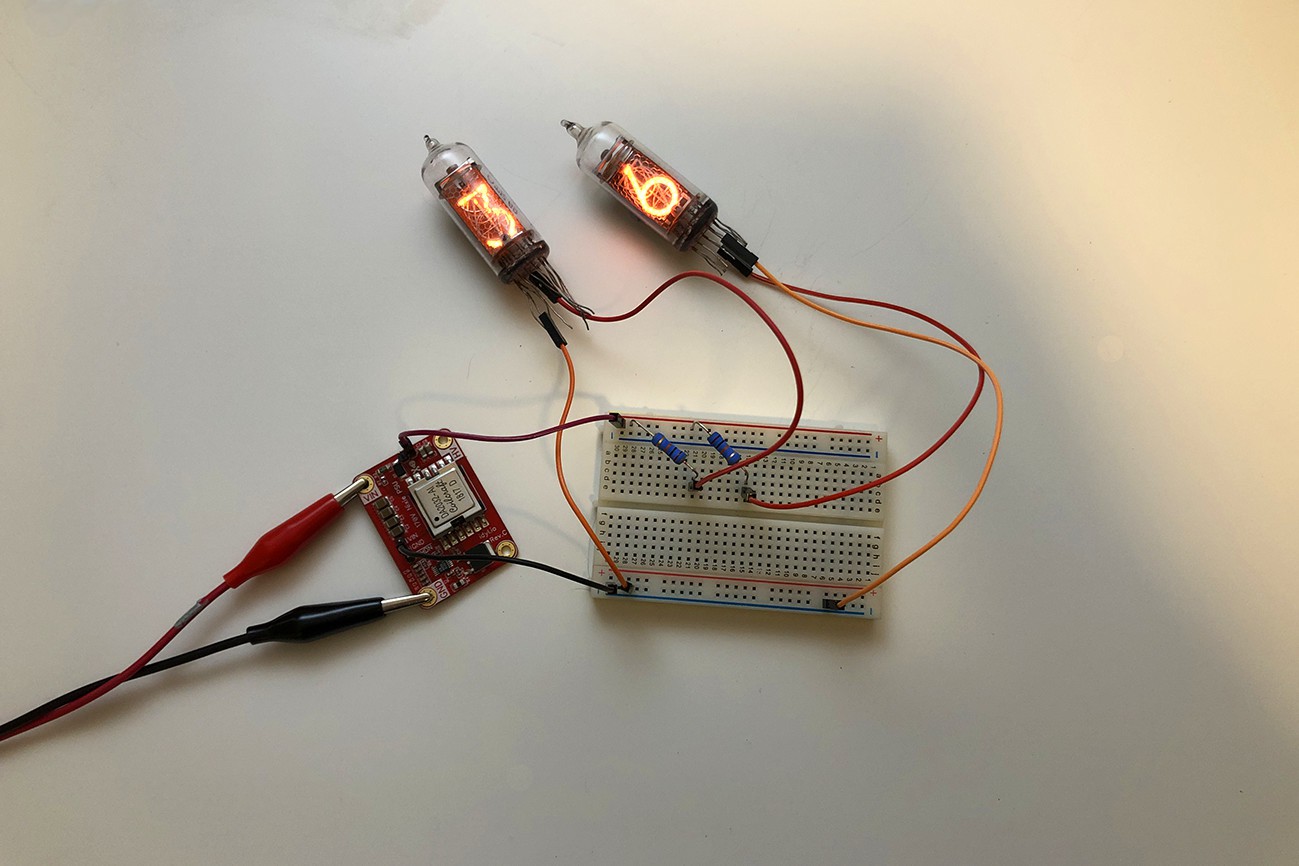
Thanks for spending the time documenting this. It was very interesting and informative.