Welcome!
⚠️DISCLAIMER⚠️
The content presented on our website, YouTube channel, Download Kit, and all other internet and real world presences, regarding potentially hazardous processes is for educational purposes only.
Viewers are hereby cautioned against attempting to replicate any techniques or procedures demonstrated unless they possess the necessary legal qualifications and certifications.
We expressly disclaim any liability for consequences arising from the replication of such activities without proper authorization or expertise.
Viewers are advised to seek professional guidance and adhere to applicable laws and safety regulations before undertaking any similar endeavors.
⚠️⚠️⚠️
Our 2022 Hackaday Prize Contest Entry Video
Quick Links
The Problem
You all know that plastic waste is bad so I'm going to summarize the scale of the problem simply with 5 numbers.
Every year we produce over 350 million tons of new plastic.
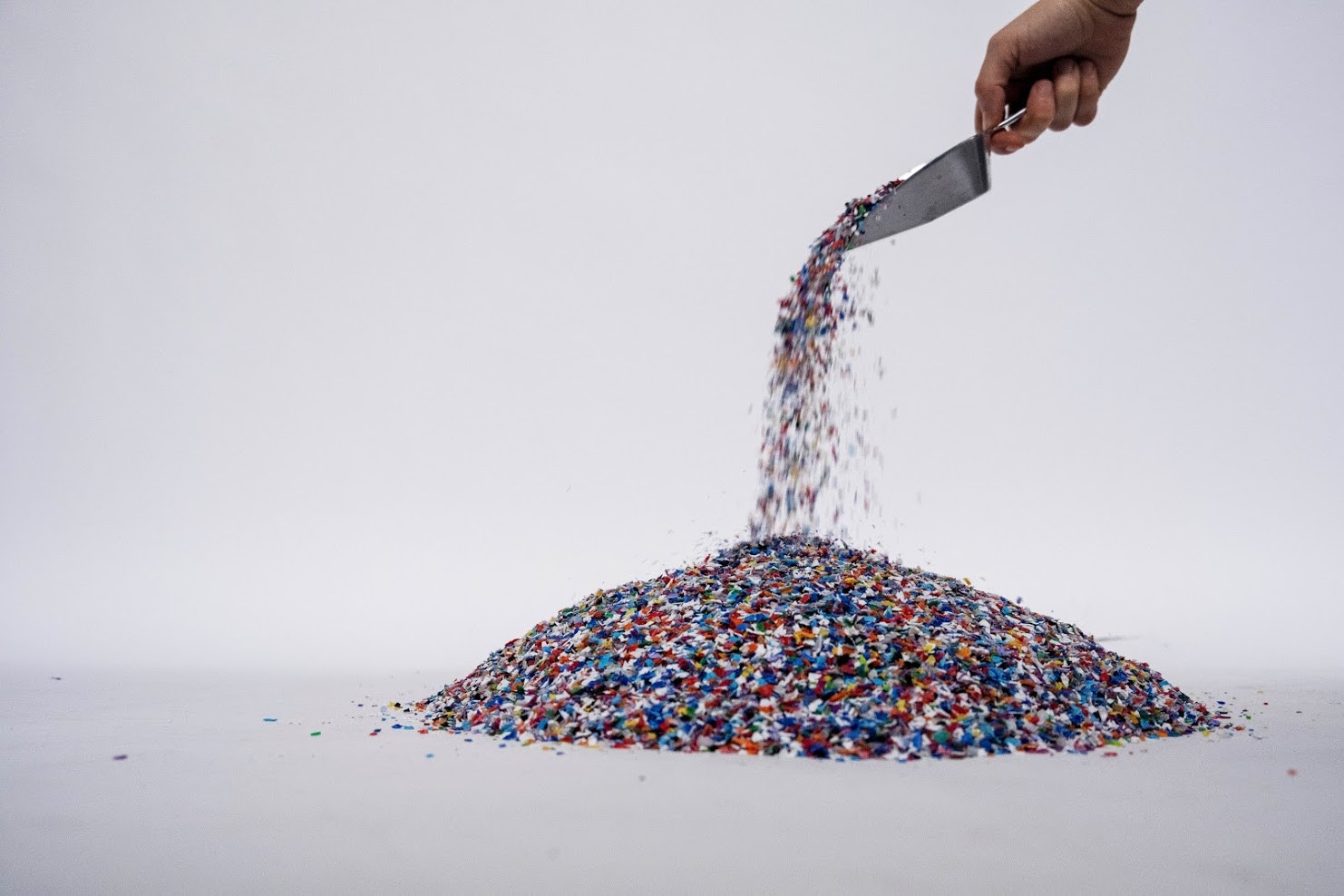
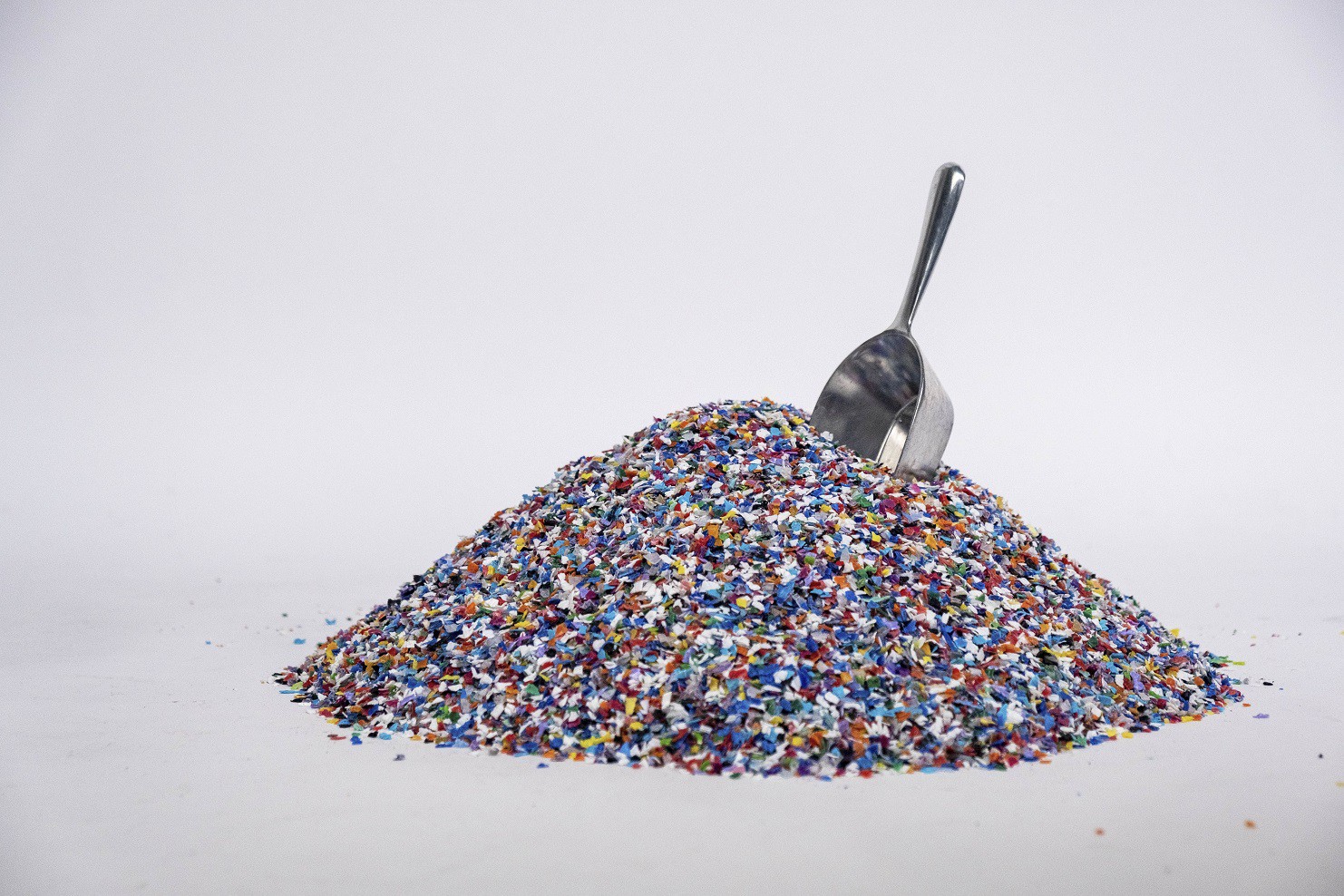
More than 90% is recyclable...
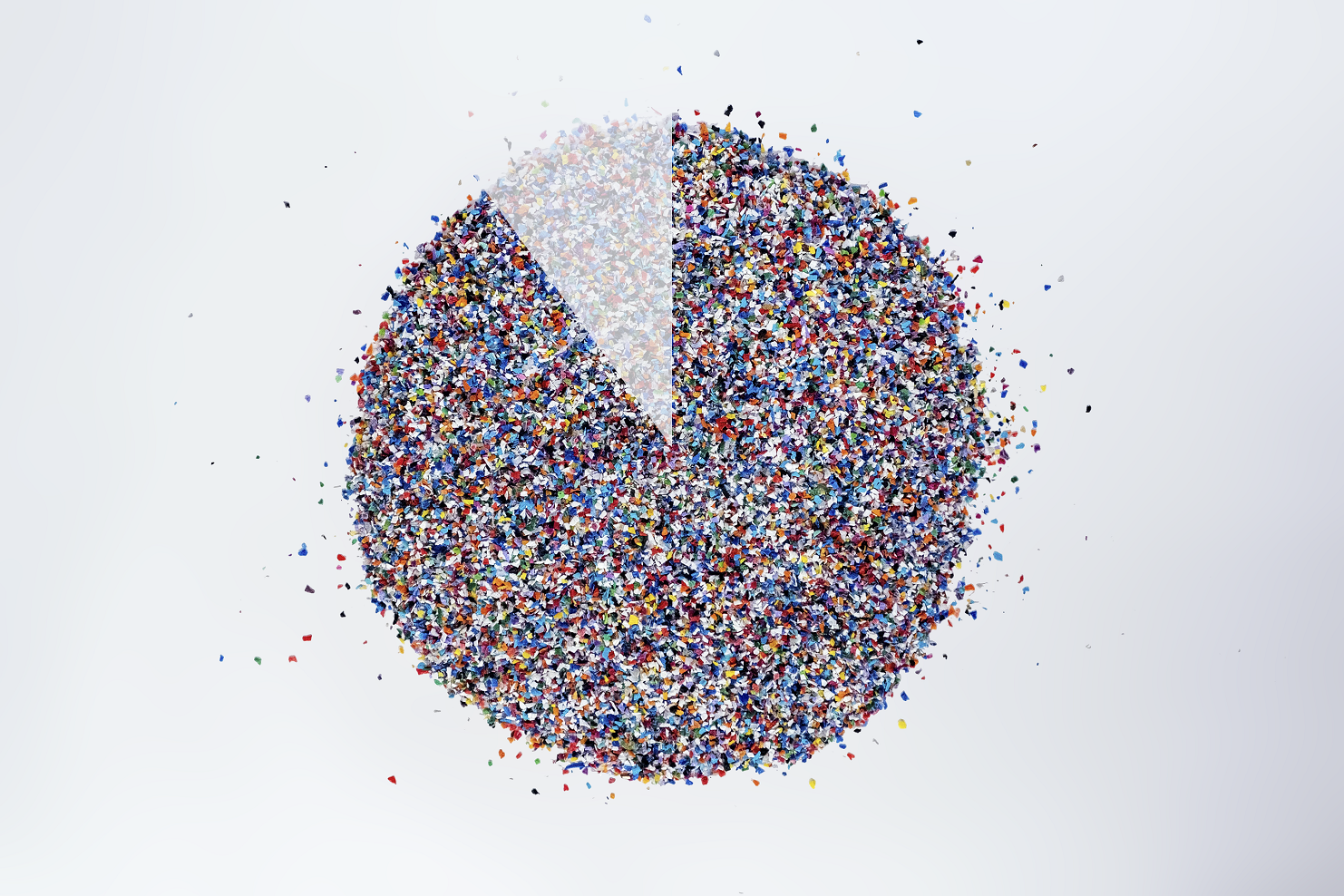
...but less than 10% actually gets recycled.
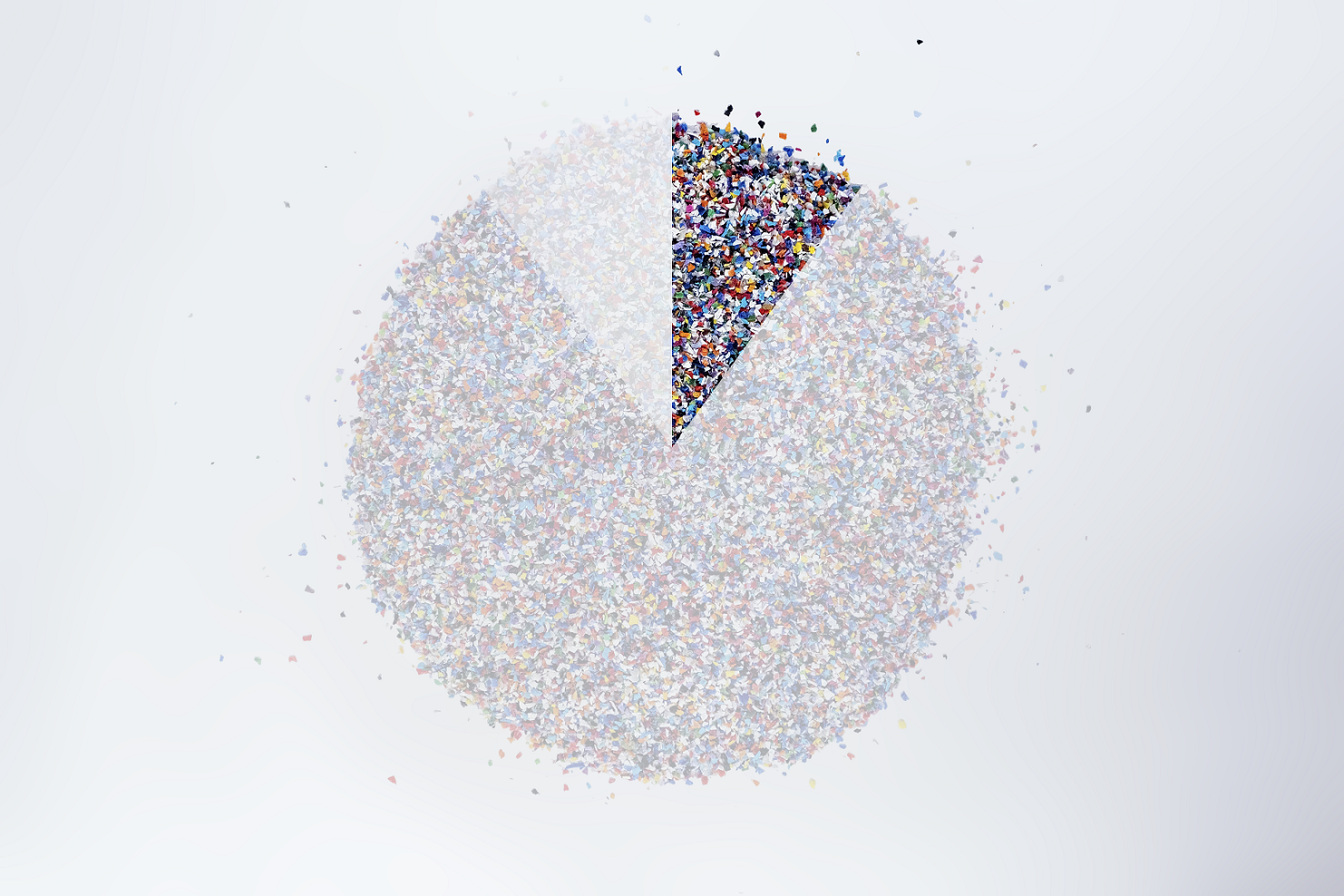
This means that there is over 6 billion tons of plastic waste in the world right now, ready to be collected and recycled.
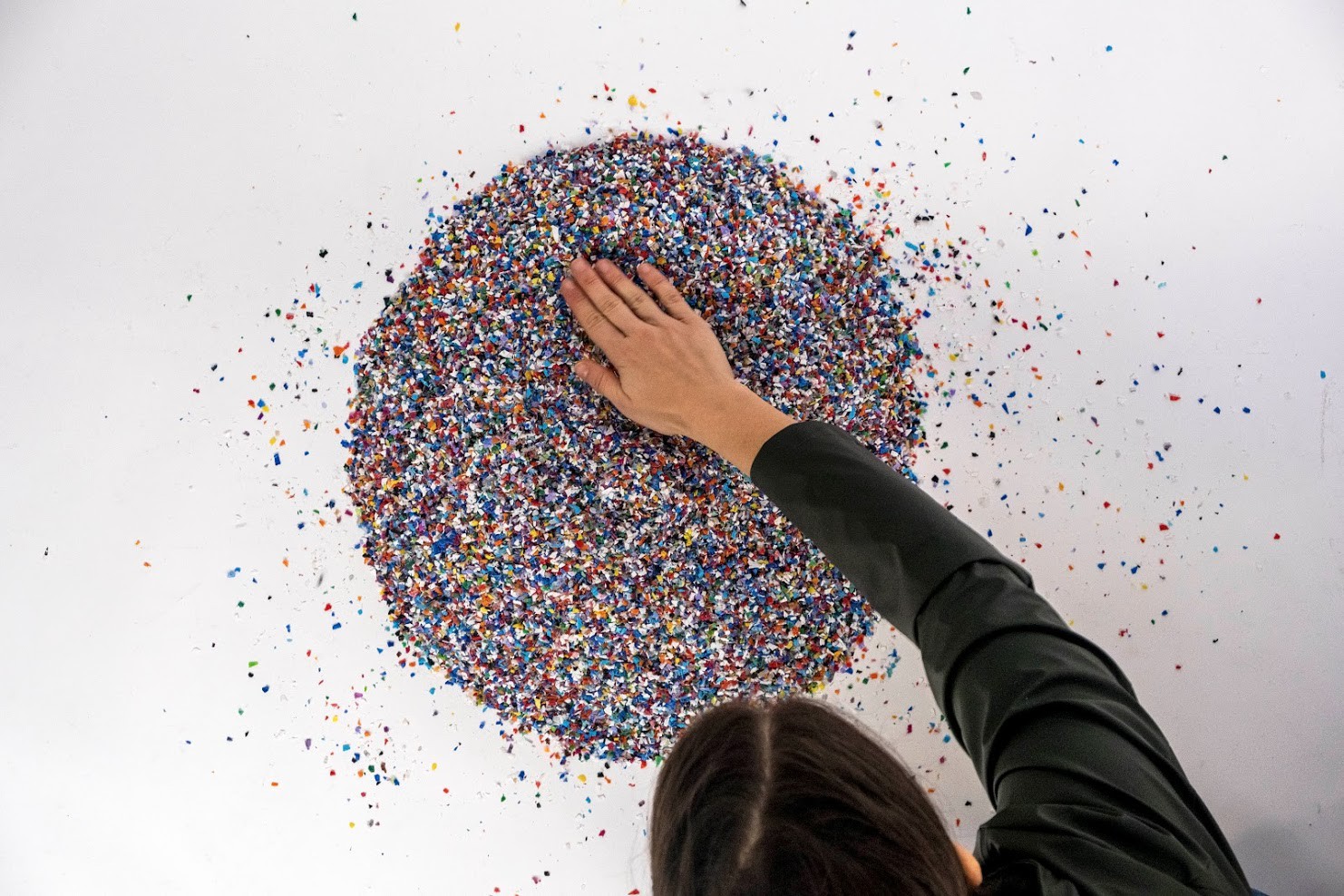
So even if we completely stopped producing plastic right now there is still a little bit we need to tidy up.
If left uncollected it remains in the food, water and air that we humans and almost every other living thing, in our ecosystem, are at risk of consuming and being polluted by it.
The Challenge: Reuse, Recycle, Revamp
We are working to dissolve the economic, technical and social barriers that prevent people from getting recycled plastic products into the world.
Our project is all about increasing accessibility to recycling equipment and hence enabling more people to recycle.
Why?
Recycling provides a solution to both:
1. Extracting raw plastic pollution from the environment by capturing and storing it in large pieces that are kept out of the ecosystem by human utilisation and are easy to manage at the end of their product life to ensure that they do not end up back in the ecosystem.
2. Providing an alternative to dependency on raw materials. Humans are always going to make things, by using recycled materials we reduce the extraction of raw material, such as wood, and its inherent burden on the environment.
Our solution, a recycled plastic skateboard deck (RPSD), is to provide the means to produce a fun, healthy and directly tangible reward for recycling that demonstrates both the aesthetic beauty and the mechanical strength of the material to its users and observers, with the aim of incentivising and catalysing plastic recycling.
A skateboard was also chosen because of its ease of manufacture. We want it to be as easy as possible for people to recycle, so we chose a simple product with no, ribs, undercuts or complex geometry and just one single solid body. This is our way of trying to dissolve any technical barriers, potential manufacturing defects and complications that would stand as obstacles in the production process.
Ease of access is why all of our research is, and always will be, open source. To reduce the barriers that IP restrictions, copyrights and patents place in front of designers and recyclers who want to start recycling. We want anyone, anywhere to be able to pick up our project with as little resistance as possible and start recycling plastic.
The process to build the mould itself has been designed to be as easy to replicate as possible without any specialist tooling, just things found in a standard metalworking workshop, a grinder, a pillar drill and a welding machine. This is to prevent economic,...
1. Thanks for the support! It motivates us to keep going!
2. The turnaround is 2 hours of work per deck, so you can make 4 in an 8 hour work day, and 32 in a normal work week, with one day for other tasks, (posting, cleaning, maintenance etc). We have tested this as a business model and it works :) (This is with one mould and one extruder), if you have two moulds per extruder theoretically you can make 6 + decks per day. As for the ROI, we have calculated an 8-year financial forecast for the project, we will share this in a project log very soon if you have any specific questions you can post them here or message us and we can answer them for you. Very cool to hear you are considering implementation!