Objectives:
• To provide an open source control system for farm robots on small farms.
Solutions:
• After many iterations, we decided to make most of the circuits in the control system user configurable, rather than having too many inflexible PCB traces on the PCBs. This has the added advantage that prototyping is easier and faster as otherwise one wrongly routed PCB trace could ruin the whole board. The main MCU is the largest STM Nucleo we could find, with 144 pins, the NUCLEO-H723ZG, and is fully laden with masses of features, including the ability to run at least 3 quadrature encoders (there's probably more available).
• Keep the components as modular as possible so, for example, we use the whole Nucleo plug in board without attempting to solder STM chips on our own boards.
• The PCBs are stackable, so more NUCLEO-H723ZG modules can be added, for example. The motor controllers are on their own separate PCBs, which are also stackable.
Main Features of Control System:
• Control at least 3 DC motors / linear actuators with in-built quadrature encoders for positioning simultaneously.
• Switch at least 16 40A automotive relays for fuel pump, starter motor, glow plugs, hydraulic cylinder solenoids etc.
• Monitor at least 4 high ampage channels to provide 'digital fuses' and protect motors etc from becoming overloaded.
• Provide at least 10 conventional fuses for motors etc.
• Four x 16 bit Resistor divider circuits for sensing battery voltage, for example.
• Eight boolean Resistor divider circuits for sensing 12V positioning induction sensors, for example.
• Each of the above modules are stackable so, for example, there could be 8 or even 12 digital fuses.
• Cm level GPS.
• 4G modem.
Build Itinerary:
Stage 1:
• Make the steering and the throttle radio controlled using the onboard quadrature encoders in the motor and linear actuator in combination with inductive sensors to provide 'homing' locations at the mid point of the steering and the neutral position of the throttle. Since the machine is hydro-static, the throttle moves seamlessly from reverse to forward with a neutral position somewhere in the middle for 'stop' - trying to operate normal manual gears would be much more challenging!
Stage 2:
• Build up a super structure for protecting the internals from the weather and provide mounting points for the various antennae required.
Stage 3:
• Design and build an 'implement' to be positioned on the tractor's 3 point hitch which will have both x and y axis cultivation. The implement probably needs to be shrouded from external sun light to prevent strong shadows interfering with cameras.
Stage 4:
• Add cameras and extra control system for crop position detection to enable y axis cultivation.
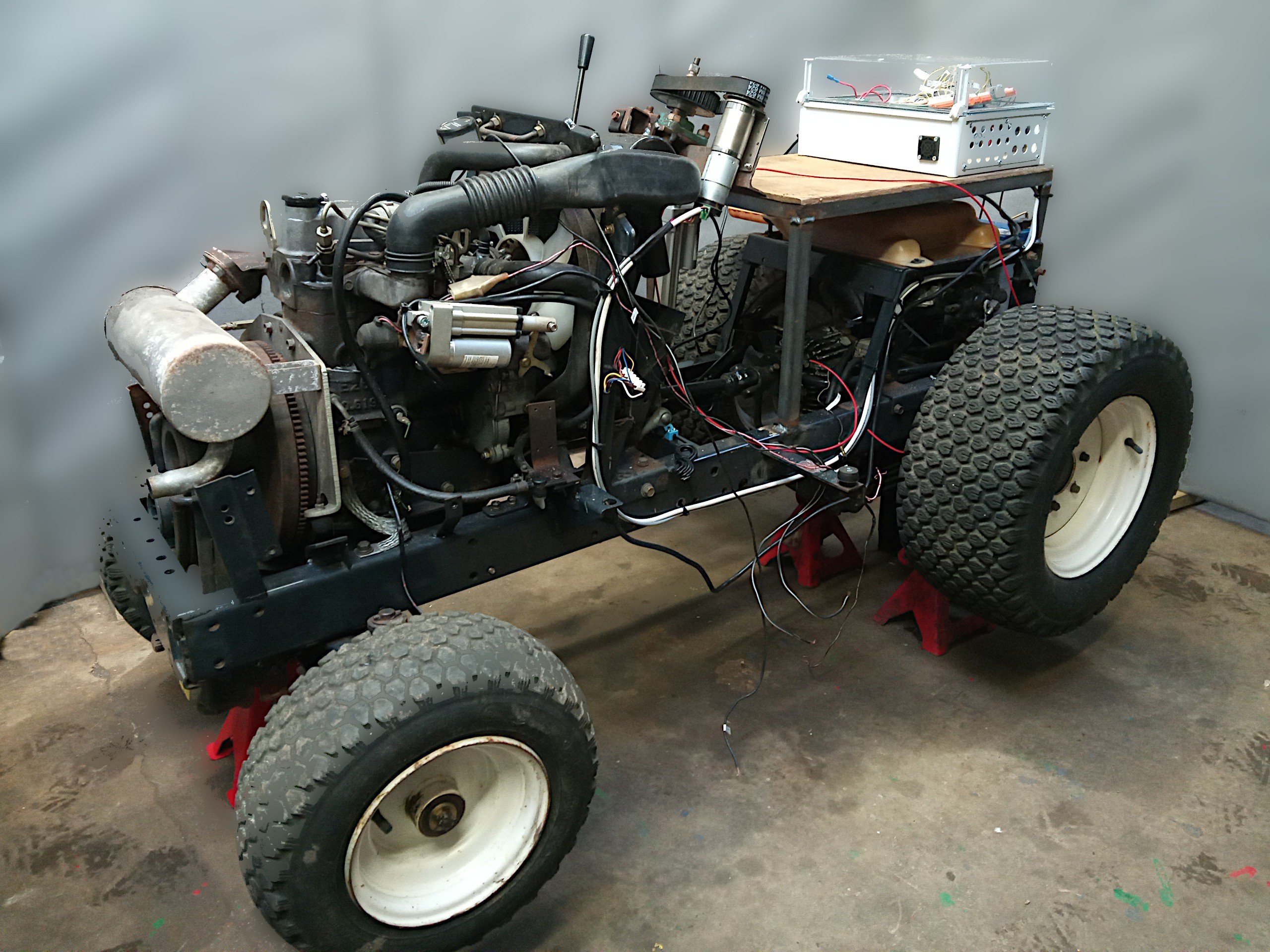