This is a continuation of the journey started with #Tote to create an affordable walking desktop robot.
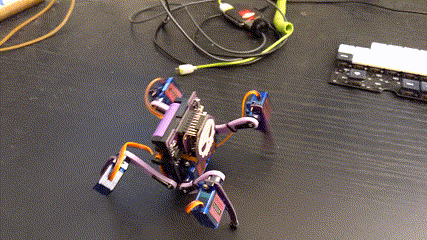
What is this?
It's a four-legged walking robot that fits on your desk, can be programmed with an USB cable without installing any special software on your computer, can be built on a budget of less than $30, and that can be easily expanded or modified, to try out new ideas. Those are the basic requirements I have set myself for this. But why?
Why am I doing this?
Because I think that the details about how such robots are able to walk, without crawling or dragging on the floor, are very interesting, and that making a physical robot work is the best possible way of learning about it—fun and rewarding. There is a big hurdle in getting into this—most of the robots you could get are either super-expensive or simple toys with hard-wired gaits. There are now some reasonable kits out there, such as those robots made by Petoi, but I think I can still do better than that in terms of both affordability and removing other barriers.
Why is this hard?
Building a walking quadruped is surprisingly easy—once you know how. You literally just need any microcontroller development board, battery, a bunch of servos, ice cream sticks and hot glue. A few hours of work, and a few weeks of banging your head against a wall while trying to get it all to work, and you are done. That's the easy part.
The challenging part is designing and documenting it all so that it can be repeated or modified and expanded, without wasting time, and with as little frustration as possible, and on a budget. This means I don't only need to get it to work, I need to think about the best ways of getting it to work, and then about the best ways of explaining them.
When will it be finished?
Probably never. That doesn't mean it won't be usable. I hope to get it to a point where it can be built by others as soon as possible. But it's one of those projects that are never completely finished, because the context in which they work keeps changing. New parts become available, such as new microcontrollers, sensors or even servos and batteries. Others become obsolete or otherwise hard to obtain. New fabrication techniques, such as laser-cutting or 3D-printing become feasible for an average hobbyist. There might even be new materials on the horizon! And the fastest changes are in the software tools available—a few years ago the only ways you could program a microcontroller was assembly, or maybe, if you were lucky, some limited version of C. Today we have Python code running on them in real time, with a lot of ready libraries, and new capabilities appear every month. I probably won't be able to incorporate it all in the design, but I fully intend to update it as new possibilities emerge.
Servo cable connectors are available at Pololu.
https://www.pololu.com/product/1924
Pololu also has a nice crimping tool.
https://www.pololu.com/product/1928
I haven't tried them yet. Ordered today. I expect them to work better than ribbon cable connectors.