Wednesday, 05/06/2024, 07:36
Well, the previous project log had so much text that it started deleting new text.
I really don't want to go 2812838218 project logs into the part I actually start building something...
I also bought a new table and one of those drawing tablets with screen on it, because, if you don't know, I like to draw things (even though I'm bad at it [hey, I make a mech project, even though I'm bad at it too]), so I won't be able to buy anything for the project for the next... What? 6 to 10 months. lol
I do hope I can make some extra money with my drawings tho... Hopefully...
Well, Anyway, starting from where we left:
Wattage consumption:
(81 kilowatts is the energy required to move 1 ton of weight at the speed of the human body)
- Arm + Shoulder + Torso + Leg of one side of the mech.
- 81 + ((81x3)x6) + ((81x3x3)x6) + ((81x3x3x3)x6) = 19,035 kilowatts = 25,380 horsepower.
- 81 + ((81x2)x6) + ((81x2x2)x6) + ((81x2x2x2)x6) = 6,885 kilowatts = 9,180 horsepower.
- 81 + ((81x1.5)x6) + ((81x1.5x1.5)x6) + ((81x1.5x1.5x1.5)x6) = 3,543.75 kilowatts = 4,725 horsepower.
- 81 + ((81x1.2)x6) + ((81x1.2x1.2)x6) + ((81x1.2x1.2x1.2)x6) = 2,203.848 kilowatts = 2,938.464 horsepower.
- 81 + ((81x1.1)x6) + ((81x1.1x1.1)x6) + ((81x1.1x1.1x1.1)x6) = 1,769.526 kilowatts = 2359.368 horsepower.
Assuming that there is no biceps/arm actuator, but a shoulder-arm stewart platform:
- (81x6) + ((81x3)x6) + ((81x3x3)x6) = 6,318 kilowatts = 8,424 horsepower.
- (81x6) + ((81x2)x6) + ((81x2x2)x6) = 3,402 kilowatts = 4,536 horsepower.
- (81x6) + ((81x1.5)x6) + ((81x1.5x1.5)x6) = 2,308.5 kilowatts = 3,078 horsepower.
- (81x6) + ((81x1.2)x6) + ((81x1.2x1.2)x6) = 1,769.04 kilowatts = 2,358.72 horsepower.
Well, let's try a non-exponential aproach then:
- 81 + ((81x2)x6) + ((81x3)x6) + ((81x4)x6) = 4,455 kilowatts = 5940 horsepower
- (81x6) + ((81x2)x6) + ((81x3)x6) = 2,916 kilowatts = 3888 horsepower
- 81 + ((81x1.5)x6) + ((81x2)x6) + ((81x2.5)x6) = 2997 Kilowatts = 3996 horsepower
Okay, this is just getting stupid.
Needless to say, screw actuator, hydraulics or pneumatics, I don't think it will be possible to continue with this insane amount of power required.
I guess this is another wall that I've stumbled upon and I need time to think on how to preoceed...
The first obvious thing that probably anyone with a lizard brain bigger than mine notice: I'm assuming that all the actuators in the stewart platform are using power, which would not occur.
And being honest, I don't know how to properly calculate that...
It is always relevant to remember myself that all of this problem comes from the fact that I'm trying to make a humanoid mech, a walker mech wouldn't need to worry about lifting weight, in fact, this project would've already been in actual construction if it wasn't for this detail... (I think).
Types of mechs that are viable/practical or not:
As you will notice, no option has a "✅" on them, that is because if they were the obvious, easy and correct option, Mechs would already be built using said options and actually viable to use.
So the "❓" means: it seems viable and practical, but I'm not sure it will work until I actually build it.
Screw Actuator Mech: ❌
I still need to calculate those, but even though it would supposedly be lighter and practical with a direct electric motor driver, unfortunately it is not as simple.
As you could see, it requires 81,000 watts (100 horsepower) to move the limbs with a force of 1000kg at a speed of 4 meters per second, and even though I'm inputting 3000kg at 1.33 meters per second, it is the same amount of energy, but transformed.
And since the electric motor would be that 80 kilowatt Reb 90 for every limb, which weights around 30kg and probably costs hundreds of dollars if you're not in the mood to build it from scratch. And don't think this is viable... For the mech.
If you are making an exoskeleton, then this value wouldn't be that high (8 kilowatts/10 horsepower), but it would still require considerable planning.
Coilgun Actuator Mech: ❓
On project log 84 I found out that there are brushed/sliding contact coilguns that are simpler and cheaper but not that better than conventional coilguns, but still better than railguns.
The thing is, what if you used them as actuators instead of guns?

And just like that, you could make an electric mech that is cheap, simple and can output force proportionally to the energy you input without worrying too much about efficiency losses, weight and the like.
The problem is that I don't know very well which size of wire, voltage and amperage are the best for it to work.
As I explained in further detail on Project Log 84, I choose 14mm thick aluminium square wires that would be 1mm apart while receiving 500 volts and 400 amps of continuous electrical current in order to output 200,000 watts maximum without heating too much.
I used solenoid calculators, but those showed absurdely high force outputs that wouldn't be reflected in real life, but I'm using the approach anyway.
I'm working with the principle that energy is neither created nor destroyed, but transformed. So, if an electric motor needs X thousand watts to lift an Y amount of weight at a Z speed, then a solenoid actuator with the same amount of power being inserted would output a similar force and speed.
Unfortunately, in order for the coils to work, they need to be exposed for the sliding contact. This obviously means that the actuator will be extremely, extremely dangerous for direct contact with the human body.
In fact, all these options are dangerous in their own right specially because of the proportion in which I will be using them. They will need A LOT of energy to work and will output A LOT of force. at a high speeds.
Needless to say: anything here can easily kill you.
Hydraulic Mech:❓
Taking into consideration the previous project log were I calculated how many liters per minute you would need to make an hydraulic mech to work, I can say with some certainty that hydraulics are out of the question for this specific task.
It doesn't matter if you are applying a few grams of force or a few tons, they will require thousands of liters of hydraulic fluids being pumped in order to actuate.
Being honest, I'm looking again at the calculations and I probably didn't make it right. I will post the result on Project Log 87 when I finish it.
There are artificial muscles that work hydraulically or pneumatically, the most common one are the McKibben artificial muscles.
But either working on liquid or pneumatic, the maximum efficiency these can achieve with a good selection of materials is around 65% with a maximum contraction of 25%. You can achieve 40% or a little more if you make hundreds of thin-braided McKibben muscles, but that would be too labour intensive.
Compared to the traditional hydraulic cylinders that achieve 95% of efficiency and contraction ratios up to 90%, this option may not sound as interesting.
But even though they need a lot of work to manualy make them, these are really light and cheaper to make.
Besides, there are a lot of articles trying to increase their efficiency and performance. So maybe I didn't find the correct one, or maybe a new, better design will be published tomorrow.
For example, these two redesigns of a McKibben artificial muscle achieved 45% and 65% of efficiency while working with Pneumatics.
https://www.mdpi.com/2076-0825/10/5/100
https://www.science.org/doi/10.1126/sciadv.adi7133
Maybe if you work with hydraulics these could reach an even bigger efficiency. Maybe.
Taking that into consideration, the two most interesting actuators for this option (at least for me):
Flexible Pulling Hydraulic Cylinder Actuator:
Essentially, the idea is to have a flexible material to be a pulling hydraulic cylinder, this way you could make something light and easy to make. Something that works just like an artificial muscle, but has better efficiency (90% or more) but without the bulkness of a conventional hydraulic cylinder.
Of cours,e this is an illustration that I found, but you could replace the piston head with a membrane expanding chamber in order to reduce friction.
Radial Piston Hydraulic Motor:
This one is way more complex than the previous option, but if you are dead-set on using rotary actuators, I do think this is a good option.
Obviously, it would be easier to make this out of polymer, like the structure of the mech.
Hydrolysis Pneumatic Mech: ❓
If you don't remember, the idea is to separate hydrogen and oxygen from water, you would need 1 liter of water to generate 1857 liters of hydrogen+oxygen gas.
(I forgot to link the article that gave the idea)
Based on the weight of the hydraulic fluid, I can take the volume of the liquid, more or less 400 to 500 liters and multiply by the pressure I intend on working with, which is 6 bar/atm, so, 500 x 6 = 3000 liters in total (since gases are compressible, unlike hydraulics).
So, 3000 liters for the mech to contract all muscles, 1500 if half is actuated, but I don't know how many liters will be used per minute, or even per hour.
We are talking about using 1500 liters of gases for a single contraction, after all, the amount required to keep the mech moving is just a guess, but it woul require a lot.
This would still require thousands of liters of air being pumped, but since you can control the output force, then it is one less source of energy losses.
- However, hydrolysis is 60% to 70% efficient.
- And I can't find a specific number, but it is said that pneumatic systems are 2% to 20% efficient, this is due to leaks, poorly sized valves and pipes and so on.
Even without a pump, you would need those. - But if you count only the actuator, it can be as high as 80% to 90%.
- You would need compressed gas tanks, made from scratch with plastic (like everything else) or bought.
- You would need mechanical brakes for position control, also more weight and complexity.
- You can recycle the hydrogen and oxygen with a fuel cell after they are used by the pneumatic system, like a turbocompressor recycling the the exhaust gases of a combustion engine.
- Limited pressure (6 bars), so bigger muscles, so big they might start weighting significantly
- hydrogen is combustable and so light/small it can pass through solid material, but HDPE and/or UHMWPE are polymers used in liners for hydrogen storage to avoid that, so I can assume it would be somewhat safe.
This one has a lot of pros and cons, and overall.
I will try and search for a material that can be separated into more inert gases for safety.
... And I can't find one at all...
I know that there is hydrogen peroxide and you could decompose it into water vapour and oxygen, but the process isn't reversible like hydrolysis...
Maybe I'm overthinking this idea?
For example, water is only 10% hydrogen, I could just react the hydrogen with the outside air in a fuel cell, like I previously suggested, and only use the oxygen released during hydrolisys in order to make it work.
It would be dangerous if something was leaking close to fire sources, but it would be way safer than use hydrogen and oxygen to power up the pneumatic actuators.
Nope, there is a whole do's and don'ts of oxygen concentrators (which work with way less oxygen output than this idea), and they literally say to NOT use any kind of cigarettes, aerosols (sprays) or even petroleum based products close to it because the oxygen concentrator can make these combust.
Evaporative Pneumatic Mech: ❌
Esteban kidnly suggested me using a refrigerant called "Trichlorofluoromethane R-11" (what a mouthfull), it is non-flamable and it evaporates at 24ºC. You could just use any other refrigerant.
So it has all the pros of the hydrolysis pneumatic mech, but without the possibility of burning me alive.
But it still has some cons related to pneumatics:
- You would need an onboard refrigerator, and if it fails, you would really need safety valves, because all of it would turn into vapor.
- And since it is a evaporative refrigerant, it would need a really big heat exchanger and/or a electric heater, or else all the tubing would freeze and crack (leading to leaks).
- I'm still trying to find more information on how to handle this one specific refrigerant, but its liquid form depends on its pressure and temperature. Which for some reason, googles doesn't show me which is.
Accordingly to this graph, at 6 bar of pressure it should liquid, and it would evaporate at around 71ºC.
But wait, doesn't that mean that the gas in the muscles would be at liquid state since they are also at 6 bars of pressure? - I can't find a specific number, but it is said that pneumatic systems are 2% to 20% efficient, this is due to leaks, poorly sized valves and pipes and so on. Even without a pump, you would need those.
- But if you count only the actuator, it can be as high as 80% to 90%.
- You would still need compressed gas tanks, but it wouldn't be much of a problem.
- You would need mechanical brakes for position control, also more weight and complexity.
- This time, the pressure wouldn't really be a limiter, but working with lower pneumatic pressures is still more efficient and practical.
Being honest, now I'm divided between dielectric elastomers and evaporative pneumatics...
Actually I noticed a relevant characteristic of it that may turn it non-viable: the compressor.
Assuming that you let some of the refrigerant liquid evaporate and pressurize, what will happen when you take it out of the muscle?
It will continue to be in the gaseous form, forcing you to compress around 1500 liters of refrigerant gas as fast as possible before it saturates the gas tanks.
BUT I don't know if it would be that simple, you could use the evaporation intake of the refrigerant to cryogenicaly cool the exhaust refrigerant gas.
On top of it, you could allow the exhaust gases to accumulate until they also reach 6 bars of pressure and let the compressor to work at somewhat minimum efort, but I'm unsure how all of that would really work.
Compared to the hydrolysis and DEA mechs, this one sounds a little too complex.
BUT if I am unable to solve the problems of the dielectric elastomers, I will pick this one.
I was calculating how much air flow you would need with this refrigerant in order to make the mech work, and as such, the amount of refrigerant gas you would need to compress back to liquid in order to do that:
- Since a human takes 3.24 steps per leg in a second while running, and since half of the mech needs 1500 liters for a single actuation, then it is safe to assume that the total number of liters in total per minute would be:
- 3.24 steps per second x 1500 liters x 60 seconds = 291,600 liters per minute.
So, 300,000 liters per minute of airflow, or 10,600 CFM is a really big amount.
This fan is capable of having such an airflow, and it has a diameter of 44 inches, or 110cm.I would need a compressor with this insane amount of airflow to work.
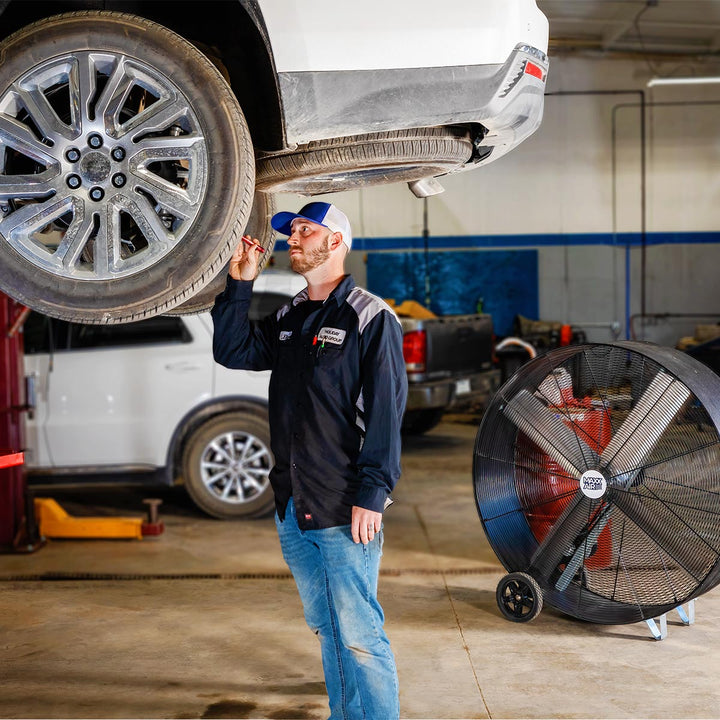
Needless to say, this is not viable.
... But I will still go through the trouble of finding out how much energy it would consume and how big it should be if it was a compressor unit.

This is a 10,000 CFM air compressor unit and it uses around 1800 kilowatts, or 1 megawatt of power.
This one below is a 1,000 CFM (cubic feet per minute)/33.6 CMM (cubic meter per minute) 8 bar air compressor and it uses 160 kilowatts (200 horsepower):
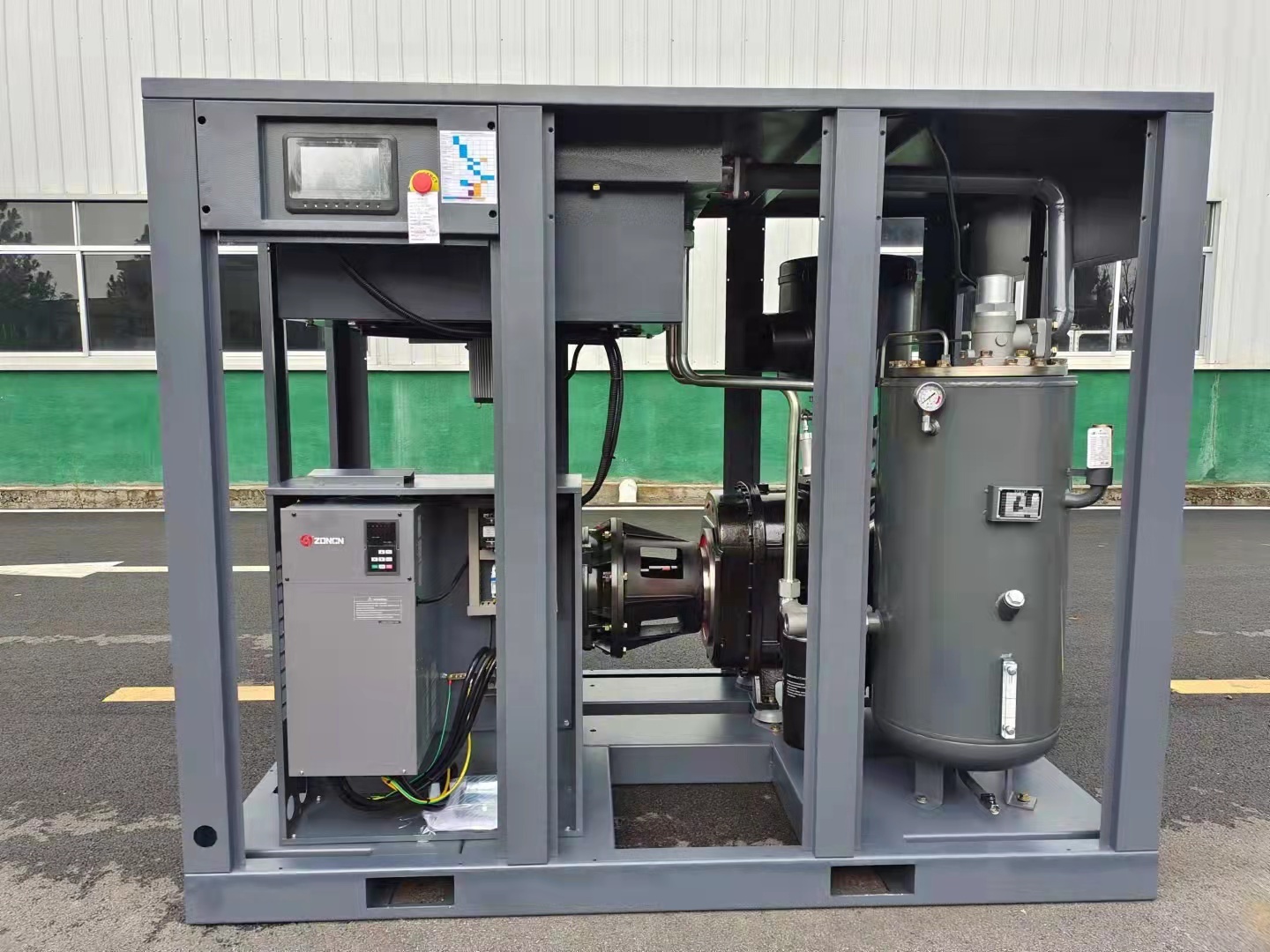
It also weights 4 tons.
Unfortunately, this is not viable. :/
Maybe measuring the compressor I'm looking at it incorrectly?
For example, looking at this chart of refrigerant gases, you can see that some of these need to be at more or less -30 degree celsius to stay at room pressure (14 psi), and as such, you would need to have a sufficiently big enough mass/cooling system to turn the used gases into liquid again.
I asked chatgpt, and for a air flow of 10,000 CFM, I would need around:
- Q=1.08×CFM×ΔT
- Q = cooling capacity or BTU/hr
- CFM = is the volume flow
- ΔT = the difference in temperature in fahrenheit.
- From room temperature of 25ºC (77ºF) to -30ºC (-22ºF)
- 1.08x10000x(77-(-22)) = 1,069,200 BTU/hr
QkW=QBTU/hr×0.000293071071 BTU = 0.00029308323 kWh.
(I don't know why the text is weird like this lol)
Q_{kW} = Q_{BTU/hr} \times 0.00029307107
- Q kW = 1,069,200 x 0.00029307107
- kW = 313.3 kilowatts or 417.8 horsepower.
It is not really a small amount, BUT, at least it seems more viable than before.
I just don't know how big of an air compressor I would need for 1 million BTU/hr...
Commercial/house air conditioner units can have up to 60,000 BTU/hr, and most of them use around 6,000 Watts per hour.
1,000,000/60,000 = 16.6666 x 6,000 = 100,000 watts or 133.3 horsepower.
The only problem is the size:
I found this marine air cooling unit with 360,000 BTU/hr:
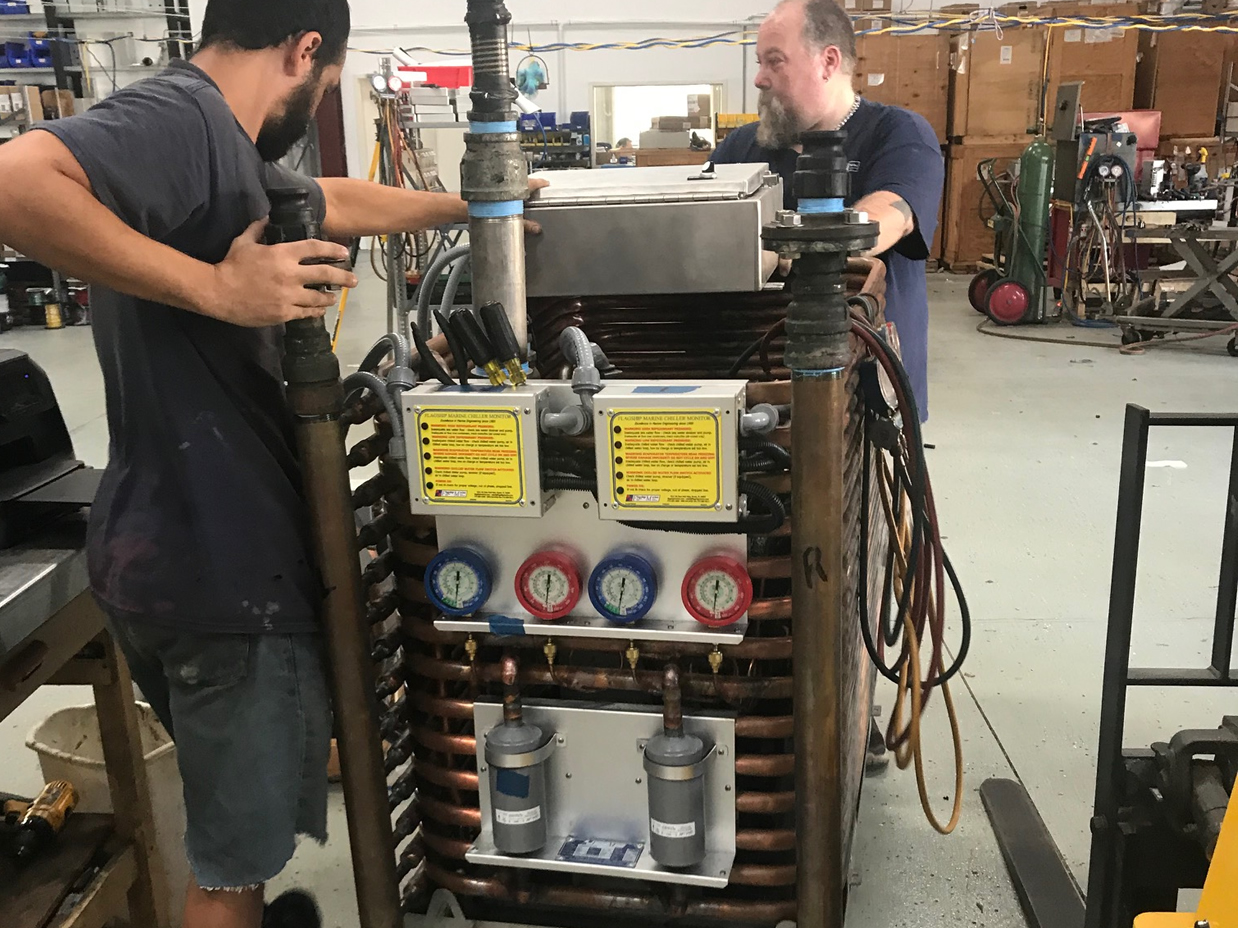
You would need 2 to 3 of these for this mech to work.
Peltier pellets could also work, but those have only 20% of efficiency when cooling.
... Which makes me wonder: if my approximation of the 10,000 CFM of air is even correct, wouldn't this means that I wouldn't need such big screw compressor just to compress/cooldown the refrigerant gas?
I genuinely think this idea would work if you had a cryogenic bath of liquid nitrogen, liquid CO2 (carbon dioxide) or similar.
... But in order to achieve a bucket worth of liquid gases, you would need a cryogenic cooler.
Unfortunately, the most efficient (and expensive) cryocooler out there is the pulse-tube cryocooler, and it only has a maximum 20% of efficiency.
Dielectric Elastomer Actuator Mech: ❓
Yes, it would be feasible IF the dielectric elastomer in question can lift at least 1000 times its own weight.
For now I'm still trying to find some place were the article with the high performance DEA is available, and IF I happen to find its, and IF happens to be simple enough to make, then it will my choice.
The article in question.
I forgot to write the pros and cons:
- Conventional DEA's materials are readly available and easy to find, most of the time.
- High performance DEA's materials really can't be sourced on stores and need to be specifically sourced through chemical companies.
- I have no idea how I will take liquid silicone rubber and turn it into 1mm thin thick square fibers for the actuators.
- Its actuation method is somewhat safe in small cases like the ones in the articles, but it is unknown how well it would work in thousands of fibers at same time, specially with such high wattages being required per actuator.
- It requires a really, really good insulation on the electronic equipment or else the electrons will just go though the insulation and toast everything in its path.
- Dealing with thousands of fibers will be a task on its own, not that the McKibben wouldn't have the same issue, but that is also a characteristic.
- It will be extra hard to figure out which fibers aren't working properly.
- Position control will need mechanical brakes.
Well, while I don't have access to the article in itself, I will at least try to find dielectric elastomers with a significant energy density and performance.
In the previous project log I used this one as a basis for calculating the weight, but I think I misscalculated something, since this one can clearly carry 1000 times its own weight (it can lift 200 grams while weighting 0.2 grams).
So, if I wanted to pull a weight of 3000kg, It would weight 3 kilograms, no?
- "Modeling and Characterizing a Fiber-Reinforced Dielectric Elastomer Tension Actuator":
Anyway, said actautor has a energy density of 10.7 Joules per kilogram. - "Printing Reconfigurable Bundles of Dielectric Elastomer Fibers":
This one has 134 W/kg, so I may assume that since this one has 134 J/kg of energy density, meaning it can lift 10,000 times its own weight? - "A Jumping Robot Driven by a Dielectric Elastomer Actuator":
This one has 28.71 J/kg. - "Triblock Copolymer Organogels as High-Performance Dielectric Elastomers":
This one (use sci-hub) has its energy density measured in MJ/m³, which accordingly to chatgpt it is around 1600 J/kg and an efficiency of 90% from electrical input to mecahnical ouput. - "A processable, high-performance dielectric elastomer and multilayering process":
This one has energy densities scales in watts and in joules, and it shows that it has a energy density of 2000 W/kg and around 90 J/kg... - "A large-strain and ultrahigh energy density dielectric elastomer for fast moving soft robot":
This one has 225 J/kg, and around 2400 W/kg so also 20,000 times its own weight?
In any manner, how each DEA is synthesized accordingly to each article:
1: Modeling and Characterizing a Fiber-Reinforced Dielectric Elastomer Tension Actuator
The soft composite layups were prepared using VHB F9473 PC elastomer tape. Within the elastomer layers, cottoncoated polyester fibers were arranged in meshes with fiber angles ranging from 15◦ to 85◦ with a constant element edge length between samples. Then for each layup, a layer of the elastomer tape was applied on either side of the fiber mesh. Once the layups were prepared, single-walled carbon nanotube (CNT) electrodes (Carbon Solutions, Inc. P3-SWNT) were applied on both sides to make the completed DEA composite. Once prepared, the maximum stress in each sample was measured with both ends fixed, such that λ2 = 1. The DEA composites were attached to a custom-built tension testing machine made with a Zaber T-LA60 A linear actuator, Zaber TSB60-I translational stage, and a PCB Piezotronics 1102-05 A load cell. The samples were stretched taut, and the actuator was exposed to a step input and held at voltage until the measured tensile force stabilized. Actuation voltages ranged up to 9 kV (UltraVolt 10A24-P15-I5) and the data was recorded by a National Instruments USB-6009 DAQ card.
A sheet of VHB 4910 elastomer tape was used for the dielectric of this experiment and was biaxially prestretched to λP S = 5 to improve its dielectric properties and discourage pull-in instabilities at low ramp rates [20]. The elastomer was left to relax for 24 hours to minimize viscoelastic effects. At this stage, CNT electrodes were applied to both sides, and aluminum foil leads were attached to the nanotubes to connect later with the power supply. Fiber meshes were prepared following the procedure outlined in Section III-A with VHB F9460 PC elastomer tape layers encapsulating fiber meshes ranging from 15◦ to 75◦ and were applied over one of the CNT electrodes. Finally, polyamid seeding particles (Dantec Dynamics PSP-50) were distributed across the surface of the elastomer. The samples were then connected to a high-voltage amplifier (Trek 20/20C-HS) and actuated up to 5 kV at a rate of 50 V/s. A further increase in voltage leads to wrinkling of the dielectric, which causes out-of-plane deformations not predicted by the modeling. Images of the actuator were taken using a Nikon D7000 at a variety of voltages. The images taken were then modified to black and white images and processed using PIV software (TSI Insight 4 G) to obtain the deformation fields in both the DEA and the surrounding elastomer. MATLAB was then used to determine the strain fields and calculate the boundary conditions applied by the surrounding elastomer on to the DEA region. Another strain test was performed to attempt to improve the strain results. [20] showed improved DEA performance was achievable using higher strain rates and lower prestrains, achieving five times higher linear strains resulting from the increased viscous impedance which prevents pull-in failure. Following this, we fabricated another actuator made from VHB 4910 biaxially prestretched to λP S = 3.5 without a relaxation period, applied an encapsulation layer, and actuated it with step inputs up to 7.5 kV. Images taken from the Nikon camera were then processed to determine the intersections of each fiber element which defined the size of a given element. After this, the dimensions of the elements in their initial and final positions were used to calculate the engineering strain. This process was repeated for all complete fiber elements and the average was reported.
It seems that this "VHB F9473 PC elastomer tape" is just a transfer tape (61 dollars/300 reais for every 50 meters), the single-walled carbon nanotubes are just too expensive and the "VHB 4910 elastomer tape" is just a silicone rubber tape.

The "VHB4910" is easy to find, it is a silicone tape. It costs 100 reais (20 dollars) for every 20 meter of this tape, it normally has 12mm of thickness. I don't even know how I would attach the electrodes to it...
Translation: "it supports 3.4 kg of weight for every meter"
2: "Printing Reconfigurable Bundles of Dielectric Elastomer Fibers"
Dielectric Ink: Fumed silica nanoparticles (CAB-O-SIL TS-720, from Cabot Corp.) were dispersed in Ecoflex 00-30 (Eco30) part A (Eco30A) and part B (Eco30B) separately by mixing in a SpeedMixer (Flack Tek, Inc) at 2000 rpm for 18 min. 12 g of the Eco30B/silica mixture was weighed into a separate container and 0.36 g (3 wt%) of SloJo cure retarder was added and mixed for another 2 min. 12 g of the Eco30A/ silica mixture was added to the container. Finally, 8 g of SE 1700 (Dow Corning Corp.) base and 0.266 g of SE1700 curing agent were added to create a final composition with a weight ratio of 3:1 Eco30:SE1700 and 30:1 SE1700 base:SE1700 curing agent. The composition was mixed at 2000 rpm for 12 min in a SpeedMixer. The resulting dielectric composition included 7.88 wt% TS-720 silica, 32.8 wt% Eco30A, 32.8 wt% Eco30B, 24.5 wt% SE1700 base, 0.82 wt% SE1700 curing agent, and 1.10 wt% SloJo. To improve the dispersion of the nanoparticles, the dielectric ink was roll milled (Torrey Hill, T50) three times. The ink was loaded into 20 cc syringes and centrifuged at 4000 RPM for 20 min to remove any trapped air. Rheology measurements were performed on an AR-2000EX shear rheometer at 25 °C using stainless steel parallel plates with a diameter of 40 mm and a gap of 0.3 mm. After lowering the top plate to the target gap, the sample was allowed to settle for 300 s before starting the measurement. Oscillatory measurements were carried out at a frequency of 1 Hz over a range of shear stress from 1 to 10 000 Pa. Cured dielectric matrices were characterized by shear dynamic mechanical analysis (DMA) using an AR-2000EX rheometer. Samples of uncured dielectric matrix were loaded into the rheometer equipped with a 20 mm steel plate with a gap of 0.3 mm. The samples were heated to 100 °C while collecting oscillation measurements at 1 Hz to monitor the curing. After fully curing, samples were cooled to 25 °C and shear DMA was carried out at a strain of 1% over a frequency range from 0.1 to 100 Hz. Parallel plate capacitors were prepared by blade coating the dielectric ink onto ITO-coated PET. The dielectric ink was cured at 80 °C for 12 h. Gold particles were used to define top electrodes with a diameter of 1 cm. Capacitance measurements were collected using an Agilent E 4980A using controlled using a Labview program. Electrode Ink: Carbon black nanoparticles (AB100, from Soltex, Inc.) were weighed into Eco30A and Eco30B separately at a content of 13.8 wt%. The compositions were mixed at 2000 rpm for 18 min using a SpeedMixer (Flack Tek, Inc). 12 g of Eco30B/AB100 mixture was combined with 0.12 g (1 wt%) of SloJo curing retarder and mixed for another 2 min. 12 g of Eco30A/AB100 was added and mixed at 2000 rpm for 12 min in a SpeedMixer, followed by roll milling three times. The dielectric ink was loaded into 20 cc syringes and centrifuged at 4000 RPM for 20 min to remove any trapped air. Rheology measurements were performed on an AR-2000EX shear rheometer at 25 °C using stainless steel parallel plates with a diameter of 40 mm and a gap of 0.3 mm. After lowering the top plate to the target gap, the sample was allowed to settle for 300 s before starting the measurement. Oscillatory measurements were carried out at a frequency of 1 Hz over a range of shear stress from 1 to 10 000 Pa. Mechanical Testing: Samples of the dielectric and electrode elastomer for tensile testing were printed into rectangular planar sheets with dimensions of 0.8 mm × 60 mm × 60 mm. After curing, the sheets were cut into dog-bone shapes following the ASTM D412a standard scaled down by 2.5 times. Specimens were stretched until rupture on a homemade stretcher (Mint, Baldor) with a load cell (FUTEK LSB200, 2 lb, JR S-Beam Load Cell) at a strain rate of 0.1 s–1. Data was acquired using a LabVIEW program. For electrode inks, the resistance was measured by a Keithley 2636A connected to the two metal clamps of the stretcher. The measuring voltage was 1 V. Device Fabrication: A multicore-shell nozzle (Figure S3a,b, Supporting Information) was prepared by an Aureus Plus 3D printer with a layer height of 25 µm and an X-Y resolution of 43 µm, as described in the previous work.[41] The nozzle, dielectric, and electrode inks were mounted to an Aerotech 3-axis stage (Aerotech, Inc.). The pressure of each channel in the nozzle could be controlled by an Ultimus V pressure pump (Nordson EFD) and switched on and off by a solenoid valve while printing (Figure S3c, Supporting Information). The relative dimensions of the DEF samples were printed onto glass plates covered with a Teflon adhesive film (Bytac, Saint-Gobain). Because the ink rheology was temperature-dependent, quickly increasing the curing temperature leads to a viscosity reduction that causes the printed structures to sag under their own weight. Hence, printed samples were first cured at a low temperature of 60 °C for 24 h to drive solidification, followed by curing for 24 h at 80 °C, and finally for 24 h at 110 °C to achieve a fully cured state.
Fumed silica is cheap and easy to find, ecoflex is just sculpiting silicone rubber that already comes with its uring agent, carbon black is expensive but replaceable, teflon is easy and the last one is "cure retarder", I don't know where to find this exactly type, but there are ones you can buy online, you can even mix acetone or alcohol to silicone to make it more liquid and retard the curing process for some time.
3: "A Jumping Robot Driven by a Dielectric Elastomer Actuator"
"The fabrication process of multilayer DE includes two processes: the fabrication of single-layer DE and the stacking of multilayer DE, as shown in Figure 8. The DE material is VHB4910 produced by the company 3M, and the main material is acrylate. In the single-layer process, a DE film with a thickness of 2 mm was stretched to 12.25 times (3.5∗3.5) its original area by a biaxial stretching machine to obtain a pre-stretched DE film with a thickness of 100 μm. The pre-stretched DE film was taken out with a large retaining ring and a small retaining ring with inner diameters of 160 mm and 140 mm (PMMA, cut with a laser cutter), respectively. The upper and lower surfaces of the pre-stretched DE film were covered with a mask (Release film, cut with a laser cutter) which had been vacated for an electrode. The flexible electrode was applied by spin coating, and the electrode pad was attached. In the multilayer DE stacking process, the prepared DE with a small retaining ring was sleeved inside another DE with a large retaining ring, and the air bubbles between the two layers of DE were removed by rolling. The large retaining ring was cut off along the edge to obtain two-layer DE with a small retaining ring. The two-layer DE was then nested into a new DE layer with a large retaining ring. We repeated the above operation and ensured that the electrode pads were aligned in the alternating layers. Variety in the multiple-layer DE could be obtained according to the requirements of different actuators by this way."
Again, the "VHB4910" is easy to find, it is a silicone tape. It costs 100 reais (20 dollars) for every 20 meter of this tape, it normally has 12mm of thickness, which is more or less the thickness that I was thinking on working with... I don't even know how I would attach the electrodes to it...
Translation: "it supports 3.4 kg of weight for every meter"
4: "Triblock Copolymer Organogels as High-Performance Dielectric Elastomers"
We developed systematic synthetic strategies to tune the bimodal system’s stress-strain responses and viscoelasticity. First, short-chain cross-linkers with softer and more-extended chains were used to replace previously explored short and stiff molecules, such as hexanediol diacrylate (HDDA), thus achieving more tunable stretchability and tensile strength (Fig. 1C and figs. S2 and S3) (8). The cross-link density/gel fraction (fig. S4) as well as the stress-strain responses were further controlled by changing the concentrations of the short-chain cross-linker, PNPDA (Fig. 1C) (8). Without PNPDA, the DE shows a similar long stress-strain plateau to that of non-prestretched VHB (fig. S5) (5, 6). With the bimodal network structure, our DE stiffens after a critical stretch ratio in its non-Gaussian region (20), which can suppress EMI. This critical stretch ratio shifts to a smaller value as the cross-link density increases. Second, the concentration of hydrogen bonds was optimized in the DE network to modify the viscoelasticity while maintaining its stress-strain relationship. A small amount of acrylic acid (AA) comonomer (2.5 parts of weight) was added, which provides side groups to form hydrogen bonds with themselves, as well as with the –NH– groups on the CN9021 and PNPDA cross-linkers (fig. S6) (21). The mechanical loss factor of DE, a measurement of the viscoelasticity, was then decreased from ~0.22 to ~0.11 at room temperature and low frequencies (fig. S7) without changing the strain stiffening behavior (table S2) and high elasticity (fig. S8). After AA is added, hydrogen bonds partially replace covalent cross-links in the network. Hydrogen bonds act as weak, physical cross-links and can dynamically dissociate, leading to a lower glass transition temperature (Tg) (fig. S9) and higher chain mobility in the network (22). As more AA is added, hydrogen bonds become highly concentrated, and the density of covalent bonds decreases (fig. S7), which results in inhibited actuation performance (fig. S10). At frequencies above 20 Hz, the storage modulus and loss factor of DE also increase rapidly (fig. S11).
Asked web search GPT, all of these costs around 400 reais (75 dollars) per 100 ML/100g. Some don't even have a price tag for them, you need to ask a quote from the supplier.
5: "A processable, high-performance dielectric elastomer and multilayering process"
"We built a bimodal-networked elastomer using two cross-linkers with different chain lengths and tailored its electromechanical properties for high actuation performance. DE films were fabricated through solution processing and cured under ultraviolet (UV) light. The long chain segment in the bimodal network ensures large elongation, and the second relatively short chain segment raises the modulus at modest strains to resist the rapidly increased Maxwell stress during actuation and suppress EMI (Fig. 1A) (8, 17). Figure 1B shows the molecular structures of reactants. Detailed formulations and nomenclature of samples can be found in table S1. Butyl acrylate (BA) and isobornyl acrylate (IBOA) were selected as comonomers to lower the modulus and improve the toughness of copolymers, respectively (18). They were also important to reduce the viscosity of prepolymer solutions (19). CN9021, a urethane diacrylate (UDA) with a high molecular weight, was selected as the flexible long-chain cross-linker, and propoxylated neopentyl glycol diacrylate (PNPDA) was used as the short-chain cross-linker (fig. S1). 2,2-dimethoxy-2-phenylacetophenone (DMPA) and benzophenone (BP) were used as cophotoinitiators to ensure complete curing through the bulk and surface of the film.
"We developed systematic synthetic strategies to tune the bimodal system’s stress-strain responses and viscoelasticity. First, short-chain cross-linkers with softer and more-extended chains were used to replace previously explored short and stiff molecules, such as hexanediol diacrylate (HDDA), thus achieving more tunable stretchability and tensile strength (Fig. 1C and figs. S2 and S3) (8). The cross-link density/gel fraction (fig. S4) as well as the stress-strain responses were further controlled by changing the concentrations of the short-chain cross-linker, PNPDA (Fig. 1C) (8). Without PNPDA, the DE shows a similar long stress-strain plateau to that of non-prestretched VHB (fig. S5) (5, 6). With the bimodal network structure, our DE stiffens after a critical stretch ratio in its non-Gaussian region (20), which can suppress EMI. This critical stretch ratio shifts to a smaller value as the cross-link density increases. Second, the concentration of hydrogen bonds was optimized in the DE network to modify the viscoelasticity while maintaining its stress-strain relationship. A small amount of acrylic acid (AA) comonomer (2.5 parts of weight) was added, which provides side groups to form hydrogen bonds with themselves, as well as with the –NH– groups on the CN9021 and PNPDA cross-linkers (fig. S6) (21). The mechanical loss factor of DE, a measurement of the viscoelasticity, was then decreased from ~0.22 to ~0.11 at room temperature and low frequencies (fig. S7) without changing the strain stiffening behavior (table S2) and high elasticity (fig. S8). After AA is added, hydrogen bonds partially replace covalent cross-links in the network. Hydrogen bonds act as weak, physical cross-links and can dynamically dissociate, leading to a lower glass transition temperature (Tg) (fig. S9) and higher chain mobility in the network (22). As more AA is added, hydrogen bonds become highly concentrated, and the density of covalent bonds decreases (fig. S7), which results in inhibited actuation performance (fig. S10). At frequencies above 20 Hz, the storage modulus and loss factor of DE also increase rapidly (fig. S11)."
Asked web search GPT, all of these costs around 400 reais (75 dollars) per 100 ML/100g. Some don't even have a price tag for them, you need to ask a quote from the supplier.
6: "A large-strain and ultrahigh energy density dielectric elastomer for fast moving soft robot"
"Polymer design:
To develop a high-performance DE under low electric fields, we design a random copolymer of 2,2,3,4,4,4-hexafluorobutyl acrylate (HFBA), 2-ethylhexyl acrylate (EA) and dodecyl acrylate (DA) (Fig. 1a). The transparent dielectric elastomer was synthesized by mixing the three comonomers in one-step UV photopolymerization (Supplementary Fig. 1). In this strategy, the rich and highly polar CF3 groups in HFBA segments provide high dielectric constant.
I just asked web search GPT to find these chemicals, all of these costs around 400 reais (75 dollars) per 100 ML.
I know that this can sound disappointing after I copy pasted so much crap from these papers, but I was considering switching from Silicone Rubber to Polyurethane Rubber, at least for the electrodes.
Accordingly to web search GPT, higher tensile strengths for dielectric elastomers can POTENTIALLY increase its contraction ratios, its energy density, durability, dielectric breakdown limit and efficiency.
Polyurethane rubber can have a tensile strength as high as 44 MPa while Silicone rubber can have a range of around 10 MPa. Silicone rubber has an elongation of around 700% and polyurethane can have around 300% to 400% maximum. Polyurethane rubber would be more durable than Silicone rubber, and it would also be better at tear resistance.
And yes, I do intend on adding fillers for both materials both at the electrodes and at the dielectric layer, like silica powder, flash graphene, dielectric grease, titanium dioxide and fiberglass. So the current properties of either material can end up significantly changing.
It is a consideration, I don't know which one is the best for this job, and I can always mix a little bit of both.
I would need around 42 kilograms of polyurethane/silicone rubber.
I found out that there are more rigid and stronger silicone rubbers (like the ones used in tires) which rigid called "shore" raging from 00-05 to 45A. The polyurethane rigidity is from 60 going up to 75.
Well, I said all that, but it seems like it is bullcrap generated by GPT, since I found some Polyurethane/Silicone rubber suppliers that actually have a data sheet, and their tensile strength is around 3.5 to 2 MPa.
Some variantions can have up to 5 MPa and an elongation at break that ranges from 200% to 400%, but it doesn't seems like these values have any kind of relationship with tensile strength and shore hardness.
However, with that in mind, Polyvinyl Alcohol has a tensile strength of 40-90MPa, 200% elongation at break and a shore hardness of 70A. It also has 10 times better dielectric constant than silicone rubber and 2 times better than polyurethane rubber.
It is also cheaper than both.
However, it doesn't mean I will only choose PVA, I'm actually looking at several options, when I'm decided I will try to make an update.
By the way, I found dielectric elastomers that use liquid metals as soft electrodes. Hum...
Source: https://www.researchgate.net/publication/369887430_Liquid_Metal_Smart_Materials_toward_Soft_Robotics
Source: https://www.mdpi.com/2073-4360/14/4/710
After all of that, I think that maybe the best option may be HASEL actuators, since they don't need to stretch themselves, they have less losses to friction.
Since dielectric elastomers (even HASEL ones) are essentially bending capacitors, you can recycle the electrical current and increase the efficiency to 60%.
You can also make a few modifications in order to increase its contraction ratios:
https://par.nsf.gov/servlets/purl/10191286
Thermoactive Actuators Mech: ❓
Esteban also suggested thermoactive artificial muscles, such as Nylon/Polyethyelene (fishing line) or shape memory alloys like Nitinol.
Nitinol is an alloy of nickel titanium, needless to say, this is quite expensive Shape Memory Alloy to work with, costing 500 to 700 dollars per kilogram.
There are other shape memory alloys that use cheaper materials, but Nitinol is still the best option both in performance and efficiency.
Of course, there are other options besides these, such as the silicone rubber carbon fiber composite artificial muscle that can lift 12,000 times its own weight (here).
This one works because the silicone rubber expands when heated, pulling the fibers apart, simulating a contraction.
These are interesting alternatives, but:
- They are too slow to contract.
- Even slower to relax.
- You would need a robust refrigerant system and turn the materials into composites with thermal paste for fast thermal dissipation.
- They reach even less than 10% to 20% thermal efficiency.
- You would need to separate the muscles in sections for a somewhat precise position control, if you are not interested on using mechanical brakes.
- They are cheap (the thermalpolymer ones) to find and make.
- They are the somewhat safe to work with, however, if the heater exceeds the polymer's temperatures, they will irreversibly melt and even catch fire. Ruining most of the muscle.
- You could "just" let the muscles in pressure bags with refrigerant liquid/gases that would evaporate at the maximum temperature the materials are allowed to heat up.
Or maybe just flow oil/water all the time so the muscles always can easily cooldown.
But both of these potions seem sketchy to me.
This video is about nitinol wires as artificial muscles, contracting and relaxing them by pumping water with different temperatures into the bundle.
If you need to pump hot and cold water this fast, wouldn't that be the same as having an hydraulic actuator tho?
I even thought on maybe attempting to make peltier plates on the fibers themselves, but these would be too small and complex to mass-produce at home.
And to be honest, even thought it has all of these cons, if Nitinol wire wasn't 700 dollars per kilogram, I would've used these a long time ago to make the mech.
By the way, there are a lot of variations on Nitinol wire, the cheapest ones are called "superelastic" and the "shape memory alloy" type is the most expensive.
There are other shape memory alloys, shape memory polymers and thermoactive polymers, but I never found one type that is easy to make at home and it is super strong.
Maybe google didn't show me all the alternatives or I simply didn't mind to look closely enough.
This one article is about a high energy density shape memory polymer and it explains how the polymer is synthesized:
"Synthesis and Film Preparation:
This synthesis is a modification of a previously described synthesis for PDMS-based, amine-terminated macromonomers. (32) A solution of H2N-PPG-NH2 (Mn ≈ 400 g/mol, Jeffamine D400) and anhydrous dichloromethane (8.0 g in 150 mL, 0.13 mM) was prepared under a N2 atmosphere. Methylenebis(phenyl isocyanate) (MPU) was added in a 1:1 molar ratio of amine/isocyanate functional groups (5.0 g, 0.13 mM). The resulting mixture was stirred for 72 h at room temperature, until the solution gelled and partially precipitated. The synthesized polymer was quenched in methanol and then fully precipitated by adding an excess of hexane. The recovered polymer was subjected to vacuum evaporation for 2 h at 90 °C. Molecular weight according to GPC: Mw = 12.0 kDa, Mn = 10.6 kDa, ĐM = 1.1 (Figure S10). 1H NMR (400 MHz, d2-C2D2Cl4, δ/ppm): 7.75 (br, 4H), 7.30 (br, 4H), 7.03 (br, 4H), 3.93 (br, 2H), 3.81 (br, 1.5H), 3.45 (br, 17H), 1.09 (br, 17–18H) (assignments given in Figure S11). Elemental analysis data: Analytical calculations for (C39H62N4O8)n: C, 65.5; H, 8.7; N, 7.8; O, 17.9. Found: C, 64.3; H, 8.5; N, 8.3; O, 18.9 (remaining).
Film samples were prepared by drop casting 100 mg/mL solutions in CHCl3 onto SiO2 wafers treated with a monolayer of octadecyltrichlorosilane (OTS) to allow for easy removal of the film and dried for over 12 h at room temperature and then again at 70 °C for at least 24 h. Higher quality films were obtained using lower concentrations (e.g., 50 mg/mL compared to 100 mg/mL), though the resulting drop-casted films were much thinner for lower concentrations, due to the decreased solution viscosity."
I was curious, and it seems like there are liquid/gel based thermoelectric materials, which maybe it could make a fibrous thermoelectric/peltier unit possible. This way you could heat and cool it on command without a super complex refrigeration system.
Source: Liquid-like Materials May Pave Way for New Thermoelectric Devices - www.caltech.edu
Source: Popular strategies for constructing polymer gel thermoelectric materials (wiley.com)
I was searching for polyvinyl alcohol based ionic polymer actuators, which is basically like a mix of a fuel cell membrane and a dielectric elastomer. However, I did found this article about a PVA shape memory polymer artificial muscle able to lift 1,100 times its own weight.
Basically, it is treated with sodium hydroxide and... That's it.
Source: https://www.ncbi.nlm.nih.gov/pmc/articles/PMC7610272/
Increasing efficiency:
I'm still writing the Project Log 87 at this moment, but I did find some information about increasing the efficiency of Shape Memory Alloy actuators:
This article claims “energy savings of up to 80%" (80% of 90% is 72% +10% to 15% = 82% to 87% efficiency):
Nickel/Titanium free SMAs:
https://www.intechopen.com/chapters/67075
https://link.springer.com/article/10.1557/s43578-021-00444-7
https://www.sciencedirect.com/science/article/abs/pii/S0141029618305030
https://www.mdpi.com/1996-1944/15/22/8089
I don’t know if this one is a rare-metal free shape memory alloy, but it showed a method to make it actuate 35 per second (35 hz): https://www.nature.com/articles/srep21118
(maybe I just missed it, but they didn’t write which alloy was used)
Other options: ❌
You may notice that the list is actually very small compared to the insane amount of different actuators out there, and that is simply because of a couple reasons:
- I only listed the ones that seems more viable and easier to DIY. Every actuator/artificial muscle sounds ✨amazing✨ when you read a news article about them, until you check its speed of contraction and relaxation, force-to-weight ratio, efficiency, cost, practicality and manufacturing process.
- Not all actuator types have their performance carefully explained and listed.
- Google simply didn't show me others.
For example, there is a type of electroactive polymer called "Ionic Polymer Metal Composite" (IPMC), you can ditch out the metal part, but most of the options that study/make this artificial muscle uses super expensive materials like gold, cobalt, nafion or a series of different materials.
The only article that I found about IPMC that actually cared about calculating its weight and output force achieved only a force-to-weight ratio of around 10, and it is made out of gold and nafion.
There are other actuators like liquid crystal elastomers, magnetorheological elastomers, carbon nanotube artificial muscles, chemically activated actuators, even light activated actuators and so many more.
But, as you can guess, they either are super expensive to make, hard to make, inefficient, impractical, slow or just have a really bad force-to-weight ratio.
All options seem interesting, now I need to figure out which one I will choose to waste my money and time on just to see everything going into flames...
Discussions
Become a Hackaday.io Member
Create an account to leave a comment. Already have an account? Log In.
You could also boil other liquids, like Trichlorofluoromethane R-11 refrigerant, that boils at 24C, or some hydrocarbons (be careful with volatility), Acetone, etc, Butane is quite easy to obtain from old AC units and refrigerators if they do not use R-11. Though Accidentally mixing these hydrocarbons with air could make them very very dangerous to handle (because one spark and BOOM)
Regardless, we do know you are already going to need a fuel tank for the generator, or at least a battery, why does the process have to be reversible? Perhaps just storing hydrogen peroxide in a tank could give you a few hours of runtime, it would expand to take up significantly more space when converted to steam and oxygen.
Regarding your previous comment, are you certain steam cannot be made on demand? instead of having to store it before use? like i mentioned, water-tube boilers, which are constantly being fed water, and were use for steam trains
https://en.wikipedia.org/wiki/Water-tube_boiler
https://en.wikipedia.org/wiki/Flash_boiler
Are you sure? yes | no
Interesting suggestions, thanks for commenting on my project logs. :)
About the reversibility: the mech would require thousands and thousands of liters of hydrogen+oxygen to work, more than 3000 liters, but that is a single contraction, so I will need way more than that per minute. And the compressed air tanks required to store so much compressed air would either need to work with very high pressure tanks (which would add another dangerous part of the already somewhat dangerous system) or I would need a gigantic air tank (also not good).
So the reversibility is just to keep the system volume small enough to take hydrogen/oxygen gases on demand and them store them again in the form of water.
Also, my objective is to make the whole thing work for at least 10 hours at nominal/maximum power, so using hydrogen peroxide would be safer and somewhat practical, but it wouldn't last very long (I think).
From what I checked I would need around 30 liters of hydrogen peroxide in 30% concentration to achieve the same 3000 liters to fill all the muscles (at best only half will be used, so 15 liters of hydrogen peroxide), that is for a single contraction, so the amount of hydrogen peroxide per minute can be just a guess, but I'm not confident on it.
I could increase the concentration, but it would increase the danger of it, hydrogen peroxide is used to instantly kill bacterial cells, and we are made out of cells.
Making steam is not really that hard, but the steam boiler can end up being too big/heavy and the muscles would need to be kept at high temperatures to avoid the steam from condensing back into water, which would require the materials of the artificial muscles to be insulating/temperature resistant, adding another layer of complexity/cost.
I mean, that is my reasoning, but maybe I'm overthinking things.
Are you sure? yes | no
Ah yeah, actually the temperature thing makes sense, the steam does have to be kept hot while in the muscles.
Perhaps using a low boiling point liquid could work, but you might need way too much to properly fill the muscles.
Speaking of, if you were to reduce the speed at which the mecha moves, perhaps electric motors would become feasible?
Also I am unsure if you have seen this already, but thermoelectric muscles are also a thing, nylon for example, contracts when heated. So a strand of these muscles would be a nylon string (tanza) with a small coil of copper wire (i've seen silver used to better results) going around the string, when a current is applied to the coil, it heats up, contracting the string.
Response time would be something you have to test though, and it definitely depends on the current.
This guy here is using nichrome wire https://hackaday.io/project/157004-material-linear-actuator-for-robotics
Are you sure? yes | no
For some reason Hackaday only allows me to answer the first comment.
I mean, yes, if I reduce the speed and/or torque, it would reduce the size of the electric motor, but we are talking about a mech that moves at the speed of a human being, not a super fast mech.
So, slowing it down even more would make it move like a snail...
Ah, yes, I have seen them, unfortunately, they are too slow to actuate and too slow to under-actuate. Just like shape memory alloys like Nitinol.
You would need a really good cooling system and separating the heating elements in sections to achieve motion control, which would be kinda complex and labour intensive.
But it would be very cheap to buy the parts.
If Nitinol wire didn't cost 700 dollars per kilogram I think I would've already used it...
(By the way, there are a lot of variations on Nitinol wire, the cheapest ones are called "superelastic" and the "shape memory alloy" type is the most expensive.)
Are you sure? yes | no
I understand, cooling would indeed add complexity. I suppose dielectric elastomers are the ones that make the most sense, if they are cost effective. how big/heavy do you think the mech will be? How different is it to an exosuit? Sorry if you have answered these already in a past log, there are many of them.
Are you sure? yes | no
Don't worry about asking, I actually like that someone is interested. And yes, there are too many project logs, I'm a bit too indecisive, unfortunately. :/
In any manner, I don't really know how heavy the mech will be, but I was aiming for something around 500kg so I don't need 100 horsepower just to run.
For now, the fuel itself would weight around 100 to 200kg, the pilot would also weight around 100kg and I still need to figure out how much the actuators would weight.
The dielectric elastomer seems interesting, but last time I checked, it seems like it would weight too much. I don't really know yet.
I was thinking on the mech being maximum 2 to 3 meters tall and for the pilot to be inside of it in a crouching position, controlling the mech's movements with force sensors without actually needing to move the whole body.
The difference from an exosuit is that you wear an exosuit, a mech you pilot. I actually wanted to make an exoskeleton, but I'm too afraid of messing something up and ending up with broken knees. So I intend on keeping the human pilot as safe as possible.
Are you sure? yes | no