[19 Dec, 14:00]
I'm still trying to mine for a solution and I thought about having multiple concentric belt rings instead of 1 solid belt. It turns out that square cross-sectional belt exists and in a variety of lengths:
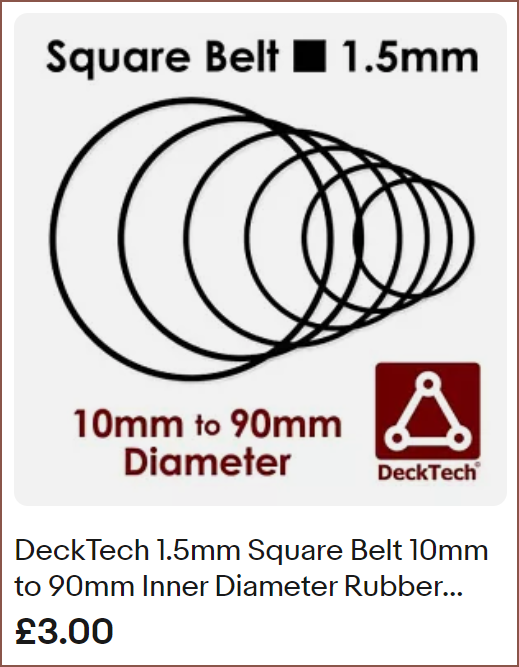
Thus I started to plan out a layout with 2mm belts, though I might also opt for 1.5mm.
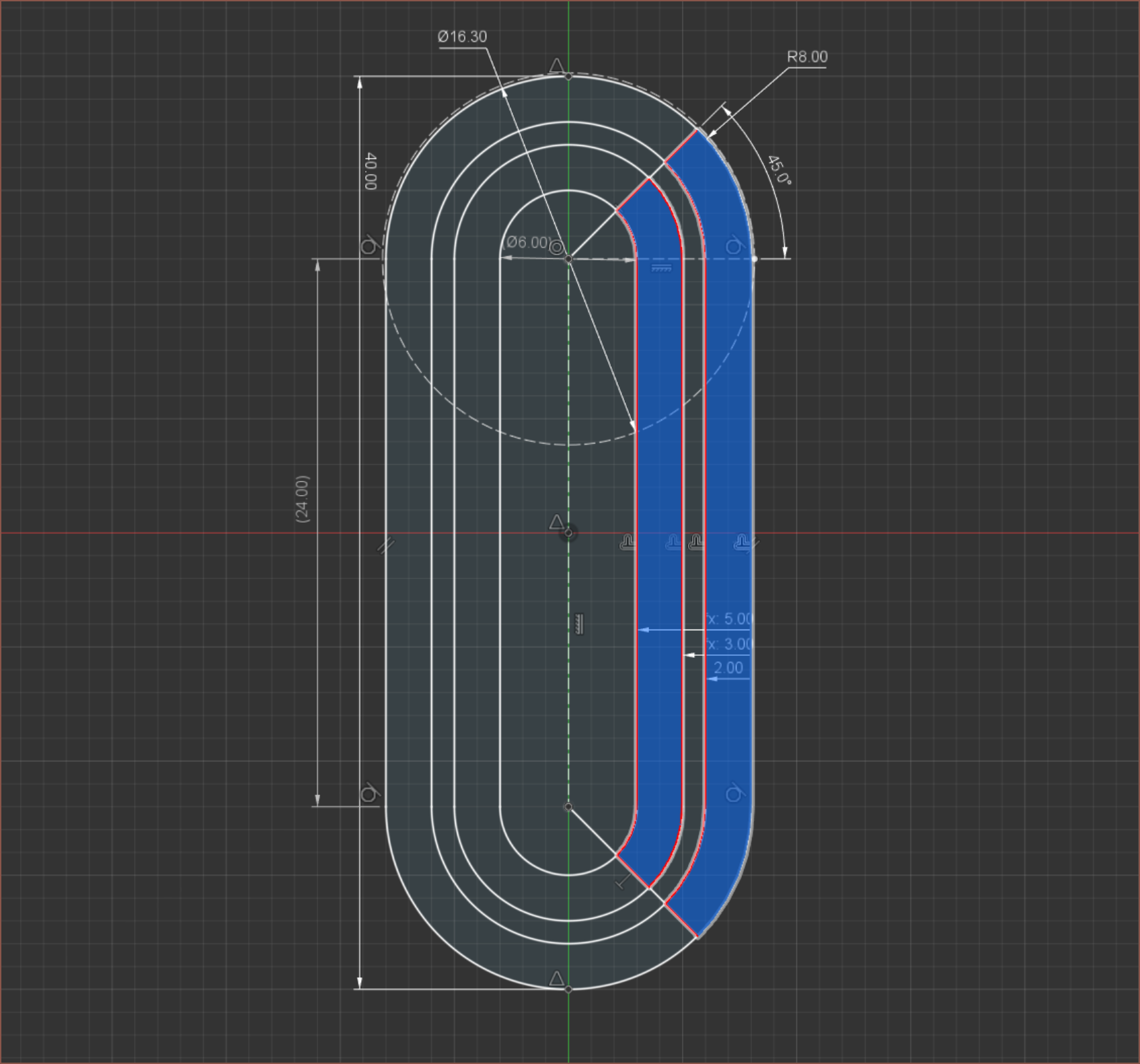
The bottom curve will have another pulley which houses the magnet and absolute encoder. The hope is that I'd be less hight constrained for PCB components, allowing for cheaper ADC and magnetic sensor alternatives.
My concerns with the design are
- the belts slipping on the motor
- the friction of the belt sliding in the highlighted section
- accurately measuring the force pushing down on the highlghted section
- longevity of these belts compared to fibre reinforced GT2 belts
- haptic feedback vibrations being absorbed by the belt
I'm going to see what cost and space saving potential there really is before going further.
[16:30] Nope.sfx
Just looked through Digikey with very loose filters and the ADC and encoder that I'm planning to use are also the cheapest that do what I need, irrespective of available PCB space. Seems Me In The Past drove a very tight Personal Best run.
Additionally, I tried Timespy with a 3mm thick plastic comb over Finger2-4 and I couldn't really feel any ergonomic benefit. I think the best case reduction in height is 5mm.
[22 Dec, 16:45]
Perhaps with more PCB space, I could opt for an RP2040 which would give me access to more programming assistance and likely has enough pins for a cheaper I2C or SPI encoder (such as what's used in Smartknob).
The main issue out of all the concerns I've highlighted is the haptic feedback vibrations being absorbed. It's unlikely that I can use rubber for this reason; it literally said on the product page that it absorbs vibrations. I believe GT2 will be fine since is fiberglass reinforced.
I've been looking into other solutions such as a track filled tightly with ball-bearing balls or small metal/printed chain, but I haven't yet found anything worthwile. I'm also thinking that I'd need to aim for 14mm of height. Even at higher thicknesses, the motor orientation switch still has merit because I'd then have the option to use a longer and more powerful motor.
I think the reason why my subconsious is weary of the current solution is because the grey zone for success is small (aka well defined). A width of 17.5mm will be well within the size to make a usable solution, and 20.5mm will have no solutions (for my hand size). That's a difference of only 3mm, half of the width of the GT2 belt.
Discussions
Become a Hackaday.io Member
Create an account to leave a comment. Already have an account? Log In.