When I started to look at commercial desktop size CNC, it seemed there were two kinds of models: the cheap ones from China at $300 (Banggood, Aliexpress, etc) and the other ones starting at $1200.
At first I thought I would buy a cheap one and upgrade it, however when looking a bit closer some issues appeared:
- The spindle will need to be replaced, and that would cost $100 + $50 for a new power supply
- The stepper motors looks like the lower end of the Nema 17 which might be a bit weak for machining aluminium
- The axis are using a lead screw and some rods which looks bulky and not sturdy enough
- The connection plates between the axis are 3d printed and I have some doubt on the sturdiness, squareness and accuracy of the assembly.
- They have a moving bed which means the footprint of the CNC is quite large compared to the working area.
It might be good for engraving PCBs but not for what I want to do.
When looking at other models, the standard Shapeoko could have been a fit but the price is a tad too high and the footprint a tad too big.
So I decided to build my own, which is more fun. I will be picking better quality components than the cheap ones, customizing the size and going for a moving gantry. I also live in an apartment, and need the CNC to be transportable and storable easily.
I'm trying to keep it as simple as possible while making sure I could increase the size one day.
I will try to make a short video explaining which components I picked and what's the reason behind. I will also publish the drawings of the fixture between the axis so that anyone can reproduce that, no matter the size of the CNC.
Below is the drawing with the dimension of the plates to be cut out and assemble to join the different axis. Please note those are not the final dimensions as I'm fine tuning them.
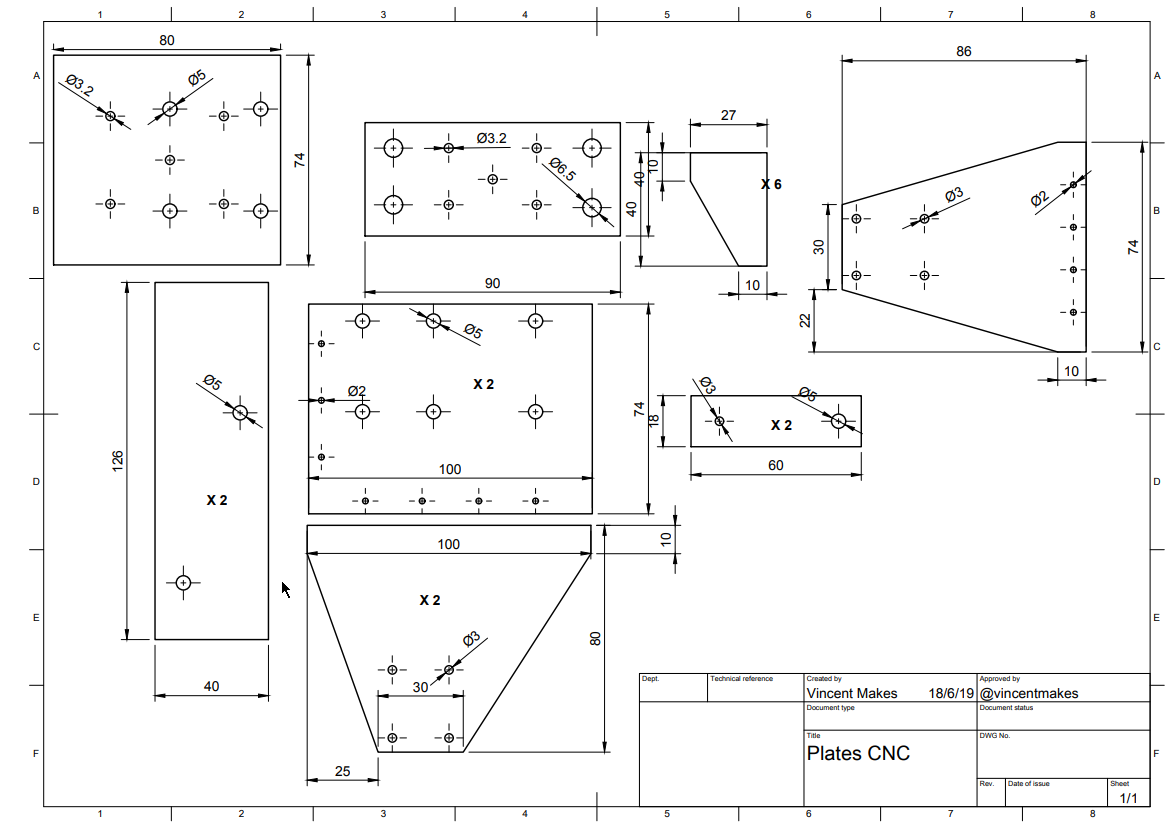
Here's the first assembly of X axis and connectors to Y axis
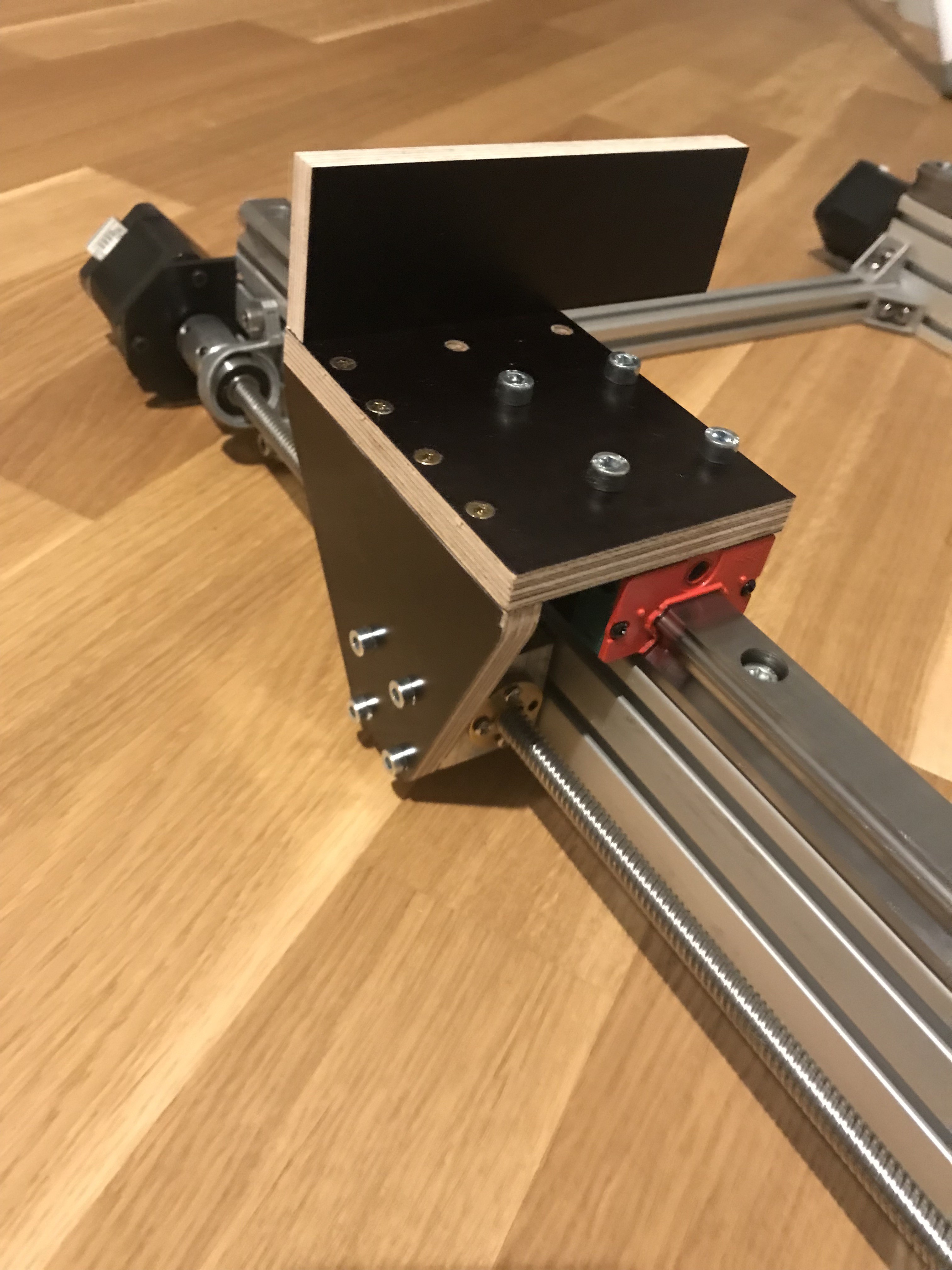
The CNC in a box, as advertised
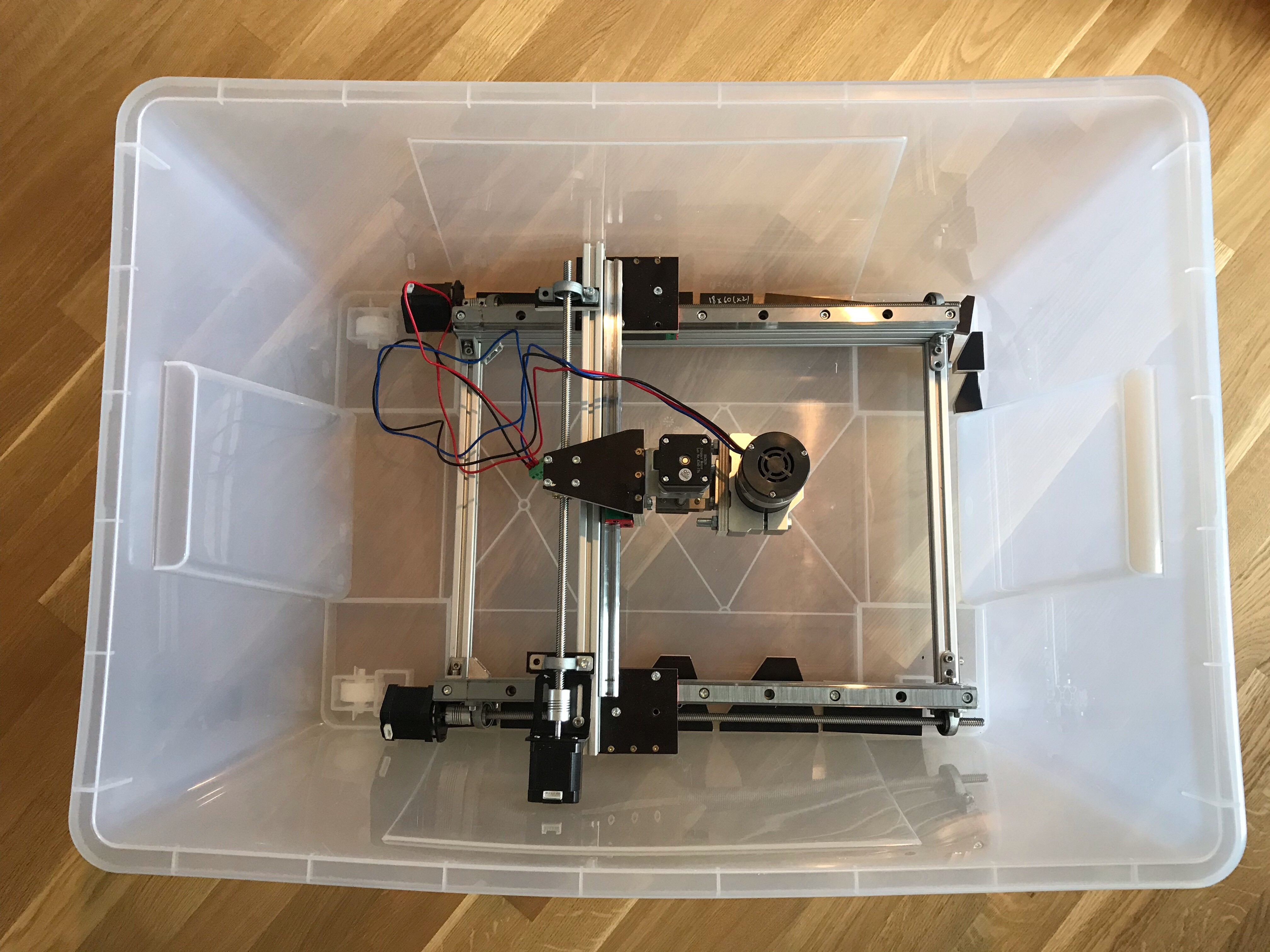
The front end of the enclosure
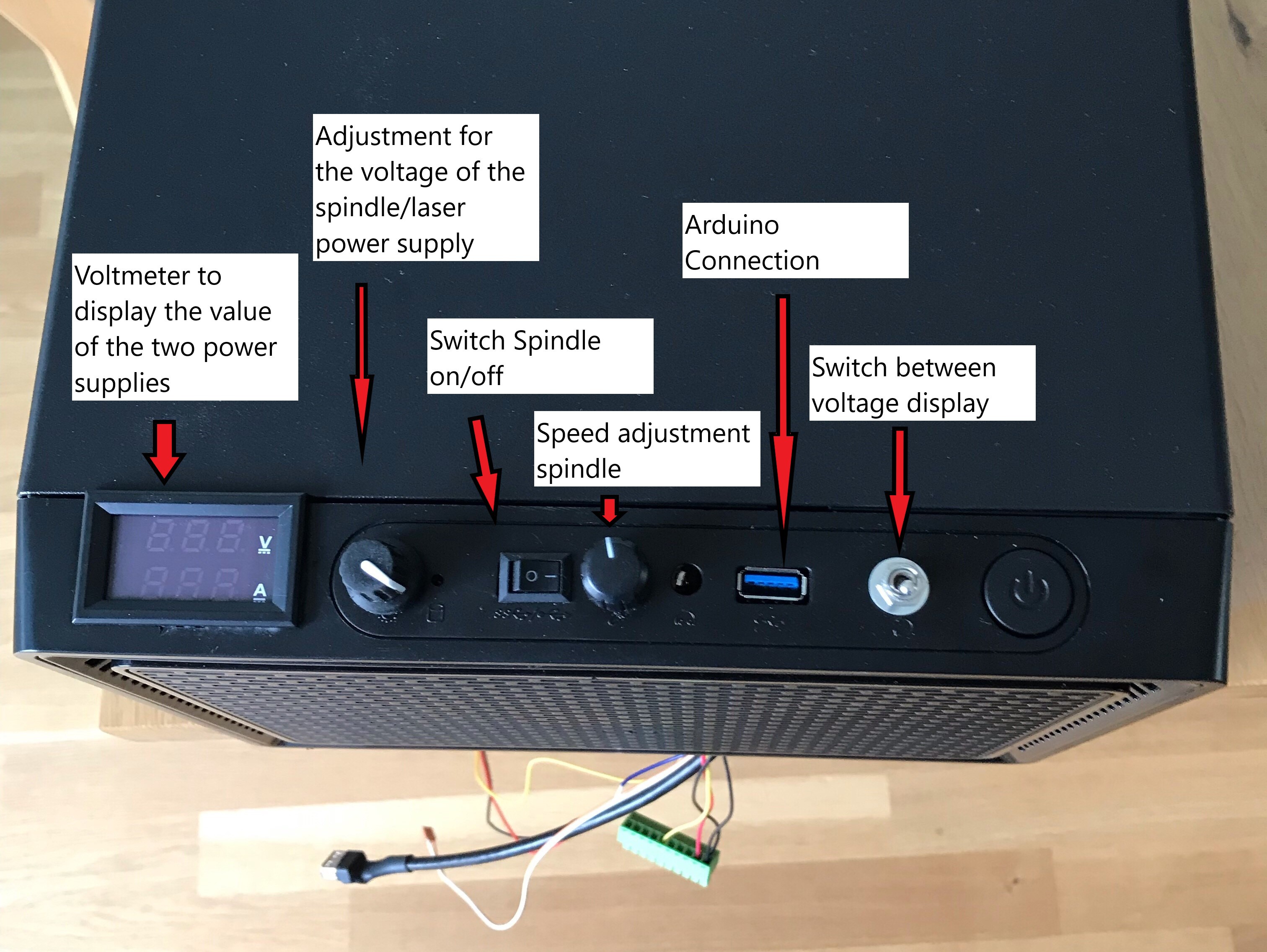
The back with the connectors
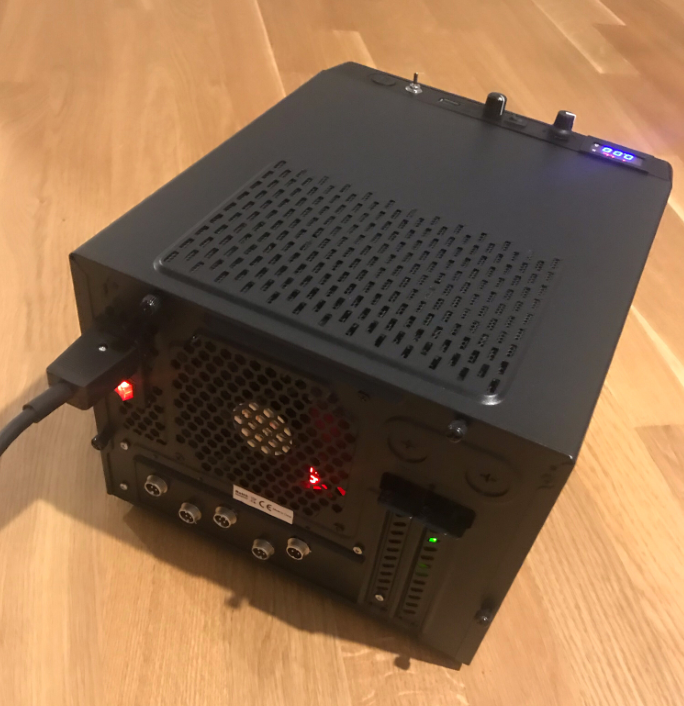