Tuesday, 11/07/2023, 17:54.
Well, I believe this will be my last project log on "theorics" of electric motors, and if you didn't notice, that's more or less "my last attempt", first I will list everything I need to do, then later I will make project logs on me doing the stuff.
Anyway, to the topic:
In the last Project Log I talked about how to make the stator and/or the rotor, but I didn't talk about how to make the winding, and that includes the motor phase and arrangement. So this will be a short Project Log (or so I believe).
Basically, every motor brushless motor has a sequence of turns (clockwise and counter-clockwise) of copper in its stator.
That is determined by the number of teeth on the stator and number of magnets on the rotor.
I think this link that DekuTree64 suggested may be useful: https://www.bavaria-direct.co.za/scheme/calculator/
PS: poles is just another name for magnets.
Since I will be using the eagle power 3D model (that unfortunately has 39 magnets on its rotor instead of 40, like the real one), which has 36 stator teeth and 40 magnets, needing the following arrangement:

https://grabcad.com/library/x8308s-outrunner-motor-1
Of course, you could simply use the other U-motor that I posted: https://grabcad.com/library/t-motor-u8-lite-1
It has 42 magnets and 36 stator teeth.
Also, these videos may help:
Just like in the first video, I would advise for a Y terminations, with higher torque with less rpms.
Relevant link/article: https://things-in-motion.blogspot.com/2019/01/selecting-best-pole-and-slot.html
It gives a lot of relevant information taht may or may not be mentioned in the videos, however it got my head scratching because in the document it links showing how many slots you would need for every magnet, I guess I don't understand brushless motors well enough to actually talk about every aspect of it. lol
---------------------------------------------------------------------------
The number of turns of each stator teeth is kinda hard to find, I couldn't find an specific calculator online, but I got advised both by ChatGPT and the Quora AI to use 20 to 24 turns on each stator teeth.
I asked around and I'm waiting the answers come by, which may or may not appear, but I believe this is a correct number of turns per stator:
"Most RC brushless motors range between ten and twenty-seven copper windings, or motor turns. The number of turns affects the motor's electrical resistance."
Source:
https://clutchrc.com/rc-motor-turns-to-kv/#:~:text=Most%20RC%20brushless%20motors%20range,affects%20the%20motor's%20electrical%20resistance.
---------------------------------------------------------------------------
Tutorials on hall sensors for brushless motors may be useful, after all these would help the ESC to properly power each stator teeth.
Edit¹:
Also, don't forget about the halbach array, it can improve the performance of your electric brushless motor significantly.
https://things-in-motion.blogspot.com/2018/12/the-advantages-and-disadvantages-of.html
https://things-in-motion.blogspot.com/2019/07/bldc-pmsm-end-turns-and-torque.html
https://things-in-motion.blogspot.com/2019/03/basic-bldc-pmsm-efficiency-and-power.html
(this blog has a lot of relevant and useful information for your DIY brushless motor)

As far as I am aware, the K=4 halbach array is the best for electric motors.
This video may also be useful.
Edit²:
Just now I found this video:
In simple terms, neodymium magnets kinda have a "ranking" system, and the strongest you can find online is N52 neodymium magnets.
Now, in the video the guy shows a different kind of use for permanent magnets, in his case, he put a small space between two magnets facing each other, not very useful in an electric motor.
However, he wraps steel wire around the magnets and for some reason it increases its magnetic strength.
You could do that to the permanent magnets on the rotor of the brushless motor in order to increase its magnetic strength even more.
Also, you may not even need wires:
---------------------------------------------------------------------------
Chat GPT explains:
"Wrapping steel wire around neodymium N52 magnets can increase the magnetic field strength due to a phenomenon known as "magnetic flux concentration" or "magnetic flux guiding." When a magnetic field passes through a material with high magnetic permeability (such as steel), the magnetic lines of force tend to concentrate or follow the path of least resistance provided by the material.
Here's why it happens:
- Magnetic Permeability: Steel has a much higher magnetic permeability than air or other non-magnetic materials. This means that it can conduct magnetic flux more effectively, allowing the magnetic field lines from the neodymium magnet to flow more easily through the steel.
- Flux Concentration: When you wrap steel wire around the neodymium magnet, the magnetic field lines tend to concentrate within the steel due to its higher permeability. This results in a stronger magnetic field in and around the steel-wrapped magnet.
- Closed Loop: The steel wire acts as a closed-loop path for the magnetic field, providing a continuous path for the magnetic flux to flow around the magnet. This helps prevent the magnetic field from spreading out and redirects it back into the magnet, effectively increasing the magnetic field strength.
As for the type of wire used, different materials will have varying effects on the magnetic field strength:
- Ferromagnetic Materials: Ferromagnetic materials like iron or steel have high magnetic permeability and are effective at concentrating magnetic flux. Steel wire is a common choice due to its availability and affordability. Thicker steel wires or multiple layers can further enhance the flux concentration.
- Non-Magnetic Materials: Non-magnetic materials like copper or aluminum do not significantly affect the magnetic field strength. In fact, they may slightly decrease the field strength by providing an alternative path of lower permeability.
In summary, wrapping steel wire around neodymium N52 magnets increases the magnetic field strength due to magnetic flux concentration and providing a closed-loop path for the magnetic field. While steel wire is an effective choice, other ferromagnetic materials with high permeability can also be used to further enhance the magnetic effect. When experimenting with different materials, it's essential to consider the safety implications and handle strong magnets with care to avoid accidents or injuries."
"The number of laminations in a brushless motor can vary based on design considerations and specific requirements. Generally, brushless motors with low RPM and high torque are designed to have a higher number of laminations in their stator cores. This is because a higher number of laminations can help reduce core losses and improve the efficiency of the motor.
It's not uncommon for such motors to have a stator core with around 18 to 36 laminations or even more. The exact number of laminations can depend on factors such as the motor size, the desired torque characteristics, the choice of materials, and the manufacturing techniques used."
"The frequency (Hertz) at which brushless motors operate can vary widely depending on their design, application, and intended use. There is no one-size-fits-all answer to this question because brushless motors can be designed to operate at different frequencies based on factors such as motor size, desired speed range, torque requirements, and efficiency considerations.
However, here are some general guidelines for the frequency range of brushless motors across various applications:
- Low RPM, High Torque Applications: Brushless motors designed for low RPM and high torque applications, such as industrial machinery and robotics, might operate in the range of a few hundred Hertz (e.g., 100-500 Hz) or even lower. These motors are optimized for torque production at low speeds.
- Medium RPM Applications: Many brushless motors used in consumer electronics, automotive systems, and other applications fall into the medium RPM range. These motors might operate in the range of a few thousand Hertz (e.g., 1000-5000 Hz).
- High RPM Applications: Brushless motors used in high-performance applications, such as drones or high-speed industrial tools, can operate at much higher frequencies. These motors might operate in the range of tens of thousands of Hertz (e.g., 10,000-50,000 Hz) or even higher.
It's important to note that the motor's operating frequency is closely related to its speed, as well as the number of pole pairs and the design of the motor controller. The motor controller generates the appropriate frequency signals to control the motor's operation and achieve the desired speed and torque characteristics.
For a specific application, the operating frequency of a brushless motor will be determined by the motor's design and the requirements of the system it's being used in. If you have a particular application in mind, it's best to consult with motor engineers or manufacturers to determine the appropriate operating frequency for your specific needs.
The operating frequency (Hertz) of a brushless motor can influence the design considerations, including the number of laminations used in the motor's stator core. The relationship between frequency and laminations is tied to the concept of core losses, which are losses of energy in the magnetic core of the motor due to factors like hysteresis and eddy currents.
Here's how the operating frequency can impact the number of laminations:
- Higher Frequency and More Laminations: When the operating frequency of the motor is higher, there is a greater potential for increased core losses due to eddy currents. Eddy currents are circulating currents that can form within the magnetic core of the motor and result in energy losses. To mitigate these losses, more laminations are often used in the stator core. Each lamination layer is insulated from the others, which helps to break up the pathways for eddy currents and reduce their effects. More laminations effectively increase the resistance to eddy current flow and help improve the motor's overall efficiency.
- Lower Frequency and Fewer Laminations: In motors that operate at lower frequencies, such as those designed for high torque at low speeds, the risk of significant eddy current losses might be lower. Therefore, these motors might use fewer laminations in their stator core to minimize manufacturing complexity and costs while still achieving acceptable efficiency.
It's important to note that the number of laminations is just one factor in motor design that affects efficiency, performance, and losses. Other factors include the choice of core materials, the geometry of the motor, the winding configuration, and the quality of manufacturing processes. Engineers and designers carefully balance these factors to create a motor that meets the specific requirements of the application while minimizing losses and maximizing efficiency.
Also, just now I stopped to consider the amount of magnets that I would need.
Assuming that I would only need one line of magnets, I would need around 1200 neodymium magnets for every brushless motor in the mech/exosuit.
Not counting the fact that these motors are 5 times longer than their original counterpart and the fact that I will be using halbach array, which ads even more magnets to the motor.
Neodymium magnets are cheap, but in these quantities, it is really, really costly.
---------------------------------------------------------------------------
Well, I talked about it in other Project Logs, but I believe it would be better to just organize everything in a single place:
By the way, I was thinking on using glitter sprayer for cakes as the sprayer for both the Iron-Air battery electrodes and the electric motor soft magnetic composite stator.
One thing I also forgot to talk about in the previous Project Log about the Iron-Air battery is the vacuum box.
You don't really need actual vacuum to work with pure iron powder, you could use an argon and/or helium filled glove box in order to work with these highly reactant materials (like pure iron powder).
I just say this because it is very hard to maintain actual vacuum and inflating a giant transparent plastic box may be easier to build and use.
You could just use helium cans for party balloons or argon gas for wine storage:
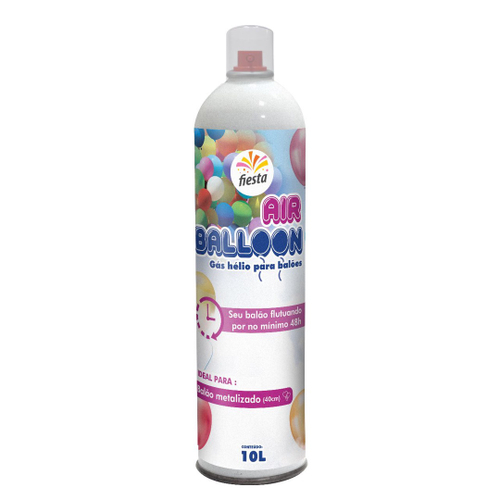

However the last option may not be as cost-effective as helium gas, since this argon for wine is still as expensive as an argon tank.
Also, I think a good option for a DIY laminated stator would be to take iron and/or silicon steel powder and melt it in paper thin laminations on a microwave kiln.
Magnetic Soft Composites are really easy to make and use, but its biggest flaw is that since it is basically powder glued together, it will leave microscopic voids filled with either air and/or the glue itself, such as the resin.
That's why (I think) companies still use laminations even though magnetic soft composites are waaaaay easier to make in a production line (you literally just pour stuff in a mold and wait it to dry out).
Silicon carbide powder is really cheap, I could find 1 to 5 kg for just around 50 reais (10 dollars).
Well, I don't think this tube furnace is as easy to make as the previous kilns, but the previous kilns weren't meant to reach 1200 ºC or more, this one can easily melt steel.
Of course, you would need to make it a little bit different for this specific need, like removing the quartz tube from the equation, but using this method you will be able to purify titanium dioxied into pure titanium using the hydrogen reduction reaction (I talked about the hydrogen reduction reaction of other metals besides iron on newer project logs).
This video is in brazilian portuguese, but it is very easy to follow.
You just make a concrete bucket, put coal in the lower half and blows air using a hair dryer and bam, you have a aluminium melting furnace.
---------------------------------------------------------------------------------------------------------------------------------------------
Something interesting that I found while watching this video, the rotor with permanent magnets have the permanent magnets quite straight while the rotor is round and it doesn't loses too much of its magnetic properties.
(around 0:55 seconds of the vid)
Me:
On a IPMSM electric motor, the magnets are embed on the rotor
How does the material turn the straight magnetic field of the magnets into round magnetic fields by applying a solid piece of metal over them?
ChatGPT:
In an Interior Permanent Magnet Synchronous Motor (IPMSM), the magnets are embedded within the rotor. The purpose of the solid piece of metal over the magnets, often referred to as a rotor sleeve or rotor core, is to shape and control the magnetic field generated by the magnets.
When permanent magnets are embedded in the rotor of an IPMSM, they naturally create a straight magnetic field aligned with their axis. However, in order to achieve efficient and controlled rotation of the motor, the magnetic field needs to be properly shaped into a rotating or circular pattern. This is where the rotor sleeve or core comes into play.
The rotor sleeve is typically made from a ferromagnetic material, such as iron or steel. These materials are highly permeable, meaning they can easily conduct and concentrate magnetic flux. When the permanent magnets on the rotor generate a magnetic field, this field interacts with the ferromagnetic rotor sleeve.
The ferromagnetic rotor sleeve essentially channels and guides the magnetic flux lines from the straight orientation of the embedded magnets into a circular or rotating pattern. This happens due to the characteristics of ferromagnetic materials:
- Permeability: Ferromagnetic materials have a much higher permeability compared to air or other non-magnetic materials. This allows them to effectively concentrate the magnetic flux lines, enhancing the strength of the magnetic field.
- Magnetic Domains: Ferromagnetic materials are composed of tiny magnetic domains that can align with an external magnetic field. When the permanent magnets create a magnetic field, the domains within the rotor sleeve align and amplify the field.
- Closed Path for Flux: The rotor sleeve forms a closed magnetic circuit with the embedded magnets, providing a path for the magnetic flux to flow. This closed path helps shape the magnetic field lines into a circular pattern.
As a result of these properties, the ferromagnetic rotor sleeve effectively transforms the straight magnetic field generated by the embedded magnets into a circular magnetic field that rotates along with the rotor. This rotating magnetic field interacts with the stator windings (the stationary part of the motor) to create the torque necessary for the motor's operation.
In summary, the ferromagnetic rotor sleeve in an IPMSM plays a crucial role in shaping and directing the magnetic field generated by the embedded permanent magnets, allowing the motor to efficiently convert electrical energy into mechanical motion.
Brushless motors do not necessarily require curved permanent magnets to be efficient. The efficiency of a brushless motor depends on various factors, including the design of the motor, the quality of materials used, and the manufacturing process. Curved permanent magnets, also known as arc-shaped magnets, are commonly used in certain types of brushless motors, such as outrunner motors commonly found in RC (remote control) applications. These curved magnets can provide certain advantages, but they are not the only factor influencing motor efficiency.
The shape of the permanent magnets and stators can indeed affect the motor's performance, but the impact of this factor is not necessarily harmful or negligible. The design of the motor should be carefully optimized to ensure efficient use of space and minimize gaps that could reduce performance. However, modern engineering and design techniques can help mitigate these concerns.
Some potential advantages of using curved magnets in brushless motors include:
- Improved Torque: Curved magnets can provide a more uniform magnetic field distribution, which can lead to smoother and more efficient torque production.
- Higher Power Density: Arc-shaped magnets can allow for a higher magnetic flux density in the air gap, potentially leading to increased power output for a given motor size.
- Reduced Cogging: Cogging is a phenomenon where the motor experiences small torque fluctuations as it rotates. Curved magnets can help reduce cogging effects, leading to smoother operation.
- Enhanced Cooling: The curved shape can facilitate better airflow within the motor, aiding in cooling and potentially allowing the motor to handle higher power levels.
However, it's important to note that not all brushless motors require curved magnets to achieve good efficiency. Motors with straight permanent magnets and flat stators can still be designed and optimized for high efficiency, provided that other design aspects are carefully considered.
In summary, while curved permanent magnets can offer certain advantages in specific motor designs, they are not an absolute requirement for motor efficiency. The overall motor design, materials used, manufacturing quality, and other factors play crucial roles in determining the efficiency and performance of brushless motors.
I'm only worring about this because I would need custom-made permanent magnets or quite literally saw them on a new shape.

The round stator teeth and the straight magnets don't really fit very well, so I would assume that these gaps decrease power/efficiency, but hey, it is a "I think", probably the difference isn't that important.
_________________________________________________________________________________________________________________________________________
However, one thing that I kinda don't like about it is the lack of adaptability, which you could simply skip (which I would advise you to) this whole process.
The idea would be to individually wind every stator teeth and use hall sensors both on the rotor and on the stator, so you could use a program to efficiently power every stator teeth the exact way you want, and on top of that, you could do the same for an electromagnetic rotor instead of a rotor with limited number of permanent magents.
This way you could (hyphotetically) change the number of poles, magnets and winding configuration instantly with a program.
The problem is that I don't know what kind of program you would need to use for such thing.
_________________________________________________________________________________________________________________________________________
OFF-TOPIC:
I was giving a serious thought on flying mechs and shared it on a discord server about airplanes, and a guy gave me a good idea, actually.
Basically, the problem with flying mechs is that they either don't care about aerodynamics and use infinite rocket fuel cheat code. The ones that actually try to be physically possible are literal planes with legs or mechs with helicopter rotors (the last not being all that bad tho in my opinion, of course).
So the guy suggested either using the "Sombrero" mech from Armored Core for Answer as a basis or a lifting body with limbs approach.
The sombrero mech is a literal fricking wing with arms and legs:
Now, the lifting body aproach is more or less the same idea, but there are some interesting possibilities with that.


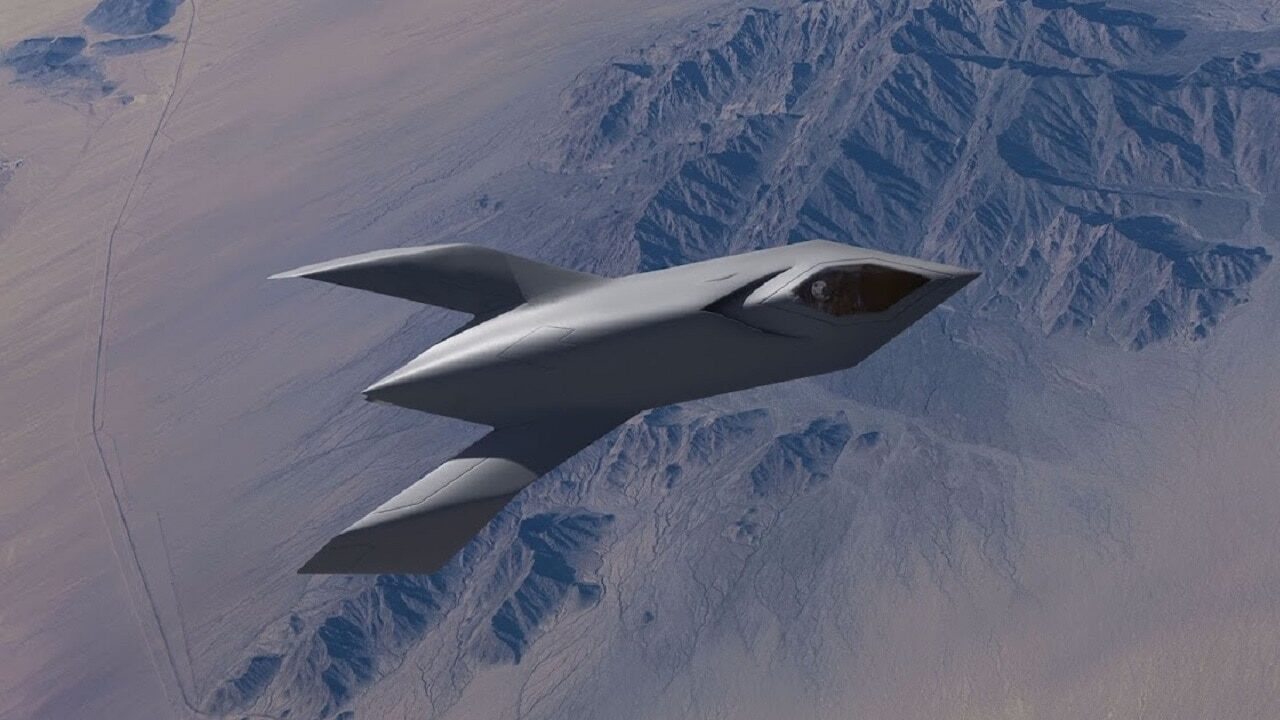
(the last pic is a lifting body aircraft drone called "bird of prey", it was said to be so stable that it didn't need fly-by-wire)
The lifting body can either be wide and blocky, be round and triangular or long and sharp.
You could literally make every limb with these kinds of shapes and surfaces, which kinda hammers home how mechs can have wacky weird shapes.


You wouldn't fly like a fricking super saiyan like most mech media shows you (such as Armored Core for an Asnwer, the mechs are like, travelling at the speed of light), but you would be able to fly without need to surpport the entire weight of the mech upwards like in the case of a helicopter rotor or an infinite rocket booster (you could still use a rocket booster tho).
Discussions
Become a Hackaday.io Member
Create an account to leave a comment. Already have an account? Log In.
You might also look into axial flux motors. They're all the buzz these days, although most DIY efforts I've seen have had very poor torque to weight ratio.
Ben Katz (maker of the MIT Mini-Cheetah) made an interesting one that doesn't use any iron in the stator https://build-its-inprogress.blogspot.com/search/label/Coreless%20Axial%20Flux%20Motor
But he never said how much it weighs or did any load testing to see how much torque it can handle.
The radial flux outrunners you've been studying are my favorite, but the stator and the iron ring of the rotor are both difficult to make yourself, and big ones are expensive to buy (with the exception of hoverboard motors). Axial flux seems to be more expensive to mass produce, but easier to DIY. Neodymium magnets and copper wire are always expensive, though.
Are you sure? yes | no
Yeah, I really wanted to make axial flux motors and transverse flux motors, but there is literally no 3D printed/DIY examples that I could find with much power at all. Which started to make me doubt the actual big claims over axial flux motors from companies.
Thanks for the suggestion, I also found this blog while looking for axial flux motors xD. But thanks for the suggestion anyway <3
Also, in one of the posts in your link, the author says that the motor consumes 24 volts and 2.4 amps, that's like 57 watts of power.
The other DIY axial flux motor of significance that I could find was that guy that makes micro PCB axial motors, the problem would be to scale it up.
Are you sure? yes | no