Designs, Electronics, and Code
All the exoskeleton glove designs, electronics, and code can be found at the following URLs:
https://github.com/newdexterity/Body-Powered-Exoskeleton-Glove
https://github.com/newdexterity/Hybrid-Exoskeleton-Glove
The project is distributed under the Creative Commons Attribution 4.0 International License (https://creativecommons.org/licenses/by/4.0/)
Background
According to the World Health Organization (WHO), in many countries, less than 15% of people who require assistive devices and technologies have access to them [1]. Impairment of hand function is one of the most common consequences of neurological and musculoskeletal diseases such as arthritis, Cerebral Palsy, Parkinson's Disease, and stroke [2]. In order to accelerate the rehabilitation process of impaired people, it is important to execute repetitive movements and to try to perform daily tasks [3]. Many robotic devices have been developed to assist patients with limited mobility of the hand during physical therapy or to augment the capabilities of able bodied users [4]. In this project, we propose two compact, wearable, and lightweight assistive exoskeleton gloves for grasping capabilities enhancement. The first device uses a body-powered mechanism while the second device is an underactuated, motorized solution.
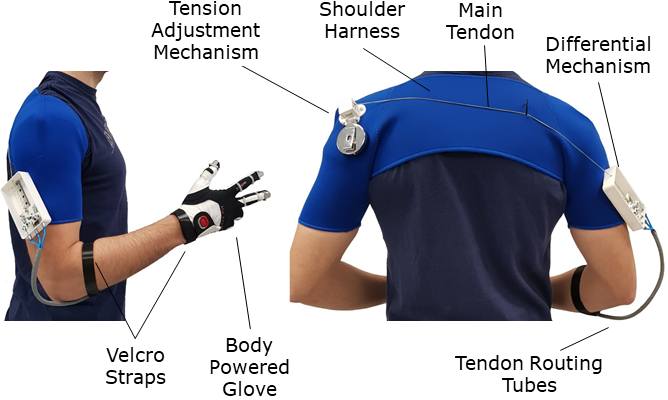
A Body Powered Exoskeleton Glove
The body-powered exo-glove was designed to enhance the grasping capabilities of the user, providing easiness and intuitiveness of operation, with long autonomy, low maintenance, and low cost. The device consists of four different parts: the differential module, the soft glove, the tendon tensioning and adjustment mechanism, and the harness.
The body-powered mechanism allows the transmission of forces from the upper body (e.g., the shoulders) to the index, middle, and thumb fingers through the tendon routing system. Simple body movements can increase the tension of the tendon, actuating the soft exo-glove.
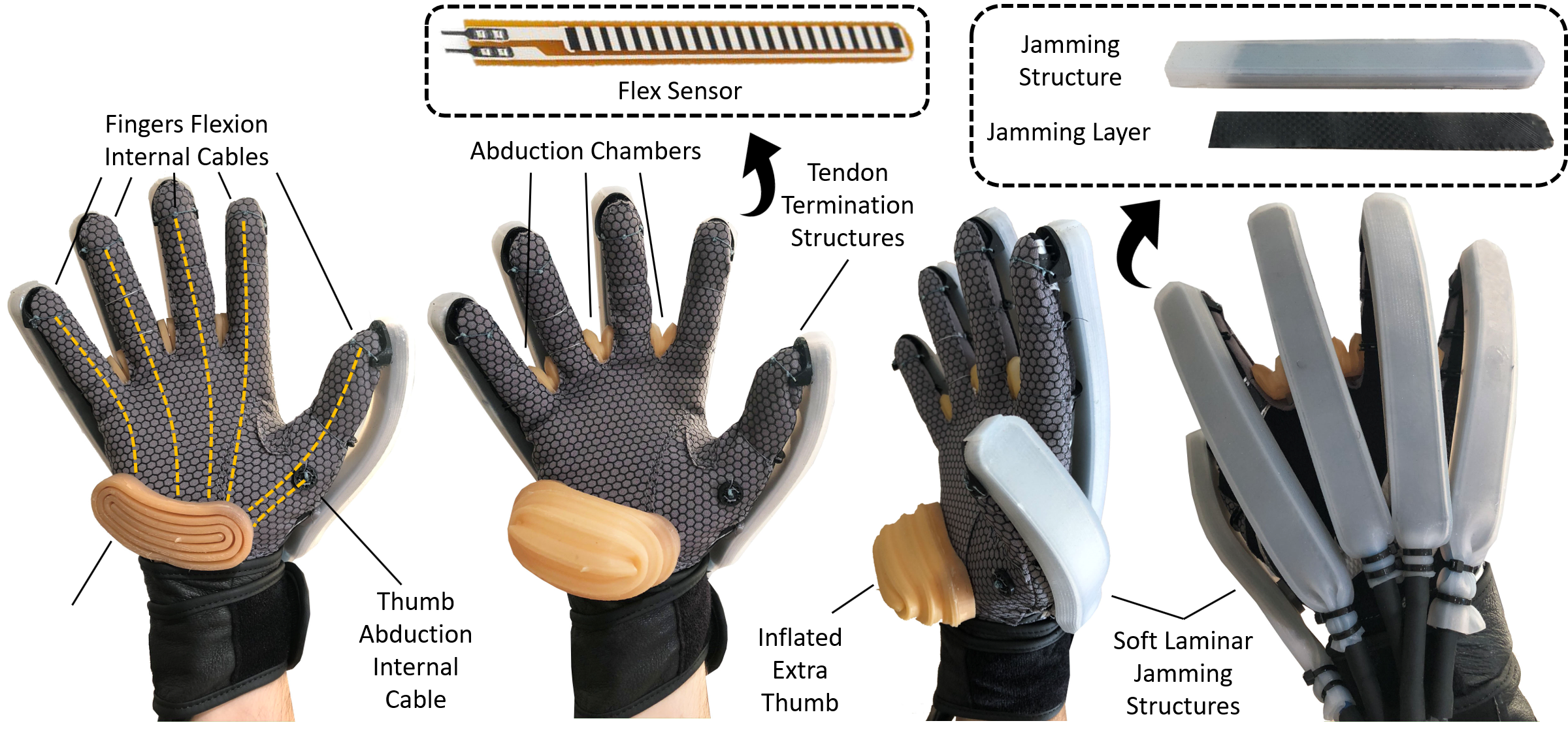
A Hybrid, Motorized Exoskeleton Glove with Variable Stiffness Joints, Abduction Capabilities, and a Telescopic Extra Thumb
The hybrid exoskeleton glove is a more sophisticated device that is composed of two main systems: the soft exoskeleton glove and the control box. The soft glove system of the device is composed of a thin, high sensibility glove, a tendon-driven system that consists of six artificial tendons, a pneumatic system that consists of four soft actuators.
The operation of the device is straightforward. Using the smartphone app, the user selects the mode desired to control the exoskeleton glove. The user can combine the motions (e.g., full grasp with abducted fingers or tripod grasp with the extra thumb inflated). A flex sensor can be selected to trigger the desired motion when a set bending angle is reached. The information is transmitted to a microcontroller through Bluetooth communication. Then, the microcontroller activates the chosen actuators that are connected to the glove.
The hybrid exoskeleton glove is modular and each of the glove features can be used independently. The abduction chambers, the extra thumb, and the jamming structures can be adapted or removed according to the user's needs.
References
[1] W. H. Organizationet al., “Guidelines for training personnel indeveloping countries for prosthetics and orthotics services,” 2005.
[2] C.-Y. Chu and R. M. Patterson, “Soft robotic devices for hand rehabil-itation and assistance: a narrative review,”Journal of neuroengineeringand rehabilitation, vol. 15, no. 1, p. 9, 2018.
[3] P. S. Lum, C. G. Burgar, P. C. Shor, M. Majmundar, and M. Van derLoos, “Robot-assisted movement training compared with conventionaltherapy techniques for the rehabilitation of upper-limb motor functionafter stroke,”Archives of physical medicine and rehabilitation, vol. 83,no. 7, pp. 952–959, 2002.
[4] P. Maciejasz, J. Eschweiler, K. Gerlach-Hahn,...
Read more »