I think 2 or 3 days ago, I was voting for the 2022 3D Printing Industry Awards and this came up:
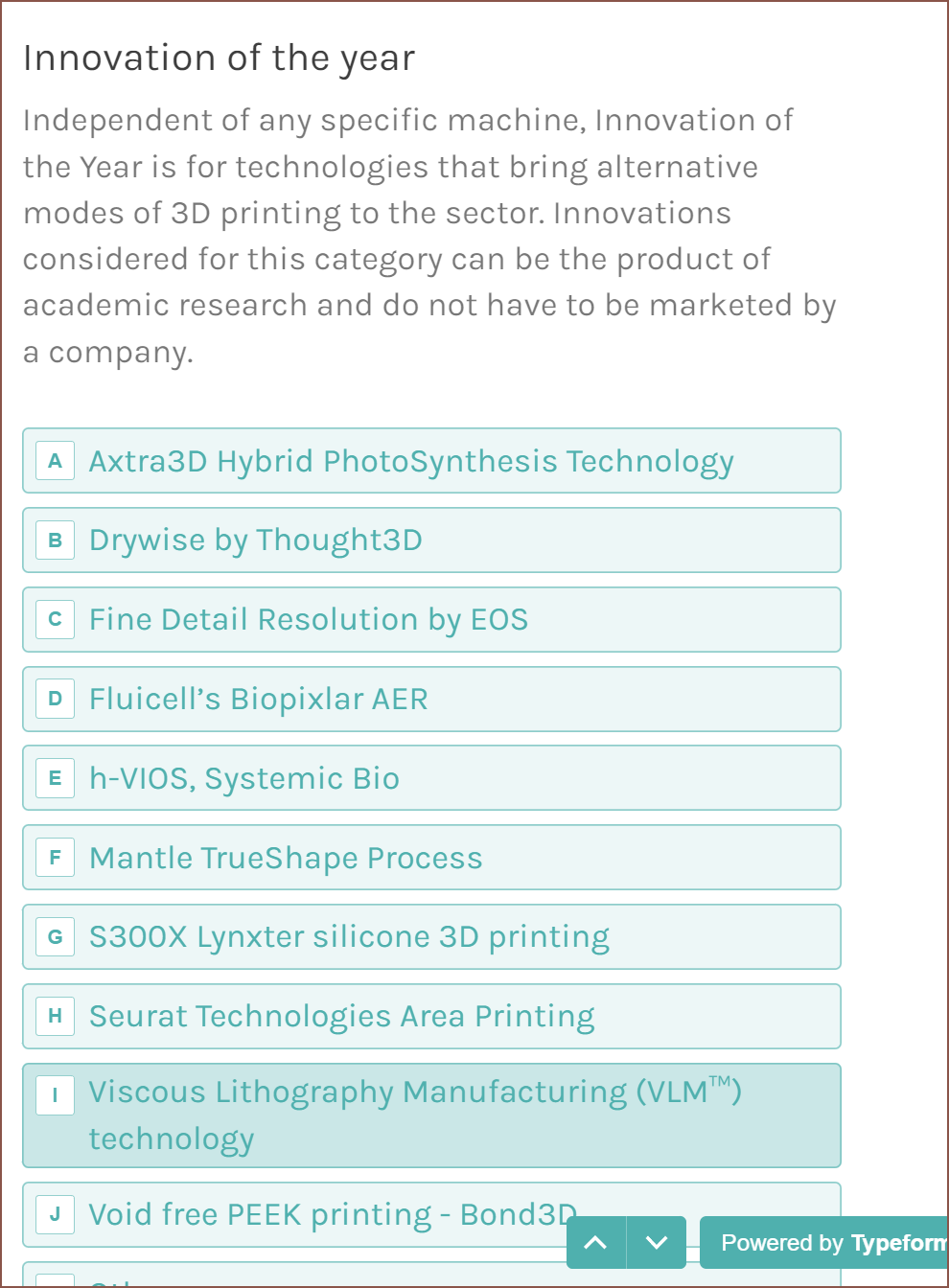
Now, obviously, I'm voting VLM, but I also wanted to see all the other technologies that were good enough to make it into this shortlist. The 2 that I'm still thinking of, days later, is Mantle's TrueShape and Seurat's Area Printing. The former uses a liquid metal mixture and the latter combines a low power, blue image beam with a high power, uniform intensity infrared beam to selectively sinter an area of metal powder.
Area Printing and the SecSavr Suspense are kind of similar in that a large build area is split into smaller area sections. I imagine an LCD panel or micromirror array was not able to handle or sufficiently block the infrared light directly, so the engineers had to get inventive.
Below are videos of both processes:
I like the background music of this video. It's got that same "innovative technology" vibe like in the VLM explaination video.
The liquid metal mixture process uses a CNC mill to improve surface quality before it's baked in an oven. An L^3 DLP process (remember that Liquid Laminate Lithography is just the name I'm giving to all resin based technologies that laminates a liquid onto a transparent film, VLM included) that I mentioned in some project log ages ago claimed to be able to work with both ceramics and metals, but I only remember the website focusing on ceramics. I'm thinking that a resin process wouldn't need milling except for surfaces that require very high precision.
Anyway, quite a lot of the current metal processes require a rather large and expensive oven. I doubt the Area Printing system helps out on cost, but it might be possible to integrate it inside a L^3 printer to save on space and increase the diversity of printable materials. I could even see it being possible that both the Area Printing and the more traditional MSLA systems work together, where
- The blue light photocures the metal/ceramic/glass infused resin in an area array, the same way in Area Printing
- The transparent film is removed, or the beam is redirected under the beam (like the Placement Block's laser)
- The patterned infrared light sinters the area array
I thought the new Hybrid PhotoSynthesis process (see below) was doing what I described in (1) but it sounds like what I thought of doing (written in a quick comment) where the edges of the pixelated layer is refined with a laser around the edges.
Another process that might be mergable into the L^3 ecosystem is Fortify's magnetic reinforcement:
Since I can't see a way to lay continuous fibres across any plane other than the one currently being printed/processed, this seems to be a good method to achieve non-planar reinforcement.
I'm just imagining a few company mergers down the line, where a printer the size of a dishwasher could be able to create a multicolour, reinforced and populated circuit board with integrated heatsink... Man I'm feeling like I should hold on to my papers, but I doubt it'll be remotely affordable.
Anyway, that's why I voted VLM as innovation of the year; these (3D printing) processes are kind of seperate but L^3 could allow them all to quad fusion merge.
[2024 - Jan 04] I've moved the research and thoughts that I had written as comments into the log itself, but more coherent.
Further research and ideas
2023 - Jan 05
Looking at the absorption spectrum of various metals and the ones I care about (mainly copper but also silver and steel) actually have rather high absorptions in the typical diode laser wavelength.
Here's another paper I found, which has this graph showing copper absorbing near 90% of 450nm light compared to something like 10% for the typical fibre laser wavelength of 1064nm. Sounds like an industrial laser that uses a 200W fibre laser could use a 20W diode laser. Why haven't I heard of such a printer? No idea; maybe my search is incomplete or the recent advancement of 20W diode lasers is so new that printers that use them are still being developed / tested.
I have found out about the VF20 from ZBAITU (same people that make the C40/C80 I'm curently planning to use) and the form factor does look nicer than other 20W options I've seen. However, at £414 it's hard to justify. If it was £300 (2X the C80) or something.. oh wait there's multiple listings--
NOUHHH I can ACTUALLY buy it for £301 quid! I got baited in! How am I supposed to say no to that??" It'll be so hard to justify the C80 now. I've been thinking "If I could get 20W [in my league budget], that would be great. I'd have more power just in-case, can cut thicker/faster and they'd probably be 24V like the rest of the system" but it was a no-deal at the >£450 prices. At £300, and especially with the compact 80x50x80mm footprint, it's more like a simple but inescapable choice.
Jan 08
Conveniently enough, I can buy atomized copper, iron and stainless steel straight from Amazon UK at seemingly affordable prices (copper and iron are <£25/kg and 316 stainless is about £60/kg). The particle sizes are 45um so I'd expect minimum layer thicknesses to be over 90um.
I do wonder if it's possible to print an iron part with a stainless steel surface. I couldn't find anything on a quick google search on "stainless steel plated iron" though.
Jan 09
I saw the below video and parts look great. I will be adding "3D printed copper and stainless steel" onto the project roadmap.
I might also look into a small polishing tool spindle, but I don't have lab/industry grade prints in mind so the surface roughness is probably fine. It really just depends on how smooth threaded surfaces need to be, or surfaces for printed bearings. Yeah... I should look into it just in-case as it would be harder to integrate it later down the line. There's also the option of using BLDC servos instead of steppers for the pick+place tools so that they can be used for both purposes.
I'm also reading this paper about additively manufacturing in copper and it's mentioned that "Fine powders with an average particle size lower than 50 μm are typically employed" so it suprisingly sounds like these online powders are good enough for science. Since it's being embedded into a liquid photopolymer, hopefully I don't have to worry about particle shape, which is something I've heard being an issue for SLS.
It is then mentioned that laser absorption is higher because of particle reflections. That sounds promising, suggesting that if I keep the photopolymer optically clear, materials that have a lower absorption of 450nm light might still be viable. Additionally, the gantry system is much slower than the control systems used in industrial settings, meaning more energy would be absorbed, further reducing optical power requirements.
But yes, I do imagine that printing metal this way would be about as fast as using an ultrafine nozzle on an FFF printer. I'm now considering that I should have X being the moving axis for the Placement Block for higher stiffness, thus higher accelerations.
Jan 13
I read this paper which talks about sintering a track of copper powder with a 445nm laser. The lower end of their wattage recommendation was 60W. Don't fear though, because the laser they use has a dot size of 0.2mm and these AliExpress lasers are 0.08mm, so the "equivalent wattage" calculation is 60 * (0.08^2)/(0.2^2) = 9.6W!!
Jan 22
I'm watching the price of the diode lasers and I think by the time I'm ready to buy, a suitable 20W laser will be £280. This lines up with the other module prices of £70 per diode.
I'm not such a fan of spending £420 on a 30W laser module, but I'd have to see how much power iron/stainless requires before deciding on going with a higher wattage laser. Shockingly, 33 - 40W lasers are coming out very soon.
Discussions
Become a Hackaday.io Member
Create an account to leave a comment. Already have an account? Log In.
I read [https://assets.researchsquare.com/files/rs-1406173/v1/6af064a8-3aed-448e-98e7-6417ba9ffdc0.pdf?c=1646754530] which talks about sintering a track of copper powder with a 445nm laser.
The lower end of their wattage recommendation was 60W. Don't fear though, because the laser they use has a dot size of 0.2mm and these AliExpress lasers are 0.08mm, so the "equivalent wattage" calculation is 60 * (0.08^2)/(0.2^2) = 9.6W!!
Are you sure? yes | no
Saw this video [https://www.youtube.com/watch?v=LIqt7muSFM8] and parts look great. I will be adding "3D printed copper and stainless steel" onto the project roadmap.
I might also look into a small polishing tool spindle, but I don't have lab/industry grade prints in mind so the surface roughness is probably fine. It really just depends on how smooth threaded surfaces need to be, or surfaces for printed bearings. Yeah... I should look into it just in-case as it would be harder to integrate it later down the line. There's also the option of using BLDC servos instead of steppers for the pick+place tools so that they can be used for both purposes.
Are you sure? yes | no
Conviniently enough, I can buy atomized copper, iron and stainless steel straight from Amazon UK at seemingly affordable prices (copper and iron are <£25/kg and 316 stainless is about £60/kg). The particle sizes are 45um so I'd expect minimum layer thicknesses to be over 90um.
I do wonder if it's possible to print an iron part with a stainless steel surface. I couldn't find anything on a quick google search on "stainless steel plated iron" though.
Are you sure? yes | no
I'm reading [https://www.intechopen.com/online-first/83547] and it's mentioned that "Fine powders with an average particle size lower than 50 μm are typically employed" so it suprisingly sounds like these online powders are good enough for science. Since it's being embedded into a liquid photopolymer, hopefully I don't have to worry about particle shape, which is something I've heard being an issue for SLS.
It is then mentioned that laser absorption is higher because of particle reflections. That sounds promising, suggesting that if I keep the photopolymer optically clear, materials that have a lower absorption of 450nm light might still be viable. Additionally, the gantry system is much slower than the control systems used in industrial settings, meaning more energy would be absorbed, further reducing optical power requirements.
But yes, I do imagine that printing metal this way would be about as fast as using an ultrafine nozzle on an FFF printer. I'm now considering that I should have X being the moving axis for the Placement Block for higher stiffness, thus higher accelerations.
Are you sure? yes | no
Looking at the absorption spectrum of various metals [https://www.researchgate.net/figure/Variation-of-absorptivity-and-reflectivity-with-a-wavelength-b-linearly-polarized_fig1_328431094] and the ones I care about (mainly copper but also silver and steel) actually have rather high absorptions in the typical diode laser wavelength.
Here's another paper I found [https://link.springer.com/article/10.1007/s00170-021-06774-4], which has a graph showing copper absorbing near 90% of 450nm light compared to something like 10% for the typical fibre laser wavelength of 1064nm. Sounds like an industrial laser that uses a 200W fibre laser could use a 20W diode laser. Why haven't I heard of such a printer? No idea; maybe my search is incomplete or because 20W diode lasers are relatively new products.
I have found out about the VF20 from ZBAITU (same people that make the C40/C80 I'm curently planning to use) and the form factor does look nicer than other 20W options I've seen. However, at £414 it's hard to justify. If it was £300 (2X the C80) or something--
"oh wait... there's multiple listings... hey this one [www.aliexpress.com/item/1005003176767302.html] is way cheaper... and there's coupons... NOUHHH I can ACTUALLY buy it for £301 quid! I got baited in! How am I supposed to say no to that??" It'll be so hard to justify the C80 now. I've been thinking "If I could get 20W [in my league budget], that would be great. I'd have more power just in-case, can cut thicker/faster and they'd probably be 24V like the rest of the system" but it was a no-deal at the >£450 prices. At £300, and especially with the compact 80x50x80mm footprint, it's more like a simple but inescapable choice.
Are you sure? yes | no
I'm watching the price and I think by the time I'm ready to buy, this laser will be £280. This lines up with the other module prices of £70 per diode.
I'm not such a fan of spending £420 on a 30W laser module, but I'd have to see how much power iron/stainless requires before deciding on going with a higher wattage laser. Shockingly, 33 - 40W lasers are coming out very soon.
Are you sure? yes | no