**COMING SOON TO CROWDSUPPLY! Follow here!**
2018HackadayPrize Final Video:
Introduction:
"Erector Set, Tinker Toys, Meccano, Lincoln Logs, LEGO ... All of these toys could be used to construct fanciful models of things, but not the things themselves. The game-changing 'toys' available to today's girls and boys are capable of making real things."
Of course that quote refers to things like 3d printers and laser engravers, but I saw it as an interesting challenge. A toy that can make real things... Why not customized coffee mugs? :)
TinyCNC PCB SPECS:
I found it necessary to make a customized PCB for this application. I could not find an off the shelf arduino based servo driver that did everything I wanted for the cost & size I needed. I ended up working with Scott Pierce and his open source pcb design to modify it for my needs. This is the result:
- Utilizes 1x Arduino Nano V3
- System Inputs: Up to 2X Analog Joysticks, Bluetooth (HC-06), Ultrasonic (HC-SR04), IR wireless remote, and of course micro-USB
- System Outputs: Up to 9x servo motors, built in Buzzer & LED.
- Power Requirements: 6VDC Wall Wart or 4X AA (Energizer Ultimate Lithium Recommended)
- Drives servos directly from battery power unhindered by the arduino and has extra wide copper traces to minimize board resistance.
Mug-O-Matic Tool Path Summary:
1. Create or find an image file you want to draw and convert it to an STL that is 0.1mm thick.
2. Use RepetierHost + Slic3r to convert the model into gcode.
3. Use Processing to send commands line by line from computer over usb.
4. Use Arduino with the Mug-O-Matic Gcode_reader sketch to decode commands.
.
So it draws on Mugs, But what else can you do with it?
All parts in the TinyCNC Collection are compatible with 2 recurring design patterns. One is the 'snap on lid' that allows you to connect different base structures around the PCB. The other is a 20mm spaced hole pattern that allows for reconfiguration of all modules at 90 deg angles. So all parts either snap together or are connected by a single size of 'plastite' screw, which forms its own threads when installed.
All actuators are powered by 9g size servos, (SG90 extremely cheap, MG90s metal gear good quality, MG91 pro-quality, FS90R continuous rotation) all are physically interchangeable.
The servos are also great because they don't require motor drivers and they are physically small and yet still able to perform meaningful work. Up to ~0.5kg from the linear actuator in my simple experiment, though it varies directly with voltage.
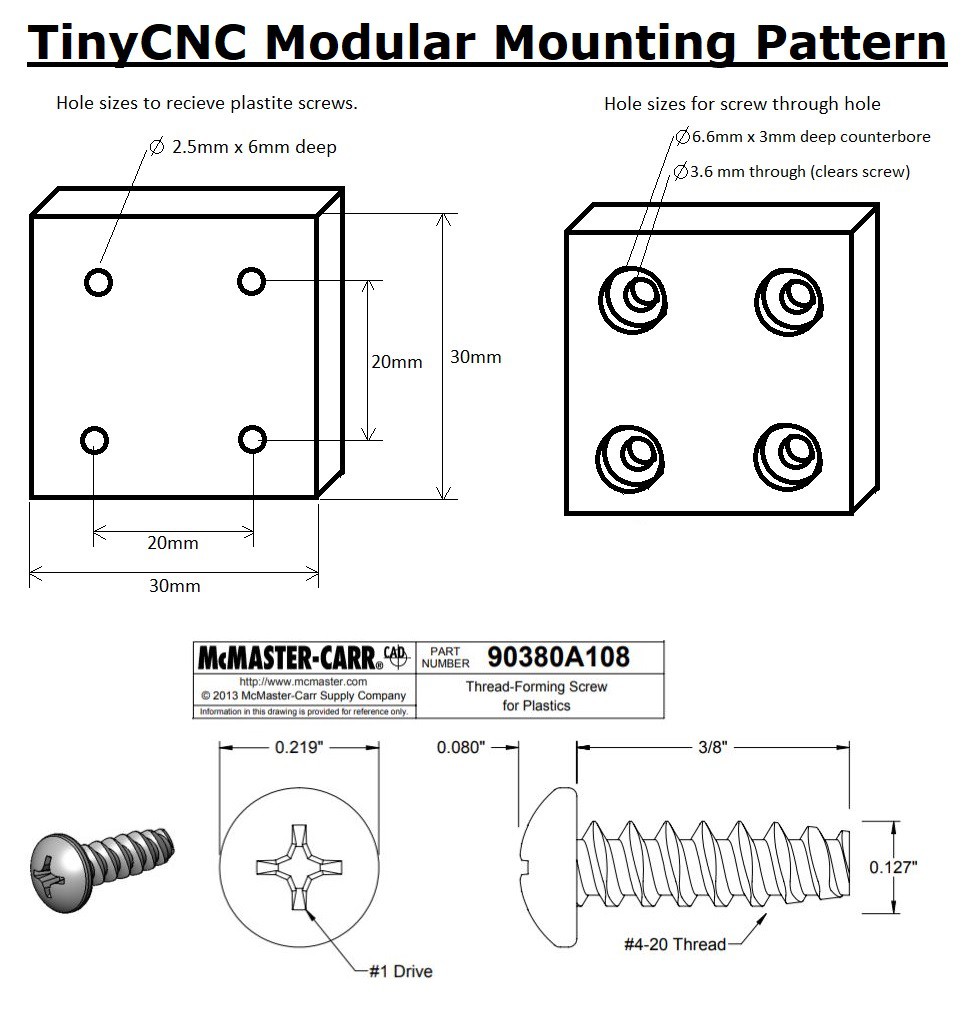
Inspiration:
My idea was inspired in part by another interesting open source plotter robot design by MakerBlock. In particular, he and others developed (GRBL based) arduino code that allowed a robot to read g-code and plot with a marker using hobby servos, a task typically done with stepper motors. Great idea and perfect for making an ultra low cost robot that still had lots of functionality.
The other part of the inspiration was to emulate the famous Egg-bot, except with lower barriers to entry, more hackability, and to produce objects with more everyday appeal.
Linear Actuator Design:
The key module in the Mug-O-Matic is the linear actuator assembly. I hadn't found anything available online so I designed one from scratch. Why a Rack & Pinion?
I choose a rack & pinion type actuator to keep the vitamins low and the movement speed fast. (As opposed to a slow leadscrew or pulley driven actuator with belts & bearings). Well for those reasons and the fact that hobby...
Read more »
Hey Mike, appreciate it! The photo might look faded, but it's actually a drawing on a coffee mug, allowing for a new design each morning. (Note: Sharpie washes off in the dishwasher.) Adding a clock is a cool suggestion—I'll throw it onto my already massive to-do list! 😊
Can you please have a look on my new initiative. I really appreciate it
https://thesonicmenu.com/