Motivation
The capability to fabricate solid-state devices is a foundational technology which has deeply transformed our lives, and is expected to become even more relevant with the advent of data-heavy applications and energy harvesting/storage. However, the fabrication processes used require enormous capital expense, which has only grown with time. As a result, the tools required to create a functioning solid-state device are out of reach for many researchers in the field, and the increasing degree of consolidation in manufacturing capacity is effectively hindering innovation.
Main Idea
The main hypothesis behind the machine is that the fundamental (although not sufficient)requirement to generate solid state devices is to place the right material in the right place. While this is currently done through the Planar process in one of it's several variations, one could in principle just use a completely 'bottom up' approach where the required material (be it an insulator, conductor, extrinsic or doped semiconductor, among many others) is deposited in the required place.
For example, let's consider a (cartoonish) Thin Film Transistor. A more serious description of it's fabrication can be found on resources such as 'The Art of Analog Layout' by Alan Hastings. In principle one just has to define the appropriate contacts, the active semiconductor region whose transport properties are modulated by the electric field, the gate insulator (usually a metal oxide) and the gate contact.
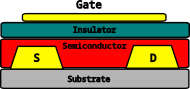
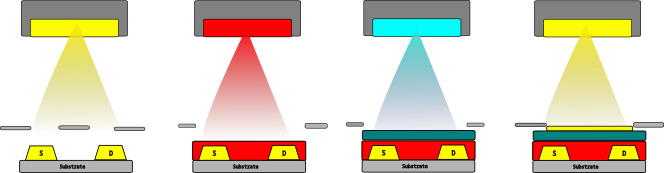
The approach used in this project is based on the combination of the following techniques:
Multi Material Pulsed Laser Deposition
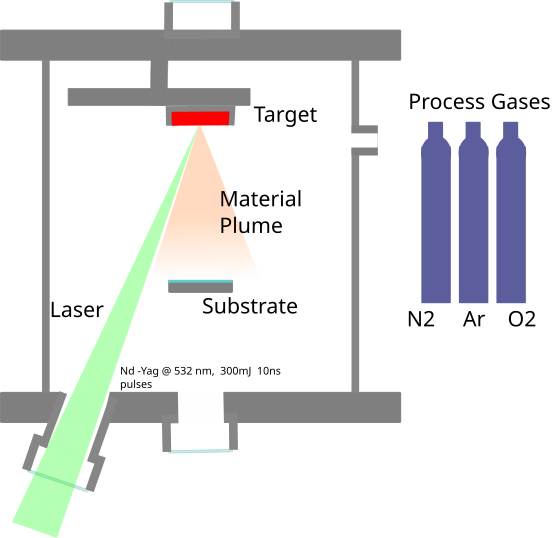
Pulsed Laser Deposition is a technique in which mass is transferred in a controlled atmosphere from a target to a substrate by means of irradiating the former with a high peak power pulse of light. The energy transferred induces out of equilibrium thermal processes in the target, resulting in the formation of a plasma 'plume' which has a stoichiometry closely matched to the target composition.
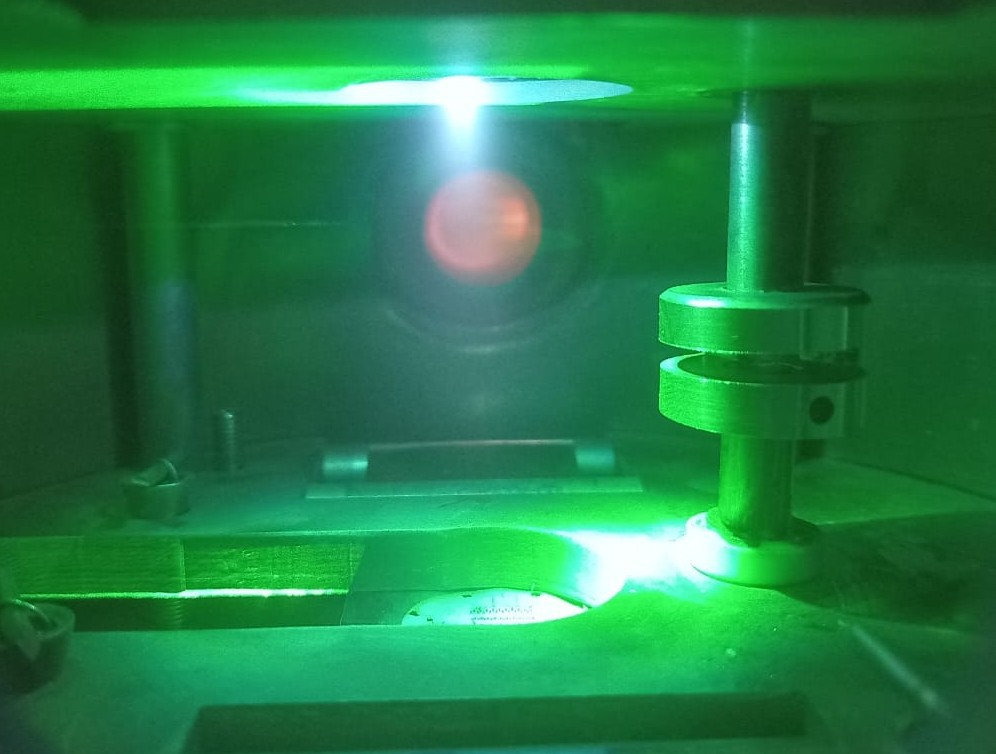
While it's not the technique of choice for industrial device fabrication (mainly due to film quality and complications associated with large area deposition, see this section), the ability to deposit a wide range of materials has made it the workhorse for many research regarding complex materials (oxides, nitrates, dichalcogenides, etc) and the applications of some interesting effects (ferroelectricity, superconductivity, …) that they show. An often overlooked characteristic of this technique is the ease of coupling of the energy over the target: one can control with exquisite precision the amount, rate, placement an timing of the energy transferred from the laser.
This simplicity allows a simple mechanical fixture to change the material being deposited:
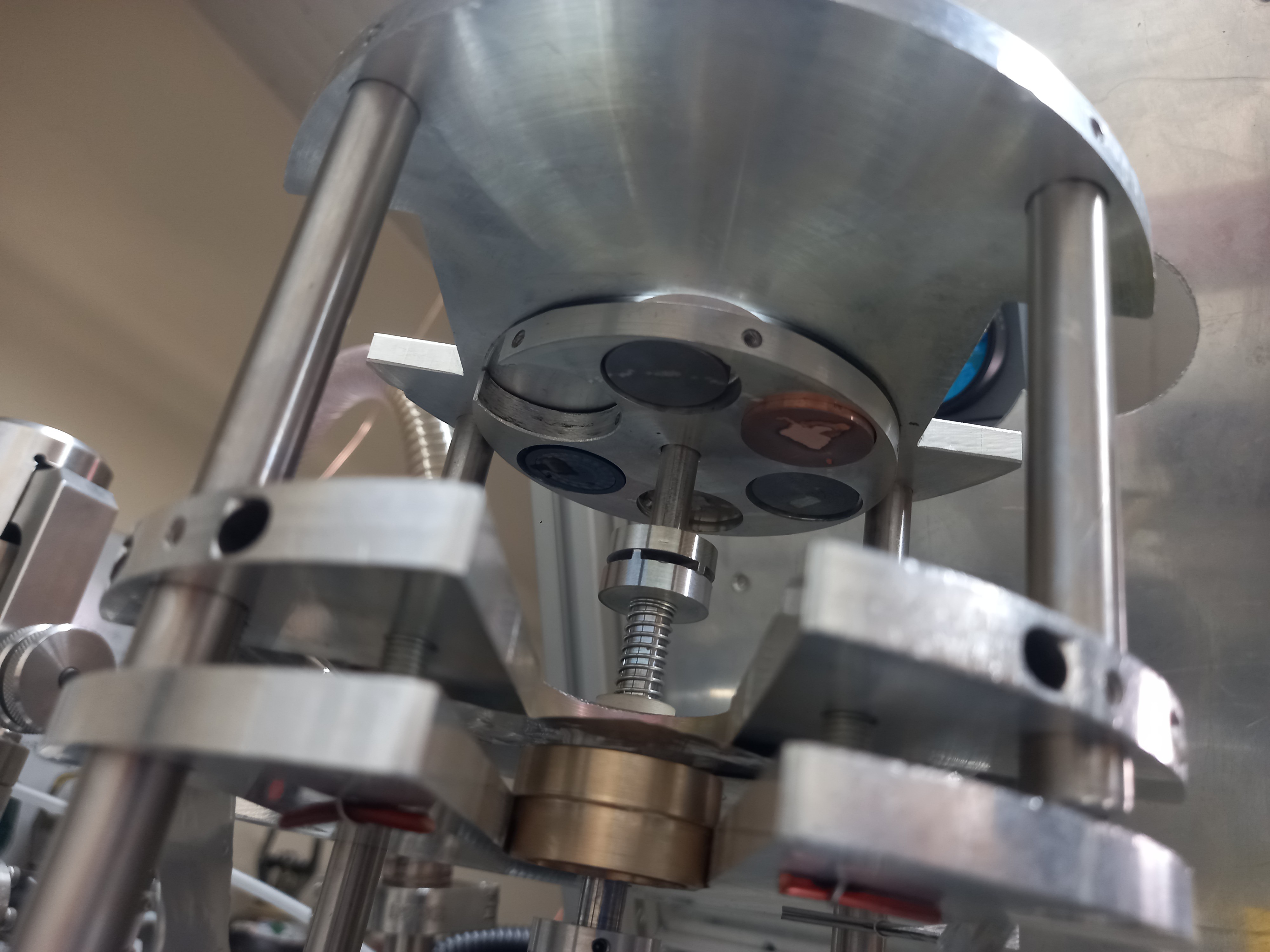
Then just a set of rotations allows oneself to greatly expand the kind of materials systems to be explored, from single materials to multilayers, alloys, (non)uniform doping, reactive deposition.
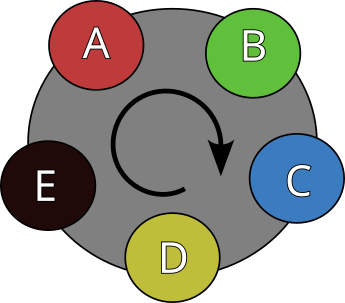

But this only allows the fabrication of thin films... a lithographic tool is needed in order to generate the patterns from which devices could be fabricated.
Shadow Mask Lithography
Also known as Stencil Lithography, it uses of a self-sustaining, usually solid mask with some defined apertures placed either in contact or some distance away from a substrate during a deposition process, which effectively allows the spatially selective transfer of material.

While this technique is seldom used in industry due to it’s practical resolution limitations, the spatial modulation of mass flow through an aperture is an inherently clean process which imposes very few limitations on the nature of the deposited species, as opposed to conventional...
Read more »
How are you going to dice the wafers and make wirebonds to a PCB or chip carrier?