This is our third attempt at creating a 3D-printed 5/3 closed-center control valve.
This time, we had clearly identified our main challenge, thanks to the lessons learned from our two previous attempts: friction.
In each attempt, moving the shaft proved impossible because the friction between the sealing ring and the printed surface was too high. Finally, we decided to switch to another material for the valve bore. We opted for a transparent acrylic tube to construct the valve body, as it provides a smooth surface and is see-through, which was an added benefit.
We then printed a new version to test the force required to move the piston with the sealing ring inside the acrylic tube.
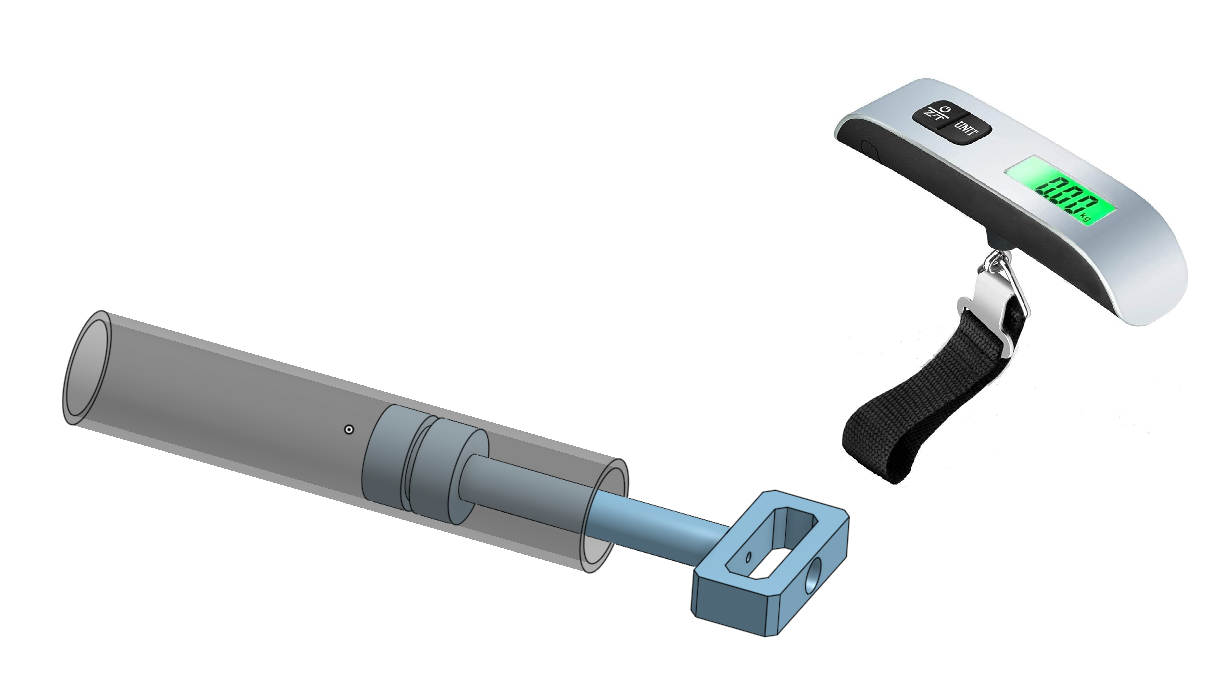
Upon testing, we found that the required force was reduced to around 200–300g when the entire assembly was properly greased. This result indicated that our second iteration, using the servo motor, could be viable with the acrylic tube.
However, in the end, we decided to abandon the 5/3 closed-center control valve design altogether. It was simply too complex to manufacture efficiently with 3D printing. After conducting further research, we discovered another type of valve that we believe will be significantly easier to produce using 3D printing technology.
Discussions
Become a Hackaday.io Member
Create an account to leave a comment. Already have an account? Log In.