The Airman Rocket
Technical Paper
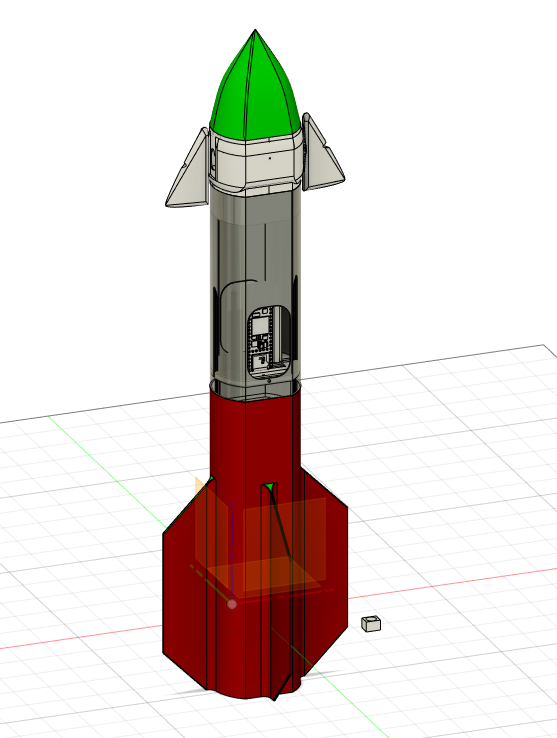
Table of contents
- Title Page
- Table of contents
- Abstract
- Problem statement & Rationale
- Design
- Design cont.
- Design cont.
- Evaluation
- Evaluation Cont.
- Conclusion
- Conclusion cont.
- references
Abstract
Model rocketry is an advancing hobby, those who participate in rocketry are always seeking ways to push the technical boundaries of the hobby. Creating a system that can perform well, can be tuned, and get recovered are goals of any hobbyist. Embedding computers in rockets is increasing the sophistication of rocket systems, it can allow the user to record data and perform flight maneuvers such as stabilization, stage separation, or guided flight. Legacy systems feature separate computers each for handling different tasks such as booster ignition, parachute deployment, or stabilization. Newer systems such as the EasyMega by Apogee Components or the Signal R2 TVC Kit from BPS space can perform these tasks simultaneously but at a high price tag of $350. Airframes for model rockets are traditionally made of cardboard or carbon fiber, but these materials make it difficult for custom shapes or added airframe complexity.
The Airman Rocket is a fully 3d-printed, auto-stabilizing, and data collecting model rocket, the rocket is designed to be fully re-usable, modular, and open source. It features an on-board flight computer, accelerometer, and servo driver for performing data collection and rotation stabilization. Stabilization is achieved through small wings on the front of the aircraft that are actuated by servos for steering.
The entire build of the Airman rocket can cost as little as $80 and offers a higher degree of customization than the other systems. In addition to the flight computer the actual rocket and flight components are included in this price tag. All documentation and files for the aircraft are available for free and is built by the consumer. The Airman rocket keeps the cost of entering the hobby low and acts as an educational tool and community platform for Those who chose to participate in the project. The rocket a still maintains high performance as a priority and accomplishes the flight profile for which it is designed.
Problem statement
Using a model rocket as the instrumentation platform, how can I record data, stabilize flight, and recover the rocket using only open-source hardware and software? The solution must be free as an intellectual property and be more affordable for the user than current options on the consumer market. The solution should allow the user to expand on the original project and learn various aspects of model rocketry.
Rationale
Using open-source micro-controllers for the rockets primary flight computer has large advantages such as; the ability for I/O expansion, the ability to be programmed in modern powerful code languages, and highspeed processing. Stabilization can be most easily achieved through fin-control in high speed applications. Fin-control was chosen over other control methods such as thrust vector or reaction wheel control because of its low mechanical complexity. 3-d printing achieved low cost custom parts. Parts could be quickly and easily prototyped and tested. Attempting to make the complex parts involved for an aircraft of this type would prove extremely difficult using any other method. 3d printing allowed for a very unique airframe shape that would be almost impossible to make using traditional methods. Posting the files online for free allows the project to build a larger community and allows the technology to disseminate to as many people as possible.
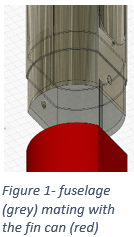
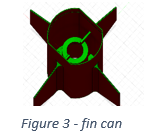
Design
For the airframe of the rocket the design was done in a CAD modeling software. The models were then exported for 3d-printing and were fabricated in PETG...
Read more »