The general idea was there would be a curved thing sitting under the speaker, but a solid hunk of PLA with infill was too boring. The part would be iterated to get the angle & size right, so any artwork had to be procedural.
The concept resembles this $30 brick.
https://www.amazon.com/dp/B002ATK2OS/
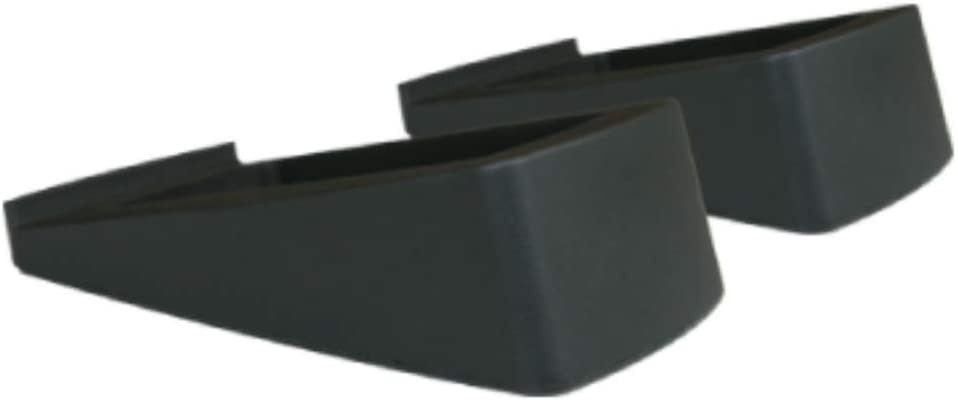
But it needs more rear support to prevent the speaker from falling backward.
The lion kingdom had a sick fascination with the 3D printed cast in Stowaway, not because it wasn't ridiculous & didn't exist just to sell Makerbots, but because of the design. The lion kingdom figured it was painstakingly modeled by paw since it didn't fit the actor & they couldn't iterate the design. The sponge was a creative way to add artistic value to a piece which would normally be made of infill. It would be the ultimate speaker stand, but modeling was difficult.
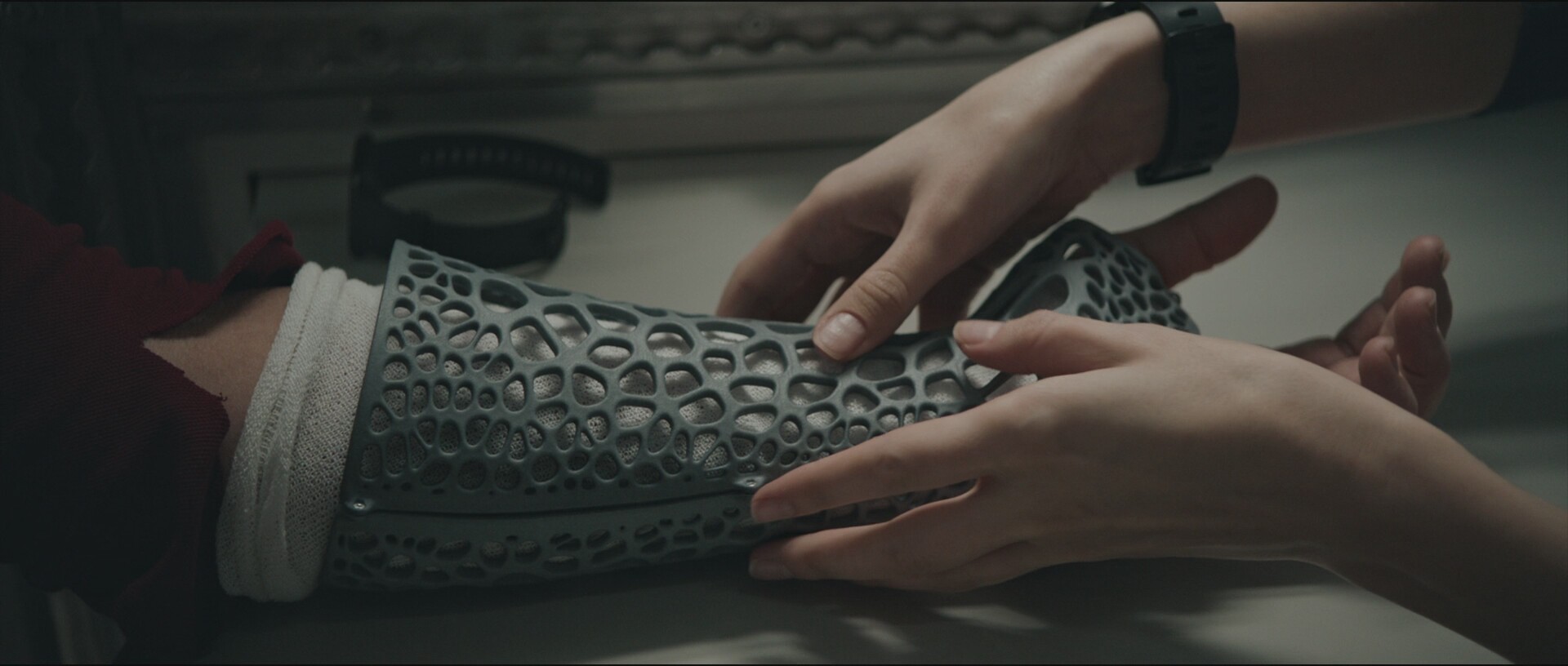
It turns out there are 3D printed casts like that. They're printed without supports & they're procedurally generated. The journey begins with the voronoi algorithm.
Wherever there have been 3D printed sponges, they were generated by the voronoi algorithm.
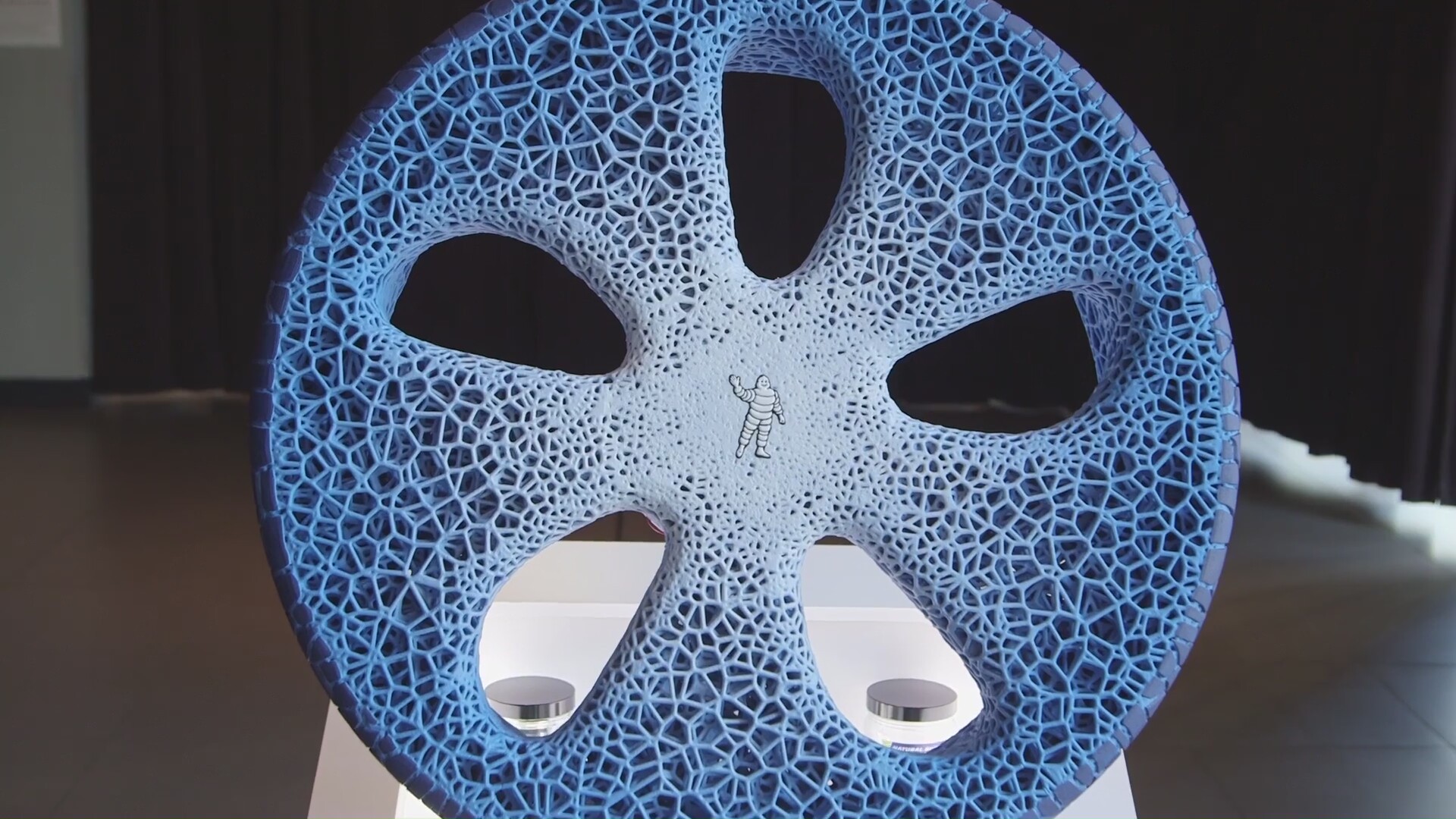
The voronoi algorithm gives us structures which can be printed without supports & which are more appealing than infill.
This page describes a process using mesh mixer, then rhino3D, then Grasshopper.
http://www.piper3dp.com/blogs/how-to-design-custom-3d-printable-casts-for-broken-bones/
The idea is to get the model in a surface form. Grasshopper converts the surface directly to the exact movie structure, using the voronoi algorithm. Most of the work seems to be converting a mesh to a nurb for Grasshopper to operate on.
There's a process using Blender
https://www.youtube.com/watch?v=NMpGmFNXSKI
The general idea is to subdivide, then decimate, which recombines the new subdivisions with randomness. The random subdivisions are the voronoi pattern. Finally, there's a wireframe modifier which converts the wireframe into new solids. Then the new solids are subdivided again to get smooth holes. Helas, this works better on a sphere than a plane.
The original plan of Signature speaker stand was for a curved object to sit behind the speaker, but a solid piece of PLA with infill was too boring. Any artwork has to be procedural because the part would be iterated to get the angle and size just right. The goal is to get the model onto a flat surface. I'm patiently waiting for it and while waiting, you should check angry birds star wars free download | emulatorpc.
https://games.lol/junes-journey-hidden-objects/