Actuators: The upper arm motors are NEMA 23 76mm with a DM452Y driver. For the underarm motors NEMA 17 48mm with DM420Y driver.
Problem 1: These motors don't give position feedback so you just have to assume that they are in the position that they should be in. A few reasons why they could be in a different position than they should be in for example UnderAmpere, Overpressure, EM interference. For many cases, an open-loop configuration is reliable enough. But they still need a zero position some methods are end stops and hard stops. we use an end stop in our case a reed switch.
Problem 2: One other disadvantage of open-loop stepper motors is that the ampere isn't dynamic, what that means is that the ampere doesn't change under any conditions those conditions may be that the rotor doesn't co-align right with the stator. because the ampere isn't dynamic the motor generates more heat. That heat must escape our design isn't ideal for heat transfer for the motors. Mostly because there are 10mm plastics surrounding the motors. We tested for a few hours and the temperature is tolerable, but it's not great for the motors.
Bearings: The bearings are deep groove ball bearings. On axis 2 the force are almost all axial forces which the bearings are not suited for, so I don't think that's going to last long. Angular Contact Ball Bearings, are more suited for this joint. The only problem is, is that they're expensive compared to Deep Groove Ball Bearings.
Joints: On the stepper motors are planetary reduction gearboxes that reduce the rpm and increase the torque. We chose a cheap gearbox that comes with some downsides like low efficiency, heavy, and high backlash. We encircle that gearbox with bearings so the reducer sits inside that joint for a more compact design.
Problem 3: Because 3D print isn't strong enough to hold the weight of the motors and reducers we need reinforcement. We used 2mm thick sheet metal to hold the motor and reducer sturdy.
End Effector: You can design your own end-effector, maybe a suction cup, electromagnet, or laser. We already made an end effector that one is a 3 finger hand actuated by three servos.
Infrastructure: The end effector is an example, the configuration of the end effector is the one we use ourselves now. The separate stm32f030 is there for minimizing cables to the end effector, and because we are more flexible with what end effector we put on.
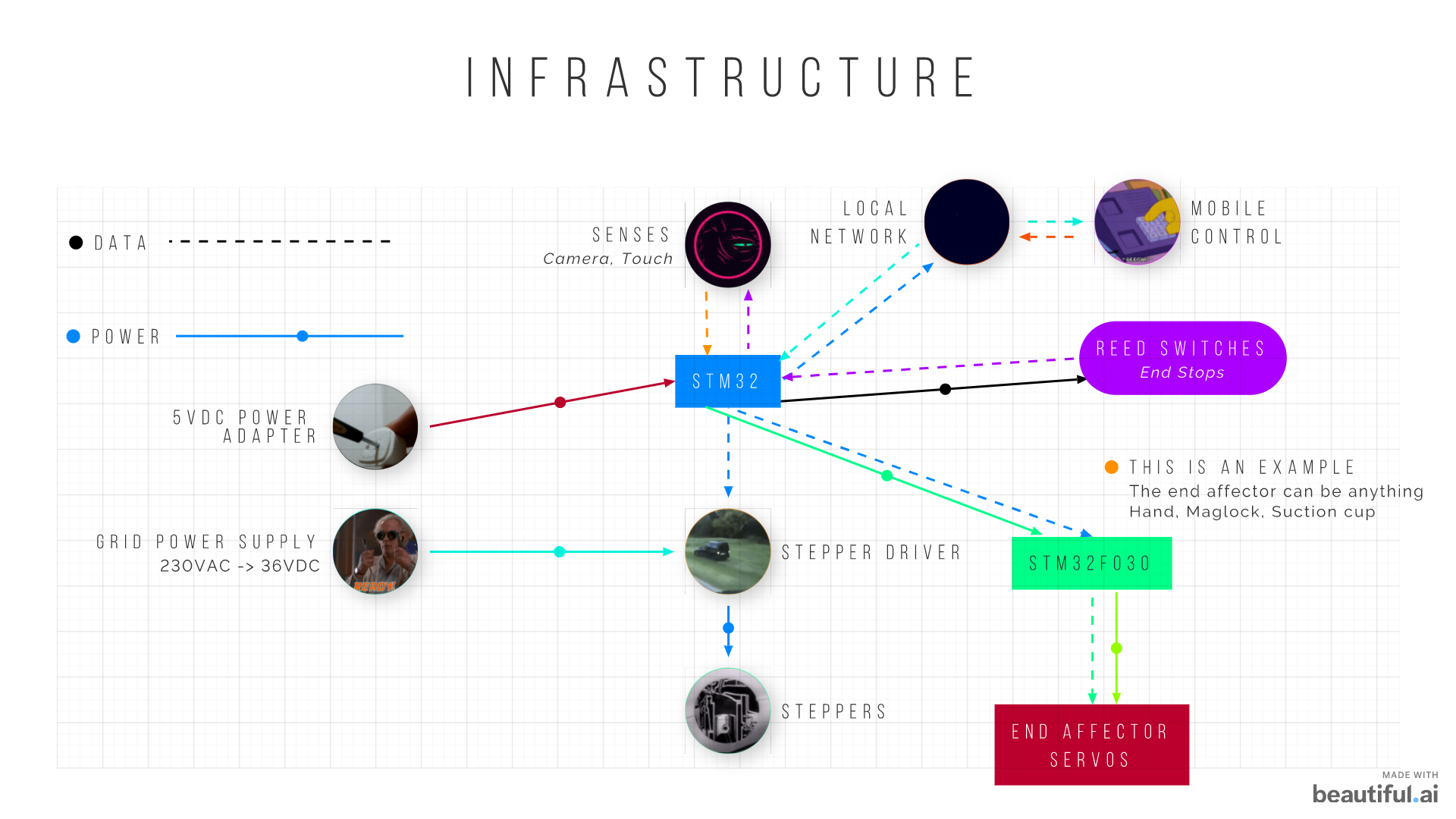