FAQ:
-
what's the difference from Klipper
PandaPi: use RPi to control 3D printer directly,except the temperature control which is just to maintain the temperature.
Klipper: uses a RPi to parse G-code,map out curves,set accelerations,and then send the motor command to the MCU via uart.
-
Why is there a mcu?
RPi has not enough GPIO pin for handle all the motors,hotend,bed,endstop,LCD,auto bed level,run out sensor.
-
how do this assure the real time control?
about the real-time, I did a test . it is not real time actually,but we guarantee motor coordination. and the RPi is more than fast enough that it is not a problem.and I test it with pi4 the cpu speed is quickly than pi3! BTW I test it with all the function like camera octoprint,they are used a lot of RAM but little CPU.
- there is a great improve to the pandapi software for high speed printing with high pressure cpu loaded. here is the a test.this is the output signal of the one raspberryPI'GPIO,and displayed by the oscilloscope.
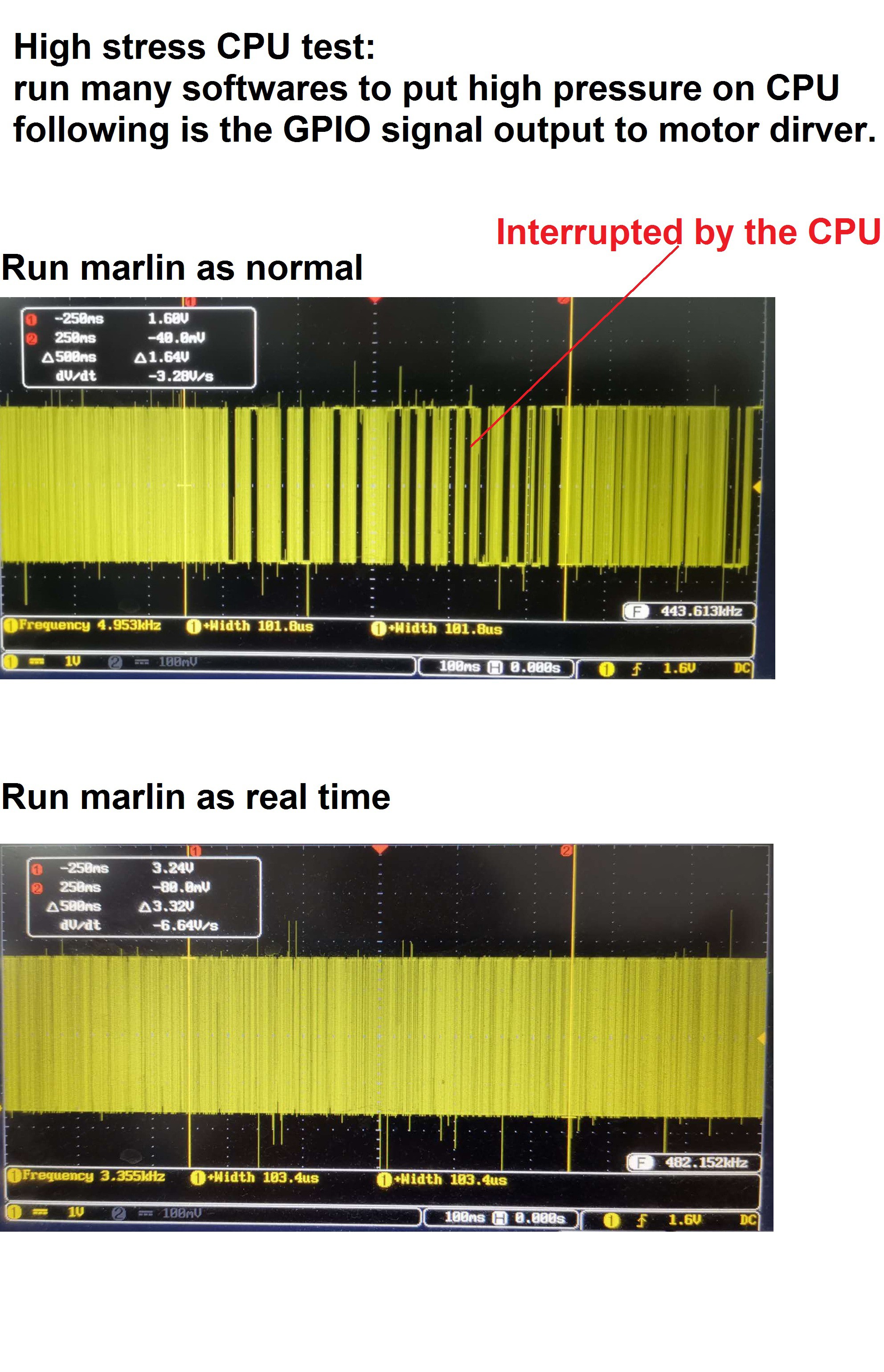
No servo ports??