RR1 is a 3D-printed DIY desktop robotic arm. The overall design follows the idea of being able to produce more of these robots so that multi-robot coordination on the desktop is possible, obtaining a small scale Industry 4.0 on the table. RR1 features 6 degrees of freedom plus one degree of freedom for gripper altogether mimicking standard industrial robots but packed in small size. The robot features closed loop control with rotary encoders attached to each joint. RR1 is powered by 7 stepper motors (6 for axes and 1 for the gripper) that transfer torque to joints via 3D-printed split-ring planetary gearbox reducers. The revision 2 has many improvements against the revision 1 (the black robot) such as PCCF gears and encoders outside joints.
To enable full reproducibility, we provide everything as open-source including source CAD files (FreeCAD) here: https://github.com/surynek/RR1/tree/main/rev.2
My collaborator Ján Chudý also made ROS-based control for RR1 and visualization of its digital twin in RVis and Unity, code here (repositories starting rr1_... and ros2-...): https://github.com/EnviloN?tab=repositories The software enables multi-robot simulation with multiple RR1s.
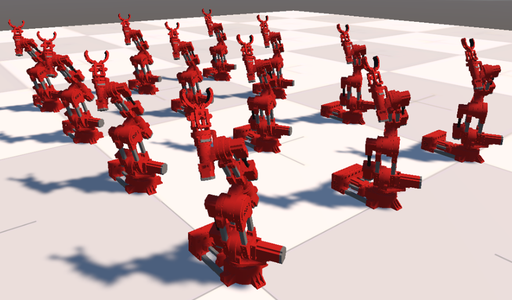
Here is a more detailed summary of the most important improvements that RR1 rev.2 brings:
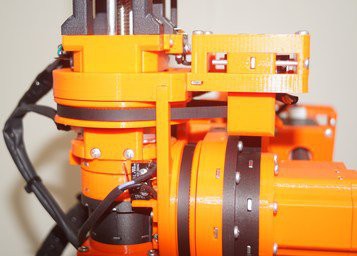
(1) The encoders for the individual joints are no longer on the shafts of the stepper motors, but directly on the joints, from which the torque is transmitted to the encoder by a belt (the GT2 6mm standard is used). From this change, we expect better sensitivity and the eventual possibility to compensate for the deflection within the arm. This change meant probably the biggest redesign, especially for the base turret, it was a challenge. But the overall design based on aluminum extrusions helped a lot, on which the encoder can be fixed and the belt can be easily tensioned by changing the position on the extrusion.
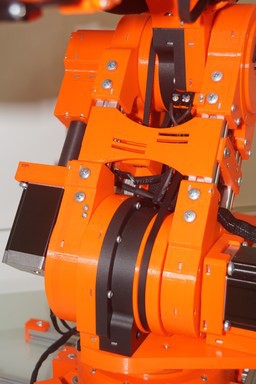
(2) Polycarbonate with carbon fiber (PCCF) is used instead of PETG for planetary gears and ring gears (the dark grey parts on the joints and everything inside is made of polycarbonate with carbon fiber). In rev.1 it was shown that PETG gears can deform or even break after intensive operation with loads (as I show in the video here). Polycarbonate with carbon fiber proved to be much better, it is a hard material, it feels like a stone, and also greatly reduced the backlash in the planetary gearboxes.
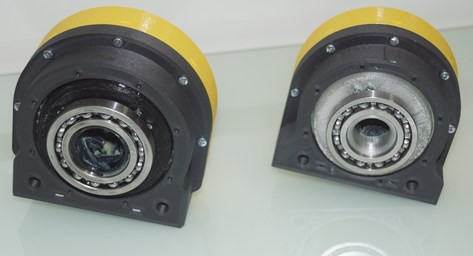
The video below shows how to calculate the reduction ratio of the split ring planetary gear box. It provides very deep insight in how this type of gearbox works. I recommend to watch the video carefully and calculate in sync with my commentary.
(3) Rev.2 uses the same type of split ring planetary gearboxes as rev.1, but they have larger ring gear diameters compared to rev.1, which greatly improves torque. New gears has larger teeth that mesh together better. Additional bearings are also used to improve the stability of the joints. The reduction ratio for large gearbox in the shoulder joint is approximately 1:40 which together with big Nema 23 motor (112mm in length) provides enough torque to lift the arm.
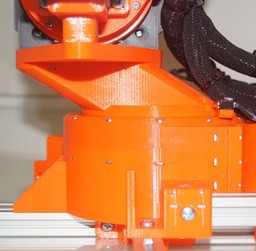
(4) The overall kinematic aspect was changed for RR1 rev.2. The arm has a base turret shifted a little forward, which improves the working space of the robot. The elbow link is further away from the elbow joint, which again improves the robot's dexterity and its working space. But mainly thanks to this, the robot can be folded into a compact form which makes it possible to put the robot in a standard large suitcase.
(5) The wrist has been completely redesigned, specifically the gripper is now attached both to the gearbox and also to another additional bearing that surrounds the motor of the gripper. This design greatly reduced the deflection of the gripper. The gripper itself has been redesigned. Compared to the rigid jaws in rev.1, rev.2 has jaws consisting of two links, which allows...
Read more »