The project consists of a servo, battery, charge circuit, microcontroller, and RF relay. When the RF relay closes, it signals to the microcontroller to start a 3 second timer. If the 3 seconds elapses without the relay opening again (to allow for power tests) the servo does a smooth 180 degree sweep, lifting the lid up and out, with the intention of pressing a green mushroom REX button.
Here is the current version, with a 3D-printable mechanism:
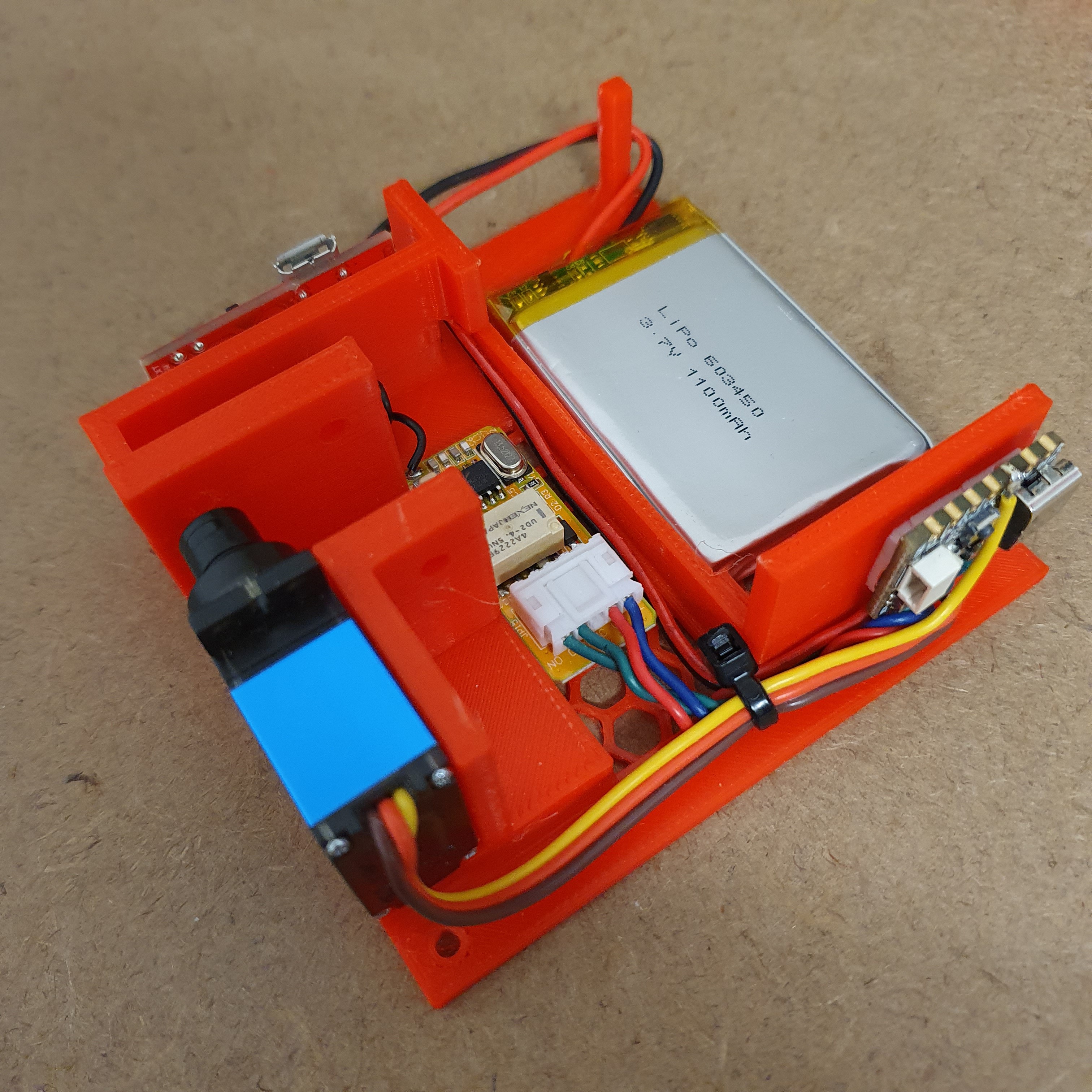
This was Version 1:
Here's a "how it would work" video with V1 hardware: