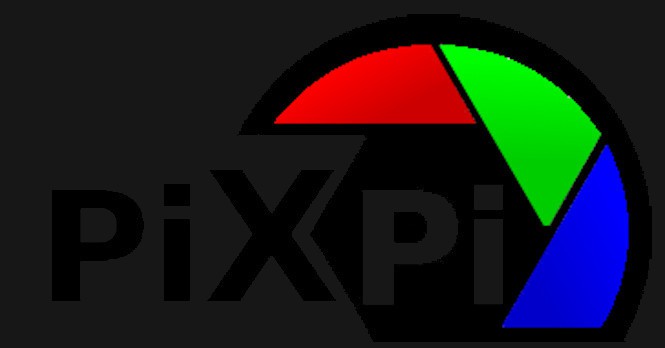
Project goals:
First goal of this project is simple, just creating controller which will make possible to create nice photos of things that are happening really fast in reliable way.
Second is to have possibility to configure it without using computer.
Third is to make interface such simple to be possible to use by photographers without technical knowledge.
Fourth is to make it as elastic as possible, so to have as much as possible ways to extend it's functionalities.
Fifth is to extend it's possibilities more than only for high speed photography, but also for macro photography, time-lapses, astro-photography by using motorised modules.
Long-term/future goal is to extend possibilities of interfacing with camera.
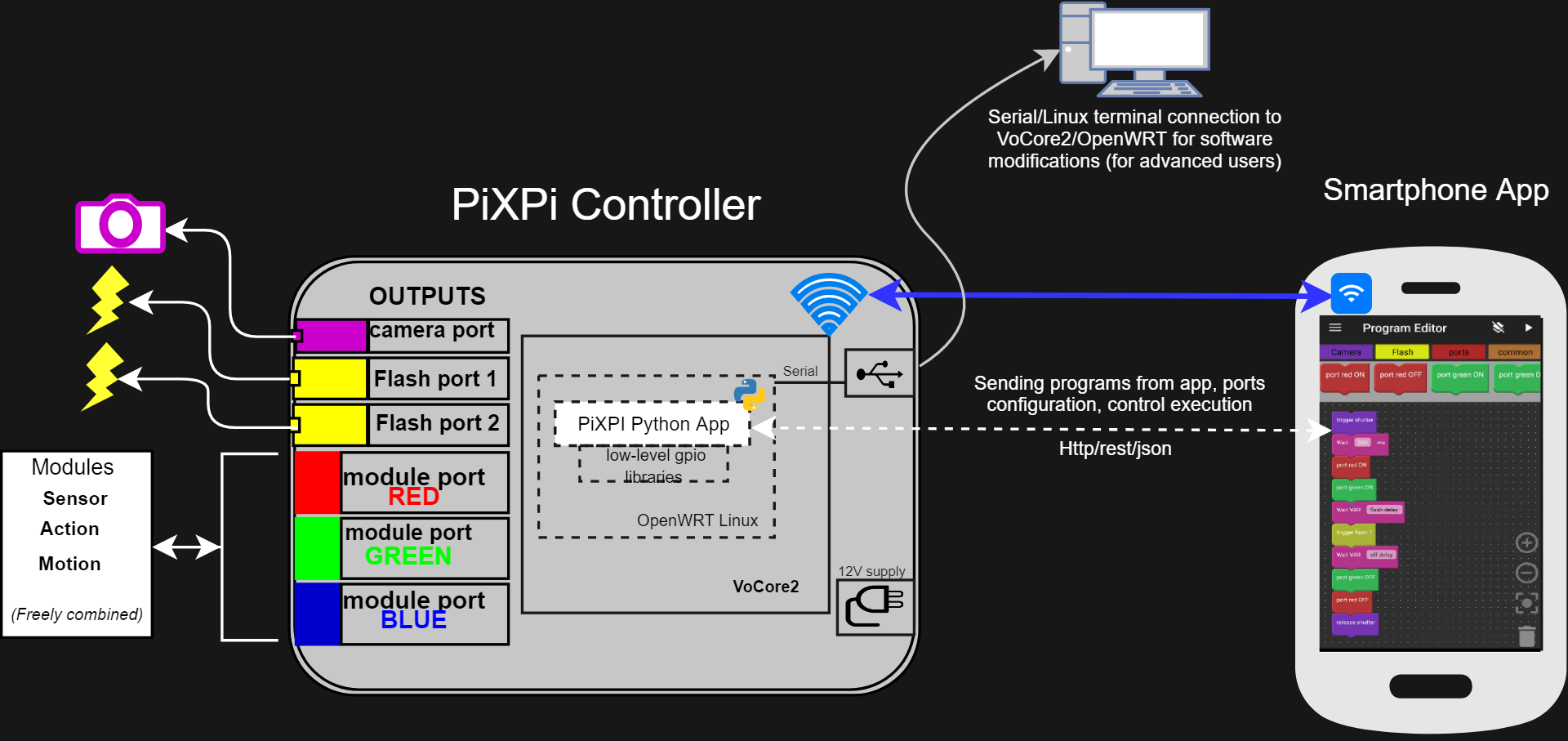
Controller board(PiXPI) is running under Linux(OpenWrt) control, on top of it is a Python application which is responsible for receiving, executing and controlling scripts created and sent from smartphone application, which I wrote for this project.
Smartphone App utilise Google's Blockly library for making creating of those scripts/sequences simple as possible. So in effect you can create them using graphical programming interface, using blocks instead of writing any code, no knowledge of Python programming is required for, user do not see Python code at all, he/she will just see blocks .
Scripts which are sent from smartphone are basically strings of python code, python was chosen as language which is powering controller, as it can execute code from string without compiling.
Scripts are sent from android application using Wifi->http->rest protocols.
Scripts are responsible for orchestrating photo shoot sequence, so camera shutter, flash and modules interfacing.
Those blocks with help of Blockly library are under the hood translated into python code and script is ready to be sent to controller board and and executed on it...
Controller board is powered by VoCore2 system-on-module, it's opensource system-on-module(https://vocore.io/).
And if you did it right, you will get some nice photos.
how to catch things that are happening very fast?
Simplifying what you need to do is trigger camera(or just flash, but will come to it later) when glass is cracking or droplets are colliding, so just in "right moment", but as this thing are happening very quickly it can be very hard to catch this "right moment" manually(i mean just pressing shutter button) as in 99% of cases you will miss the perfect shoot, as for example colliding drops when you will see splash is about 1-2ms.
So here external triggering coming with help, all DSLR camera has connector for remote triggering
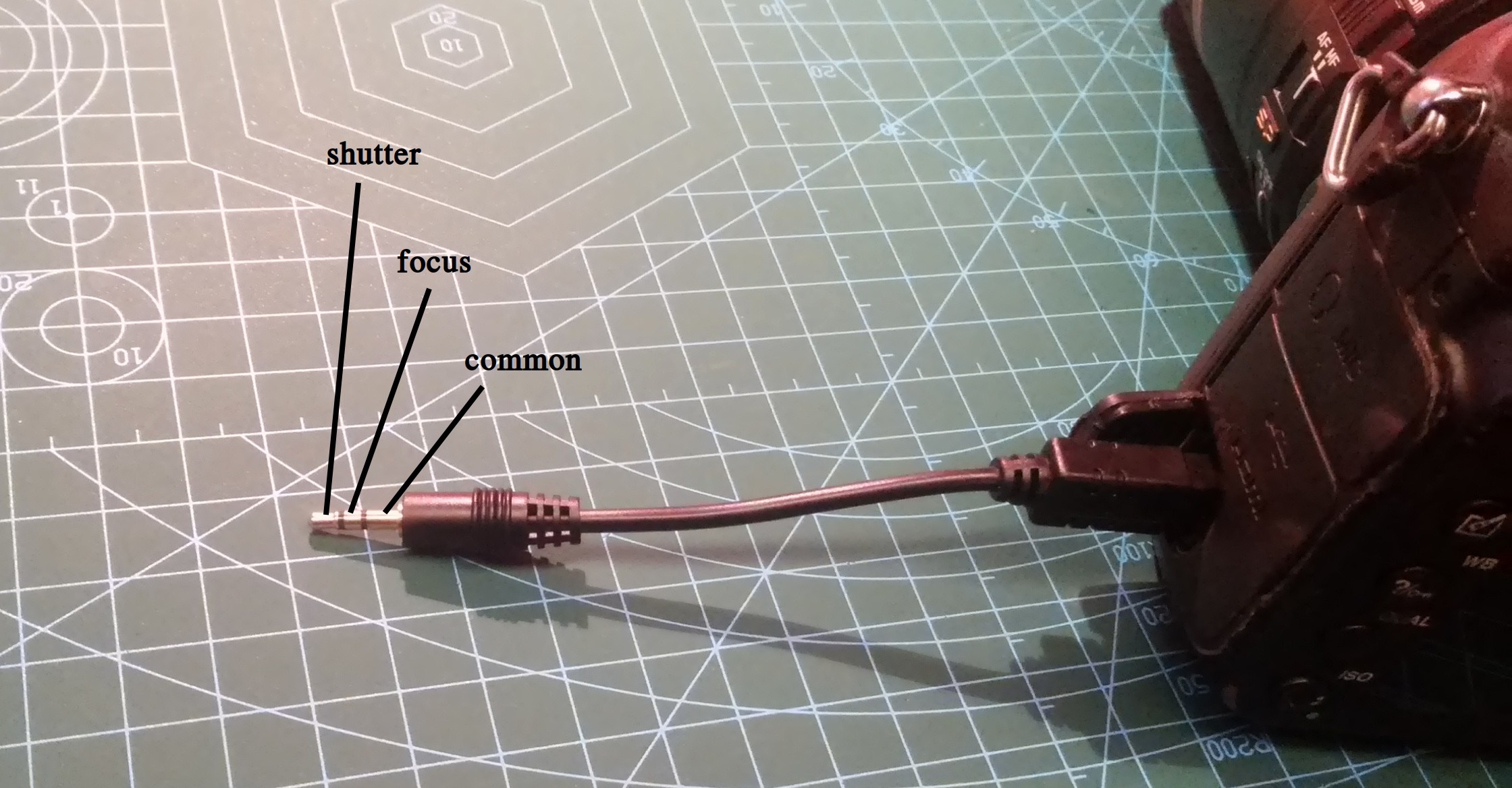
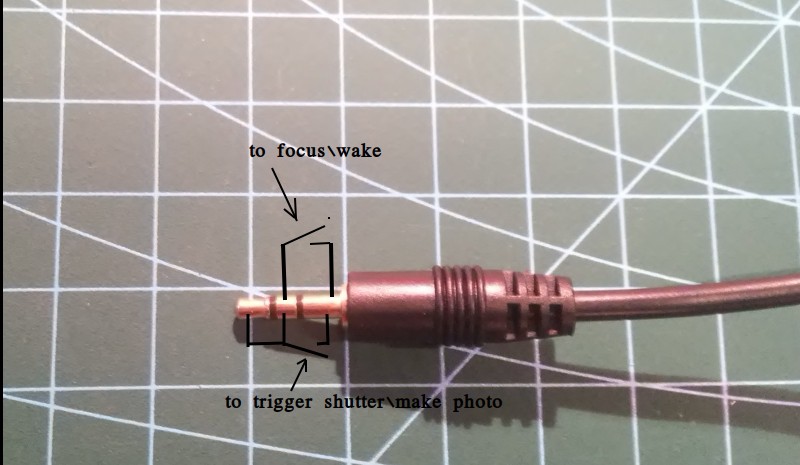
Future plans are to implement more interfaces to control more than just camera trigger.
Sense an action:
So using external triggering of, what can be done is that you can couple it with something which will trigger camera...
Read more »
Hi there, I have a question: does this can be used to control a DSLR-based film scanner ?
To be more clear, like these ones:
https://hackaday.io/list/175104-diy-film-scanners
Hope that helps/inspires.