Most modern robots fall into one of two categories: professional grade or hobbyist level. Professional robots are generally built for a single purpose (e.g. industrial manufacturing, vacuuming, security) and cannot be easily adapted for other applications. Hobbyist level robots are often built for flexibility and extensibility but the hardware required to make them robust and reliable is expensive.
Hoverbot bridges the gap between the two categories by repurposing existing cheap consumer products and leveraging modern software tools. The result is a moderately priced (~$250), extensible, functional robot.
This project is broken down into a collection of modules that can be either used in combination to create your own Hoverbot or used individually as components in other projects. Hoverbot modules:
- Reprogramming hoverboards for robots - Update the hoverboard motor controller firmware to control the wheels via a serial interface.
- Reverse engineering automotive backup sensors - Read the backup sensor data for use as generic obstacle detectors.
- Assembling Hoverbot - Combine a hoverboard, backup sensors, an IKEA table, some LEDs, a web camera, and a Raspberry Pi into a mobile robot!
- Programming Hoverbot - Get the code and write some Javascript to program a custom robot.
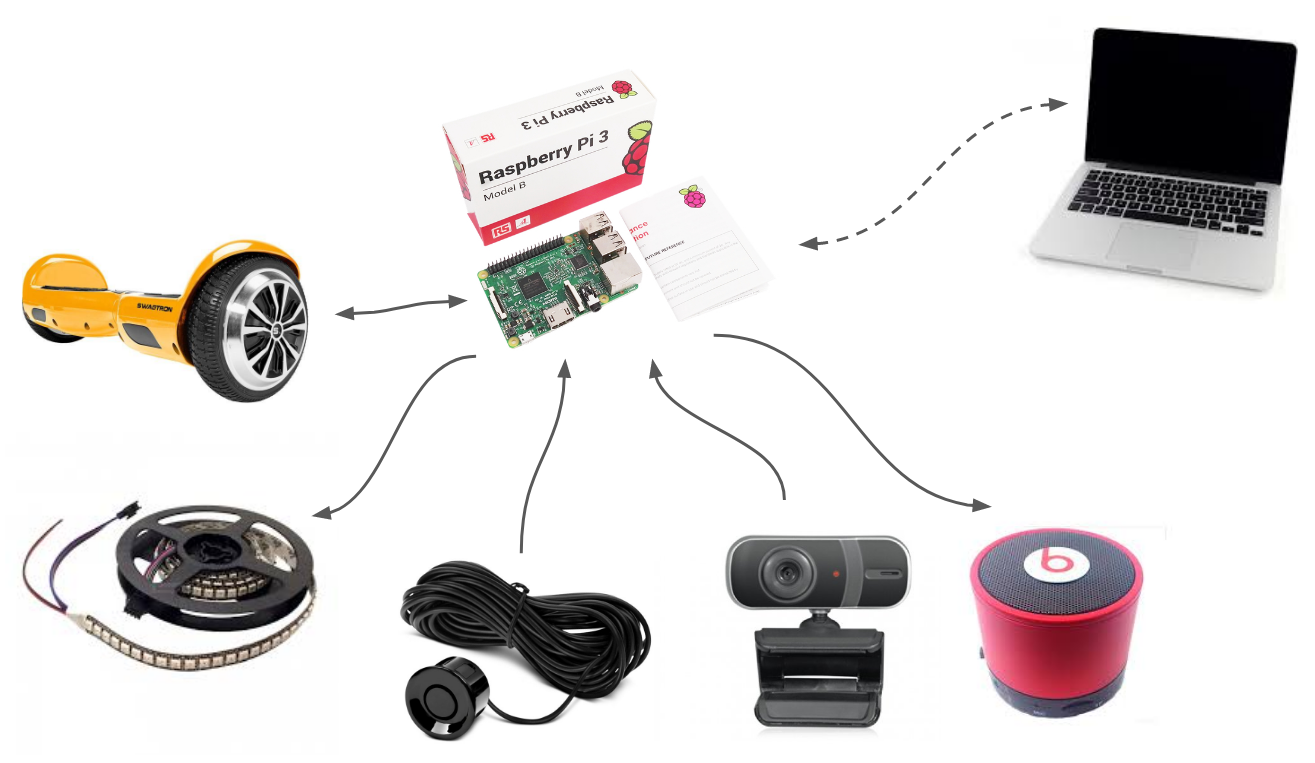
Hello !!!
After compiling .bin calibrate works
Calibration soft bes does not work
After uploading .bin, the board turns on after 1 second
there is a problem with
/* IWDG init function */
static void MX_IWDG_Init(void)
{
__HAL_RCC_WWDG_CLK_ENABLE();
hiwdg.Instance = IWDG;
hiwdg.Init.Prescaler = IWDG_PRESCALER_8;
hiwdg.Init.Reload = 4095;
if (HAL_IWDG_Init(&hiwdg) != HAL_OK)
{
error_handler();
}
HAL_IWDG_Start(&hiwdg);