So the right turn errors were from the servo horn jumping a cog & getting cracked, not the pot. It happened for some time, but intensified with the camber adjustment, because of the increased rolling resistance. There are servo savers & a return to feedback problems or going back to stock camber & tire wear.
The direct servo link is a huge benefit to video quality & lions are more interested in efficiency, so the decision was made to return to the stock camber & apply liquid electrical tape to the tires. The mane problem with a more robust vehicle is the increased weight of batteries, so efficiency is a goal. The other problem is starting a new learning process when most everything that can go wrong with the lunchbox has been found. Fixing wheels & transmissions isn't the only thing lions do.
$7 later, there was this.
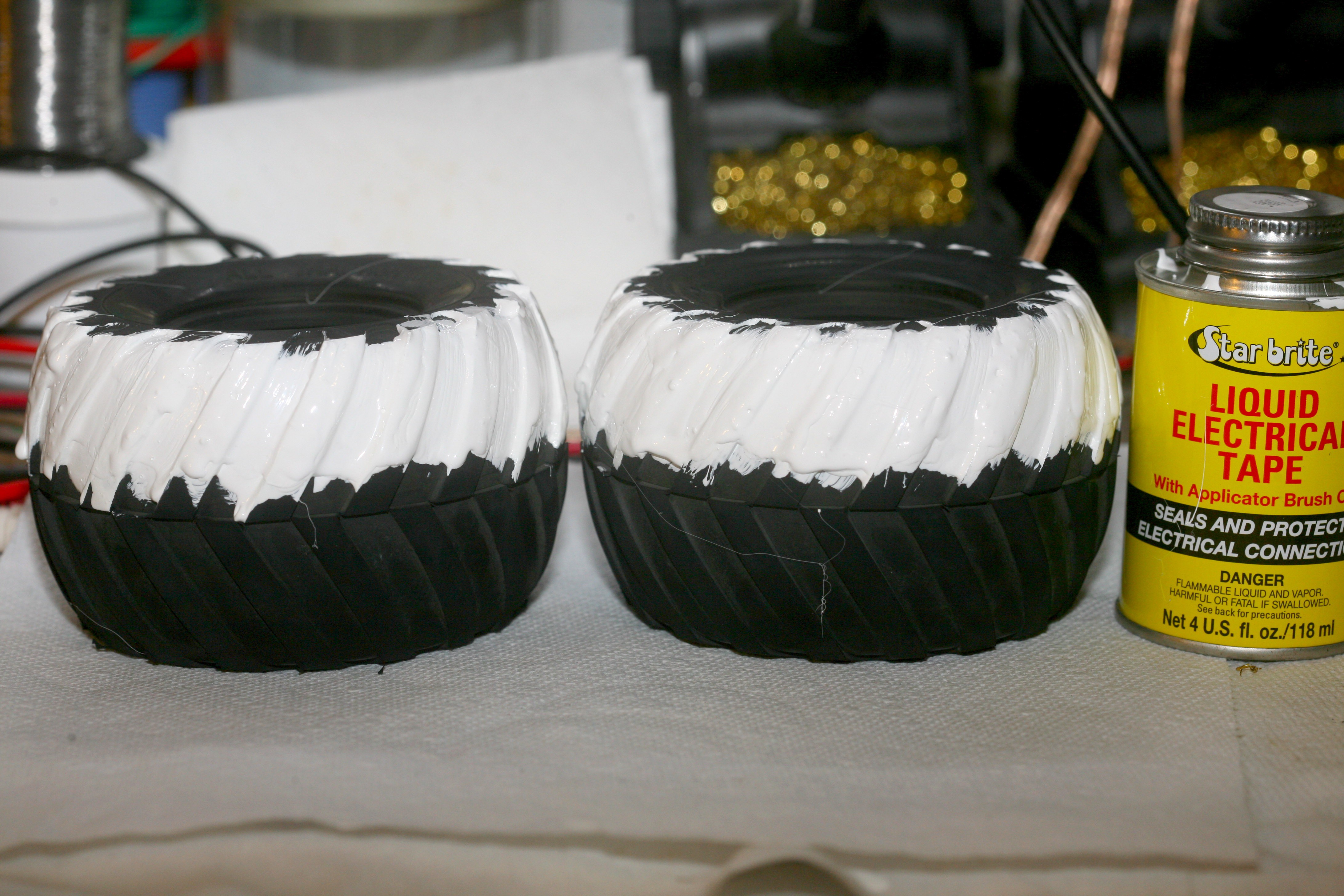
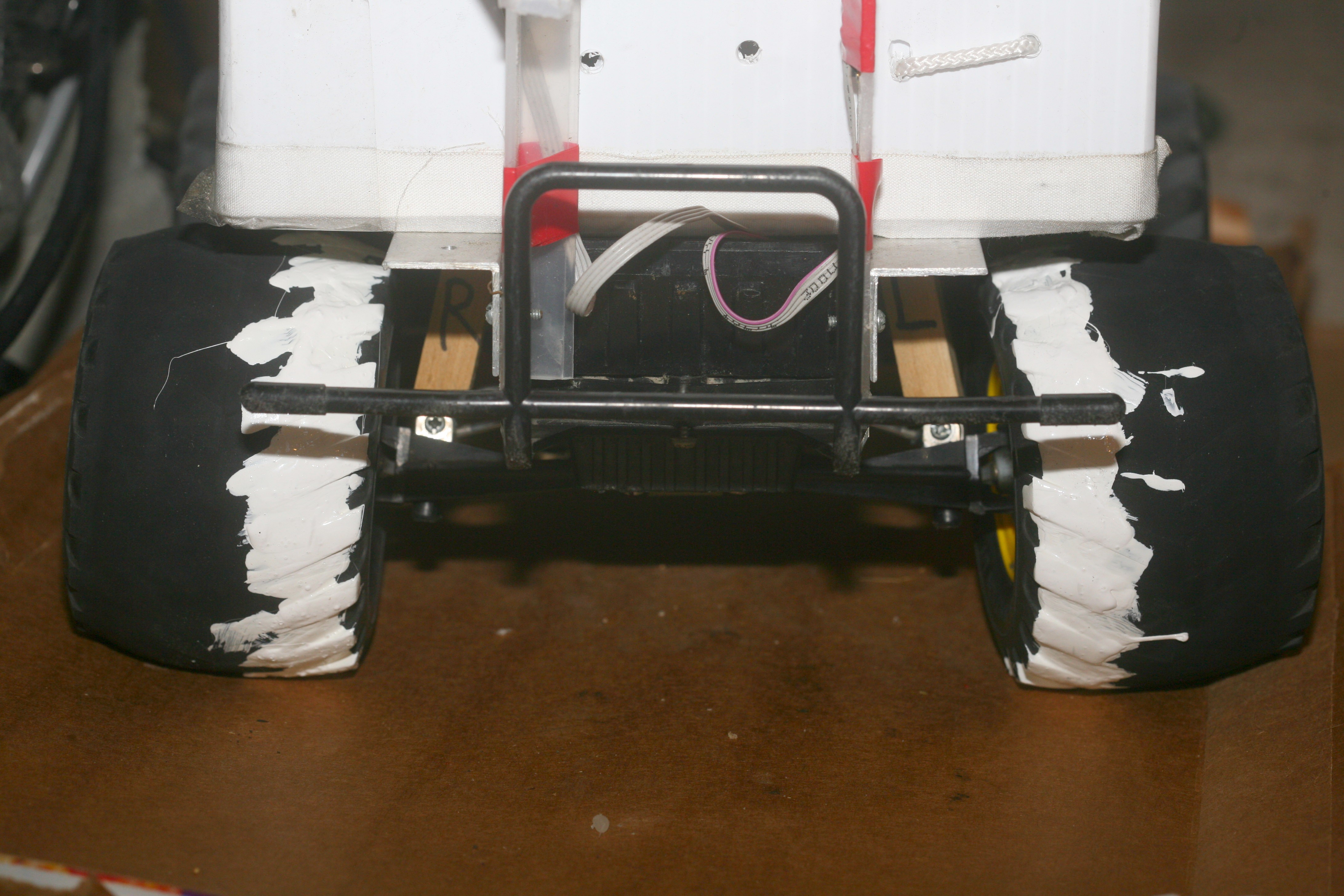
This was very expensive, but worth trying.
Another 1.4 mile test, but with no cargo & speed reduced, dropped back to 328mAh/mile & theoretically the most efficient toe in should be the same in both camber settings.
Another 9.45 miles with 2.6 at 7m12s/mile flaked the coating completely off. That burned 2775mAh or pretty much what it was before lowering the suspension.
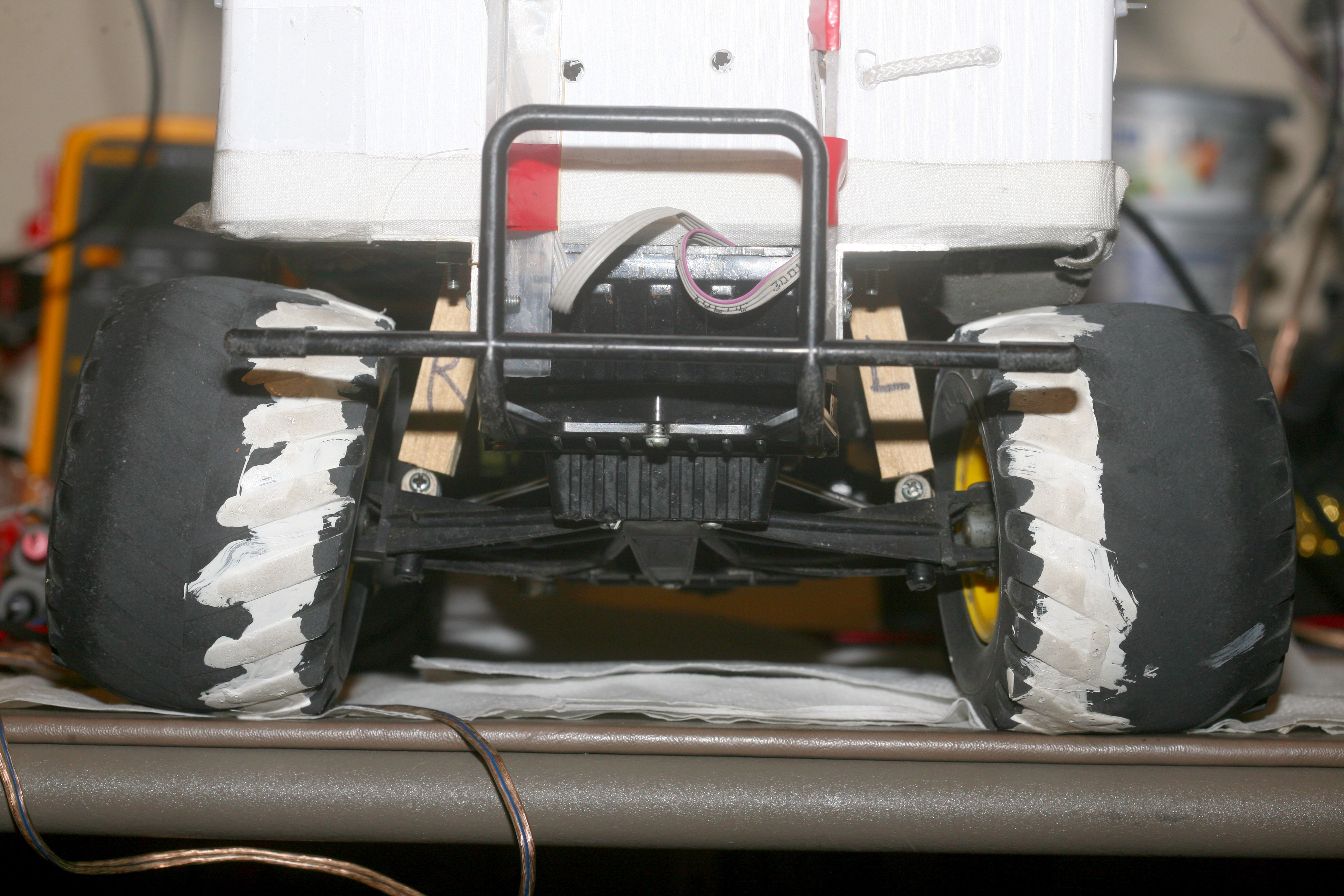
At least, it showed the friction was concentrated on a small part of the edge & this small contact area was probably the key to great efficiency. The toe in with stock camber was the same as the best efficiency with vertical camber, so there wasn't a cross talk between camber & toe in.
Discussions
Become a Hackaday.io Member
Create an account to leave a comment. Already have an account? Log In.