SurgeyOS is a complete, integrated surgical robotics platform, which is configurable and modular.
The main structure has a base and a gantry which allows movement in 3D cartesian space of an arm base. The gantry moves with respect to the base (y-axis as shown on the onshape pictures below), the arm base moves with respect to the gantry in two axes (vertical z-axis and horizontal x-axis as shown on the onshape picture)
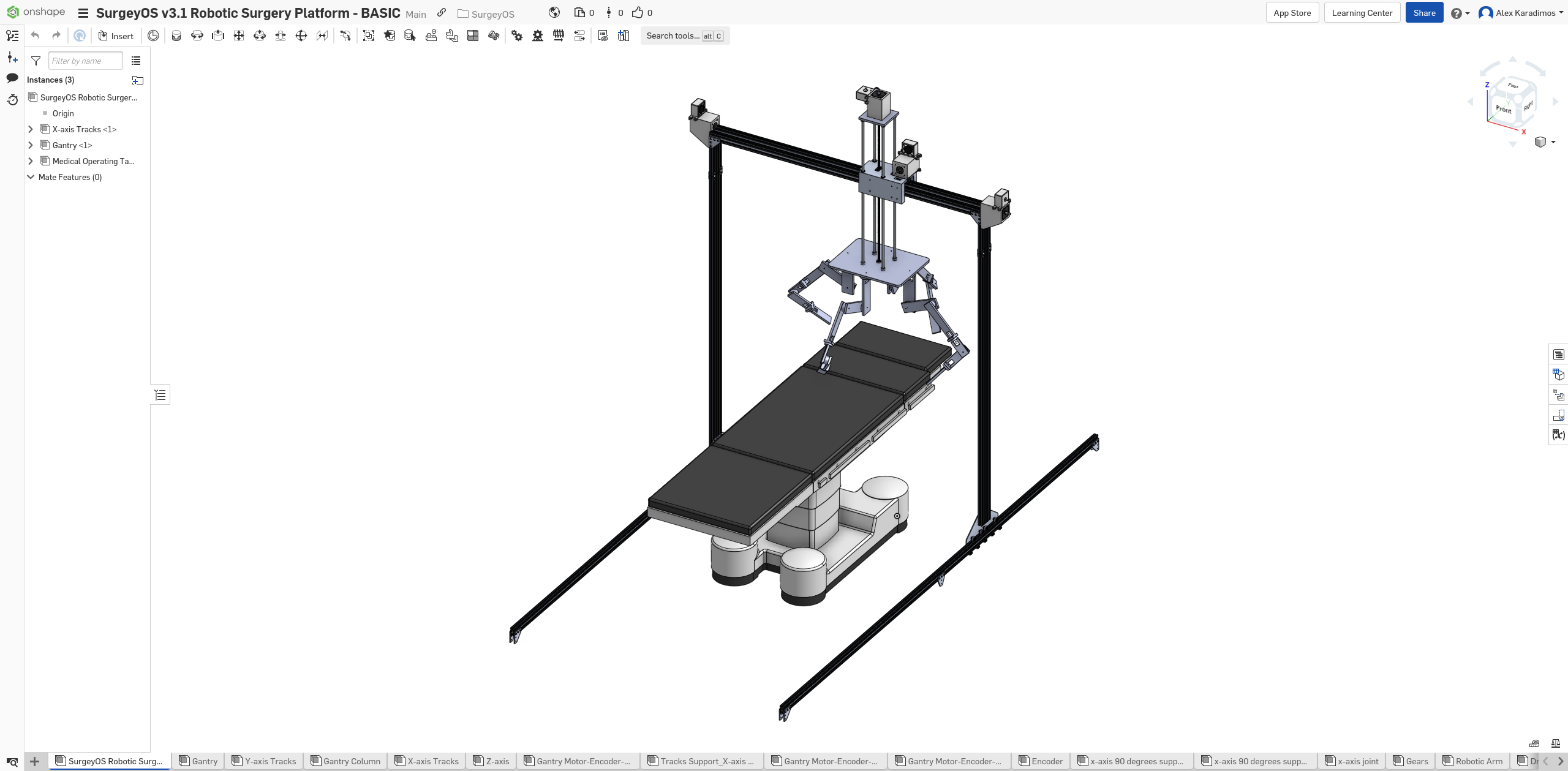
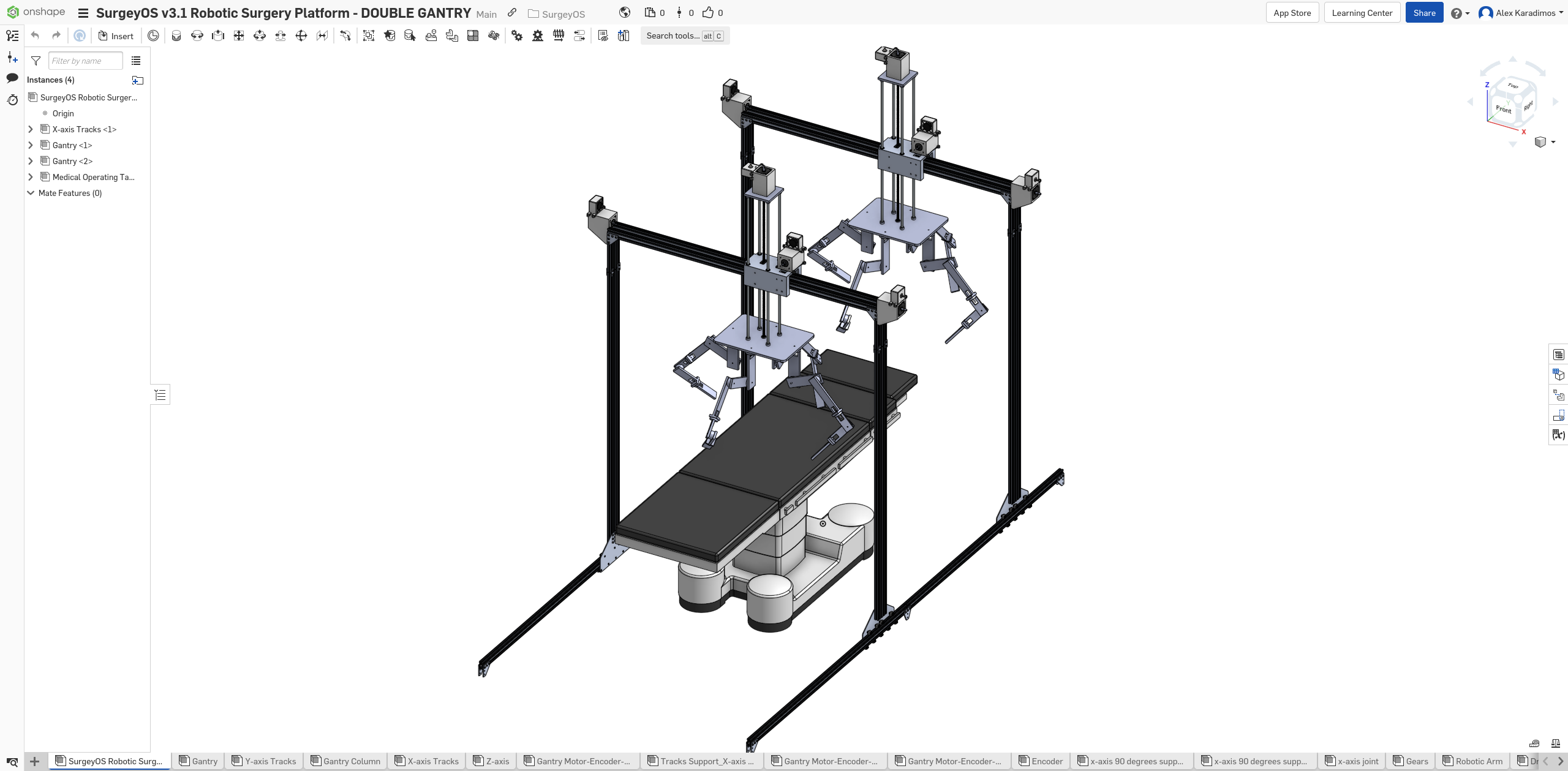
The above designs are available on Onshape:
Platform’s main components:
- Base: two parallel tracks, which allow the movement of the robot in the y-axis
- Gantry: aluminum structure, which moves parallel to the tracks and which functions as the track for the arm base
- Arm base: a structure that can move in two dimensions on the gantry (z-axis and x-axis), on which are attached the surgical robotic arms
- Surgical Robotic arms: Robotic arms that are attached to the arm base and operate with 6 degrees of freedom, to manipulate with flexibility, precision and repeatability, the surgical tools, each one of which, is attached to an arm’s end effector
Most of the structures (tracks, gantry columns and beam) are made with OpenBuilds open source hardware (v-slot aluminum extrusions and wheels) and other components, such as motor housing, arm base, robotic arms etc. can either be 3D printed or machined with a CNC.
The robot’s software is powered by the ROS (Robot Operating System) open-source framework.
The challenge the project addresses.
SurgeyOS aims to be a more accessible and inexpensive tool to researchers, medical students and doctors. Typically, Surgery Robots are very expensive and there are many institutions that can’t afford them. SurgeyOS is an open source platform and thus any university can afford to build one and conduct research and help in understanding, improving and learning more about Surgery Robotics.
Surgery Robotics come at a cost of $2 – 3 million dollars with an extra cost of $180,000 a year for maintenance and an operation can cost a patient an extra amount of $2,000 - $4,000. (https://www.forbes.com/sites/jenniferhicks/2017/11/02/new-studies-look-at-cost-and-benefits-of-robotic-surgery/#3180a00e6d47 , http://healthydebate.ca/2016/10/topic/robotic-surgery )
Open source surgery robotic platforms such as the one presented in this project, can lead to more affordable equipment with same hardware and software quality, which will then have as a result more affordable surgical operations. (Similar case: Laboratory equipment: Cut costs with open-source hardware https://www.nature.com/articles/505618d )
Project Advantages
- Open-source hardware and software reduces the total cost to the minimum (cost for buying the hardware parts)
- Open-source license means flexibility in how the robotic platform will be used for research.
- The platform is designed with a modular approach, so any researcher, medical student or doctor can adjust it based on their needs and requirements.
SurgeyOS is modular by design and can be configured in multiple ways based on different needs:
- Single gantry with single arm base
- Single gantry with double arm base
- Double gantry with one or two arm bases
- Arm base can have up to 4 robotic arms (typically 2 or 4)
- Dimensions can also be configured, but with some limitations in minimum dimensions of gantry and base, so that the robot’s components will be collision-free
- Besides the arm base, other components can be attached on the gantry as well e.g. medical imaging equipment, custom 3D bio-printer etc.
Use cases and research possible with the platform:
- Extend surgery robotics to more anatomical areas of the body
- Semi/Fully autonomous operation
- Robotic arms, collision-free orchestration
- Exterior and interior anatomical computer vision
LICENSES
This is an open source project.
- Software is licensed under the Apache 2.0 License https://github.com/ehosp/eHOSP-Surgical/blob/master/LICENSE...
Hey, everyone! Make sure to also check out our latest HealthTech/MedTech project here https://hackaday.io/project/165310-clintelli