ARX X1M
Design Overview
X1M focuses on developing an advanced mechanical design that maintains a high functionality whilst being modular and maintaining ease of assembly. The hand mainly functions off of a configurable whippletree block that drives two removable finger modules (index & middle, ring & pinky) when actuated. Driving the actuation is a configurable 1 to 3 stage block and tackle pulley system to provide mechanical advantage or shorter actuation for use with motorised attachments. Additionally, alternative attachments may be placed on the back of the palm using the additional mounting holes. The thumb on the hand is also a removable module for a fixed thumb or an actuated thumb. Wrist can be rotated 180 degrees with 7 indented positions that can be adjusted for varying stiffness.
Design Features
- Mechanical prosthetic design
- Easy to print - No TPU prints
- Easy to assemble - Roughly 30 mins to assemble with minimal need for drilling, cutting or sanding
- Materials are fairly easy to source - Uses common screws, fishing line, elastic cord and 3D printer filament
- Design is durable and is capable of withstanding impacts and drops
- Able to assist with lifting and grasping of objects - Able to lift 8kg
- Modular hot-swappable finger and thumb sections
- Configurable whippletree and pulley system allowing for 1 to 3 stages
- Additional print features (custom brim, supports and part reinforcements) are added to aid printing
- Back of the palm has additional mounting holes for extra attachments
- Compatible motorised attachment in works
- Wide range of rubber finger tip options available
Hand Design
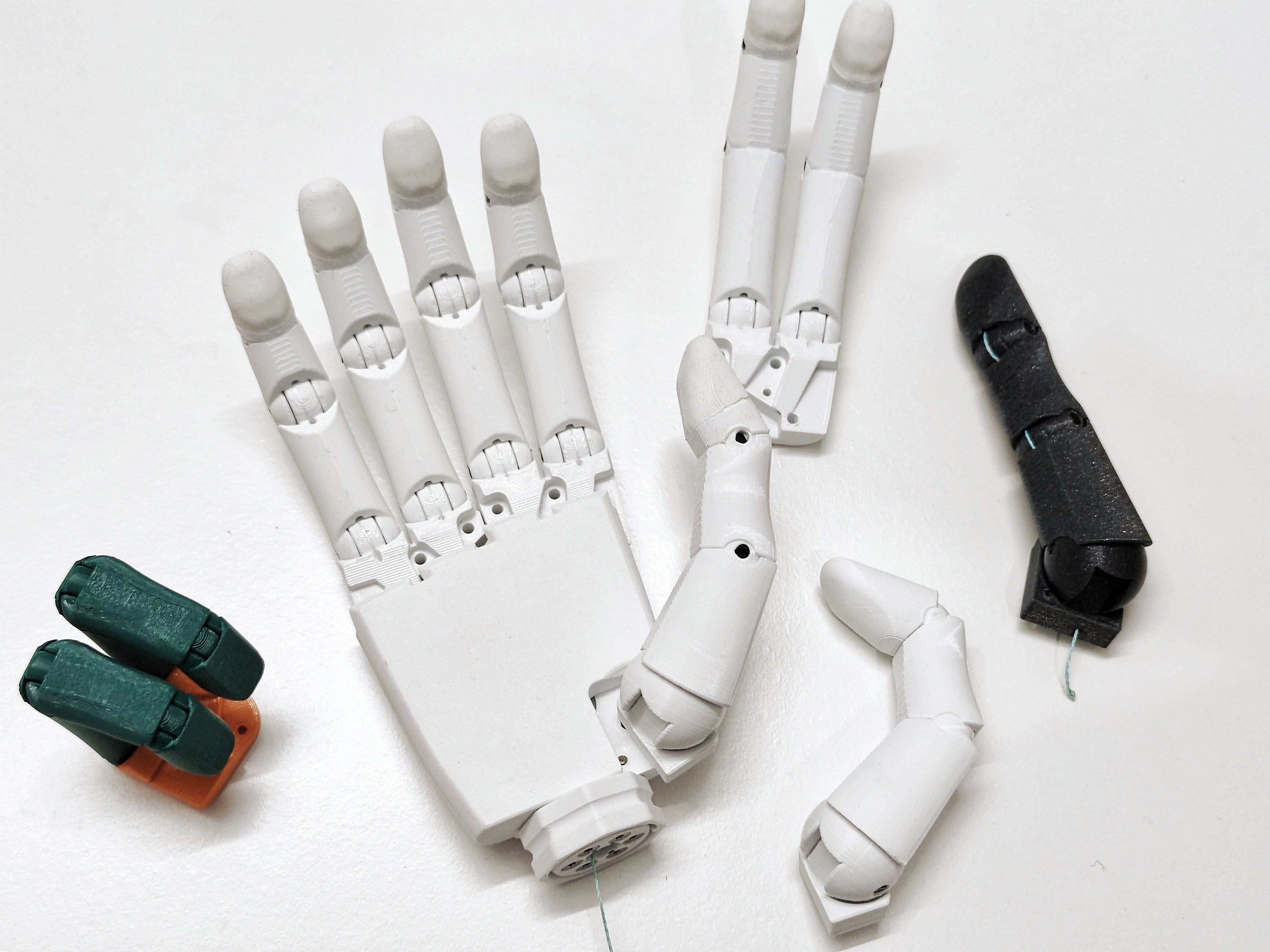
- Finger Modules
The fingers of the hand are separated into two modules with one module consisting of the index and middle, and the second module consisting of the ring and pinky. The modules can easily be swapped out by removing a few screws and unhooking the tendon line.
The ability to swap out the finger module aids with allowing for ease of customisation and experimentation of alternative parts. The fingers of the module can have fewer joints, posable, fixed or can be designed to be application specific. Alternative finger mechanics like TPU joint fingers or compliant fingers can also be experimented within the same design as a module.
Current fingers used in the modules also bring their own set of customisability and experimentation, as the pins, tendons, elastic and rubber grips can be adapted to whatever possible requirements or lack of source materials. Every part of the finger can be disassembled and replaced, so each part can be replaced with alternative materials or designs. Shown bellow are a range of possible elastics (TPU, silicone, latex and nitrile) as well as a range of possible finger tip materials (silicone cast, finger protector, TPU print, rubber feet, Sugru)
- Thumb Module
The thumb module allows for swapping out between a fixed thumb or an actuated thumb. Both thumbs have a 3 position ratcheting mechanism which is user adjustable. The module is only held by one screw which allows for easy replacement in case of any damage to the thumb or to swap to a different type. Additionally, application or user specific thumbs can be designed.
- Palm
Whippletree system designed into the palm consists of a rotating block with a channel for each pair of fingers, index-middle and ring-pinky. Each channel allows for slipping between the pairs of fingers to provide independence between fingers when either is obstructed when closing. When either pair is fully obstructed, the rotating block allows for further independence between finger pairs.
For the pulley system used in the palm, mechanical advantage can be configured by adjusting the method of cord attachment as shown in picture bellow. With a 2x mechanical advantage, the cord is attached to the main palm body, and routed through the whippletree block. For 3x mechanical advantage, an additional pulley is added to the cord path and the cord is attached to the whippletree...
no,, unfortunately