THE BASIC .4MM NOZZLE PLA SETTINGS:
This makes very high quality parts, but takes forever.
nozzle: .4mm
layer height: .2mm
line width: .4mm
wall thickness: 1.2mm
top/bottom thickness: .8mm
ironing: off
infill: 25%
nozzle temperature: 230C Best layer adhesion is 230C
bed temperature: 60C on a buildtak FR4 bed. 50C on a buildtak magnetic bed.
speed: 50mm/s
wall speed: 25mm/s
top/bottom speed: 25mm/s
travel speed: 75mm/s Prevent crashing into lumps
initial layer speed: 20mm/s
retraction: 5mm
print cooling: OFF Better layer adhesion
support: touching buildplate
support overhang angle: 80deg
adhesion: skirt
Layer height must be a multiple of .04mm. Thicker layers print faster but make rougher diagonals. Layers over .32mm can't make diagonal overhangs at all .
Design parts with multiples of the layer height.
Design 45 degree angles instead of using support whenever possible.
Avoid brims & rafts at all costs. The bottom layer needs to press onto the bed to be flat.
Place parts in the center of the bed because this area tends to have more stable height.
Lions have never had any use for print cooling. It might be useful for artwork but it weakens layer adhesion & the fan has to be cleaned.
BED ADHESION:
The stock Ender 3 bed is a buildtak bed. It works at 60C. Increase temperature to increase adhesion. Decrease temperature to decrease adhesion.
For most models, the lion kingdom only heats the bed for the 1st layer. It retains most of its adhesion after cooling. Only difficult models with little contact with the bed need full time bed heating.
Lower the nozzle to press the filament down & increase adhesion. Raise the nozzle to decrease adhesion.
Any print bed, whether glass or plastic, must be kept free of skin oil. Washing it off with dishwashing soap greatly enhances adhesion. If the bed is clean, the nozzle can achieve adhesion with very little downward pressure.
Remove the bed, let it cool down, & bend it to remove the part. Use an xacto knife to remove the skirt & extra bits.
Ordinary glass provided no significant adhesion or improvement in leveling, but required a lot more heat. The trick with glass is it makes a smooth surface. There are specially treated glasses which might give better adhesion, for a price.
BED LEVELING:
Lions started out by using this file to coarsely level the bed:
https://cdn.hackaday.io/files/1764067547354304/CHEP_M0_bed_level.gcode
It's a modified version of https://www.thingiverse.com/thing:3235018
Clean excess filament from the nozzle before leveling. Heat the bed to the printing temperature before leveling by going to control->temperature->bed.
After much experience, lions switched to just going to prepare->auto home, then prepare->disable steppers, then manually sliding the nozzle around. Instead of sliding paper under the nozzle, lions just eyeballed the nozzle height. The nozzle height after auto home should be right on the bed. It doesn't raise it a layer height.
Bed leveling is manely affected by changing nozzles, slippage of the springs & X arm. The center of the bed is higher than the sides because it rocks around the center. Turn the eccentric nuts under the bed to reduce the rocking, but it can never be completely eliminated.
Once coarsely leveled, it only needs to be fine tuned while printing the skirt. Lions print 4 skirt lines. There's no need to print a test pattern.
AUTOMATED BED LEVELING
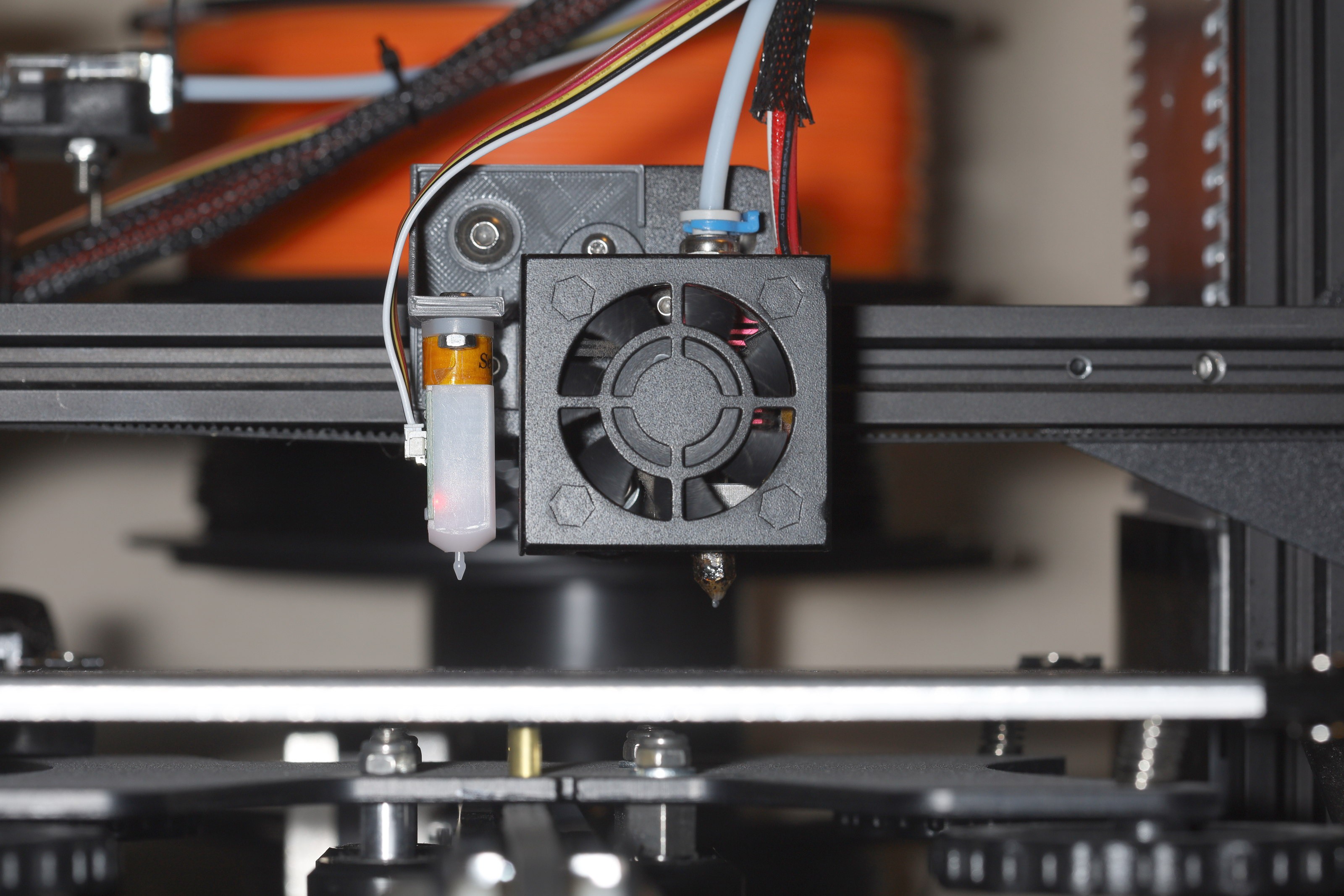
https://hackaday.io/project/176406/log/197418-auto-bed-leveling-with-the-3dtouch
Automated bed leveling is cheap enough to be considered essential...
Read more »
Someday maybe you'll win. For now, this is a somewhat convoluted mess of printing... Get a cricut and step away from the 3D printing.