Overview
I have built a relatively small USB-C powered capacitive discharge spot welder, which can be used to build battery packs for various devices and avoid throwing old devices out just because it's not possible to buy an original battery anymore. I tried to design this spot welder in a bit different way than other spot welders.
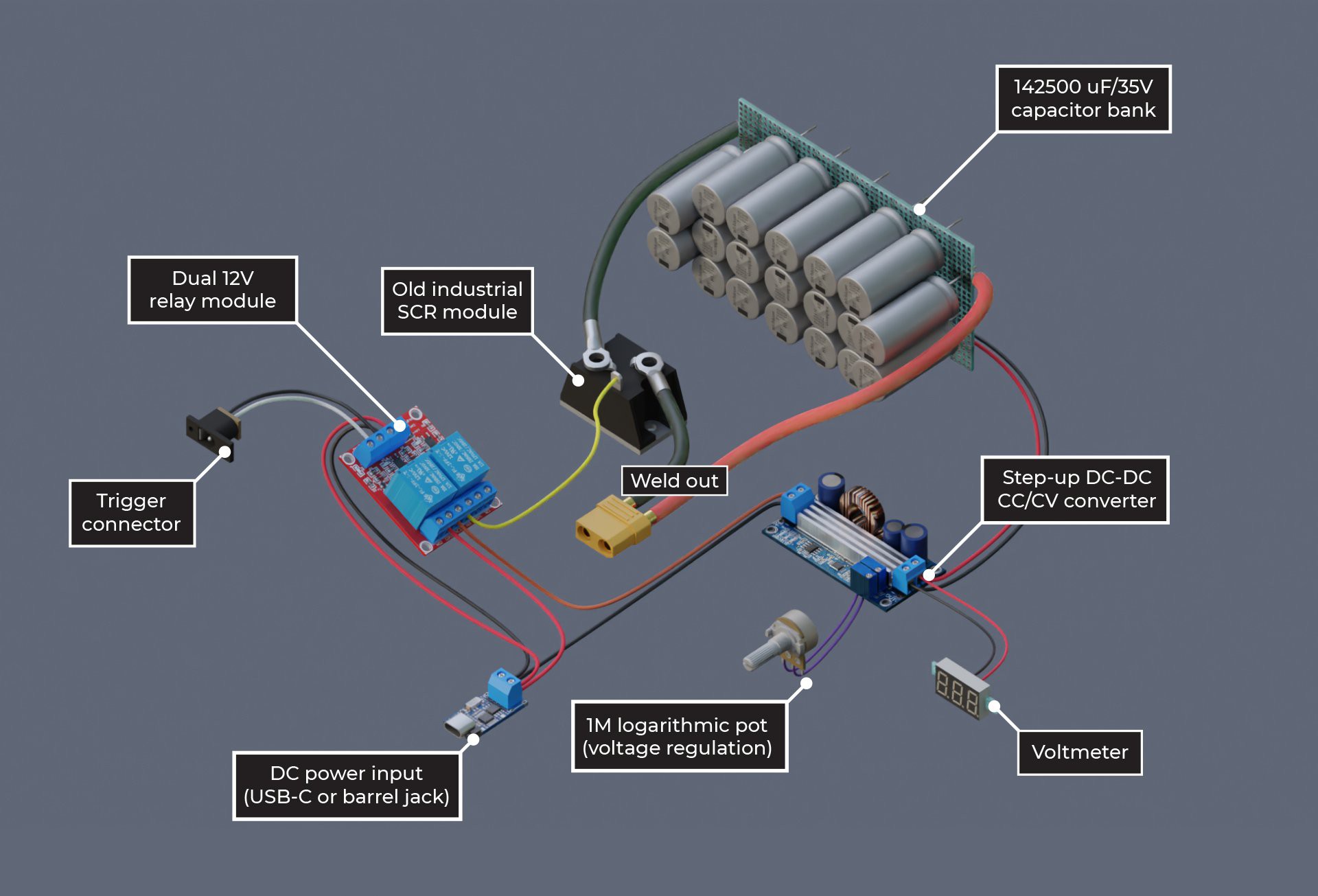
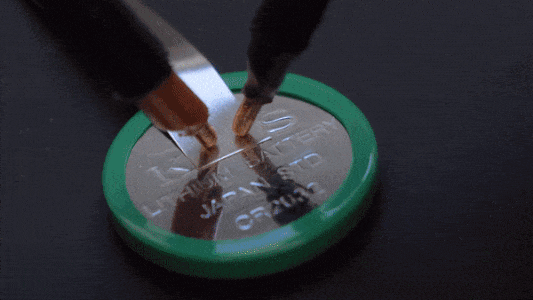
The challenge
1. I wanted this spot welder to be relatively safe to use and safe to store. Other spot welders often use car batteries, microwave oven transformers, high-current li-po battery packs or supercapacitors as power source. All of these things seemed to be very powerful and somehow scary to me, so I decided to use an capacitor bank made of regular electrolytic capacitors. These capacitors can store enough energy to make a spot weld, but not much more than that, and there is less of an risk of something bad happening in case of a short circuit.
2. I wanted this device to be fairly easy to build and avoid the need to use custom PCB. Therefore I created it in a modular manned, and chose to use an old industrial SCR module to switch the welding current, off-the-shelf relay module with slight modifications to time the pulse triggering and charging right, step-up converter module with potentiometer added to control the pulse energy and USB-C PD trigger module (optional) to allow powering the welder with powerbanks.
3. No microcontrollers: a button, a panel voltmeter, a potentiometer and a relay module with timing capacitors should be enough. Might help a bit in times of silicon shortage.
4. I wanted it to be compact. I made a custom 3D printed panel and packed everything tightly, but in a rather tidy manner into a plastic case. I didn't want to use a bulky footswitch, therefore the triggering button is placed right on the welding electrode, easily pressed with a finger.
What to do next
At the current stage, this spot welder uses mostly off-the-shelf modules and does not use a custom PCB. This is exactly what I aimed for and probably the most cost effective way to build this device. However, an ability to build it from scratch would also be nice, because it would allow a greater degree of customization of the device, and possibly making it even smaller. Therefore I am in the process of creating a schematic of this spot welder using discrete components to replace the relay module and step-up converter board.
Initial tests already have shown that this welder is capable of creating usable welds of nickel stripes, but I need to do more tests with various voltages and strips of different thickness.
Currently this spot welder uses automotive grade Nichicon capacitors. It would be a good idea to check the feasibility of using cheaper capacitors, and test if it's better to use higher voltage ratings, or higher capacity.
After a lot of trial and error with my own version using over 370mF of capacitance (similar setup to Lynneandpeter4947) I can't recommend building this setup. The SCR module simply doesn't provide enough control to the pulse duration and strength, compared to FET control systems. Maybe if you happen to have a large capacitor bank on hand, otherwise I've spent ~$70 on this project and for a bit more I could have gotten a pre built more reliable super capacitor welder. Thanks "Wojciech "adalbert" J" for the guide however, it's well made!