(update: counterweight delete)
CNC Kitchen video - thanks Stefan!
Even though the Minamil is minimalistic, the part quality Paul can achieve with it blew me away!
Hackaday.com writeup - thanks Bryan Cockfield!
Hackaday Podcast 136 - thank you @Mike Szczys & @Elliot Williams for the kind comments!
"I'm frankly shocked by the quality of the parts coming out of this" 11:54
Hackaday Prize 2021 finalist! - thank you judges!
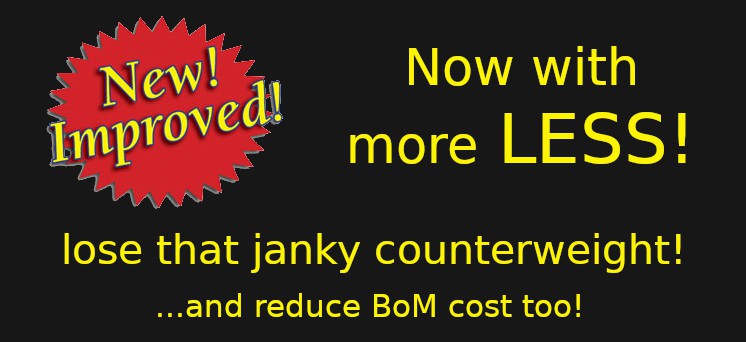
(mocking the style of over-hyped package labeling, in case that got lost in translation)
Many of the photos and videos here show a big counterweight rigged off the side of the little machine. But nevermind. That's now "legacy product". Because the new Z axis does better with less. Yay for maximizing minimality!
This little CNC mill works well enough to produce an eye-candy demo video:
(that's a "new" (June 2022) demo vid; here's the first eye candy demo)
...and mill fine-pitch circuit board traces:
What little CNC mill?
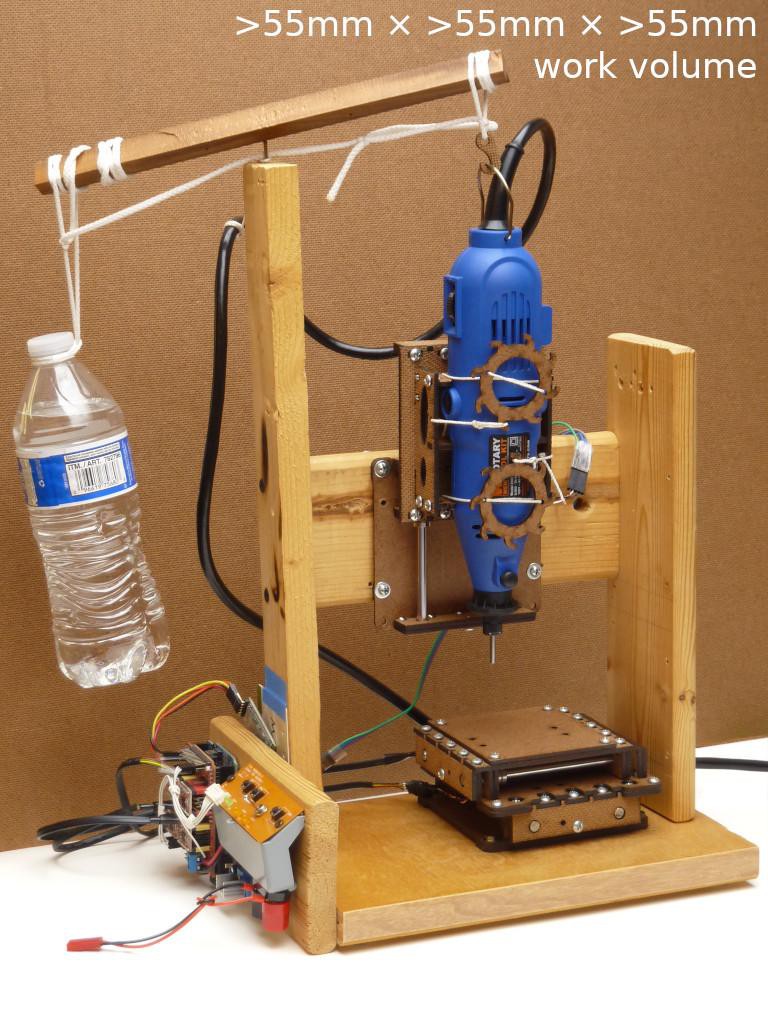
Minamil: a minimal CNC mill
First there was #CDCNC, a highly-constrained just-barely-functional one-off toy built by improvisation with found junk and simple tools.
Here I'm developing an idea that came from thinking about whether or not there is any space between a dumb stunt like CDCNC and a commercially (i.e. efficiently) produced entry level CNC mill/router. Early results seem encouraging.
In contrast to CDCNC, this is about reproducibility from a simple BoM, economical access to laser cutting, and instructions for building your own sub-mini CNC mill.
Next there may be #"Desk Accessory" CNC Milling Machine. For progress in that direction, with not much more effort in the frame+enclosure department:
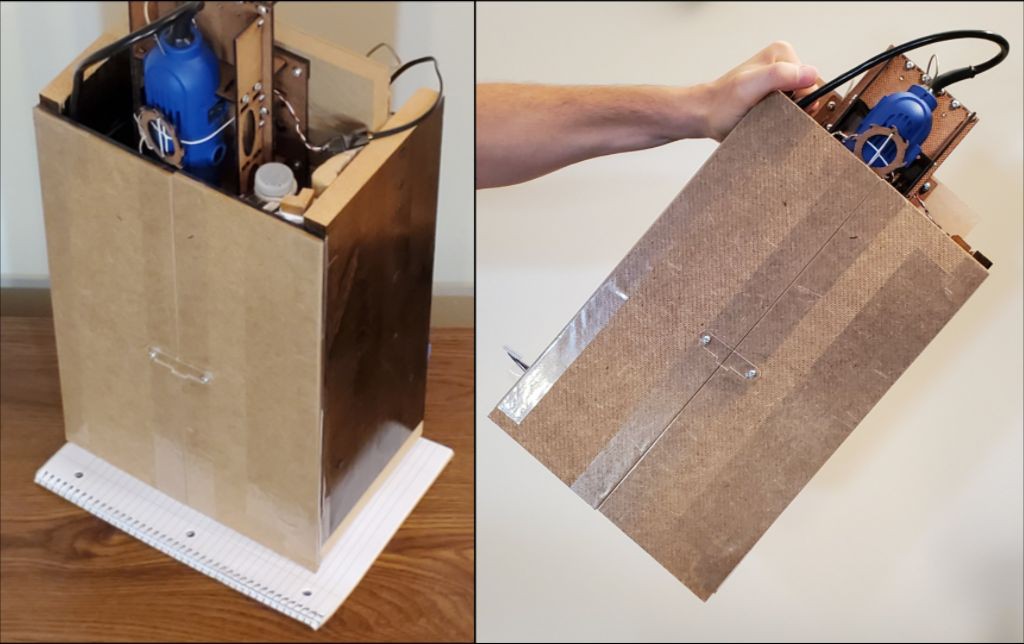
(different Z axis in those two pics - part of [what used to be but isn't anymore] the not-quite-so-minimal "and friends" part of the project title that I haven't written much about yet)
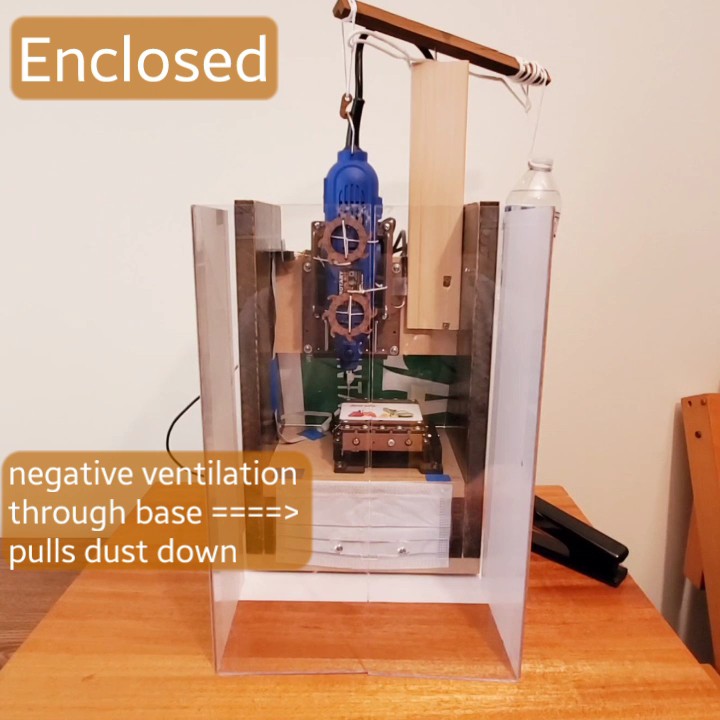
Telescoping axes allow the enclosure to fold up smaller when parked and expand for operation:
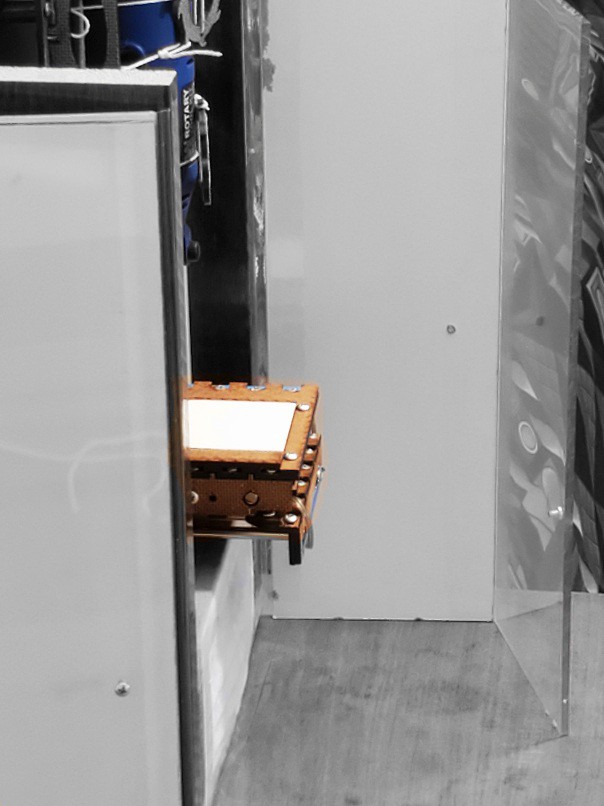
Selected Log Entries
- Build!
- Parts source / cost notes
- milling PCB (so... MCB?)
- milling aluminum
- material removal rate (MRR) in acrylic
- uh oh... unexpected trouble with self-locking leadscrews
- how it works (could use some updates re later learning)
- compact & convenient packaging
- building blocks: the slide sub-project
- trying intentional interference -- which has worked so far
- first assembly (the eye-candy video)
- first part
- first try with XY & Z
- HaDPrize 2021 Challenge 3: not selected 😞
- HaDPrize 2021 Challenge 5: selected 🙂
Hahah... The 'faux' ad, and I 'm thinking 'counterweight' ? And then I see the counterweight. Made me laugh, thank you.