For the last few years, I have been working with engineering students at Cal Maritime, operating autonomous boats to gather oceanographic data. The most successful boat to date has been Dumbo, a 1 meter long catamaran (built by students) that measures salinity, temperature, and dissolved oxygen in San Francisco bay. Here is a link to a video of Dumbo in action.
I designed n3m0to be a smaller, 3-D printed boat that can carry the same instruments as Dumbo and perform the same mission. The goal is for n3m0 to be easily assembled for students and "citizen scientists" to perform on-the-water measurements. It isn't a speed boat, but should be fast enough to beat the strong currents in the Carquinez Strait, while I hope for an hour or so of run-time (yet to be tested).
The hull shape is based on lines from a PT boat that I found online. I widened the aft sections for more volume and drew it up in Fusion 360.
The hull is printed in sections to fit most 3-D printer volume restrictions. And you can choose cool stripe patterns! Someone please build one with resistor color codes.
N3m0 uses the APM autopilot system and Rover firmware for fully autonomous operations. You can set up waypoints and the boat will go to them and take a measurement. N3m0 currently carries a ESP8266-based payload computer with a water temperature sensor. The data can be retreived from the boat's web server.
I use Tower on my android phone for the groundstation.
N3m0's mechanical parts are standard model boat fare: steering servo, brushless motor, propeller shaft and prop.
N3m0's payload computer is based on a ESP8266 board and small OLED display.
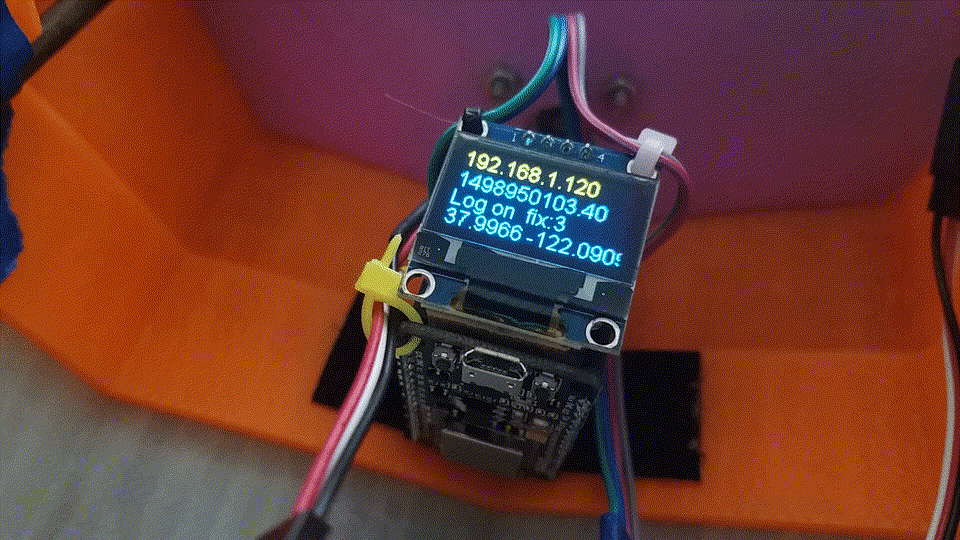
This computer listens to the telemetry data from the autopilot and takes measurements at each waypoint in the route. The data is saved to a file and the payload computer runs a webserver so you can view and save the data. The webserver can connect to your home wifi or serve as an access point if you are in the field. The data is stored as a text csv file but you can also get a geojson format file, or an html file with a map display (sample data).
Current status: N3m0 is working. As of July 2017 the boat has successfully operated autonomously and has gathered data with its temperature sensing payload computer.
Video of first autonomous operations (you can hear the Andropilot groundstation software announce the waypoints):
I know this project is probably long retired, but I have a question regarding the prop shaft. What diameter of K&S tubing did you use? Thanks, and great project.