We are aspiring mechatronic engineers, and for a school project, we were given the opportunity to create something of our choice. We decided to build a small hydraulic arm to deepen our understanding of hydraulics and linear motion systems.
The project features a fully custom-designed 3D-printed 4/3 rotary directional control valve using mg90s servo.
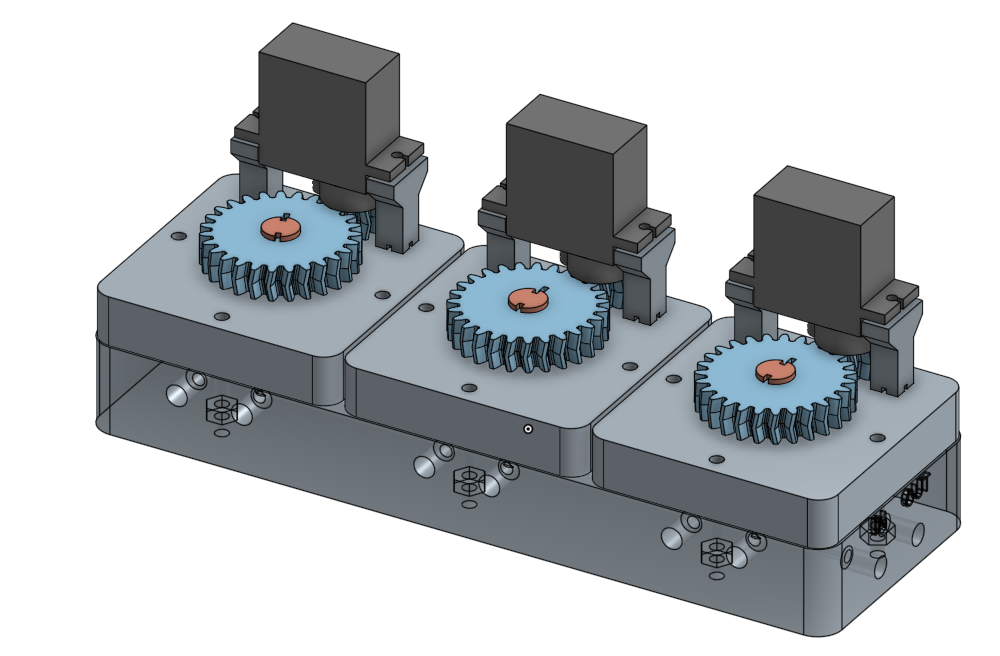
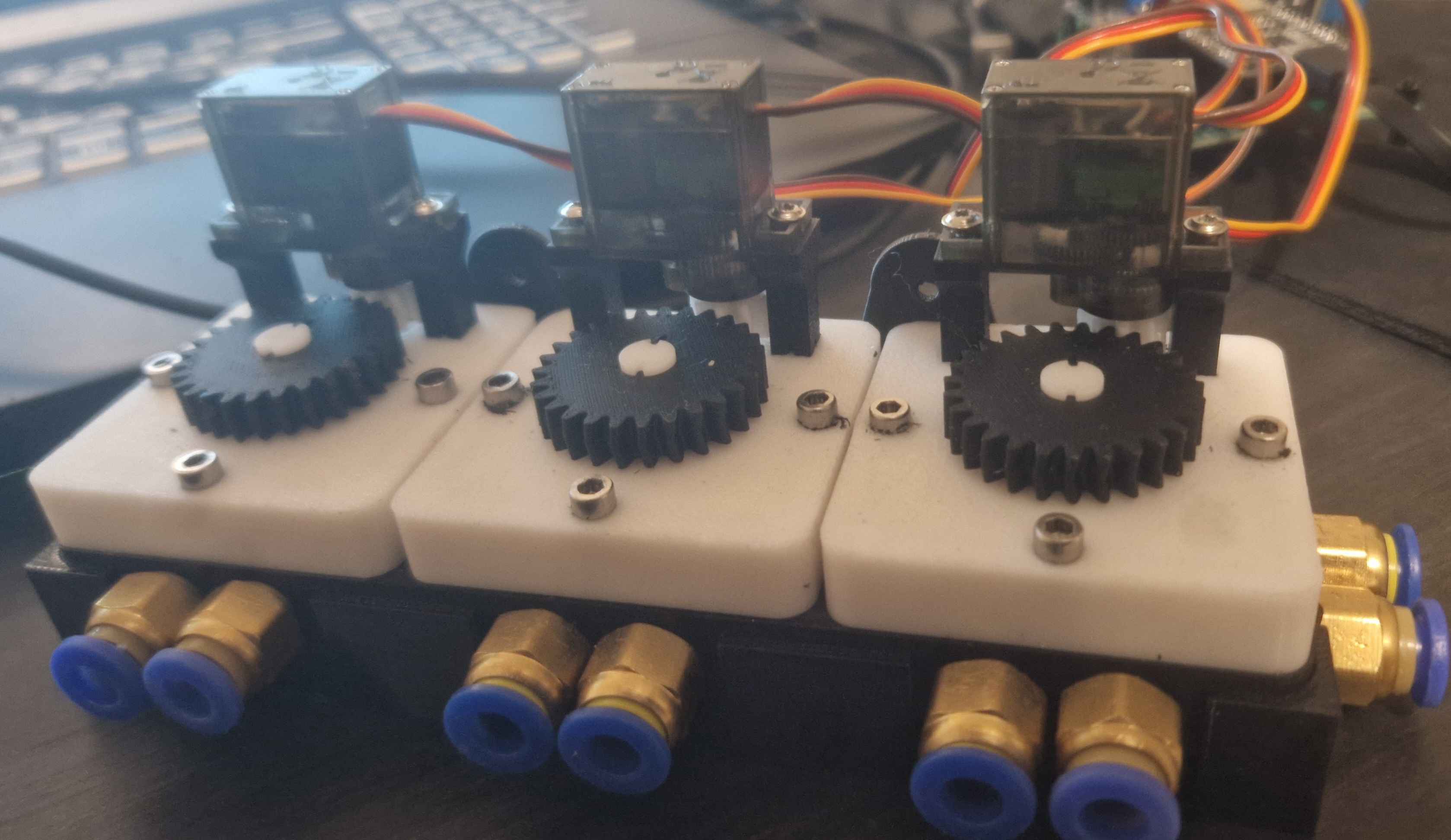
And a custom circuit with IoT control powered by an ESP32
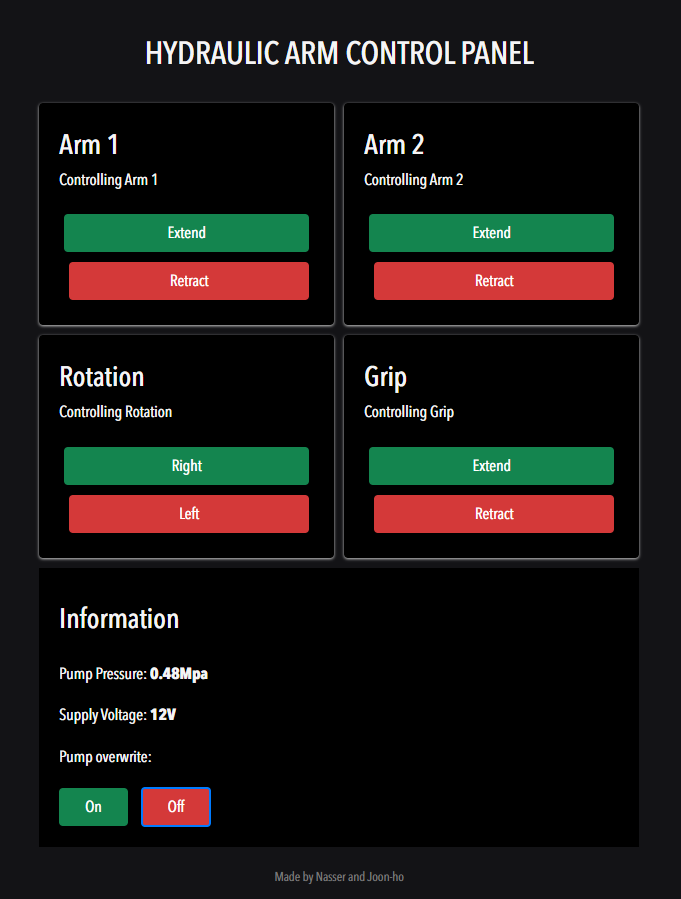