That's where I'm currently heading ( My 2019 ) :
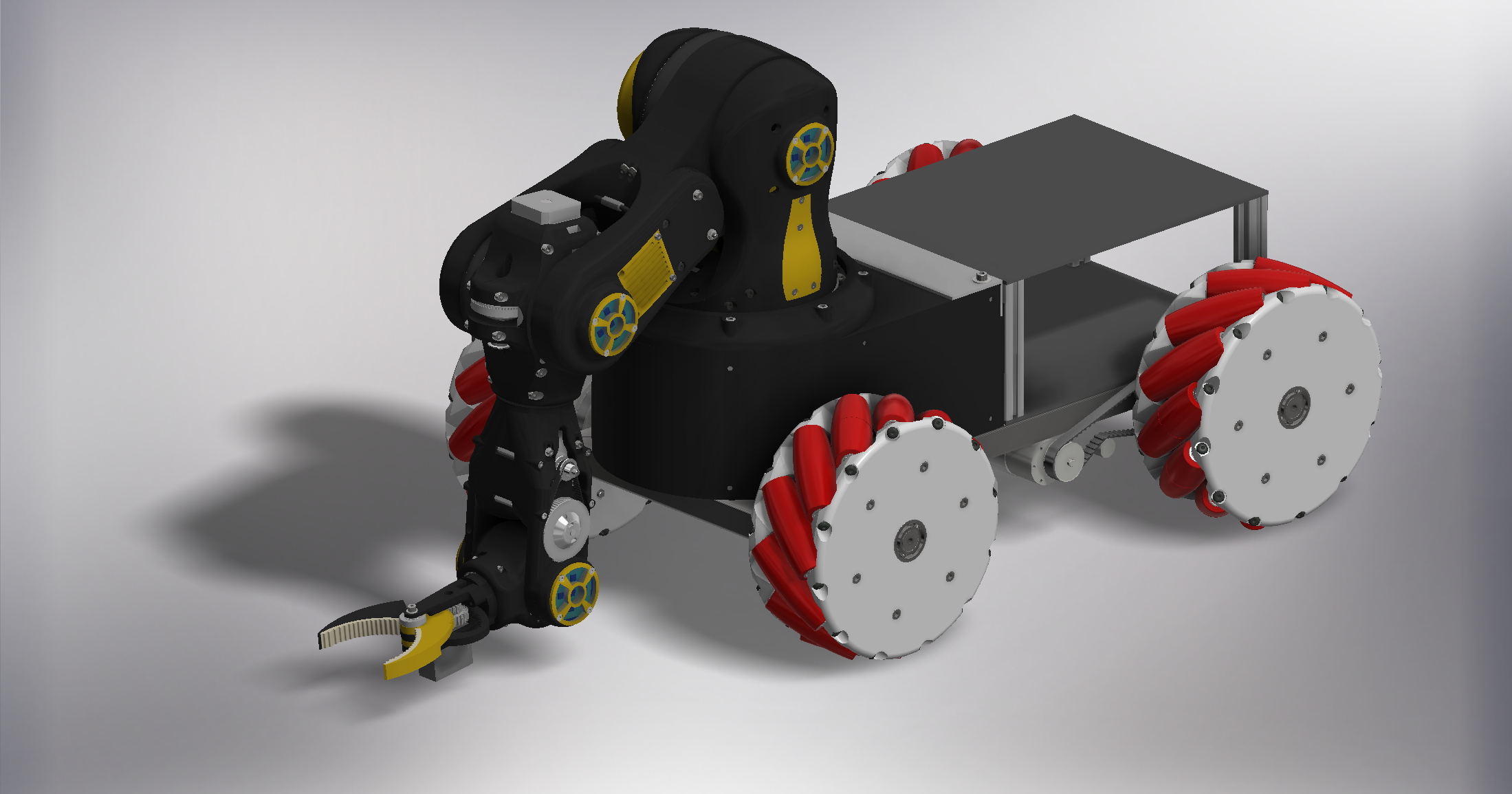
The four robots I build since this project started.
Version 4 now nearly done and in testing.
Take a look at the Gripper I designed for my Robots:
Version 4 is now nearly complete:
I also started uploading the files on github:
https://github.com/4ndreas/BetaBots-Robot-Arm-Project
And a components list for version 4:
Your robot arm seems to work well enough to be able to repair itself. At least it should already be possible to teleoperate one or two arms to command a computer-controlled repair mission. I imagine it's possible to design a simple process which replaces a damaged timing belt, all within a reasonable amount of time and with minimal human input. Thanks for sharing the source files!